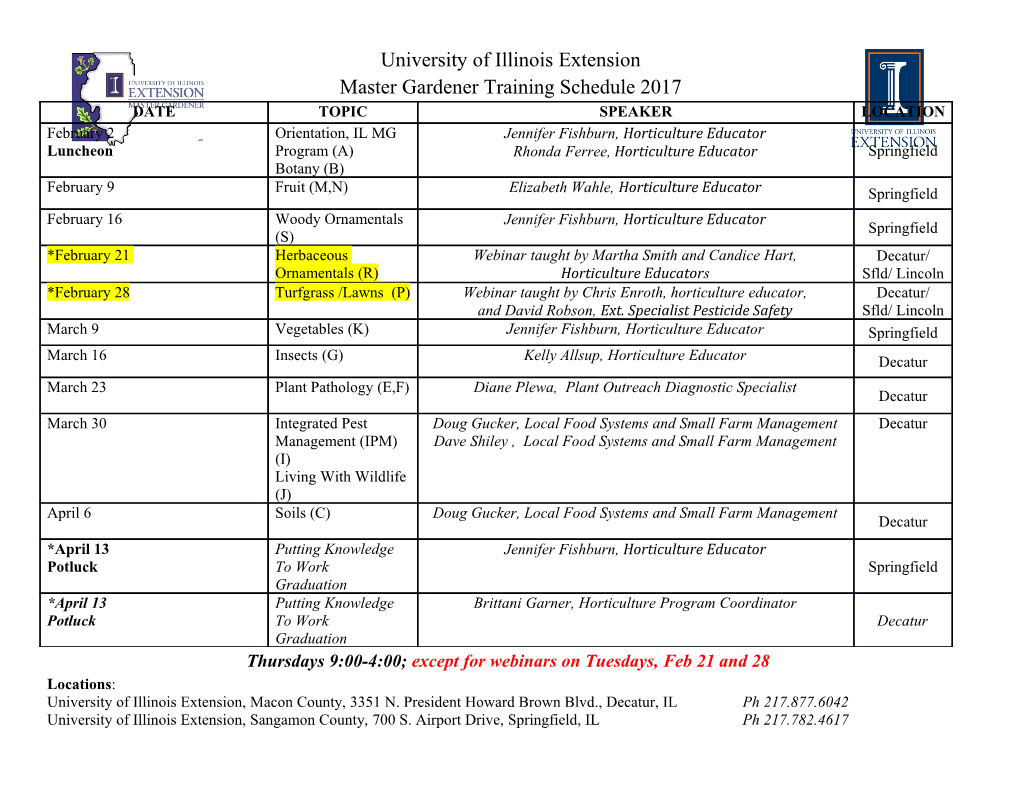
Repivoting Arbors - Slip fit & Loctite Method Also “The Polishing and Burnishing of Arbors” Another of the more advanced clockmaking tasks is the repivoting of arbors to replace worn or broken pivots. As with many aspects of clockmaking, there are a couple of approaches to this task. Ultimately, the replacement pivot needs to be concentric and properly burnished and this article discusses the “slip fit & Loctite method” which is the approach I used to successfully pass that part of my AWCI Certified Clockmaker exam. SECTION I: Repivoting Arbors Step 1: Determine Original Dimensions: Measure pivot diameter, pivot length, arbor shoulder to shoulder. Goal is to replicate the original dimensions for the certification test. This is not as critical in real practice as one can re-bush the pivot hole. a. Use the Vernier calipers to measure the shoulder to shoulder dimension. b. Use the micrometer for pivot diameter c. Use 1/100th or 1/64th ruler for pivot length Step 2: Check Lathe for Truth: Place male centers in headstock and tailstock to check for alignment. If they are not perfectly aligned, Loosen headstock & tailstock, realign until the male centers are pointed directly at each other and then snug up the headstock & tailstock. Recheck the male centers and if aligned, remove the male centers. If not aligned, which can happen after snugging them up, repeat the aforementioned re-alignment process. Step 3: Check Wheel for Truth: Fit up wheel in lathe & check wheel, arbor and remaining pivot for truth. Oppose arbor and pivot against a male center in the tailstock and adjust them as necessary. Step 4: Determine "Right Size" Drill and Plug Diameter: Using original pivot diameter dimension, calculate "right size " drill size and plug diameter. For best results in determining “right” sizes, use the “right size worksheet”. It accommodates all the variables and provides one a place to “hold” their calculations. Believe it or not, it is easy to forget your starting and intended end points particularly for short term memory folks such as myself. Worksheet Narrative: Determining the right sizes is an iterative process whereby one compares and contrasts closest drill size and available plug material sizes. Machinist drill size chart is the reference guide of choice for this process. When determining these sizes there are three variables to consider: 1. Pivot's finish dimension equals same diameter as the original pivot. This goal is primarily for the certification test. In actual practice, while the original dimension is the target, it is not critical as one can rebush the pivot hole to the new finish dimension. 2. Leave enough material for polishing & burnishing. If the plug diameter will need to be machined, then add to the original pivot diameter approx. .003" for polishing. If no machining of the plug will be necessary, meaning you have the exact "right size" plug material, add .001", as little polishing should be necessary and burnishing removes very little material, generally not more than .0005”. 3. Leave the plug undersized of the hole for the slip fit. The goal is something less than .001" undersized. Achieving a “right size” slip fit is a case by case, try and retry process caused by three factors. a. Moving from a non-fit to the right sized sticky fit goes very, very quick when you are talking in terms of .0001”. Sometimes a quick touch of the India stone to the plug is all you’ll need to get that just right sticky fit. Pay attention!! The good news, if you take too much material off and have a sloppy fit, you can easily remake a new plug. It only takes a few minutes to do. b. A drill will make a larger hole than the actual drill size. Just how much, is case by case. This is due to the nature of the drilling operation removing slightly more than its actual size and to the lathe runout. While watchmaker lathes are very accurate, they are not perfect and therefore they have some miniscule amount of runout. Collectively these two factors combine to make the hole larger than the original drill size. Just how much, is case by case. c. The plug material deflects when being machined by the lathe cutting tool. This is particularly true on the plug end farthest away from the headstock. Therefore it will machine more material off then the readings are calling for. This is problematic when you are working with .0001” tolerances and material removals. Ergo why I recommend below stopping the use of lathe cutting tools when you are at .001” oversize of the right sized diameter and to changeover to the India stone. Step 5: Determine "Right Size" Plug Length: Pivot length finish dimension needs to equal the original pivot length. Overall plug length is the length of the original pivot x 2 for American T/S arbors and x 2 ½ for modern German movements + scant 1/64” in each instance to allow for final finishing i.e. leave the plug length long until after the plug is secured in the hole. For best results use the “right size” worksheet. Again, this is a great place to “hold” your calculations. 2 Step 6: Remove Damaged Pivot: There are several methods for removing the damaged pivot. Each of them requires the right tools and technique and it is always best to practice until a satisfactory technique is repeatable. Unless one is skilled with gravers…Removal of damaged pivot is best done with the wheel fit up in the lathe, having the pivot turning in reverse and using a jewelers saw. Using any other method risks damage to the shoulder. Fitting up the wheel into the lathe and cutting the pivot off without the arbor turning works poorly. While the saw will cut smoothly, invariably, the jewelers saw will cut at an angle and cut into the shoulder, a very poor result. Perhaps this has something to do with the narrowness of the jewelers saw making it difficult to avoid human error. Cutters and nippers pinch/squeeze off the arbor and will leave you with a considerable uneven, rough surface to deal with. Removing the pivot with a jewelers saw while the lathe is turning in reverse will achieve the flatter, smoother surface one is looking for. I believe this has to do with the pivot revolving while cutting and the reverse direction that the arbor is spinning. As the pivot is turning, it is being cut all the way around at faster rate of speed then one could do by hand and the reverse direction is pulling the saw straighter. While you’ll likely end up with a “pip” by using the saw, the result will be flatter and smoother and the pip can be readily removed by stoning or facing it off. Place the lathe motor in the reverse position i.e. switch in the down position. Fit up the wheel in the lathe, securing with steady rest, if necessary. Choice of jewelers saw blade: the rule of thumb, according to Archie Perkins, is you want 3 to 4 teeth engaged with the material at all times, in this instance the pivot diameter. This is a bit of a balance as you are starting a larger cut and going to smaller i.e. the pivot material gets cut smaller and smaller. Lay the jewelers saw blade onto the pivot next to the shoulder and turn on the lathe with a medium speed and using a moderate sawing motion proceed to saw the pivot off with the arbor turning. After pivot is removed, likely you’ll left with a pip and perhaps some fraze. You’ll need to stone it or face it flat. Either works. The important part is to end up with a flat surface to bring the center drill up to and achieve a centered hole. o If using the India stone, bring it up to the shoulder and eyeball it square against the shoulder and proceed to stone any pip off and bring it flat. 3 Step 7: Drill Hole in Arbor: Choice of Drill: Drill is oversized – Plug is undersized Depth of hole is the same as the length of the original pivot for all arbors except for modern German movements which should be 1 1/2 times the length of the original pivot. A nice, consistent technique for achieving this is to use the adjustable stop located on the chuck holding spindle in the watchmaker lathe’s tailstock. Loosen this stop and locate it on the mid part of the spindle and then snug up the stop. Loosen the spindle and with a machinist rule situated behind, move the spindle with the fixed stop to the desired depth and snug up the spindle. Insert the “right sized” drill into an appropriate collet, bring the drill up to the entry point made by center drill (see below) and snug up the tailstock. The right sized drill will be something between .0005” and .001” larger than the right sized pivot diameter. When ready to drill, loosen the spindle and begin. Drill until the stop makes contact with the tailstock housing. Typically one is using HSS drill, therefore the RPM’s can be high. Start with center drill. The right size center drill is not so much measured by its point as it is by the cone part of the center drill. It is the first part of the cone diameter that should be close to the drill size as you want the center drill to enter the arbor until the cone just begins to enter.
Details
-
File Typepdf
-
Upload Time-
-
Content LanguagesEnglish
-
Upload UserAnonymous/Not logged-in
-
File Pages10 Page
-
File Size-