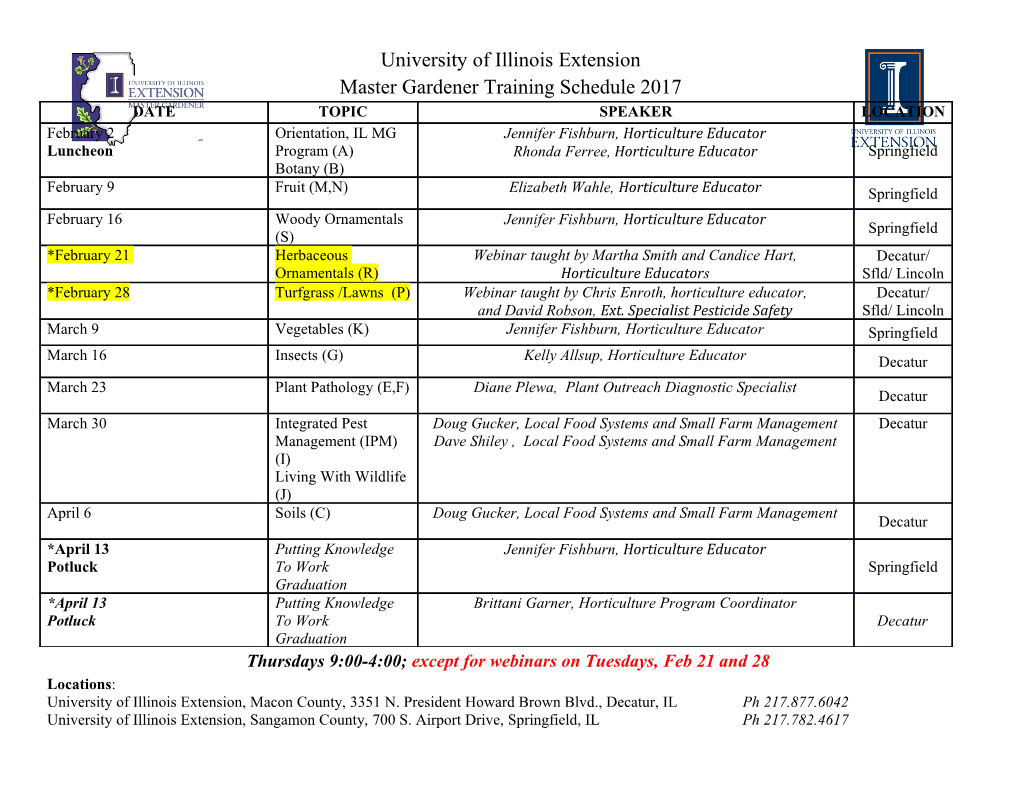
DEGREE PROJECT IN TECHNOLOGY, FIRST CYCLE, 15 CREDITS STOCKHOLM, SWEDEN 2020 Venturi Undertray KTH Bachelor Thesis Report Selma Boudali and Mattias Olausson BACHELOR THESIS TRITA-ITM-EX 2020:134 KTH ROYAL INSTITUTE OF TECHNOLOGY SCHOOL OF INDUSTRIAL ENGINEERING AND MANAGEMENT MACHINE DESIGN SE-100 44 STOCKHOLM Bachelor thesis TRITA-ITM-EX 2020:134 Venturi Undertray Boudali, Selma Olausson, Mattias Approved Examinator Supervisor . 2020-05-12 Ulf Sellgren Ulf Sellgren Commissioner Contact person KTH Formula Student Aaron Poutiainen ABSTRACT This bachelor thesis aims to describe the work performed for the design of the undertray for the Kungliga Tekniska Högskolan Formula Student(KTHFS) race car. The goal was to achieve an aerodynamically optimized undertray design that follows the regulations of the competition and the targets set by KTHFS concerning the weight, the size, the materials needed for its manufacture and costs. After some research on previous work, the concept, on which we decided that the undertray would rely on, is Venturi tunnels inspired by the Aston Martin Valkyrie, chosen for its ability to provide a large amount of downforce with a negligible amount of drag using ”ground effect”. Numerous CAD design models were created in Solid Edge and a finalized design was then ported over to Siemens NX to be analyzed using Star-CCM+ and its Design Manager feature. The CFD analyses and optimization was performed in Star-CCM+ with regards to pressure gradient, streamline velocity and downforce. These were done with variable parameters in areas such as expansion height, inlet area and ride height. Contained within this report is a more detailed description of how the CFD analysis was performed as well as suggestions for manufacturing said undertray. 1 Given the time constraints and the societal impacts of COVID-19, manufacturing had to be removed from the scope of the project, however, a step-by-step manufacture guide is provided within. Analysis of uur final design showed 428 N of downforce, a weight of 2.55 kg and a production cost of approximately 2320 SEK. It therefore passes the requirements for weight, cost and ride-height rule regulations set by Formula Student and internal KTHFS targets. Keywords Race car aerodynamics, undertray, Venturi effect, Formula student, CFD analysis, Topology optimization. 2 Kandidatexamens arbete TRITA-ITM-EX 2020:134 Venturi Underrede Boudali, Selma Olausson, Mattias Godkänd Examinator Handledare . 2020-05-12 Ulf Sellgren Ulf Sellgren Uppdragsgivare Kontaktperson KTH Formula Student Aaron Poutiainen SAMMANFATTNING Detta kandidatexamesarbete syftar till att beskriva arbetet som utförts för konstruktions- designen av Kungliga Tekniska Högskolan Formula Student (KTHFS) racerbils underrede. Målet var att uppnå en aerodynamisk optimerad underredes design som följer de regler och krav fastställda av KTHFS gällande vikt, storlek, material som behövs till tillverkningen och kostnader. Efter en litteraturstudie på tidigare arbete, blev Venturi tunnlar, inspirerade av Aston Martin Valkyrie, konceptet som vi beslutade att uderreden skulle bygga på och valda på grund av deras förmåga att förbättra bilens prestanda genom sitt nedkraftsbildande och försumbar mängd drag med hjälp av ”ground effect”. Många CAD-designmodeller skapades i Solid Edge och en slutgiltig design överfördes sedan till Siemens NX för att analyseras med Star CCM+ och dess Design Manager- funktion. CFD-analyserna och optimeringen utfördes i Star CCM+ med avseende på tryckgradient, strömlinjehastighet och nedkrafter. Dessa gjordes med variabla parametrar i områden som utvidgningshöjd, inloppsarea och frigångshöjd. I denna rapport finns en mer detaljerad beskrivning av hur CFD-analysen utfördes samt förslag för tillverkning. Med tanke på tidsbegränsningarna och samhällseffekterna av COVID-19 fick vi ta 3 bort tillverknink från projektets omfattning, men en steg-för-steg tillverkningsguide tillhandahålls i rapporten. Analyser av vår slutgiltiga design visade på 428N downforce, en vikt på 2,55 kg och en produktionskostnad på cirka 2320 SEK. Den överenstämmer därför kraven för vikt, kostnad och frigångshöjd som fastställdes av Formula Student. Nyckelord Aerodynamiken på racerbil, underrede, Venturi effekt, CFD analys, Topologioptimering 4 ACKNOWLEDGEMENTS First and foremost we would like to especially thank Per Niva, multidisciplanary technical problem solver at Avalon Innovation, for taking the time to share his expertise in the subject and guiding us. We would also like to express our sincere gratitude to Yushi Murai for discussion on fluid- mechanic topics and the thesis manuscript. We would like to thank our fellow KTHFS teammates, especially Aaron Poutiainen and Vivek J Shah for the support they showed us during the course of this project. We also wish to express a special thanks to Selma Rahman for her continued support and input into the structure of the thesis report. Last but not least, we would like to thank our supervisor Ulf Sellgren for letting us turn our passion project into a thesis. Selma Boudali & Mattias Olausson Stockholm, May 2020 5 NOMENCLATURE Denominations Symbol Description ρ Density of flowing fluid ps Total pressure P Static pressure q Dynamic pressure u; v; w Velocity of fluid in x, y, z direction g Acceleration due to gravity h Elevation of fluid with respect to ground T Stress deviator tensor f Body force ν Kinematic viscosity Abbreviations CAD Computer Aided Design CFD Computational Fluid Dynamics AC Aerodynamics and Composites KTHFS Kungliga Tekniska Högskolan Formula Student KTH Kungliga Tekniska Högskolan FS Formula Student VIM Vacuum Injection Molding FEM Finite Element Method 7 Table of Contents ABSTRACT 2 SAMMANFATTNING (SWEDISH) 4 ACKNOWLEDGEMENTS 5 NOMENCLATURE 7 TABLE OF CONTENTS 9 1 INTRODUCTION 11 1.1 Background ................................ 11 1.2 Problem Statement ............................ 11 1.3 Purpose .................................. 12 1.4 Goal .................................... 12 1.5 Methodology ............................... 13 1.6 Delimitations ............................... 14 2 FRAME OF REFERENCE 15 2.1 Ground Effect ............................... 15 2.2 Related Work ............................... 19 3 EXECUTION 23 3.1 Pre-thesis work .............................. 23 3.2 Initial design ............................... 24 3.3 Second design .............................. 25 3.4 The McDonald’s design ........................ 27 3.5 Design Manager ............................. 29 3.6 Potential production ........................... 32 3.7 Costs and weight ............................. 36 4 RESULTS 39 5 DISCUSSION AND CONCLUSIONS 41 5.1 Discussion ................................. 41 9 5.2 Conclusion ................................ 44 6 RECOMMENDATIONS AND FUTURE WORK 45 7 REFERENCES 47 A Material Properties 49 A.1 Material Description ........................... 49 B Excerpt from Formula Student regulations 55 B.1 Formula student rules .......................... 55 APPENDICES 49 10 1 INTRODUCTION 1.1 Background Kungliga Tekniska Högskolan Formula Student (KTHFS), is a non-profit student organization with the sole purpose of designing, constructing and racing an electrically driven race car to compete in Formula Student competitions. In order to produce an optimally performing car, a number of areas have to be taken into account and therefore is KTHFS divided into a number of subgroups: Mechanical Design, Vehicle Dynamics, Powertrain & Electronics, Driverless, Business Marketing, Management and lastly there is Aero & Composites (AC), in charge of the entire aero package of the car. This is the group of which we are members, working on the construction of the undertray. To be able to have a functioning car, a lot of communication is necessitated between the team groups. This can be challenging especially for decision- makings concerning the placement, shape and size of our undertray but is a really good learning experience for us as engineering students. 1.2 Problem Statement The competitions of Formula Student require that each team follows a list of rules. These have an impact on the decisions related to the design of the race car and some of the rules may be constraining especially for the aerodynamic design of the undertray. The one that is significantly important to focus on is about the static ground clearance. Any part of the vehicle other than tires must be at least 30 mm clear with a driver in the seat (Formula Student, 2020). Apart from the rules, within the team some constraints are decided together. One of these is the budget of 42 000 SEK which plays a determining role in the manufacturing aspect of the undertray. There is also a maximum weight target of 7.5 kg, set internally, that impacts its design and material choices that need to be sustainable. Of course, the placement of other car parts made by other subgroups conflicts also with the construction and placement of the undertray. Our mission as members of the AC subgroup is to find a solution for how to construct an undertray achieving an optimal aerodynamical performance while respecting the above- 11 mentioned rules. 1.3 Purpose As a vehicle reaches higher velocities the amount of air passing around the car increases as well. Normally this would lead to an increase in drag as the vehicle encounters increase resistance in correspondence with the increased velocity. But the usage of the air flow contouring the car makes it possible to benefit in an improvement of downforce with less drag thus increasing
Details
-
File Typepdf
-
Upload Time-
-
Content LanguagesEnglish
-
Upload UserAnonymous/Not logged-in
-
File Pages58 Page
-
File Size-