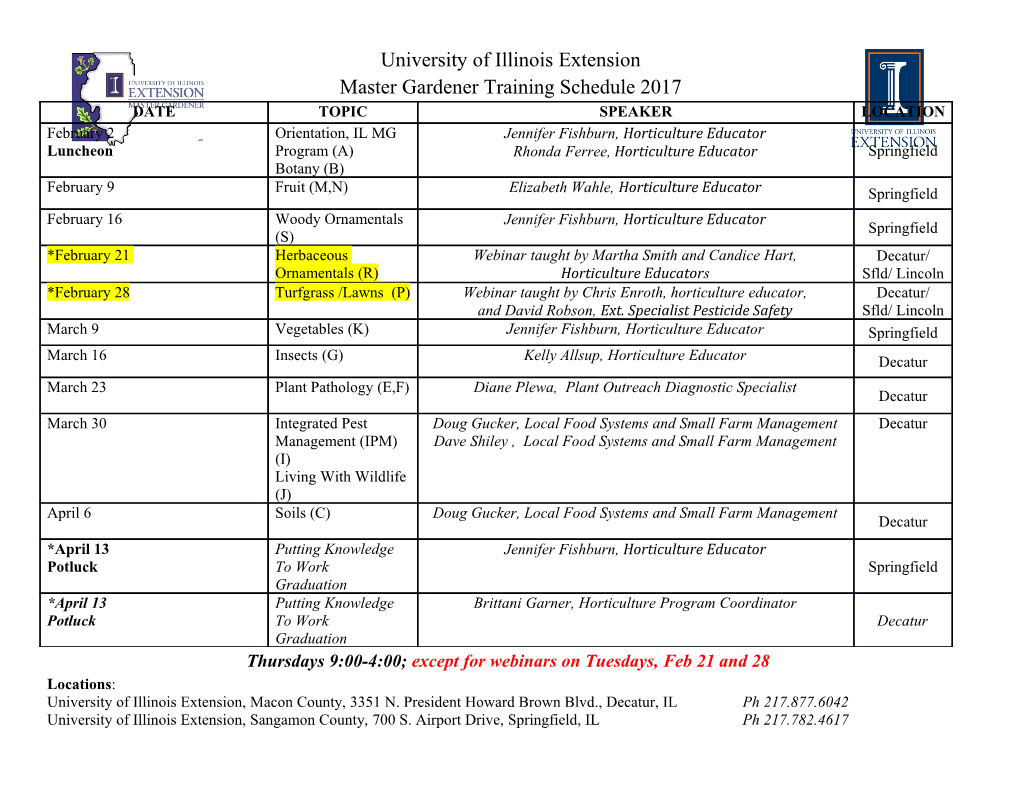
Cell Design and Layout Kenneth Yun UC San Diego Adapted from EE271 notes, Stanford University Overview n Wires n FPGA n Gate Array n Standard Cell n Datapath Cells n Cell Layout n Reading n W&E 6.3-6.3.6, 5.3 Wires n Part of capacitive load n Need to know the length to size (driver) gates n Need to plan for it n Resistance n Long wires have RC time constants n Special wires n Power, ground, and clock n Need to have low resistance Wire Properties Layer Resistance Capacitance Connects to M2 Low Low M1 M1 Low Low diff,poly,M2 poly Medium Low gate,M1 ndiff Medium High S/D,M1 pdiff Medium High S/D,M1 Wire Characteristics r L L Layer R• R•/Rtrans R = = Rsq t W W metal 0.1W 1/1.5x105 poly 5W 1/3000 L ndiff 5W 1/3000 W t pdiff 5W 1/3000 nMOS 15KW 1 pMOS 30KW 2 Wire Usage n Diffusion n Bad wire (high capacitance) n Only used to connect to transistors n Poly n Resistance high: good for short, local interconnects n Do not use to route outside cells or as jumpers in long wires n Metal n M1: only conductor that can connect to poly and diff n M1,…,Mn-1 for general wiring n Mn for Vdd, Ground, and clock routing Cell Implementation Technologies n Field programmable gate arrays (FPGA) n Chips prefabricated; program fuses/anti-fuses n Gate arrays (mask programmable) n Transistors prefabricated; customize metal to generate cells n Standard cells n All cells have fixed height n Wiring may be restricted to channels n Macro cells n Similar to standard cells but n Wiring done over cells n Memory (2D array) FPGA n Logic is programmed into chip after fabrication n Programming done using n Memory cells and CMOS switches n Fuse/anti-fuse n EPROM cells hold values for 10 years n Customizing wires n To program connections, need switches n Switches have R and C; slows down signals on wires n Completely prefabricated in large volume n Cost effective for certain applications FPGA Wiring n Standard cell like wiring (with channels) n Each channel has wires of different length n How many of each length determined by design statistics n Use logic blocks as repeaters when necessary n Problem: switches in wires (high resistance) Gate Array n Transistors predefined n W/L all the same (or choice limited) n Transistors prefabricated n Chip covered with transistors (sea of gates) n Designer provides metal patterns that form logic gates by connecting transistors n Transistors under wiring channels not used. Why? n Cheaper and faster to manufacture than standard cells. Why? Gate Array Layout Vdd A B Vdd out Gnd Gnd 2-input NAND Standard Cell n Appropriate for all or part of a custom chip n All cells have the same height (with abutting power and ground) n Cells tiled into rows n Rows separated by routing channels n Channel height variable Cell Height (includes Vdd, Gnd) Channel height Standard Cell Layout Example Macro Cell reg mux adder n Standard cell with wiring done inside cell n 1D – datapath bit slice n 2D – memory n Wires kept short and regular n Less wiring area n Less wire load (drivers can be smaller) bit line n Order cells to minimize wire lengths control (word line) Datapath n Fixed height cells with bit pitch set to n height of tallest cell n accommodate the total number of over-the-cell wires per bit n 128l a good choice n Often, cells are mirrored (every other cell is flipped vertically) to share Vdd and Gnd rails. Why? n Some cells take up multiple bit pitches n E.g., 4-bit Manchester carry chain n Variable width n Depends on functionality of cells Datapath (continued) n Wires over cells n Bit lines for data n Word lines for control, clock n Place cells to minimize number of horizontal tracks and wire lengths FB FA FB FA Registers Adder Slice Plan R R R R LA LB MX LB LA Add Requires 3 Tracks Basic Layout Guidelines n Do wire planning before cell layout n Assign preferred direction to each layer n Group p’s and n’s n Determine input/output port locations n Power, ground, and clock wires must be wide n Determine cell pitch n Height of tallest cell n Number of over-the-cell tracks and wire lengths n Use metal for wiring n Use poly for intra-cell wiring only n Use diffusion for connection to transistors only n Do stick diagram first! Basic Cell Layout Guidelines n P-N spacing is large, so keep pMOS together and nMOS together n Mirror cells, if necessary. How does it help? n Vdd and ground distribution must be in wide metal n Vdd runs near pMOS groups n Ground runs near nMOS groups n Layers in alternate directions n M1 and M2 should run in (predominantly) orthogonal directions. Why? Transistor Layout Good bad bad bad n Transistors should be at least as wide as contacts (4l) n Use as many contacts as possible for wider transistors n Don’t use 3l device except for weak devices Transistor Folding n Better aspect ratio for large transistors n Reduces diffusion area 8/2 8/2 8/2 8/2 16/2 16/2 32/2 32/2 16/2 16/2 8/2 8/2 8/2 8/2 Folding Series Gates n Fold the whole stack, not individual transistors Example: Standard Cell Latch n Static design n F’ generated internally n Feedback isolated from output F in out Standard Cell Stick Diagram Transistors share diffusion Local poly routing Vdd Room for M2 track over cell Gnd clk in out Standard Cell Layout Datapath Cell Layout Options n Data/control n Data bus in M1 and control in M2 n Data bus in M2 and control in M1 n Power/Ground n in control direction (vertical) n in data direction (horizontal) Stick Diagram (1) n Start with just wires ST ST’ RD RD’ Vdd DIN DOUT Gnd Stick Diagram (2) n Draw transistors connected to inputs and outputs ST ST’ RD RD’ Vdd DIN DOUT Gnd Stick Diagram (3) n Draw remaining transistors ST ST’ RD RD’ Vdd DIN DOUT Gnd Power and Ground n Resistance of power supply line must be very small n If too large, then the voltage supplied to gates will drop (why?), which may cause malfunction of gates n So, power supply lines must be wide metal n Rtrans >> Rmetal n Not so easy since wires are long and transistors are large Power IR Drop n Example: for 100K gate chip n Each gate drives 1mm wire (200fF) in 500ps n I = C dV/dt = 200fF x 2.5V / 500ps = 1mA n If all switch at once, 100A! n Even if only 10% switch at once, still 10A peak current! n Considerable IR drop! n Need many supply pins, wide power supply wires n Grids are good for low R Power Distribution n Distribute power on thickest metal local buses Gnd Vdd.
Details
-
File Typepdf
-
Upload Time-
-
Content LanguagesEnglish
-
Upload UserAnonymous/Not logged-in
-
File Pages31 Page
-
File Size-