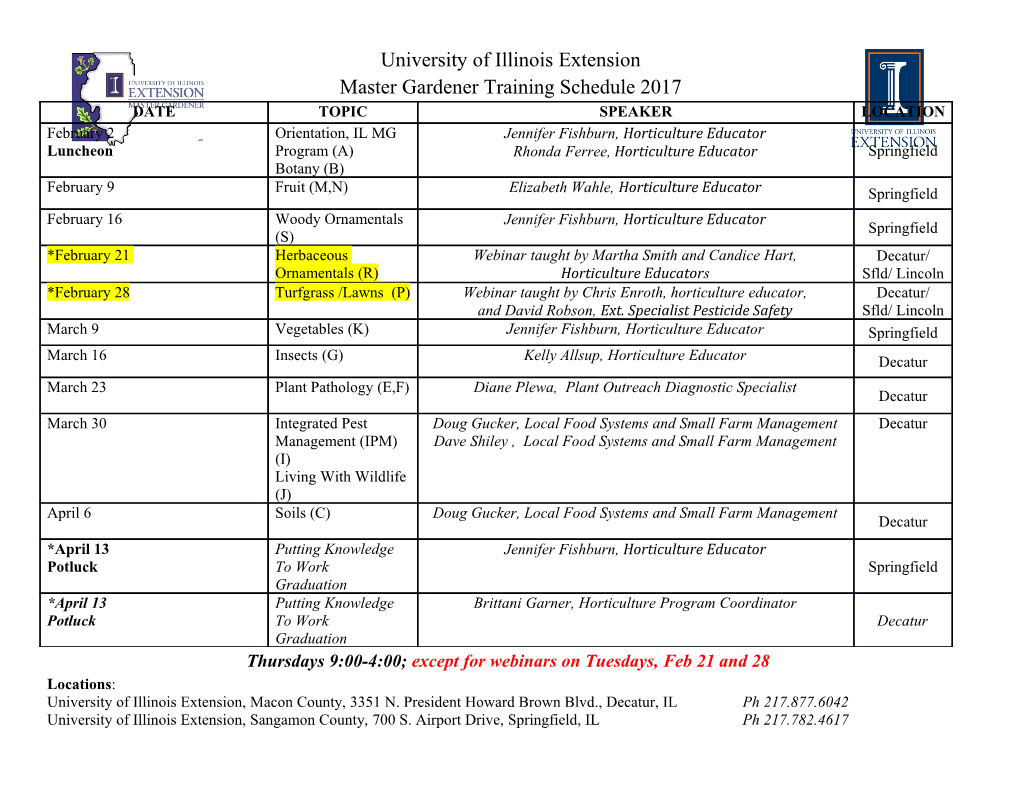
3D Numerical Settlement Analysis of a New Subway Station Close to an Existing Subway Station Jidong Li* Lianjin Tao** Junhai An*** Binglin Wu**** Key Laboratory of Urban Security and Disaster Engineering, Ministry of Education, Beijing University of Technology, Beijing 100124, China *PhD student Dept. of Civil Engineering, Beijing University of Technology, Beijng (100124) ,China (Corresponding Author, e-mail: [email protected]) **PhD student, Dept. of Civil Engineering, Beijing University of Technology , Beijng (100124) ,China; e-mail: [email protected] ***Professor,Dept. of Civil Engineering, Beijing University of Technology , Beijng (100124) , China; e-mail: [email protected] **** PhD student, Dept. of Civil Engineering, Beijing University of Technology , Beijng (100124) , China; e-mail: [email protected] ABSTRACT This paper presents a case analysis of the settlement value of the existing Subway Station during the construction of a new subway station close-attached undercrossing in Beijing, China. A micro-distortion excavation control method is proposed, that is the flat-top straight wall Cross Diaphragm (CRD) + multiple pre-top bracing concealed excavation construction methods. Furthermore, a numerical analysis using a finite difference program, FLAC3D, was conducted to analyze the settlement value of the existing Subway Station. .The results show that the maximum accumulated settlement value distribution was a shape of “W”; the largest settlement value is 2.96 mm, occurred above 5 drift; The accumulative deformation of the existing station was largest when the excavation of 1-drift and 2-drift was completed; Jacks plays an important role in the active controlling the settlement value of the existing station. The excavation of 1-drift destroys original crustal stress equilibrium, the plastic zone is formed; The plastic zone scope of soil above excavation section is largest, the thickness is about 12.5m. KEYWORDS: construction method; settlement; the existing subway stations; jacks INTRODUCTION The project of Beijing metro line 10 2nd-phase Gongzhufen Station which pass through line1 the existing station is the biggest beneath closely attached the existing lines engineering in Beijing, in order to guarantee normal operation of the existing subway, it requests the existing station sedimentation value caused by the new station construction is not more than 3 - 5785 - Vol. 19 [2014], Bund. T 5786 mm, the differential settlement value of deformation joint on both sides is not greater than 2 mm, the engineering is extremely difficult. Under the strict requirements, the flat-top straight wall CRD + multiple pre-back shore underground excavation construction method is proposed. As the technology is put forward and implemented, it is expected to solve a big difficulty in underground engineering and break through the bottleneck in beneath engineering, and provide an important foundation for the development of domestic subway construction. Although there exist some studies on the interaction between new excavations and existing tunnels (Lo and Ramsay, 1991; Dolezˇalová, 2001; Sharma et al., 2001; Liu et al., 2008, 2009; Ishihara,2001; Takeshi,2003; Qian Fang,2012) , studies focused specifically on the effect of new subway station close-attached undercrossing existing subway station are surprisingly scarce. Therefore, there are pressing needs for in-depth study on this subject. PROJECT PROFILE Engineering Background Gongzhufen subway station is an interchange station connecting Line 1 and Line 2 of Beijing subway. It is located at the intersection between Fuxing Street and West Sanhuan Street (Figure 1) . The length of the Line 1 part and the Line 10 part of this station is 169.7m and 193.65m respectively. The undercrossing section of Line 10 was single layer double span flat-straight-wall rectangle shape structure, which was 26.1m in length, 14.05m in width and 9.32m in height. The Gongzhufen station of Line 1 was built in 1967, reinforced concrete rectangular frame structure, which was 20.3m in width and 7.95m in height. The cover depth to the middle crown is about 4.5m for Line 1, and 12.5m for Line 10. There are four deformation joints of the existing Line 1 station in the undercrossing construction influence scope, the distance that new station away from deformation joints is 1.271 m, 11.659m, 2.409m and 10.521m respectively. The profiles reveal that the undercrossing excavation area was located mostly in conglomerate layer, mudstone layer and pebble bed layer. 4.5.m 9.32m The Line 1 Gongzhufen Station Deformation joint 1 Deformation joint 2 Deformation joint 4 Deformation joint 3 1.271 m 11.659m 10.521m 2.409m The Left Line The Right Line 14.05m Figure 1: Positional relation of two stations Vol. 19 [2014], Bund. T 5787 A NEW CONCEALED EXCAVATION CONSTRUCTION METHOD The construction method adopted for close-attached undercrossing part of Line 4 and Line 10, as shown in Figure 2. The main construction steps of which were: (1) Reinforcing 1-drift by advanced deep injection grouting before excavation; (2) excavating 1-drift, installing jacks at the top of grille, supporting the lower drift walls by advanced small catheter grouting; (3) excavating 2-drift, uploading 1-drift jacks force after grille closed, preloading layers and controlling deformation of existing station dynamically;(4) taking lateral deep-hole grouting for 3-drift and 5-drift through 1-drift; (5) shotcreting primary lining, and casting secondary lining within 1-drift and 2-drift, installing vertical steel-pipes supporting, with jacks, between roof and floor, and setting up horizontal steel-supporting between side walls. Erecting primary lining simultaneously with the secondary lining template, and exerting a little vertical jacking force to keep structure stick tightly; (6) repeating (3) , (4) , (5) in the 3-drift and 4-drift respectively; (7) excavating 5- drift, chiseling off local steel grating initial lining, setting up steel supporting between roofs; (8) excavating 6-drift, chiseling off local steel grating initial lining, setting up steel supporting between bottom plates; (9) increasing jacking force on both sides of vertical steel-pipes supporting, dismantling steel grille and jacks on both sides of 5-drift, chiseling off the rest of median lamella;(10) shotcreting primary lining and casting secondary lining in the 5-drift and 6-drift, when the second lining meets the design strength by more than 95%, reducing the vertical jacking force gradually, dismantling jacks. Jack Jack Steel Shotcrete 3 5 1 Steel Grating Lining 4 6 2 Steel Grating Figure 2: The construction step sequence diagram NUMERICAL CALCULATION Calculation Model In order to effectively control the existing station deformation value, numerical analyses using FLAC3D, a commercial finite difference program, was performed to calculate the deformation of the existing Line 1 station, and determined the displacement-distributing control index of the existing station in different stages and the jacking force that jacks Vol. 19 [2014], Bund. T 5788 undertook in each construction stage. Numerical model is shown in Figure 3, soil and structural calculation parameters are tabulated in table 1 and table 2. (a) The overall grid model (b) The cross grid model Figure 3: The calculation model Table 1: Soil calculated parameters Thickness Gravity Poisson's bulk modulus Frictional Cohesion Number Name /m /(kN/m3) ratio /MPa angle /(°) /kPa Miscellaneous 1 2.8 1750 0.3 10 8 10 fill 2 silt 3.4 1900 0.28 15 26 18 3 Silty clay 3 2050 0.28 20 14 30 4 Silty sand 4.3 2000 0.25 30 25 0 5 The pebble 3.5 2100 0.22 55 45 0 6 conglomerate 19 2400 0.2 1000 50 20 Table 2: Structure calculation parameters Number Name Poisson's ratio Gravity/(KN/m3) Modulus of Elasticity/ MPa 1 Grouting pebble 0.21 2300 90 The existing 2 0.2 2500 30000 structure 3 Primary support 0.2 2400 28000 4 Second lining 0.15 2500 30000 Calculation Data Analysis (1) The final cumulative settlement of the station structure is shown in Figure 4, the maximum accumulated settlement value distribution was a shape of “W”; the largest settlement value is 2.96 mm, occurred above 5 drift, meets the index of settlement is not more than 3 mm, that shows the flat-top straight wall CRD + the multiple pre-top bracing concealed excavation construction methods can effectively control the settlement of existing station structure. (2) The deformation value of each excavation stage is shown in Figure 5. When l-drift and 2-drift are break-though, the cumulative deformation value is 1.73mm, accounting for 58.8% of the total deformation; when pilot 3-drift and 4-drift are run-through, the cumulative deformation is 2.17 mm and accounting for 73.8% of the total deformation; the settlement is smaller during the excavation process of 5-drift and 6-drift; but the existing structure produced a larger settlement when parts of jacks is removed, that accounting for 31.5% of the total deformation. (3) The distribution curve of jacking force in each construction stage is shown in Figure 6. (1) A sharply change phase of jacking force in 1-drift is mainly focus on 2-drift is cutthrough, the sharply change phase of jacking force in 3-drift is mainly focus on 4-drift cutthrough, When the 5-drift and 6-drift is cut-through, the jacking force reaches 120t within 1-drift and 3- drift; Unloading jacking force after 6-drift is cutthrough, the existing station occurs sharply deformation, the stage sedimentation value is 1.2 mm, but the final deformation of the existing station is still stable within 3 mm. (4) The monitoring data shows that the maximum differential settlement value on both sides of deformation joint is less than 1mm in the construction process, is shown in Figure 7. So combining the closely attached undercrossing with the actively control of jack top-bracing can effectively avoid the defects that the differential settlement on both sides of deformation joint is too large in the traditional construction methods.
Details
-
File Typepdf
-
Upload Time-
-
Content LanguagesEnglish
-
Upload UserAnonymous/Not logged-in
-
File Pages8 Page
-
File Size-