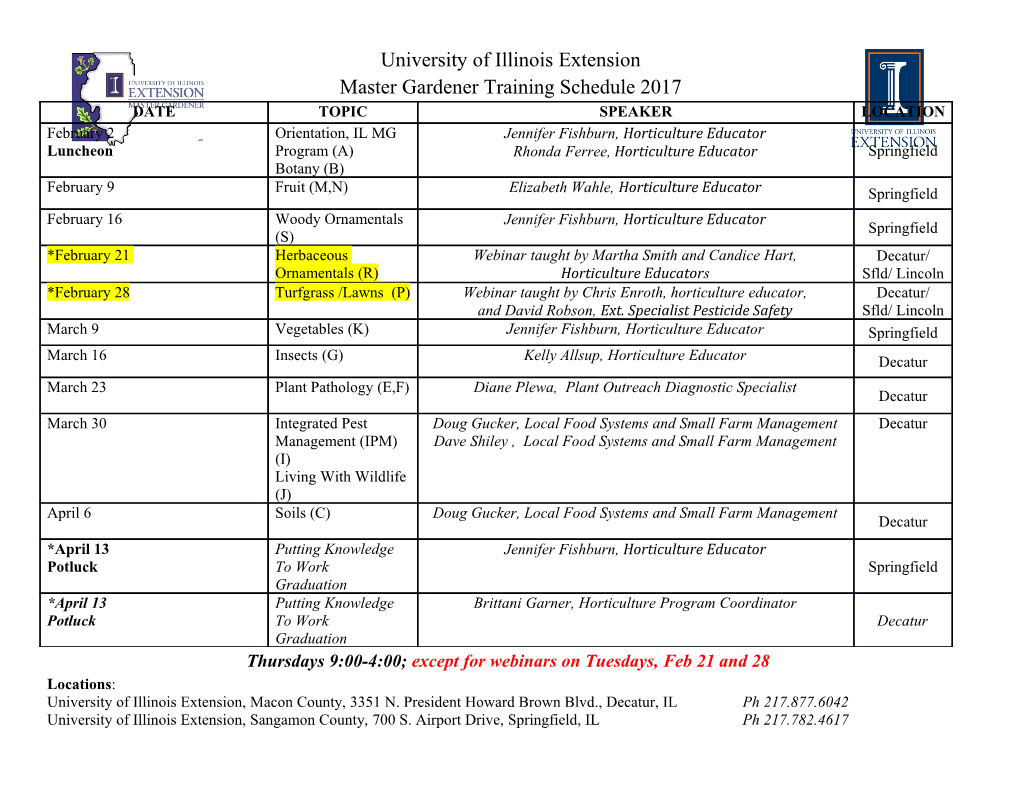
MSC.visualNastran enterprise Features of MSC.Marc The World Leader in Nonlinear and Coupled Physics Simulation Features of MSC.Marc MSC.Software Corporation, the world leader in nonlinear and coupled physics simulation, introduces you to MSC.Marc, an integrated member of the MSC.visualNastran Enterprise family. MSC.Marc has been known since 1971 for its versatility in helping market leaders to design better products, and solve simple to complex real-world engineering problems. Today, MSC.Marc has evolved and matured through constant development and worldwide use by thousands of engineers. Please read on to discover how its many capabilities will enable you to solve the most challenging nonlinear and coupled physics problems. Table of Contents Element Technology .......................................................................... 1 Solution Procedures .......................................................................... 2 Parallel Processing .......................................................................... 2 Mesh Adaptivity .......................................................................... 3 Automated Contact Analysis .................................................................... 3 Metallic Materials .......................................................................... 4 Nonmetallic Materials .......................................................................... 5 Cyclic Symmetry .......................................................................... 5 Heat Transfer .......................................................................... 6 Automated Remeshing and Rezoning ..................................................... 6 Interactive Nonlinear .......................................................................... 7 Failure Analysis .......................................................................... 8 Nonstructural Analysis .......................................................................... 9 Interactive Interpretation of Nonlinear Analysis .................................... 10 Mesh Generation ........................................................................ 10 Support Services ........................................................................ 12 Features of MSC.Marc The composite capability also exists for continuum elements. For modeling of fiberous composites, the rebar elements can be used. The MSC.Marc Element Library Element Technology • Trusses With over 150 finite element types, MSC.Marc can be used to • Shells (thick, thin, and axisymmetric) represent any geometry. These elements are modern, accurate • Membranes and robust, and may be used with virtually all of MSC.Marc’s • Plane Stress analysis capabilities. There is no practical limit to the number of • Generalized Plane Strain elements or the number of element types allowed in the analysis. • 3-D Solids The elements include lower-order and higher-order triangles and • Gaps quadrilaterals for 2-D analysis, or tetrahedron and hexahedron for • Rebar 3-D analysis. Both conventional integration, and reduced • Semi-Infinite integration (with hourglass control) options are available. Many of • Beams (solid, open, and closed section) the elements have been enhanced to use an assumed strain, • Plates mixed method, or constant dilatation formulation, which exhibits • Plane Strain superior behavior over conventional isoparametric elements in • Axisymmetric Solids many applications. Special elements are also available for • Incompressible modeling incompressible and nearly incompressible behavior. • Pipe Bends Lower-order triangular and tetrahedral elements have recently • Cables been added to the arsenal that may be applied to incompressible • Composite materials. These elements can be used with conventional elasticity, Mooney, Ogden, and other large-strain elastomer MSC.Marc also has the ability to transform the results from a 2-D models. The shell element capability is especially strong, with axisymmetric analysis to a 3-D analysis. The first stage has initially both thick and thin shell formulations. All shell elements can be axisymmetric geometry and loading. The second stage can involve used in conjunction with the composite capability. The definition of asymmetric loading and, hence, be fully three-dimensional. Large ply orientations, material properties, and failure criteria may be savings in computational costs can be obtained with this specified easily through the thickness of the shell. procedure. 3-DD Tetrahedral Element 1 Solution Procedures Working with our hardware partners, MSC.Marc utilizes the latest software technology to take advantage of hardware advances including parallel processing architectures. Complex 3-D nonlinear analysis was a dream only a few years ago. With MSC.Marc, it is now a production reality. MSC.Marc uses the latest proven numerical analysis techniques to provide the fastest, Parallel Processing most accurate results possible. All calculations are performed in MSC.Marc uses parallel processing capability to solve very large double precision. The optimal computation algorithm is available scale models. The enabling technology is based on domain for a large spectrum of analysis capabilities. decomposition methodology and is available on shared and distributed memory machines as well as a cluster of workstations Large deformation behavior can be represented using several for UNIX, NT, and Linux operating systems. The MPI protocol is formations including: used for communication between different domains. The implementation offers a highly scalable solution with nearly linear • Lagrangian and super linear speed improvement on the dedicated machines. • Eulerian Most features of MSC.Marc are available within the parallel framework. • Total and Updated Lagrangian • Total and Updated Eulerian Fine thread rolling benchmark: Transient analysis problems can be solved using a variety of time There are 76800 elements and 233523 degrees of freedom in integration procedures. Nonlinear systems are solved with minimal this model. The table shows analysis wall times and scalability computation costs using one of the following strategies: numbers for the fine thread rolling benchmark with MSC.Marc 2001 on a representative platform. • Newton (Full or Quasi) • Implicit or Explicit Dynamics CPU Wall Time Scalability • Adaptive Load Stepping 1 66159.14 1.0 2 32371.70 2.0 The adaptive load capability moderates the load to assure 4 16198.24 4.0 convergence and stability. It can be used for a variety of analysis 8 7852.56 8.4 types including structural, dynamic, creep, and thermal. Several 16 4531.77 14.6 criteria are available to control the load step size. For problems involving instability or buckling, arc-length strategies are available. The efficient solution of the system of linear equations is at the core of the MSC.Marc program. Problems of 500,000 degrees of freedom are routinely solved on modern workstations. The following solution techniques are available: Direct methods (Profile, sparse, or multifrontal sparse) • symmetric • nonsymmetric • complex Fine Thread Rolling Iterative Methods (sparse storage) • symmetric • preconditioned conjugate gradient 2 Features of MSC.Marc Design Sensitivity and Optimization MSC.Marc performs design sensitivity and sizing optimization for linear structural analysis. Design variables include: Mesh Adaptivity • Shell thickness • Beam area and moments of inertia MSC.Marc’s easy to use, powerful adaptive meshing procedures • Young’s modulus improve accuracy while reducing overall computational cost. • Poisson’s ratio • Mass density MSC.Marc provides an adaptive meshing capability for both linear and nonlinear analysis. In linear problems, the mesh is repetitively Automated Contact Analysis enriched until the error criteria are satisfied. Over 10 different criterion can be used simultaneously. When geometric information MSC.Marc has the world’s most advanced capabilities to model is available, such as the boundary curves or surface definition, the contact between bodies. This allows for the automated solution of adaptive meshing feature uses this information, which results in a contact problems where contact occurs between a deformable geometrically precise mesh. The adaptive meshing technology can body and a rigid body, or between multiple deformable bodies. be used with the linear order triangular, tetrahedral, quadrilateral, Deformable bodies are simply a collection of elements, and rigid brick continuum, and shell elements. Also, the mesh can bodies are a collection of geometric entities. These geometric automatically unrefine, in areas where the refinement is no longer entities are curves or surfaces defined using a variety of needed, to keep the model computationally inexpensive. geometric descriptions, including NURBS (Non-Uniform Rational B- Splines. Being a collection of elements, the surfaces of Plasticity deformable bodies are faceted. These facets maybe represented using analytical surface descriptions. Rigid bodies can be subject For plasticity problems, the adaptive meshing technique can be to any arbitrary motion using either displacement, velocity or force used to its advantage, to enrich the mesh in areas where material control. Furthermore, contact bodies may also be glued to each nonlinearity occurs. other to simulate situations like rigid grips on a deformable tensile specimen or joining dissimilar meshes. This easy definition of Welding contact distinguishes MSC.Marc from other FEA codes claiming to solve contact problems.
Details
-
File Typepdf
-
Upload Time-
-
Content LanguagesEnglish
-
Upload UserAnonymous/Not logged-in
-
File Pages16 Page
-
File Size-