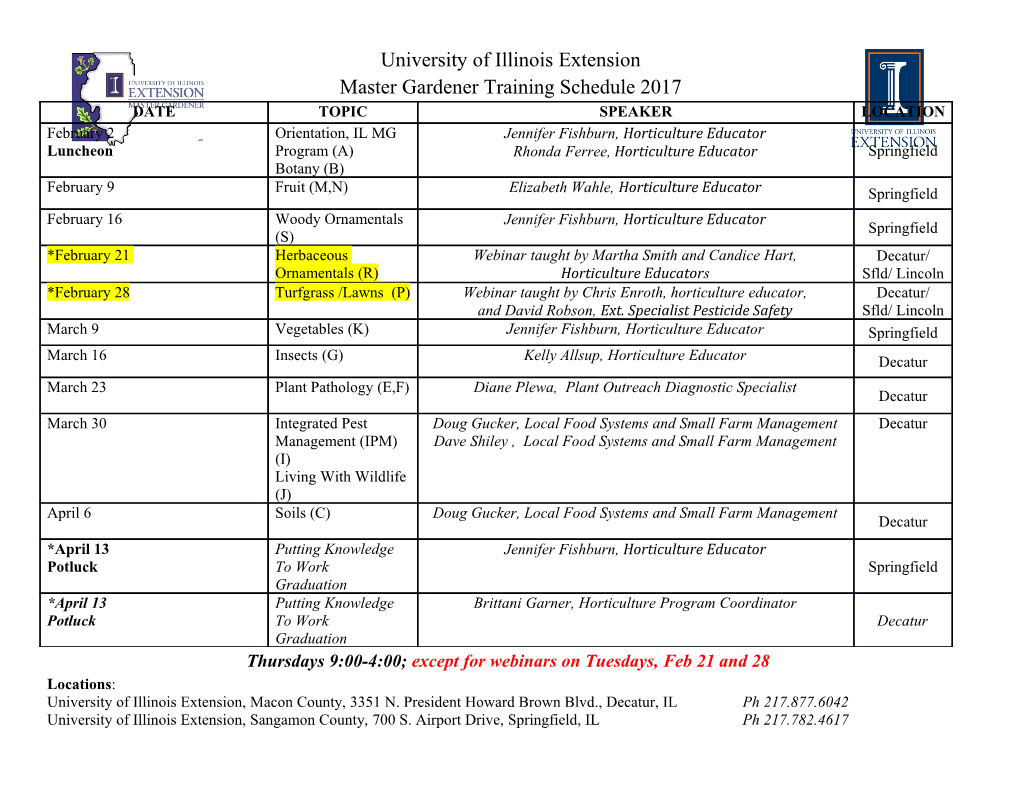
RL10 Engine Ability to Transition from Atlas to Shuttle/Centaur Program Joseph F. BaumeisterI NASA Glenn Research Center, Cleveland, OH 44135 A key launch vehicle design feature is the ability to take advantage of new technologies while minimizing expensive and time consuming development and test programs. With successful space launch experiences and the unique features of both the National Aeronautics and Space Administration (NASA) Space Transportation System (Space Shuttle) and Atlas/Centaur programs, it became attractive to leverage these capabilities. The Shuttle/Centaur Program was created to transition the existing Centaur vehicle to be launched from the Space Shuttle cargo bay. This provided the ability to launch heaver and larger payloads, and take advantage of new unique launch operational capabilities. A successful Shuttle/Centaur Program required the Centaur main propulsion system to quickly accommodate the new operating conditions for two new Shuttle/Centaur configurations and evolve to function in the human Space Shuttle environment. This paper describes the transition of the Atlas/Centaur RL10 engine to the Shuttle/Centaur configurations; shows the unique versatility and capability of the engine; and highlights the importance of ground testing. Propulsion testing outcomes emphasize the value added benefits of testing heritage hardware and the significant impact to existing and future programs. Nomenclature LH2 = liquid hydrogen LOX = liquid oxygen O/F = oxidizer fuel ratio ONPSP = oxidizer net positive suction pressure OPIP = oxidizer pump inlet pressure TDRSS = Tracking and Data Relay Satellite System I. Introduction NASA’s Centaur vehicle was the first of a new generation of space vehicle upper-stage rockets that pioneered the use of liquid hydrogen fuel for space flight. The Centaur upper-stage was developed by NASA Lewis Research Center, now Glenn Research Center in Cleveland, Ohio. The Centaur became the world’s first high-energy upper- stage, burning liquid hydrogen (LH2) and liquid oxygen (LOX) to place payloads in geosynchronous orbits or to provide escape velocity for interplanetary space probes. In combination with the RL10 engine (currently manufactured by Aerojet Rocketdyne), the Centaur became the highest performing upper-stage and one of the most prominent launch vehicles in America’s exploration of space. The vehicle has more than 200 launches that included sending the Voyager spacecraft to the outer planets, Viking landers to the surface of Mars, Cassini to Saturn, and the New Horizons probe to Pluto. The Centaur Vehicle was developed and manufactured by General Dynamics / Astronautics under the direction of NASA’s Lewis Research Center.1 The Centaur Program started in 1958 with its first successful flight in November 27, 1963 at Cape Canaveral Air Force Station in Florida. Since then the vehicle has undergone numerous evolutionary upgrades and modification to improve its performance, operability, and reliability. From 1966 to 1989, the Centaur-D configuration was used as the upper-stage for 63 Atlas rocket launches (55 successful launches). Today the Atlas/Centaur has evolved into a I Aerospace Engineer, NASA Glenn Research Center, Propulsion Division, 21000 Brookpark Rd., Cleveland, OH, 44135. 1 American Institute of Aeronautics and Astronautics suite of Atlas supported vehicles launching from both Cape Canaveral Air Force Station and Vandenberg Air Force Base. Hydrogen in its natural state is a gas and is the lightest and simplest of all elements. Liquid hydrogen is colorless, odorless, and very lightweight. To remain in a liquid state, hydrogen must be kept supercooled to -423 °F (-253 °C). For the Centaur to accommodate liquid hydrogen, new technologies were required. This included developing a highly integrated propellant storage and utilization system that included thermal insulation, propellant feed system and propulsion capable engines. It also required appropriate hydrogen ground handling and controls. This lightweight Centaur vehicle with engines that utilized liquid hydrogen and oxygen mixture could then deliver about 35 percent more thrust per pound of propellant than other conventional kerosene-type fuels. The RL10 propulsion engine was a major sub-system in the successful Centaur Program and continues to provide sustained reliability and performance. Its efficiency and capabilities have kept the Centaur in the forefront of space flight. Integrating the existing Centaur RL10 engine within the Space Shuttle was a cornerstone of the Shuttle/Centaur Program. The RL10 operational flexibility enabled easy transition with minimal modifications and the ability to transition to a human space flight environment. We will explore the differences between the Atlas/Centaur and Shuttle/Centaur vehicles, impacts on the propulsion system, and the role ground testing provided. II. Atlas/Centaur Vehicle Configuration The Atlas/Centaur is an expendable launch vehicle derived from the SM-65D Atlas intercontinental ballistic missile in the late 1950s. The Atlas boosters were developed by the United States Air Force and were repurposed for NASA’s Atlas/Centaur Program. The Atlas first stage booster rocket was mated to the new Centaur liquid-hydrogen and liquid-oxygen cryogenic fueled upper stage. This high-energy Centaur upper-stage was capable of placing much heavier payloads into higher earth orbits, unmanned lunar trajectories, or planetary trajectories by incorporating the new RL10 propulsion system. This Atlas/Centaur design is shown in Fig. 1 & 2. The Atlas/Centaur-2 launch demonstrated a successful Centaur vehicle separation and flight with the first RL10 engine inflight burn of liquid hydrogen and liquid oxygen. The Centaur vehicle had an extraordinary operational success record and has been called “America's Workhorse in Space”. Figure 1. Atlas/Centaur Configuration and Atlas/Centaur-2 Launch. Figure 2. Early Centaur Configuration. 2 American Institute of Aeronautics and Astronautics The Centaur D-1 vehicle was 29 feet in length and had a diameter of 10 feet with all avionics and payload mounted on the forward adapter. It had no internal support structure and was pressurized to maintain it shape and strength. The thrust was obtained from two RL10 engines that generate 15,000 nominal pounds of thrust each. These engines were capable of being shut-down and restarted during flight to increase mission capability and were gimbaled to provide spacecraft directional control. Figure 3 shows the Centaur engine configuration as the vehicle is being lowered into a NASA Lewis Research Center Test facility. In addition, smaller hydrogen peroxide engines provided additional thrust for propellant settling and attitude control during transition and low thrust coast periods. This vehicle had the capability of lifting over 8000 pound payloads into near Earth orbits, 2300 pounds to the Moon, and boosting 1300 pounds on interplanetary trajectories. Unique Centaur design features and upgrades included: Thin wall stainless steel tanks (lightweight). Structural rigidity was provided by propellant pressure (prior to propellant loading, nitrogen gas pressurization provided structural support). A common double-bulkhead to separate the LOX and LH2 tanks. Multiple engine restart vehicle. Hydrazine monopropellant reaction control system (previously a hydrogen peroxide system). Tank pressure from RL10 boost pumps (previous hydrogen peroxide system). Centaur powered by one or two RL10 rocket engines. Figure 3. Atlas/Centaur Being Lowered into NASA Lewis Research Center Test Facility. III. Titan-Centaur Vehicle Configuration The Centaur was also successfully integrated with the United States Air Force Titan vehicle known as Titan IIIE. The Centaur was modified to be used as the third stage on the Titan IIIE vehicle. From 1974 to 1977, the Centaur D- 1T configuration launches included the Viking 1 & 2, Voyager 1 & 2, and Helios 1 & 2. Figure 4 shows the Titan/Centaur configuration. Figure 4. Titan/Centaur Vehicle (Left), Centaur and Payload (Middle), August 20, 1975 Titan Centaur Launch of Viking 1 Spacecraft (Right). 3 American Institute of Aeronautics and Astronautics IV. Centaur RL10 Engines The RL10 engine was designed as a regeneratively cooled system (hydrogen cooled thrust chamber) which included a turbo-pump that utilized an expander cycle (thrust chamber expanded hydrogen to power turbo-pump).2 The original Centaur engines flown on the first successful Atlas/Centaur flight were designated as the RL10A-3 engines. Over the years, prior to the Shuttle/Centaur Program, the engines were upgraded to enhance vehicle performance, shown in Table 1. The engine is shown in Fig. 5. Table 1. Early RL10 Engine Performance Upgrades. RL10 Model Number RL10A-1 RL10A-3 RL10A-3-1 RL10A-3-3 RL10A-3-3A Thrust, lbs. (Vacuum) 15,000 15,000 15,000 15,000 16,500 ISP, sec. (5.0 Mixture) 424 429 433 444 446.4 Chamber Pressure, psia 300 300 300 395 465 Throat Diameter, in. 6.0 6.0 6.0 5.1 4.9 Expansion Ratio 40:1 40:1 40:1 57:1 61:1 70 long Engine Envelope, in. Unchanged Unchanged Unchanged Unchanged 40 wide Figure 5. RL10A-3-3A Engine Side Views. Each Centaur RL10A-3-3A engine at space vacuum conditions produced a rated thrust of 16,500 pounds and a 444.4 ± 2.5 sec nominal specific impulse at a nominal propellant oxidizer to fuel mixture ratio of 5.0:1. The engines also gimbal which provides flight control, are capable of inflight restarts, and provide a small amount of hydrogen gas for vehicle fuel tank pressurization. Solenoid
Details
-
File Typepdf
-
Upload Time-
-
Content LanguagesEnglish
-
Upload UserAnonymous/Not logged-in
-
File Pages17 Page
-
File Size-