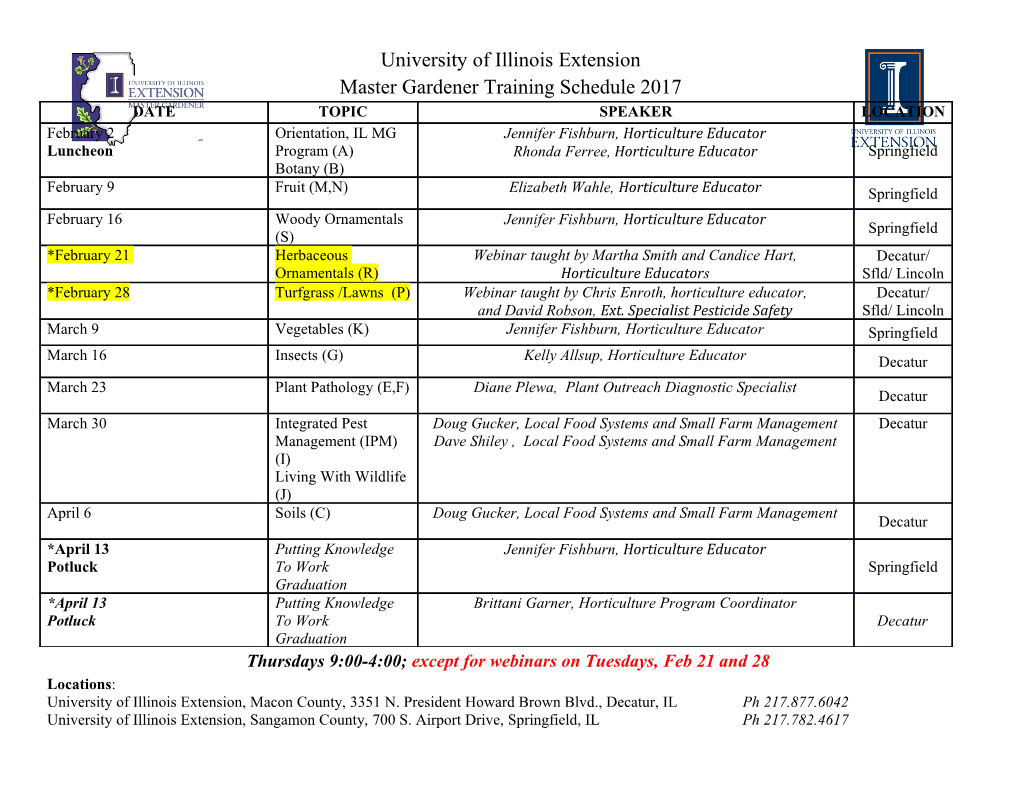
Flat Jack Method for Measuring Design Parameters for Hydraulic Structures of the Koyna Hydro Electric Project in India Keshav Ral Dhawan, Chief Research Officer, Central Water & Power Research Station, Khadakwasla, Pune– 411 024; [email protected] ABSTRACT: The paper presents two different projects: The first involves a case with limited rock cover on a side of an excavated surge shaft located near a steep slope. The second involves the assessment of design parameters of an existing masonry dam for use as input in dynamic analysis. The induced stresses in the surge shaft of Koyna Hydro Electric Project (K.H.E.P.) stage-IV were measured with flat jack. These tests were first performed in a 4 m diameter pilot shaft and after the shaft was excavated to its full diameter of 22.70 m. The stresses increased from 3.96 MPa to 5.09 MPa, when the 4m- diameter surge shaft was expanded to its full diameter of 22.70 m, in the case where significant rock mass cover existed at EL 651.00 m. However stress reduction or no variation in the induced stress was measured in the portion of insufficient rock cover. In the second case, to determine the design parameters of Kolkewadi masonry dam of K.H.E.P stage-III, flat jack tests were conducted at the upstream side of Kolkewadi masonry dam in masonry of 1:4 and 1:3 and at downstream sloping side in masonry of 1:5. It is impractical and difficult to obtain mechanical properties of masonry in laboratory from the extracted core samples, due to intrinsic nonhomogeneity of the material. The brick/stone and mortar layers caused anisotropic behavior of masonry. Average deformation modulus for 1:3 masonry was 32.8 GPa. Similarly, the average deformation modulus for the 1:4 and 1:5 masonry was 19.0 and 13.7 GPa respectively and were adopted for the dynamic analysis. Induced stresses in the masonry dam were found to be nearly equal to the overburden. KEYWORDS: flat jack, masonry dam, surge shaft, deformation modulus, induced stresses SITE LOCATION: IJGCH-database.kmz INTRODUCTION The surge shaft is an important component of the Koyna Hydro Electric Project (K. H. E. P), Stage-IV. Fig.1 shows the location of different stages of the K. H. E. P. The surge shaft is located in a narrow hill with low rock cover i.e. less than 4 times the surge shaft diameter. The lower rock cover is present around North-East-South (N-E-S) side of the surge shaft due to very complex topography. Fig.2 shows the location of the surge shaft in the hill slope. The effect of lower rock cover was required to be investigated (Dhawan and Singh, 2002). The rock cover effect was investigated around the 121 m deep; 22.70 m diameter surge shaft of K. H. E. P, Stage-IV, by flat jack tests around the surge shaft (Fig.3). The local geology indicates presence of alternate layers of volcanic breccia and amygdaloidal basalt. Volcanic breccia is located between EL 682 to 692 m, 647 to 655 m and 610 to 619 m and the rest comprises of amygdaloidal basalt. As the upsurge in the surge shaft may reach up to EL 651.00 m, in-situ studies to determine the stresses near that level were required to be carried out. To determine the induced stresses and effect of lower rock cover, flat jack tests were conducted at two elevations: at EL 637.60 m in basalt and 651.0 m in volcanic breccia in the 4 m diameter pilot shaft (Fig.3) and at EL 651.0 m in the fully expanded surge shaft of 22.70 m diameter. Another application of flat jack test is presented for the Kolkewadi uncoursed rubble (UCR) masonry dam located at Alore village, District Chiplun, Maharashtra and part of K.H.E.P. Fig.1 shows the location of Kolkewadi dam which is Stage-III of K.H.E.P. The length and height of Kolkewadi dam is 497.0m and 56.80m with gross storage of 36.22 Mm3.The dam was constructed in 1975, when the seismic activity was considered low in Koyna region. The Government of Maharashtra formed an Experts’ Committee after the Killari earthquake (magnitude 6.4 Richter scale) on 30th September 1993 near the Submitted: 11 March 2011; Published: 21 May 2012 Reference: Dhawan, K.R. (2012). Flat Jack Method for Measuring Design Parameters for Hydraulic Structures of the Koyna Hydro Electric Project in India. International Journal of Geoengineering Case histories, http://casehistories.geoengineer.org, Vol.2, Issue 3, p.182-195. doi: 10.4417/IJGCH-02-03-01 International Journal of Geoengineering Case Histories ©, Vol. 2, Issue 3, p. 182 http://casehistories.geoengineer.org dam. The Committee recommended carrying out dynamic analysis of Kolkewadi dam by adopting realistic design parameters for the different parts of the dam. These parameters needed to be determined. Major portions of the dam have been constructed with UCR masonry with different proportions of cement sand to mortar ratios of 1:3, 1:4, and 1:5. Cores of different sizes (100 and 150 mm diameter) were extracted from masonry parts of the dam body and were tested in the laboratory to assess the design parameters. Laboratory test results of masonry cores indicated large variation of properties due to variations in percentage of mortar, as well as orientation and size of stones in the extracted cores. Thus, in-situ testing of the masonry portion of the dam was required to be conducted using the flat jack method in an effort to assess the deformation modulus, Poisson’s ratio and induced stresses. The technology of the flat jack test has been modified and adopted for the purpose of evaluation of brick and stone masonry structures in Italy by Rossi (1982, 1985). Rossi developed initial specifications for the optimum size and placement of flat jacks, techniques for measuring deformations, the proper calibration of flat jacks, and post-test analysis of data. Analytical studies have been performed in support of the experimental results. Sachhi et al. (1986) conducted extensive nonlinear finite element analyses of both the single and double flat jack tests in masonry materials. They found their numerical models to be generally in support of experimental evidence, and offered some insight regarding the effect of certain assumptions on the accuracy of the results. Based on their analytical work, the authors recommend that if the flat jack test is carried out to failure on masonry, the failure stress should be reduced by 20% to estimate the unrestrained compressive strength. Similarly, the in-situ stress test may overestimate the actual state of stress by as much as 10% according to their models. It is explained that the Flat jack test provides a direct measure of the vertical stress at a point in the structure. Thus, the test provides an indication of the factor of safety in terms of compression failure in masonry. The test also yields deformation modulus and Poison’s ratio of the tested material. Figure 1. Koyna H.E. Project (Stage I-II-III-IV) schematic layout. CASE STUDY I: IN-SITU STRESSES IN ROCK MASS AT SURGE SHAFT OF KOYNA H.E. PROJECT In order to account for the lower rock cover available around the surge shaft, flat jack studies were performed to measure the induced stresses and deformability of the rock mass in the surge shaft at two stages of excavation (Dhawan and Singh, 2004). At the first stage the measurements were carried out in the 4 m diameter pilot shaft at two levels: at EL 637.60 m in amygdaloidal basalt and at EL. 651.0 m in breccia (Fig. 4), to allow for a comparison of the state of stress and deformability at these levels. In the second stage, measurements of induced stresses and deformability of the rock mass were made for the fully excavated surge shaft of 22.70 m diameter at EL. 651.0 m only (Fig.4), as adequate rock cover was available at EL. 637.00 m. The flat jack test locations are shown in Fig.4. International Journal of Geoengineering Case Histories ©, Vol. 2, Issue 3, p. 183 http://casehistories.geoengineer.org Figure 2. Schematic layout of Koyna H.E.Project stage-IV. Figure 3. Location of flat jack test platforms in pilot shaft and other major constituents of the surge shaft. International Journal of Geoengineering Case Histories ©, Vol. 2, Issue 3, p. 184 http://casehistories.geoengineer.org Figure 4. Location of flat Jack tests at EL 637.60 m. and 651.0 m. in pilot shaft and at EL 651.0 m. in fully excavated shaft (radii not in scale) Evaluation of In-situ Stresses When stresses are to be determined near the surface, as in this case, the flat jack method represents probably the most suitable method. The flat jack tests were carried out in the surge shaft, as per I.S.13946, Part IV, (1994). Equation 1 is used to evaluate the stresses: PK1=PθK2+Ph K3 (1) Where P is the cancellation pressure, P and Ph are the yielding stress in the horizontal and vertical slot directions respectively (Owen and Hinton, 1980). Constants K1, K2, K3 are determined to account for the size of slot effects, expressed by equations 2, 3 and 4: Y 1 (2) KC1 o 1 ao Co ao 1 Y K C Yo a C1 2 Yo (3) 2 a C Y 1 (4) K3 Yo 2 a C a where: Y 2 Y 2 a and a o 1 2 1 2 Co C The length of flat jack is 2Co, Poisson’s ratio,, length of slot is 2C, distance between two reference pins is 2Y and width of slot is 2Yo.The slot axis is passing through the center of slot section and parallel to the plane of slot width (Fig.5).
Details
-
File Typepdf
-
Upload Time-
-
Content LanguagesEnglish
-
Upload UserAnonymous/Not logged-in
-
File Pages15 Page
-
File Size-