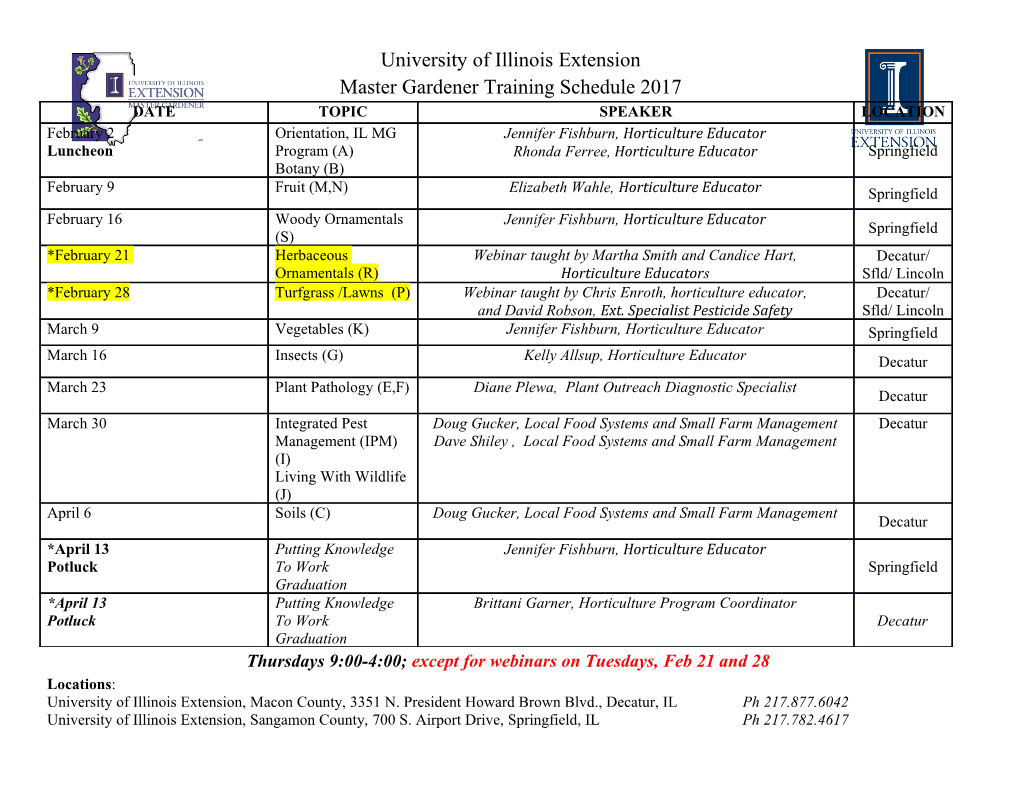
Safety Practices for Working with Beryllium Oxide Products SF301 - Version 3, March, 2018 BeO Beryllium oxide (BeO), in solid form and as contained in finished products, presents no special health risks. However, like many industrial materials, beryllium oxide does present a health risk if handled improperly. The inhalation of beryllium oxide dust, mist or fume can cause a serious lung condition in some individuals. The degree of hazard varies depending on the form of the product, and how the material is processed and handled. You must read the product specific Safety Data Sheet (SDS) for additional environmental, health, and safety information before working with any beryllium containing material. In addition, processing beryllium oxide ceramic shall be conducted in accordance with the Beryllium Standard for General Industry (29 CFR 1910.1024) established by the Occupational Safety and Health Administration (OSHA) which includes a Permissible Exposure Limits (PEL) of 0.2 microgram beryllium per cubic meter (0.2 µg/m3) as an 8- hour Time Weighted Average (TWA), a Short-Term Exposure Limit (STEL) of 2.0 µg/m3 determined over a 15-minute sampling period and ancillary requirements prompted at an Action Level (AL) of 0.1 µg/m3 or other specified situations. SOURCES OF EXPOSURE All ceramic removal operations performed on beryllium oxide products must be performed with appropriate work practices and engineering controls designed to control the release or generation of airborne beryllium-containing dust, mist or fume. The following table provides a summary of those processes that typically present low inhalation concern (green) and those that may present a likely inhalation hazard (yellow). Low Inhalation Concern Likely Inhalation Hazard Operations Operations Adhesive Bonding Abrasive Blasting Drilling Plasma Spray Assembly Abrasive Processing Dry/wet Tumbling Polishing Brazing (< 1,100o C) Abrasive Sawing Extrusion Powder Handling Electroless Plating Atomizing Filing by Hand Powder Pressing Electroplating Attritioning Firing of green ceramic Process Ventilation Firing (< 1,100o C) Boring Firing of refractory Maintenance Hand Solvent Cleaning Brazing (> 1,100o C) metallization (> 1,100o C) Reaming Handling Broaching with green Grinding Sand Blasting Heat treating (< 1,100o C) ceramic Gun Drilling Sanding Inspection Brushing Honing Scrap Management Laser Resistor Trimming Buffing Hot Isostatic Pressing (HIP) Sectioning Metallizing Centerless grinding Lapping Shearing Packaging Chemical Cleaning Laser Cutting Sintering of green ceramic Painting Chemical Etching Laser Machining Sintering of refractory o Non-destructive testing CNC Machining Laser Scribing metallization (>1,100 C) Plasma Cleaning Cold Isostatic Pressing (CIP) Laser Marking Snapping Plating Coolant Management Laundering Solution Management Radiography/X-ray Crushing Machining Spray Drying Shipping Cutting Metallography Tape casting Soldering Deburring (grinding) Milling Turning Sintering (< 1,100o C) Deburring (non-grinding) Mixing Water-jet Cutting Ultrasonic Cleaning Destructive Testing Piercing Ultrasonic Testing Dicing 1. Operations in the “Low Inhalation Concern” category represent operations that typically release non-respirable (>10 micrometer) particles, are not expected to generate significant ultra-fine particulate, and/or are not expected to result in exposures in excess of the OSHA PEL. 2. Operations in the “Likely Inhalation Hazard” category represent those operations which may release respirable (<10 micrometer) particles, may generate ultra-fine particulate, may generate beryllium oxide and/or may result in exposures in excess of the OSHA PEL. 3. This list is not all-inclusive and variation can exist within specific processes. Determine, then verify, the adequacy of engineering and work practice controls by conducting an exposure characterization of all copper beryllium processing operations. 4. Effective ventilation, work practices and personal protective equipment use can control a “Likely Inhalation Hazard”. 5. When evaluating operations, consideration must be given to potential exposures from activities in support of these operations such as setup, preparation, cleanup and maintenance. WORK PRACTICES AND CONTROL MEASURES The following exposure control measures must be considered for particle producing operations involving beryllium oxide products: Wet Methods Machining operations are usually performed under a liquid coolant flood which assists in reducing airborne particle dispersion. However, the process may also require complete hooded containment and local exhaust ventilation (see exhaust ventilation section below). Care must be given to lubricant containment which prevents splashing onto floor areas, external structures or operators’ clothing. Coolant splash which does deposit outside the ventilated enclosure should be cleaned up immediately. Splashed coolant must not be allowed to dry because it may carry with it particulate containing beryllium oxide which can later become airborne. Cycling of liquid machining lubricant/coolant containing finely divided beryllium oxide in suspension can result in the particle concentration building to a point where beryllium oxide may become airborne during use. The coolant reservoir should be enclosed and ventilated. A coolant filtering system is recommended. Exhaust Ventilation Local exhaust ventilation with full enclosure hooding must be used on all machining operations capable of producing airborne beryllium oxide dust, mist or fume. The type of ventilation required depends on the characteristics of particle generation. Particulate generation can be highly variable as determined by feed rate, feed speed, size and speed of the tooling, tool sharpness, coolant flow, configuration of the part being machined, etc. The hooding should completely enclose the “point of operation” area without interfering with the travel of machining tooling. The enclosure should have no openings which would allow direct release of airborne particulate outside the enclosure. Any opening within the normal range of direct particle/coolant scatter should be baffled or convoluted in design to prevent a direct release outside the enclosure. Enclosure doors should be interlocked to the machine controls. If the doors are opened, the machine should stop automatically. Ventilation systems should be interlocked to the machines in a manner which requires the ventilation to be operating before or concurrent to the startup of the machines. Dry machining of beryllium oxide requires a close capture, high velocity, low volume ventilation system. High velocity/low volume ventilation pick-ups must be located as close to the point of particulate release as possible and be positioned “in line” with the direction of particle generation. Where necessary, custom fabricated ventilation duct inlets should be provided to optimize capture of chips and particulate released by particle producing processes. In addition to having a close capture ventilation system, a secondary total enclosure may be necessary when dry machining beryllium oxide. The particles generated when using powered grinders or roto tools can be very difficult to control due to the random nature of particle generation. The use of powered grinders and roto tools must be controlled in a ventilated partial or complete enclosure designed to draw particles away from the operator. Alternative methods to powered grinders such as wet filing or wet hand sanding should be used where possible. Dry hand sanding or filing of beryllium oxide must either be performed inside a ventilated enclosure or performed completely wetted or submerged. Parts and other contact materials must be cleaned before removing from the ventilated enclosure or immediately after wet processing. Compressed air must not be used to clean parts. Resi- due on tooling and contact materials must not be permitted to dry and should be cleaned and/or double bagged in a moist condition to prevent airborne exposure during subsequent handling. Disruption of the airflow in the area of a local exhaust inlet, such as by a man cooling fan, should be avoided. The discharge of air from an air cleaning system into the work place air is not recommended due to the potential for exposure in case there is a failure of the filtration system. The system should be discharged outside and away from building makeup air inlets. Most process air emission sources will require an air permit from a local and/or state air pollution control agency. The use of air cleaning equipment may be necessary to achieve the permissible emission. Tempered makeup air should be provided to prevent excessive negative pressure in a building. See the Material Safety Data Sheet (MSDS) for detailed information on air emission requirements. Ventilation equipment should be checked regularly to ensure it is functioning properly. Ventilation training is recommended for all users. To be effective, the ventilation system should be designed, installed and maintained by qualified personnel. Tooling During machining of beryllium oxide products, the tooling may become contaminated to a point where subsequent conditioning and sharpening activities may need special controls and work practices. Tooling used to machine beryllium oxide should be dedicated to the activity or should be cleaned prior to use in other areas or on other materials. All tooling should be cleaned immediately after removal from a machine by wet cleaning methods to ensure no loose particulate remains
Details
-
File Typepdf
-
Upload Time-
-
Content LanguagesEnglish
-
Upload UserAnonymous/Not logged-in
-
File Pages4 Page
-
File Size-