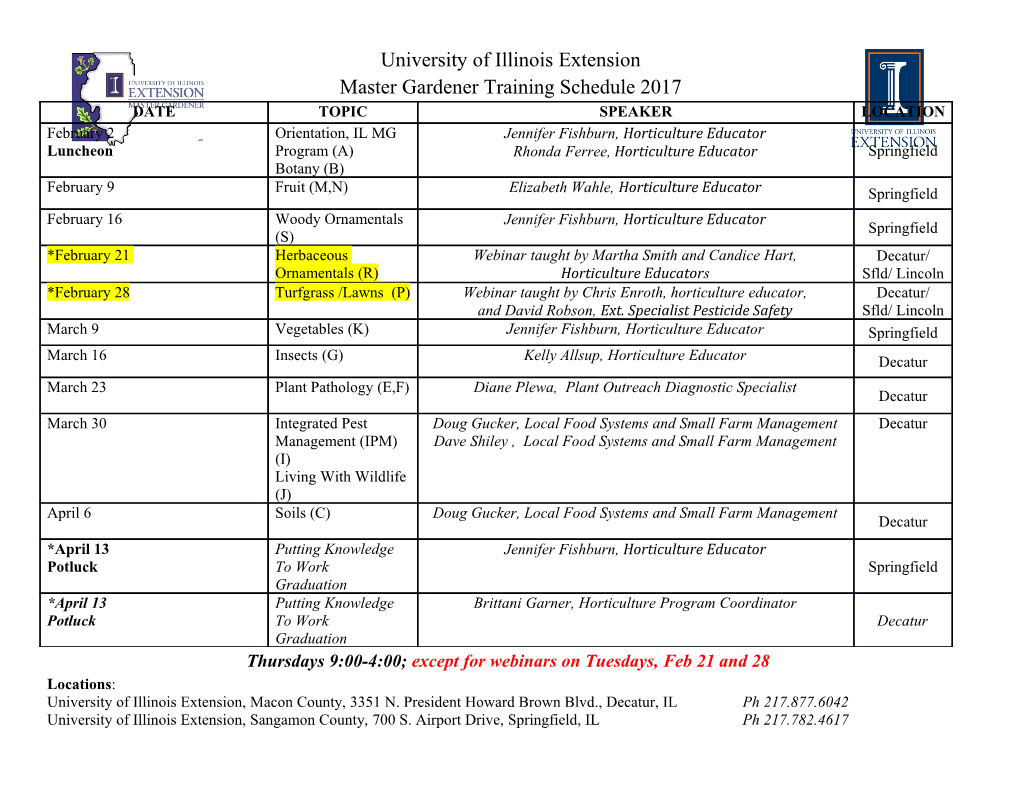
Applications Technical application notes on cell culture and fermentation 2 Table of Contents Cell culture Title Cell line Product Doc. Page Parallel CHO Cell Cultivation in Eppendorf BioBLU® c Single-Use BioBLU Single-use Vessels, CHO 355 6 Bioreactors DASbox Mini Bioreactor System Leachable Studies on Mammalian Cell Culture in BioBLU® Single-Use CHO, Vero BioBLU Single-use Vessels 308 12 Vessels Development of a Scale-Down Model for rAAV Viral Vector Production Sf-9 DASbox Mini Bioreactor System 303 18 Using a Sf9/BEV System Intelligent Control of Chinese Hamster Ovary (CHO) CellCulture Using CHO BioFlo 320 356 22 the BioFlo® 320 Bioprocess Control Station Perfusion CHO Cell Culture in a BioBLU® 5p Single-Use Packed-Bed CHO BioBLU 5p Single-Use Vessel 336 28 Vessel Pitched-Blade vs. Spin Filter vs. Packed-bed Basket: CHO Cell Culture CHO CelliGen 310 320 32 Comparison Growing CHO Cells in a New Brunswick™ CelliGen® BLU Benchtop, CHO BioBLU Single-Use Vessels 312 38 Stirred-Tank Bioreactor Using Single-use Vessels Single-use Scalability: Cho Cell Culture Using 5 to 50 L New CHO BioBLU Single-Use Vessels 257 42 Brunswick™ CelliGen® BLU Benchtop, Stirred-Tank Bioreactors CHO Cell Culture with Single-use New Brunswick™ CelliGen® BLU CHO BioBLU 5p Single-Use Vessel 254 48 Packed-Bed Fibra-Cel® Basket Cultivation of Human CAP® Cells: Evaluation of Scale-Down Capabilities BioBLU Single-use Vessels, CAP 291 52 Using Single-use Bioreactors DASbox Mini Bioreactor System Optimization of HEK293 Cell Culture in a New Brunswick™ CelliGen® HEK293 BioFlo/CelliGen 115 314 56 115 Bioreactor for the Production of Recombinant GPCR Hybridoma Culture Using New Brunswick™ CelliGen® 310 with Packed- Hybridoma CelliGen 310 258 60 bed Fibra-Cel® Basket Impeller Sf-9 Insect Cell Culture Using a New Brunswick™ CelliGen® 310 Sf-9 CelliGen 310 316 64 Bioreactor: Using Headspace Air Overlay for Reduced dCO2 Insect Cell Culture Using the New Brunswick™ BioFlo®/CelliGen® 115 Sf-9 BioFlo/CelliGen 115 256 68 Benchtop Fermentor/Bioreactor with Spin Filter Assembly An Update on the Advantages of Fibra-Cel® Disks for Cell Culture Various Fibra-Cel Disks 313 72 Taking the Strain (EBR, Spring 2014) Vero CelliGen 310, CelliGen 510 - 76 3 Stem cells Title Cell line Product Doc. Page Expansion of Human Bone Marrow-Derived Mesenchymal Stem Cells in BioBLU Single-Use Vessels, MSCs 305 82 BioBLU® 0.3c Single-Use Bioreactors DASbox Mini Bioreactor System Large-scale Production of Human Mesenchymal Stem Cells in BioBLU® MSCs BioBLU Single-Use Vessels 334 90 5c Single-use Vessels Scalable Expansion of Human Pluripotent Stem Cells in Eppendorf BioBLU Single-Use Vessels, iPSCs 292 102 BioBLU® 0.3 Single-use Bioreactors DASbox Mini Bioreactor System DASGIP Parallel Bioreactor Massively Expanding Stem Cell Suspensions (GEN, 2012) iPSCs - 106 Systems Stem Cell Expansion in Bioreactors (Infographic) MSCs - - 109 Fermentation Title Cell line Product Doc. Page Setup of a Microbial Hyaluronic Acid Production Process Using the S. zooepi- BioFlo 120 337 112 BioFlo® 120 Bioprocess Control Station demicus Push-Button Simplicity: Automatic Fermentation with the BioFlo® 120 E. coli BioFlo 120 310 116 Auto Culture Mode Transfer of an Itaconate Production Process in Ustilago maydis to the U. maydis BioFlo 120 309 122 BioFlo® 120 Bioprocess Control Station High-Density Escherichia coli Fermentation and Protein Production E. coli BioFlo 120 307 126 using the Eppendorf BioFlo® 120 Bioprocess Control Station Scale-Up of Escherichia coli Fermentation from Small Scale to Pilot DASGIP Parallel Bioreactor E. coli 306 132 Scale Using Eppendorf Fermentation Systems Systems, BioFlo 320, BioFlo 610 High-Density Fermentation of Corynebacterium glutamicum for C. DASGIP Parallel Bioreactor 304 140 Renewable Chemicals Production glutamicum Systems Production of Polyhydroxybutyrate from Lignocellulosic Hydrolysates— BioFlo/CelliGen 115, BioFlo Optimization of Bacillus sacchari Fermentation and Scale Up from 2 L to B. sacchari 302 146 610, BioFlo Pro 200 L Simulating Process Limitations in Microbial Cultivation: A Parallel Two- C. DASGIP Parallel Bioreactor 301 152 Compartment Scale-Down Approach glutamicum Systems The Eppendorf BioFlo® 320 Bioprocess Control Station: An Advanced E. coli BioFlo 320 340 158 System for High Density Escherichia coli Fermentation High Cell Density Fermentation of Escherichia coli Using the New E. coli BioFlo/CelliGen 115 335 164 Brunswick™ BioFlo® 115 Continuous Separation of E. coli Fermentation Broth Using a CEPA® LE E. coli CEPA LE Centrifuge 319 168 Laboratory Centrifuge System A Comparative Study: Small Scale E. coli Cultivation Using BioBLU® BioBLU f Single-use Vessels, E. coli 297 170 Single-use and Reusable Vessels DASbox Mini Bioreactor System High Cell Density E. coli Fermentation Using DASGIP® Parallel DASGIP Parallel Bioreactor E. coli 294 174 Bioreactor Systems Systems 4 Fermentation (continued) Title Cell line Product Doc. Page Scalability of Parallel E. coli Fermentations in BioBLU® f Single-use BioBLU f Single-use Vessels, E. coli 293 178 Bioreactors DASbox Mini Bioreactor System Amino Acid Fermentation: Evaluation of Scale-Down Capabilities Using E. coli DASbox Mini Bioreactor System 290 182 DASbox® Mini Bioreactors Process Development for Silage Inoculants – Optimization of Lactobacillus DASGIP Parallel Bioreactor 299 186 Lactobacillus sp. Fermentation with Parallel Bioreactor Systems sp. Systems Fed-Batch Biofuel Production Process Using a New Brunswick™ S. cerevisiae BioFlo/CelliGen 115 318 190 BioFlo® 115 Using Redox Measurements to Control Anaerobic Yeast Fermentation in S. cerevisiae BioFlo 310 317 194 a New Brunswick™ BioFlo® 310 Fermentor Anaerobic Yeast Fermentation for the Production of Ethanol in a New S. cerevisiae BioFlo 310 311 198 Brunswick™ BioFlo® 310 Fermentor Determination of k a Values of Single-Use Bioreactors (Summary of L - BioBLU f Single-Use Vessels - 202 DECHEMA report) Advanced software and automation Title Product Doc. Page DASbox Mini Bioreactor A Generic Biomass Soft Sensor and Its Application in Bioprocess Development 357 206 System, DASware control DASGIP Parallel Bioreactor A Quality-by-Design Approach to Upstream Bioprocess Interrogation and Intensification Systems, DASware control, 300 214 DASware analyze DASGIP Parallel Bioreactor Automated Bioreactor Sampling – Process Trigger Sampling for Enhancing Microbial Systems, DASware control, 298 220 Strain Characterization DASware analyze DASGIP Parallel Bioreactor Isobutanol from Renewable Feedstock - Process Optimization by Integration of Mass Systems, DASware control, 295 226 Spectrometry to Two 8-fold DASGIP® Parallel Bioreactor Systems DASware analyze Efficient Bioprocess Development (World Pharma, 2015) DASware control, DASware - 230 DASware design, DASbox Mini DoE Bioprocess Development (World Pharma, 2014) - 231 Bioreactor System Cell Culture APPLICATION NOTE No. 355 I May 2017 Parallel CHO Cell Cultivation in Eppendorf BioBLU® c Single-Use Bioreactors Katharina Blaschczok1, Sebastian Kleebank2, Ulrike Becken2, and Dieter Eibl1 1Zurich University of Applied Sciences, Wädenswil, Switzerland; 2Eppendorf Bioprocess Center, Jülich, Germany Corresponding author: [email protected] Abstract In industrial bioprocess development time and process runs in a DASbox® Mini Bioreactor System cost pressure is high. A promising strategy to equipped with BioBLU Single-Use Vessels. We reduce the development time is to combine parallel compared cell growth, viability, and the metabolic experimentation with the use of single-use equipment. profile in four parallel bioprocesses and found that In this study we cooperated with Dieter Eibl and his the processes developed highly similar. These results team at Zurich University of Applied Sciences (ZHAW) confirm the excellent suitability of this bioprocess to assess the reproducibility of parallel cell culture system for efficient process development. Introduction Bioprocess development aims at maximizing the yield and System equipped with BioBLU Single-Use Vessels perform the quality of the desired end product while minimizing comparably. To assess this, the Eibl team analyzed the costs. Numerous process variables exist, including cell growth and viability, and the metabolic profile in four the producer strain, the medium composition, the process parallel CHO cell processes. duration, the feeding strategy, and process parameters like temperature, pH, and DO. Researchers usually optimize many of them by empirical experimentation, which requires many process runs. Parallel bioprocess systems have the great advantage that multiple experimental parameters can be tested simultaneously in one run, which ensures maximal comparability between runs and saves precious time. The development time can be further reduced by the use of single-use bioreactors. With single-use equipment lengthy cleaning and sterilization procedures are omitted and the time between runs can be reduced. Fig. 1: DASbox Mini Bioreactor System equipped with The aim of this study was to test whether cell culture BioBLU 0.3c Single-Use Vessels. processes run in a parallel DASbox Mini Bioreactor APPLICATION NOTE I No. 355 I Page 7 Materials and Methods Bioprocess system and vessel Process parameters and cultivation procedure The researchers carried out the processes in BioBLU 0.3c Figure 2 illustrates the cultivation procedure and Table 1 Single-Use Vessels with a maximum working volume of summarizes the cultivation parameters. 250 mL. They controlled four vessels in parallel
Details
-
File Typepdf
-
Upload Time-
-
Content LanguagesEnglish
-
Upload UserAnonymous/Not logged-in
-
File Pages232 Page
-
File Size-