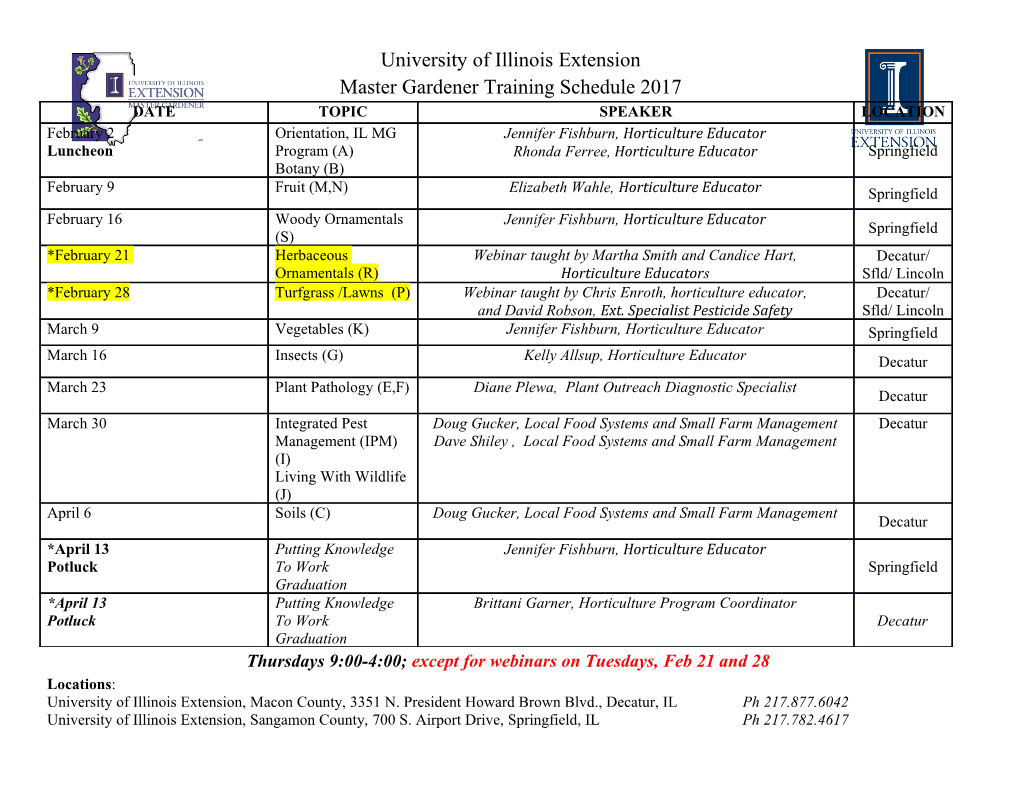
University of Nebraska - Lincoln DigitalCommons@University of Nebraska - Lincoln Biological Systems Engineering--Dissertations, Biological Systems Engineering Theses, and Student Research Spring 5-2015 Controller Area Network (CAN) Bus J1939 Data Acquisition Methods and Parameter Accuracy Assessment Using Nebraska Tractor Test Laboratory Data Samuel E. Marx University of Nebraska-Lincoln, [email protected] Follow this and additional works at: http://digitalcommons.unl.edu/biosysengdiss Part of the Bioresource and Agricultural Engineering Commons, and the Mechanical Engineering Commons Marx, Samuel E., "Controller Area Network (CAN) Bus J1939 Data Acquisition Methods and Parameter Accuracy Assessment Using Nebraska Tractor Test Laboratory Data" (2015). Biological Systems Engineering--Dissertations, Theses, and Student Research. 47. http://digitalcommons.unl.edu/biosysengdiss/47 This Article is brought to you for free and open access by the Biological Systems Engineering at DigitalCommons@University of Nebraska - Lincoln. It has been accepted for inclusion in Biological Systems Engineering--Dissertations, Theses, and Student Research by an authorized administrator of DigitalCommons@University of Nebraska - Lincoln. CONTROLLER AREA NETWORK (CAN) BUS J1939 DATA ACQUISITION METHODS AND PARAMETER ACCURACY ASSESSMENT USING NEBRASKA TRACTOR TEST LABORATORY DATA by Samuel E. Marx A THESIS Presented to the Faculty of The Graduate College at the University of Nebraska In Partial Fulfillment of Requirements For the Degree of Master of Science Major: Agricultural and Biological Systems Engineering Under the Supervision of Professor Joe D. Luck Lincoln, Nebraska May, 2015 CONTROLLER AREA NETWORK (CAN) BUS J1939 DATA ACQUISITION METHODS AND PARAMETER ACCURACY ASSESSMENT USING NEBRASKA TRACTOR TEST LABORATORY DATA Samuel E. Marx, M.S. University of Nebraska, 2015 Adviser: Joe D. Luck Electronics have become a standard in agricultural equipment and the trend of “smarter” equipment is on the rise. To have “smarter” equipment, a working knowledge of the accuracy of the data being transmitted throughout that equipment is needed. The controller area network (CAN) bus is the current interface to machine operation data transmitted between electronic control units (ECUs). Because CAN bus has been around for nearly thirty years, numerous devices have been created for interfacing with the bus. Choosing a device can be a challenge, especially without knowing if there are differences between the logging methods for true data representation. By logging simultaneously with three different methods, data was analyzed to determine if excessive error existed between logged datasets. Additionally because many messages are calculated (e.g., not measured directly), determining the accuracy of those messages can be important for management decisions or research studies. One calculated CAN bus message that holds a great deal of value is the engine fuel rate, and because it is calculated rather than measured, excessive error may exist in the CAN bus value. A comparison between the calculated CAN bus fuel rate message and a physically measured fuel rate provided information on the message accuracy. The Nebraska Tractor Test Laboratory (NTTL) has a certified fuel rate measuring system capable of ±0.5% accuracy (OECD, 2012; Wold, et al., 2015). Results showed that error between logging methods was quite low, however file size was an issue with some of the logging methods. Waveform file logging required only 6% memory space compared to the frame logging methods. Fuel rate as recorded from the CAN bus resulted in a ±5% error from physically measured fuel rates. Error for higher fuel rates within the torque curve were closer to ±1%. These results indicated that the fuel rate given by the CAN bus can indeed be used for management or research purposes. iv Dedication I would like to dedicate this book to all of the people who have supported and encouraged me throughout my life. I can guarantee that I wouldn’t be where I am now if was not for them. v Acknowledgements First and foremost, I must thank God for providing me with daily motivation to complete this project. Also a great deal of thanks to my wife for her constant support. I would also like to thank the Nebraska Tractor Test Laboratory, in particular the engineers of NTTL, Rodney Rohrer, Justin Geyer, Doug Triplett, and Brent Sampson. John Deere for allowing CAN bus collection during NTTL tests. Dustin Dam for aid in National Instruments setup and programming. Dr. Matt Darr at Iowa State University for aid in learning more about CAN bus at conferences as well as an arranged session at ISU for CAN training. Dr. Erin Blankenship for assistance with the statistical analysis and SAS programming. Finally thanks to Julie Thompson for always being around to help with anything needed. vi Table of Contents CHAPTER ONE: INTRODUCTION ............................................................................. 1 Electronics in Agriculture ............................................................................................ 1 CAN Bus Use in Agriculture ....................................................................................... 2 CAN Bus Data Logging in Agriculture ....................................................................... 2 CAN Bus...................................................................................................................... 3 SAE J1939 ................................................................................................................... 4 Engine Fuel Rate ......................................................................................................... 6 OBJECTIVES ...................................................................................................................... 6 CHAPTER TWO: COMPARING VARIOUS HARDWARE/SOFTWARE SOLUTIONS AND CONVERSION METHODS FOR CONTROLLER AREA NETWORK (CAN) BUS DATA COLLECTION .......................................................... 8 ABSTRACT ........................................................................................................................ 8 INTRODUCTION ................................................................................................................. 9 OBJECTIVES .................................................................................................................... 10 METHODS AND MATERIALS............................................................................................ 10 Test Setup .................................................................................................................. 11 Controller Area Network Interface ............................................................................ 12 Frame Data ................................................................................................................ 13 Waveform Data .......................................................................................................... 14 SAE J1939 Database ................................................................................................. 14 Data Collection Methods ........................................................................................... 14 Microsoft Excel Hex to Engineering Unit Conversion ............................................. 16 National Instruments Diadem Hex to Engineering Units Conversion ...................... 18 Frame Data Synchronization ..................................................................................... 19 Frame Data Re-Sample/Average ............................................................................... 20 Analysis ..................................................................................................................... 20 RESULTS ......................................................................................................................... 22 File Sizes.................................................................................................................... 22 Hex Data to Engineering Units .................................................................................. 23 Difference Between Logging Methods ...................................................................... 24 Synchronization ......................................................................................................... 26 CONCLUSIONS ................................................................................................................ 27 CHAPTER THREE: VALIDATION OF MACHINE CAN BUS J1939 FUEL RATE ACCURACY USING NEBRASKA TRACTOR TEST LABORATORY FUEL RATE DATA ................................................................................................................... 29 ABSTRACT ...................................................................................................................... 29 INTRODUCTION ............................................................................................................... 30 OBJECTIVES .................................................................................................................... 31 METHODS AND MATERIALS............................................................................................ 32 Test Setup .................................................................................................................. 32 CAN Bus Interface .................................................................................................... 33
Details
-
File Typepdf
-
Upload Time-
-
Content LanguagesEnglish
-
Upload UserAnonymous/Not logged-in
-
File Pages90 Page
-
File Size-