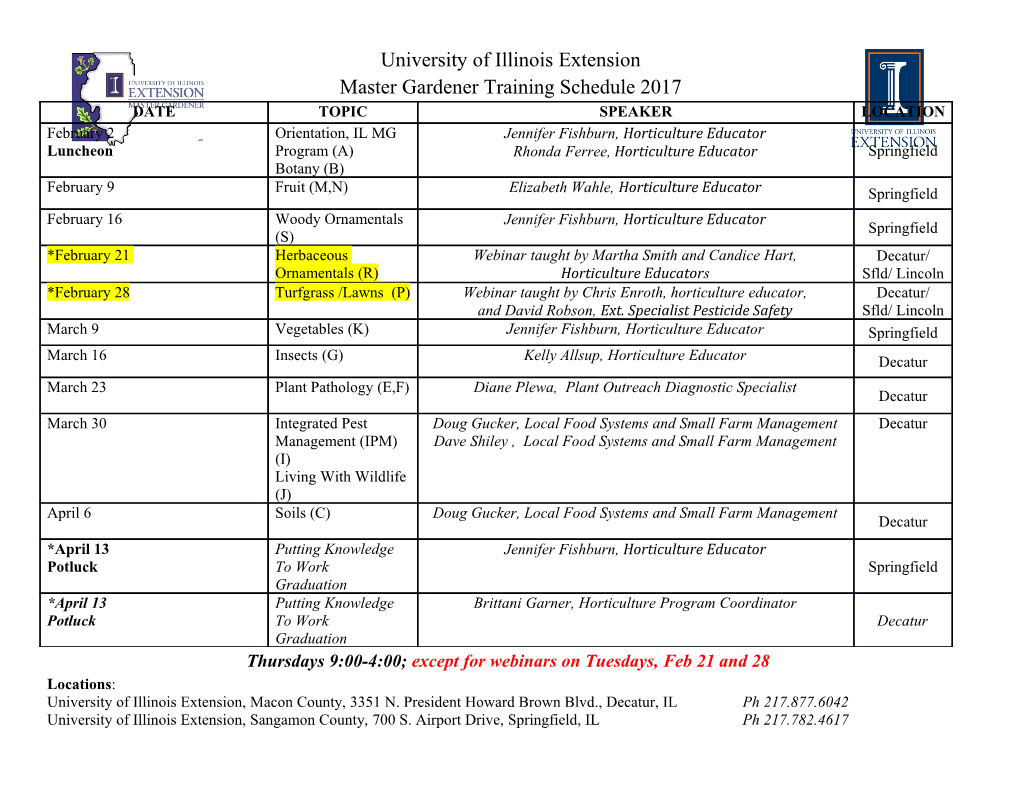
TUBULAR BIOREACTOR FOR HYDROGEN SULPHIDE REMOVAL FROM GEOTHERMAL POWER STATION COOLING WATER Rob Fullerton – Beca Ltd, New Zealand Taupo – North Island NZ Taupo Wairakei Wairakei Geothermal Power Station • Wairakei – one of earliest geothermal power stations in the world • commissioned 1958 – 1963, installed capacity 192MW • current capacity 157MW Cooling Water System . ~17 m3/s Waikato River water for direct condenser cooling A Station B Station CW in CW out CW = Cooling water Cooling Water System Geothermal steam 0.2m3/s Steam Turbines Cooling water + condensate Direct contact 17m3/s condensers 17.2m3/s Water pumps 157MW power Waikato River Waikato River The Challenge . H2S in the geothermal steam condenses into the cooling water and is discharged back to the river – aquatic impacts 3 . H2S concentration in discharge about 1000mg/m (~1mg/L) . Discharge Permit: H2S discharge to river ─ Prior 2012 : No consented limit - 10,000 kg/week ─ By 20 August 2012: 2,800 kg/week (72% reduction) ─ By 20 August 2016: 630 kg/week (94% reduction) . Requires sulphide reduction to ~50 mg/m3 The Challenge Geothermal steam containing H2S 0.2m3/s Cooling water Steam Turbines + condensate 17.2m3/s Direct contact 1000ppb H2S 17m3/s condensers To be reduced to 50ppb by Cooling water 2012 157MW power Waikato River Waikato River Sulphide Oxidising Bacteria - A Solution? • Need for strategy to control sulphide recognised • Thinking started in 2000 • SOB naturally occurring – esp. in geothermal areas • Biological sulphide oxidation - conversion of H2S to sulphate • SOB biofilm observed on existing outfall structure • Cooling water from power station 30 - 35oC, pH ~6, dissolved CO2 • Could SOB be used to achieve 95% sulphide removal? Initial Pilot Trials – 2000 - 2005 Algae overgrowth Sheets – channels - Pipes The Eureka Moment SOBs seem to grow best in fast moving flow Pilot Testing – Initial pipe trials Sulphide sampling • Biofilm established on inside of pipe – good H2S removal • High velocity prevents excessive biomass build-up • Lack of light prevents algal growth • Pipe bioreactor proved in concept Pilot Testing 2010 100mm dia. x 200m /150mm dia. X 400m SOB Biofilm Beginning section 100m End section 200m 100mm dia. x 200m results 150mm dia. x 400m results Sulphide Removal Model S = substrate concentration 푑푆 휇푚 퐵 푆 µ = maximum specific growth rate = m K = half-saturation constant 푑푡 푌 (퐾푠 + 푆) s B = biomass concentration Y = biomass yield • Sulphide concentration is low B >> S • biofilm quasi-steady state with constant thickness, viz. growth = detachment 푑푆 푆 dS/dt = rate of substrate change = −푣 v = maximum substrate utilisation rate 푑푡 푚 (퐾 + 푆) m 푠 ks = half saturation constant 2 • Calculate removal rate for each pipe segment (gH2S/m /d) • Fit to non-linear least squares Monod model Monod curve fitting 2 3 vm = 13.85 gH2S/m /d Ks = 235mg/m Design Curve Minimum pipe length ~160m +25% safety factor = 200m Pipe bioreactor - process concept 100mm dia. x 200m Outlet Velocity 0.8m/s sulphide Flow = 6.7L/s < 50ppb 100mm Sulphide oxidising bacteria biofilm Power station cooling water forms on pipe Inlet sulphide = 1000ppb inside surface Full scale pipe bioreactor concept plant Flow = 17m3/s ~2000 pipes x 200m in parallel 390km of pipe !! 200 x pipes per layer 10 layers Proposed sulphide treatment system 2012 Geothermal steam + H2S Pipe bioreactor Steam Turbines 17.2m3/s Direct contact 17m3/s condensers 4.2m3/s cooling 13m3/s 1000ppb water 50ppb H2S H2S 157MW power 2,800kg/week 17.2m3/s Waikato River Waikato River Proposed sulphide treatment system 2016 Geothermal steam + H2S 13.2m3/s 1000ppb H2S Pipe bioreactor Steam Turbines Direct contact 13m3/s condensers <80ppb H2S Cooling water 630kg/week 120MW power Waikato River Waikato River Full Scale design Challenges . Design began January 2011 . Never been done before – collaboration between contractor and designer . Physical constraints – high groundwater + hot (60oC) . Power station can’t stop – build off-line . Hydraulics – available head 1.5m – require pumping . Energy efficiency – design low head system . How to install 380km of 100mm dia. HDPE pipe Innovative “over – under” syphon 100m . Bioreactor pipe configuration ― 1890 pipes ― 5 banks of 378 pipes ― 42 pipes x 9 layers ― Magnetic flow meter each bank Bioreactor Layout Site Overview December 2011 Construction of pipe field . PE Pipe Design ─ Extruded on site ─ 100m lengths ─ No joints ─ 2.5mm wall ─ Embedded into weak cement matrix – “soilcrete” ─ 378km in 5 months Construction of pipe field Construction of pipe field Soilcrete embedment made from local pumice sand Construction of pipe field Construction of pipe field Return chamber – end pipe field Pump inlet channel Bioreactor outlet channel Bypass weir Bioreactor Performance Permit Compliance Full scale performance 3 . H2S concentration meeting target of >80% (~50mg/m ) . Power station meeting sulphide mass emission limit of 2,800 kg H2S/week . Optimisation of operating conditions to minimise power consumption . Current performance gives confidence to meet 2016 discharge limit of 630 kg H2S/week The world’s largest tubular bioreactor.
Details
-
File Typepdf
-
Upload Time-
-
Content LanguagesEnglish
-
Upload UserAnonymous/Not logged-in
-
File Pages39 Page
-
File Size-