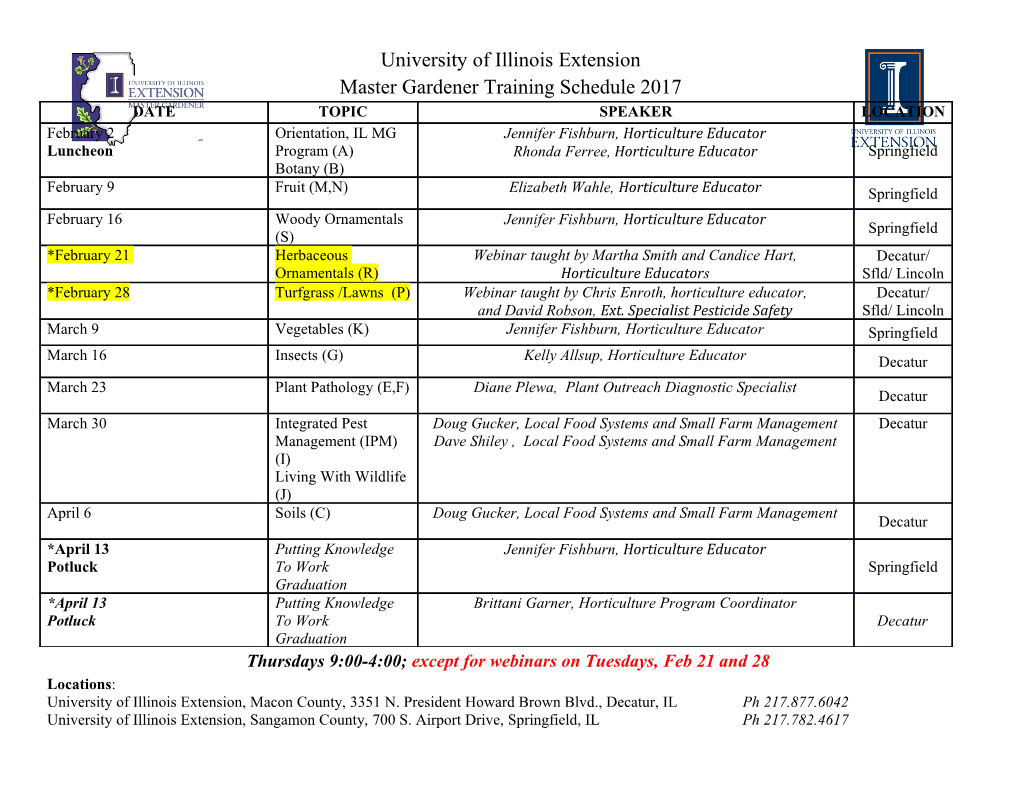
History of Steel Processing Andrew Ruble Department of Materials Science & Engineering University of Washington Seattle, WA 98195 Abstract Although primitive furnaces could make use of iron ore, early cast and wrought iron production methods were time consuming and unpredictable, since the chemistry was not well understood. The important chemistry behind iron processing lies with oxygen and carbon reducing iron ore, as well as oxygen removing solid carbon as a gas. As the landscape of steelmaking began to develop, these reactions were understood and utilized to develop processing methods that produced high quality steel in large amounts. Use of a blast furnace reduced the iron ore, and methods like puddling, the Bessemer process, the open-hearth furnace, and the basic oxygen process were used to manipulate the carbon and oxygen reactions to their advantage. Scrap steel could also be incorporated such as seen in an electric arc furnace. Module Objectives The objective of the module is to introduce methods of iron processing. The thought process and chemistry behind each method are shown to familiarize students with real world application of chemical reactions. Students will be able to discuss each processing method, how new methods improve the steelmaking process, and the chemistry behind each new method. Student Learning Objectives The student will be able to Recognize the chemistry necessary for iron processing Differentiate between iron processing methods Describe the current landscape of iron processing 1 MatEd Core Competencies Covered: 7. A Identify the General Nature of Metals 7.I Explain Causes for Differing Materials Properties 9.B Define and Describe Types and Properties of Cast Iron 17.B Describe Techniques used for Metals Processing Key Words: Iron, Steel, Processing Type: PowerPoint presentation with short online activity and class discussion Time required: one class period Suggested prerequisite: Iron and Steel: Properties and Application Target grade level: High School; also Introductory College/Technical School Equipment and Supplies Needed PowerPoint projection system Table of Contents: Abstract 1 Module Objectives 1 Student Learning Objectives 1 MatEd Core Competencies 2 Equipment and Supplies 2 Curriculum Overview 3 Module Procedure 6 Optional Student Activity 8 Supporting Materials 8 Acknowledgements 8 Evaluation 8 2 Curriculum Overview The history of iron processing, and therefore steel processing, demonstrates civilization’s demand for a versatile engineering material and the creativity of the engineers of the time. Iron’s high strength and ductility made it much more useful than the brittle materials of history such as wood and ceramic but required a greater scientific understanding and greater technology to implement. Early metallurgists did not understand phase relationships or even concepts of the atom, so processing iron ore was difficult. Small steps in understanding the chemistry led to new processes that allow control over the quality of iron and steel produced while maximizing quantity and quality. Early metallurgists were familiar with melting copper, so they attempted to melt the iron ore they found. The primitive furnaces, which could melt copper due to its low melting temperature of about 1100 degrees C (around 2000 degrees F), were not able to liquefy the iron ore, which melts just above 1500 degrees C (2700 degrees F). With enough time, however, in a charcoal furnace, iron ore would heat up to form a semi-malleable mass which could be hammered and shaped. This took a lot of time and energy, and the product was called wrought iron (wrought meaning worked). Impurities present were worked out by hammering although many still remained, leading to low performance and inconsistency among wrought iron pieces. Each piece needed to be worked individually, which was time consuming. This technique did not oust bronze as the leading metal of the day but it was a step towards the utilization of iron. The production of wrought iron is a great example of conceptual understanding coming much later than the discovery. Iron ore exists mostly as an oxide, Fe2O3, which is not suitable for any application, but when it is heated with charcoal (carbon) and air (oxygen), the iron ore and carbon monoxide reduce to form iron and carbon dioxide. This is the main reaction that was slowly understood over time by metallurgists and it is important to remember: 2C + 02 -> 2CO Fe203 + 3CO -> 2Fe + 3CO2 The reaction between the carbon C and oxygen gas O2 form carbon monoxide CO, which also produces a lot of heat. This is very important as it removes carbon from the iron by turning it into a gas. This carbon monoxide reacts with iron ore Fe2O3, reducing it to pure iron Fe and carbon dioxide CO2 as a gas. As furnace temperatures increased with advances in technology and chemistry, metallurgists were eventually able to fully melt iron to produce cast iron. Since the metal is molten, it can then be ‘cast’ into shapes. As you can see in the phase diagram below, the melting point of iron is lowered significantly as carbon content increases from – for pure iron to – at 4% C. The first cast iron was produced near this point, which allowed the early furnaces to melt it completely. However, once cooled, this material was brittle due to the 3 high carbon percentage. Often, the liquid metal was cast into manageable shapes, such as bars, to be remelted and processed separately from the furnace. This temporary state of the iron is known as pig iron, mostly characterized by its high carbon percentage. Figure 1: Phase diagram of iron and carbon. Notice the lowered melting temperature around 4% carbon. This processing of iron ore to pig iron was done using a blast furnace. The blast furnace is a tall cylindrical structure which utilizes a continuous process where a combination of iron ore and fuel (such as coke) are inserted into the top of a furnace while air is pumped in from the bottom. The air rises and reacts with the fuel, using the above reactions, reducing the iron ore. Molten iron then flows out the bottom, where it is cast into bars for pig iron. This process needs to be running continuously so blast furnaces often run for many years at a time, and are very difficult to stop and start. As pure oxygen became available, using pre-heated oxygen dramatically improved the pig iron quality and output. One technique for using pig iron was known as puddling. Since no more carbon needed to be added to the iron to decrease the melting temperature, a fuel source was ignited separately from the pig iron to avoid any more additions of carbon or other elements from the fuel to the iron. The heat was directed onto the pig iron, which was melted and combined with iron ore, creating the above combustion and reduction reactions, removing carbon and other contaminates. As the carbon was removed, the melting temperature of the iron increased, effectively solidifying iron with a lower carbon content. The iron 4 solidified into lumps which were extracted. This could be shaped into bars, creating a product similar to wrought iron but without the hammering. While there were a few early techniques for producing steel, none really worked until Henry Bessemer come up with his technique known as the Bessemer process in the 1850s. Bessemer created a process where air was bubbled up from the bottom through a vessel of molten iron. One might think that this would cool the iron, but the forced air was a better source of oxygen than adding iron ore (like puddling). The added oxygen removed the carbon impurities and created large amounts of heat, which would sustain high temperatures in the molten iron, allowing all the carbon to be removed. This new method took only about 20 minutes and completely revolutionized the steel industry, cutting the price of steel more than 75% and increasing steel production tremendously. This steel was very useful, but since the Bessemer process used air, the iron was exposed to nitrogen which caused steel to be somewhat brittle. A more advanced version of puddling used a new invention called the open hearth furnace, a furnace designed to reuse heat from escaping gas. Similar to puddling, the open hearth furnace was heated separately to avoid any contaminants but, instead of coke, used natural gas, which burns near 2000 degrees C to heat the furnace. Combining the new furnace design with gas allowed the furnace to reach and maintain high temperatures, easily melting pig iron and even scrap steel, which was starting to become prevalent. Once the steel was melted, the chemistry was altered until the desired composition was reached. Since the chemistry was carefully controlled, the operators did not need to wait for the iron to solidify, such as in puddling; the iron could be poured out immediately. Each batch took about 8 hours to complete. The open hearth furnace did not replace the Bessemer process, but complemented by using large amounts of scrap steel. When pure oxygen became commercially available, it replaced air in the Bessemer process and, along with some other improvements, became known as the basic oxygen process, and was widely used starting in the 1950s. Often, molten iron direct from the blast furnace could be used. In the basic oxygen process, high pressure oxygen is blown into the steel, either from the top or bottom, which removes carbon while also producing heat to keep the iron molten. Along with adding a few extras, such as limestone and magnesium to remove other impurities, this method produced very high quality steel, up to 350 tons in 40 minutes. Using mostly pig iron, the basic oxygen process did not allow use of large amounts of scrap steel. Some scrap could be used, but scrap was still mostly processed with the open hearth furnace.
Details
-
File Typepdf
-
Upload Time-
-
Content LanguagesEnglish
-
Upload UserAnonymous/Not logged-in
-
File Pages9 Page
-
File Size-