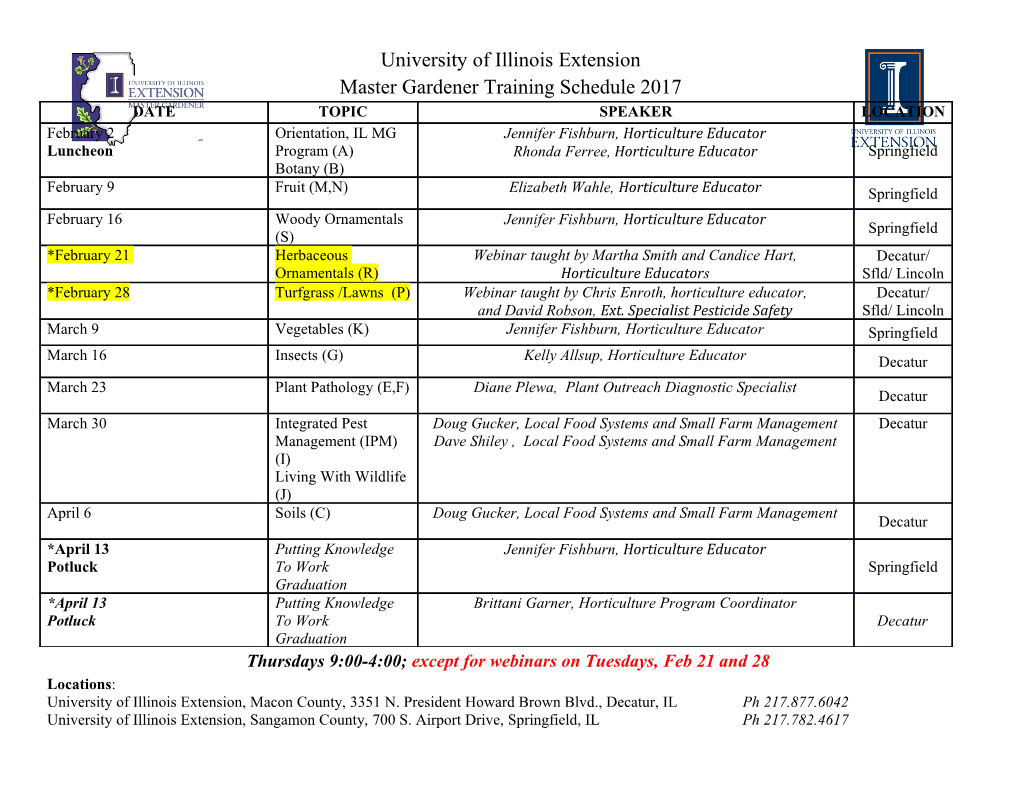
9th International DAAAM Baltic Conference "INDUSTRIAL ENGINEERING 24-26 April 2014, Tallinn, Estonia FINITE ELEMENT METHOD AND ITS USABLE APPLICATIONS IN WEAR MODELS DESIGN Sivitski, A; Põdra, P. Abstract: FEM models allow to perform Archard’s wear law, first published by more accurate calculations of contact Holm [3] and used for dimensionless wear strength and to predict the wear characters coefficient K calculation, was based on the of materials. The prognosis of material experimental observations and was initially behavior under load makes it possible to written in form: save resources and to abandon a trial-and- V F error method. The development of a FEM = K N , (1) model as well as operating with FEM s H programs is a complicated and time- consuming process. The skills of model where V is the volume wear (m3), s is simplification become more and more the sliding distance (m), FN is the normal important. The shape and the number of load (N) and H is the hardness (Pa). elements, moduli of elasticity of materials The more important wear parameter, wear and contact stiffness parameters should be depth h, is calculated by dividing both also considered. At this moment there is no sides of equation (1) by the apparent usable application for FEM models contact area: creation available for wear calculations. In this paper usable application for contact h = kps , (2) stress FEM calculations of coated bodies is offered, that can be used by engineers of where p is the normal contact pressure different areas. (Pa) over that particular discrete region, s Key words: Wear of materials; Coatings; is sliding distance (m), k = K/H is the FEM Hertz contact and Wear models dimensional wear coefficient (Pa-1). The Hertz elastic contact theory [4] has 1. INTRODUCTION widely been used for contact stress distribution calculations. However, Hertz Sliding wear is one of the most common contact model has assumptions, such as all wear types that takes place in different bodies are considered elastic, the contact mechanical contacts. It has been suggested between them is ellipse-shaped, frictionless that the dominant parameters that influence and non-conforming. the sliding wear rate are loading and For sphere on plane surface contact (see sliding parameters of contact [1,2]. The Fig.1) the contact radius r (m) can be given sliding law of contact is easily determined as: by mechanism kinematics. The calculation of contact stress in the sliding contact area, 3F R r = 3 N 1 , (3) defined by loading and the shapes of 4E* contact bodies, is more complicated process. According to the linear wear where R1 is the radius of sphere (m) and models, the volume wear directly depends E* is the normalized elasticity modulus on normal pressure in the contact. (Pa) defined by equation: 71 1 FEM program ANSYS Workbench 14.5 E* = , (4) 2 2 was used for Hertz contact model (1− µ1 ) (1− µ2 ) + calculations. The axisymmetric 2-D model E1 E2 was created to save the calculation time. The isotropic sphere had an axial modulus where E1, E2 and μ1, μ2 are the moduli of elasticity (Pa) and Poisson’s ratios of of elasticity (E1) of 200 GPa (steel) and a two contact bodies’ materials. Poisson’s ratio (μ1) of 0.3. The sphere was pressed vertically to the contact interface FN with a rigid counterbody – rigid plane R1 (plane surface). The modulus of elasticity of rigid plane (E2) was assumed to be +∞ and Poisson’s ratio (μ2) equals 0. After model geometry designed the mesh was configured (see Fig 2). The edge Fig.1. Sphere on plane surface contact. sizing function was used in the contact area to refine the mesh. The greater is the The normal contact pressure p distribution number of elements near contact the better is dependent on the contact radius r with the results will converge within appropriate -6 the maximum value pmax (Pa) in the center bounds. Contact element size of 5∙10 m of the contact area: was selected and number of elements was equal to 20787. This contact element size 3FN gives the most optimum normal contact pmax = 2 (5) 2πr pressure results accuracy along with acceptable duration of numerical The numerical method - finite element simulation and analysis. method (FEM) can be used as an alternative method for contact pressure determination. This method is useful for complex systems, when analytical solutions are not available. FEM is based on considering the bodies as sets of discrete elements and on finding approximate solutions to boundary value problems what is solutions to differential equations that satisfy these boundary conditions, of the elements. The use of Fig. 2. Mesh of the Hertz contact model. FEM together with appropriate wear To prevent the two surfaces from passing models is probably the only possible through each other, Augmented Lagrange method to be used for coated system wear contact formulation method was used. characteristics calculation. According to Augmented Lagrange method the higher is contact stiffness the lower is 2. FEM application for sphere-on-plane penetration [5]: contact model 2.1 Hertz contact model of uncoated FN = k N x p + λ , (6) contact where kN is contact normal stiffness Before making FEM simulations with (N/m), xp is surface penetration (m), λ is complicated coated system, Hertz contact an extra term (N) that makes this method model with the simple uncoated bodies less sensitive to the magnitude of the must be used in order to verify the FEM contact stiffness in comparison to model. Pure Penalty method [5]. For general bulk 72 deformation–dominated problems it is FKN FKN FKN recommended by ANSYS [5] to use the =1 =10 =100 Numerical normal contact normal contact stiffness factor (FKN). 899 1002 1020 FKN specifies a scaling factor for contact pressure pmax, (MPa) stiffness that is automatically calculated by Table 3. Numerical results of maximum ANSYS. The scaling factors are usually in normal contact pressure pmax, (MPa) for the range of FKN = (1...100) between different FKN values. sphere edge and rigid plane surface. The higher is the value of contact normal Figure 3 demonstrates the FEM stiffness, the more accurate is the result of distribution of normal contact pressure in FEM simulation. However, too high FKN the contact area if FKN = 10. values cause difficulties with convergence. Frictionless contact was selected for Hertz contact model as frictionless behaviour allows the bodies to slide relative to one another without any resistance [5]. Sphere was defined to be the contact body. Plane was defined as rigid target body. Finally the asymmetric behaviour of contact was specified. The asymmetric behaviour of contact means that only the contact surfaces are constrained from penetrating the target surfaces. The normal force of Fig. 3. Normal contact pressure distribution in Hertz contact (FKN = 10). FN = 1 N and sphere radius R1 = 0.003 m were used in FEM simulation. In tables 1 Result of the numerical simulation of and 2 the results of analytical and uncoated Hertz contact revealed that numerical contact radius and maximum optimal number of elements, element size normal contact pressure are presented. and contact normal stiffness values are Relative critical for normal contact pressure Analytical Numerical error (%) numerical calculations. Contact radius 0.0217 0.022 4.4 r, (mm) 2.2 Sphere–on–plane contact model for Table 1. Analytical and numerical results coated contact of contact radius r, (mm), FKN = 10. Hertz elastic contact theory formulae can Relative Analytical Numerical be applied only in case of uncoated error (%) systems. Experimental research is therefore Normal contact 987 (acc. to mostly used for coated systems wear pressure pmax, 1013 r value) 2.6 (MPa) 1002 characteristics analysis. Using FEM Table 2. Analytical and numerical results numerical method for coated bodies wear of maximum normal contact pressure pmax, simulation is therefore highly interesting. (MPa), FKN = 10. Although sliding wear is affected by many aspects, such as substrate and coating According to the ANSYS solution results, materials physical and chemical properties, the relative error of the normal contact sliding velocity, wear test duration, pressure numerical calculation is 2.6 %. temperature and humidity etc., the normal The optimal value of FKN = 10 was contact pressure associated with normal selected previously from a number of Hertz loading and contact bodies shapes is one of contact simulation results with different the most important parameters that should FKN values (see Table 3). be determined. The use of FEM numerical 73 simulations for coated systems contact properly explored. However some pressure prognosis helps to define the most researchers [9,10,11] have found that wear suitable coatings for different substrate resistance increases with modulus of materials. elasticity increase. Materials with a higher In this work coated sphere on rigid modulus of elasticity usually have higher uncoated plane contact model was done hardness. 6 with the coated sphere radius R1 = 0.003 m Previous experimental research [ ] revealed and the normal force FN = 1 N as before. that coatings with lower modulus of elasticity and E/H ratio like AlTiN have Substrate Hardness Modulus of lower dimensional coefficient of wear Substrate material H elasticity 3 type 1 (CoW) k (mm /Nm) on substrates with designation (HV) E (GPa) 1 higher modulus of elasticity (HM) (see SF CWTS Weartec™ 843 HV0.01 199 Table 6). PM CWTS Vanadis 6 843 HV0.01 210 NS 38CrMoAl8 850 HV0.01 300 TiCN/ TiCN/ AlTiN/ AlTiN/ H15 CWTS HM CWTS HM HM 1555 HV0.3 590 (WC-15Co) 1. CoW k -5 -5 3 2,2·10 - 7,6·10 Table 4. Mechanical properties of substrate (mm /Nm); - 2. CoW k materials. - 1·10-5 - 6,9·10-5 (mm3/Nm); Mechanical properties of investigated Table 6.
Details
-
File Typepdf
-
Upload Time-
-
Content LanguagesEnglish
-
Upload UserAnonymous/Not logged-in
-
File Pages6 Page
-
File Size-