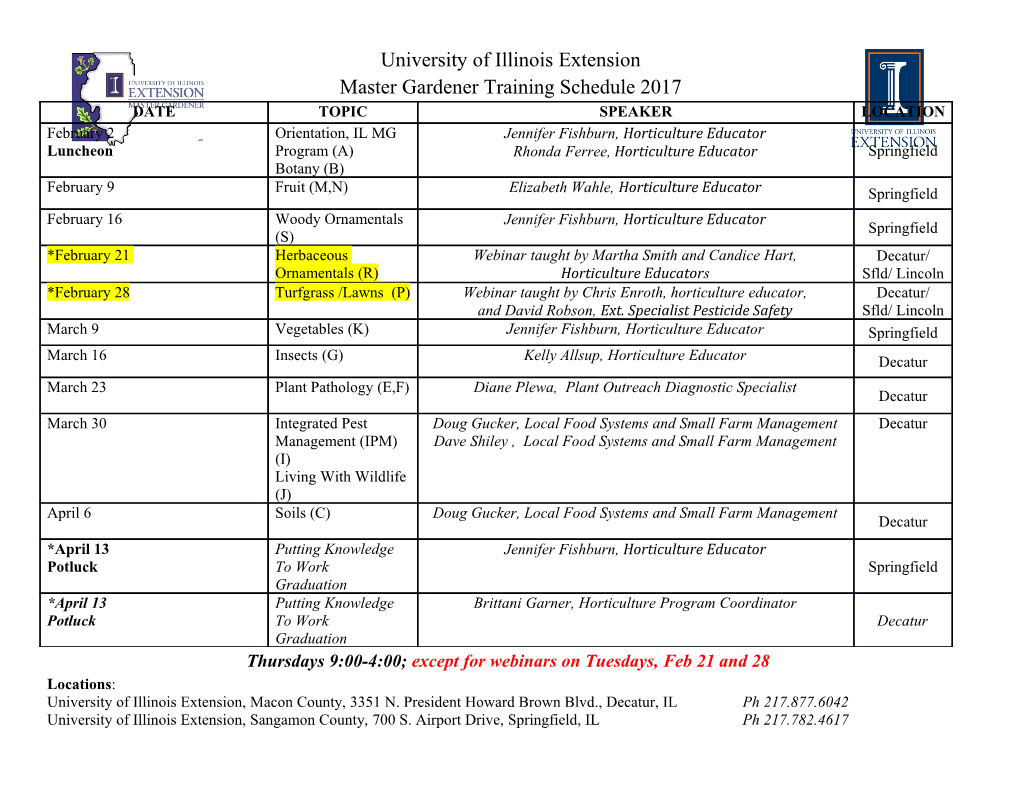
CORE Metadata, citation and similar papers at core.ac.uk Provided by Concordia University Research Repository Received July 17, 2018, accepted August 28, 2018, date of publication September 10, 2018, date of current version October 8, 2018. Digital Object Identifier 10.1109/ACCESS.2018.2869718 Modeling and Design Empirical Formulas of Microstrip Ridge Gap Waveguide ABDELMONIEM T. HASSAN 1, MOHAMED A. MOHARRAM HASSAN 1,2, (Member, IEEE), AND AHMED A. KISHK 1, (Fellow, IEEE) 1Electrical and Computer Engineering Department, Concordia University, Montreal, QC H4B 1R6, Canada 2Electronics and Electrical Communications Engineering Department, Cairo University, Giza 12613, Egypt Corresponding author: Abdelmoniem T. Hassan ([email protected]) ABSTRACT Recently, interest in the microstrip ridge gap waveguide (MRGW) has increased due to the need for a self-packaged and low-loss structures for millimeter-wave applications. The MRGW consists of a grounded textured surface, which is artificially representing a perfect magnetic conductor surface loaded with a thin low dielectric constant substrate with a printed strip. This is topped with another dielectric substrate covered with a conducting plate at the top as a ground plane. Currently, the full-wave and optimization tools are used to design the MRGW structure. Consequently, an efficient modeling and design tool for the MRGW is proposed in this paper via curve fitting. Closed form empirical expressions for the effective dielectric constant, characteristic impedance, and the dispersion effect are provided. The developed expressions are generalized for arbitrarily chosen MRGW parameters. The expressions are verified with the full-wave solution. The results show the potential of the proposed approach in modeling the MRGW structure INDEX TERMS Gap waveguide, RGW, microstrip, printed RGW, curve fitting. I. INTRODUCTION bottom sides and two rows of metallized via holes on the The millimeter-wave frequency band is a potential candi- left and right sides [9]. SIW provides the same advantages date for various 5G applications [1]. This requires high gain as the conventional metallic waveguide. However, this guid- antennas in an array arrangement with an efficient feeding ing structure suffers from dielectric losses, which can be of network. Typically, conventional waveguides are used to cre- concern at mm-wave frequancy range. ate a slot antenna array with low loss and high gain [2]. All the aforementioned limitations can be overcome, espe- However, at millimeter-wave (mm-wave) frequencies, feed- cially in the mm-wave range, by using gap waveguide ing network design becomes more complicated and diffi- technology introduced in [10]–[12]. The ridge gap waveg- cult to manufacture, especially to maintain the electrical uide (RGW) concept is based on an air gap sandwiched contact between the different metal parts [3], [4]. On the between two parallel plates, where most of the fields are con- other hand, planar microstrip technologies are also used for fined. The bottom plate has a smooth continuous metal (ridge) implementing antenna array feeding network due to its low surrounded by textured surfaces acting as an Artificial Mag- cost, compactness, and ease of manufacturing [5]. However, netic Conductor (AMC). A smooth metal plate covers the bot- dielectric and radiation losses [6], as well as the possibil- tom plate with an air gap, acting as the signal ground plane. ity of coupling to surface waves, limit the use of such The gap between these two parallel plates should be smaller technology [7] at mm-wave frequencies. Surface waves and than a quarter wavelength at the highest frequency over an the spurious radiation of the feeding network affect the radi- operation band to stop the waves over the textured surface ation characteristic of antenna arrays, such as the sidelobe and only allow it to propagate between the parallel plates. level and antenna gain. Moreover, the substrate integrated The main advantages of this technology are the alleviation of waveguide (SIW) is another guiding structure that was intro- dielectric and radiation losses, surface wave suppression and duced in [8] and has been used at mm-wave frequencies. resolving the electrical contact issue between the metal plates Basically, SIW resembles the waveguide technology in a at high frequencies. The AMC implementation has been real- printable format. Electromagnetic waves in SIW propagate ized using different approaches. It can be implemented using through the dielectric material with metal on the top and a metal pin (bed of nails) [13] or using mushroom patches 2169-3536 2018 IEEE. Translations and content mining are permitted for academic research only. 51002 Personal use is also permitted, but republication/redistribution requires IEEE permission. VOLUME 6, 2018 See http://www.ieee.org/publications_standards/publications/rights/index.html for more information. A. T. Hassan et al.: Modeling and Design Empirical Formulas of MRGW on microstrip substrate [14], which is referred to as printed expressions [26], [27], empirical expressions for the MRGW RGW (PRGW) [15]. are obtained. The analysis procedure of the MRGW is veri- Creating arbitrary circuits that have bends and discontinu- fied using structures in different scenarios. The main contri- ities is challenging in the RGW and PRGW configurations butions of this work can be summarized as follows: as this disturbs the bed of nails and mushroom periodicity. 1) proposing analysis and synthesis formulas for the This requires adjusting the nails or the mushroom positions. MRGW to facilitate the design process in Sec. II; To avoid such a problem, elevating the ridge away from 2) introducing general expressions for the effective dielec- the bed of nails or mushroom surface was proposed without tric constant and characteristic impedance for several the need to connect the ridge surface to the ground using a possible configurations of the MRGW in Sec II-A; thin low dielectric constant substrate. As such, the period- 3) demonstrating the validity of the proposed formulas for icity of the bed of nails or mushroom is not disturbed, and various cases of the MRGW in Sec. III; and the signal is propagating in the air-filled guiding structure. 4) considering the material dispersion at high frequency Also, the air gap can be filled with a dielectric. In this into the design formulas in Sec. IV. case, a printed circuit with all the needed discontinuities can be used with its ground and then flipped to face the periodic texture. Such a structure is referred to as inverted microstrip line as the signal is propagating in the dielectric substrate of the microstrip line. The inverted microstrip struc- ture is considered as packaged microstrip line [16], which was treated in several publications [17]–[21]. These are very FIGURE 1. Microstrip Ridge Gap Waveguide (MRGW) structure with complicated structures to be analyzed and designed due to the Electromagnetic Band Gap (EBG) mushroom with arrows indicate the interaction between the periodic structure and the microstrip field lines of the quasi-TEM mode. line. However, they have received more attention because of merging the advantages of the metallic waveguides in term of II. MRGW STRUCTURE AND MODELING low losses with the advantages of microstrip technologies in MRGW can be considered as a parallel plate waveguide filled terms of compact size and ease of fabrication. Hence, it can with air or dielectric with thickness d and permittivity r1, be a preferred candidate for feeding network design at the or a microstrip line with possible air substrate. The inner mm-wave frequency range. conductor surface of the microstrip line is the surface of Here, we will consider this structure in its general form the ridge. The microstrip line (ridge) is elevated above the where we consider the possibility of filling above and below AMC surface by a dielectric spacer that has permittivity r2 of the stripline with arbitrary dielectric materials, which will and thickness t. The geometry of the MRGW is presented be referred to as MRGW. One of the main obstacles to design in Fig. 1, which can be seen as an inverted microstrip line the MRGW is the absence of closed-form expressions to enclosed with an AMC. The electric field is mostly within calculate or synthesize the characteristic impedance and the the air gap. However, some of the fringing field lines will effective dielectric constant. Therefore, the design of these be in the substrate. As a consequence, the propagating mode lines and components such as power dividers, delay lines, is not a pure transverse electromagnetic mode (TEM), but and hybrids is based on numerical tools. In [22] a study with quasi-TEM. In addition, the substrate material underneath two 90◦ bends was conducted beside a quadruplet bandpass the ridge is nonmagnetic with unity relative magnetic per- filter design implemented using MRGW technology without meability (i.e., µ D1). An attractive advantage of MRGW using closed form expressions. Other work using MRGW configurations with an air gap is that the effective dielectric for antenna array design was implemented to provide high constant is much smaller than the spacer dielectric constant. gain using optimization tools [23]. Using optimization tools Therefore, the loss tangent is substantially reduced, and the is time-consuming, especially for antenna array design. The component dimensions can be increased, which gives more design time can be reduced if closed-form expressions are flexibility in the design at
Details
-
File Typepdf
-
Upload Time-
-
Content LanguagesEnglish
-
Upload UserAnonymous/Not logged-in
-
File Pages9 Page
-
File Size-