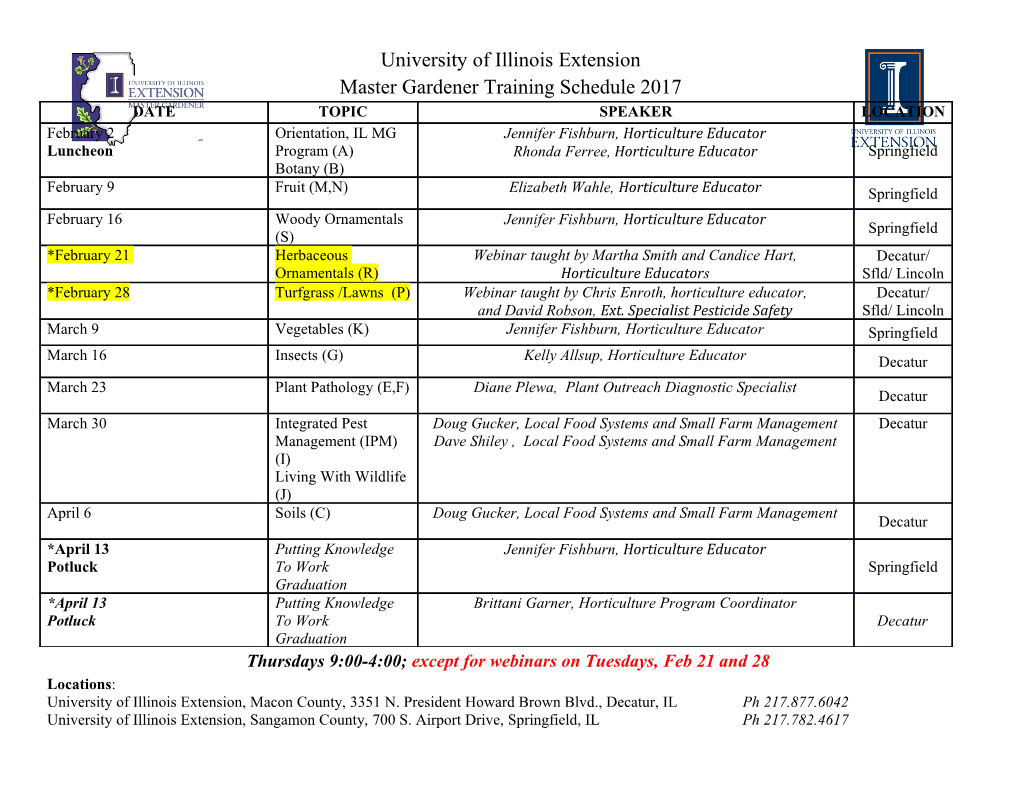
Journal of Power Sources 365 (2017) 408e418 Contents lists available at ScienceDirect Journal of Power Sources journal homepage: www.elsevier.com/locate/jpowsour Stall/surge dynamics of a multi-stage air compressor in response to a load transient of a hybrid solid oxide fuel cell-gas turbine system * Mohammad Ali Azizi, Jacob Brouwer Advanced Power and Energy Program, University of California, Irvine, USA highlights Dynamic operation of a hybrid solid oxide fuel cell gas turbine system was explored. Computational fluid dynamic simulations of a multi-stage compressor were accomplished. Stall/surge dynamics in response to a pressure perturbation were evaluated. The multi-stage radial compressor was found robust to the pressure dynamics studied. Air flow was maintained positive without entering into severe deep surge conditions. article info abstract Article history: A better understanding of turbulent unsteady flows in gas turbine systems is necessary to design and Received 14 August 2017 control compressors for hybrid fuel cell-gas turbine systems. Compressor stall/surge analysis for a 4 MW Accepted 4 September 2017 hybrid solid oxide fuel cell-gas turbine system for locomotive applications is performed based upon a 1.7 MW multi-stage air compressor. Control strategies are applied to prevent operation of the hybrid SOFC-GT beyond the stall/surge lines of the compressor. Computational fluid dynamics tools are used to Keywords: simulate the flow distribution and instabilities near the stall/surge line. The results show that a 1.7 MW Solid oxide fuel cell system compressor like that of a Kawasaki gas turbine is an appropriate choice among the industrial Hybrid fuel cell gas turbine Dynamic simulation compressors to be used in a 4 MW locomotive SOFC-GT with topping cycle design. The multi-stage radial fl Computational fluid dynamics design of the compressor enhances the ability of the compressor to maintain air ow rate during Surge/stall dynamics transient step-load changes. These transient step-load changes are exhibited in many potential appli- cations for SOFC/GT systems. The compressor provides sustained air flow rate during the mild stall/surge event that occurs due to the transient step-load change that is applied, indicating that this type of compressor is well-suited for this hybrid application. © 2017 Elsevier B.V. All rights reserved. 1. Introduction contained in fuel directly into electrical energy through electro- chemical reactions. SOFC power plants have been proven as an Climate change, air quality challenges, and limited fossil energy alternative power generation technology in electric utility appli- resource availability, have spurred the consideration of more en- cations and have been used in a variety of residential, commercial, ergy efficient and lower emitting energy conversion strategies for and industrial applications. These types of power generation plants stationary power plants. Existing power plant technologies include have also been evaluated and advanced theoretically in both loco- gas turbines, steam turbines, the very popular combined cycle that motive, stationary and unconventional applications [1e8]. SOFC includes both, and reciprocating engine power plants. Integrated systems have operated on various types of fuels such as CO, natural hybrid systems have the potential to operate at higher efficiency gas, hydrogen (H2), propane (C3H8) landfill gas, diesel and JP-8 than a fuel cell or gas turbine alone. Solid oxide fuel cells (SOFC) are [9e12]. SOFC power systems operate at higher temperatures than electrochemical devices that convert the chemical energy other types of fuel cells such as proton exchange membrane fuel cells (PEMFC), phosphoric acid fuel cells (PAFC) and molten car- bonate fuel cells (MCFC), which are also used widely in stationary * Corresponding author. and transportation (PEMFC only) applications [13,14]. E-mail address: [email protected] (J. Brouwer). Hybrid fuel cell-gas turbine (FC-GT) systems provide clean http://dx.doi.org/10.1016/j.jpowsour.2017.09.010 0378-7753/© 2017 Elsevier B.V. All rights reserved. M.A. Azizi, J. Brouwer / Journal of Power Sources 365 (2017) 408e418 409 energy at high efficiency [15]. The only turbo-machinery device compressor and the turbine, were challenging during the hybrid that has been previously tested for hybrid fuel cell-gas turbine system startup [23]. In that study, the compressor bleed air was systems has been micro gas turbine generator (MTG) technology. used to avoid the compressor surge during the hybrid system Previously, MTG technology has been demonstrated as integrated startup. Ferrari et al. designed and installed an SOFC-GT physical with a high temperature SOFC and MCFC. In a given size class FC-GT emulator in the framework of a European Integrated Project [24]. hybrid power systems posses the highest efficiency and lowest The focus of their study was to minimize the viscous pressure loss emissions of all fossil fueled power plants [16]. In the future, SOFC- in order to: 1) Reduce the unbalance between the compressor and GT hybrid systems are one of the most promising technologies for the expander, 2) Maintain an accurate measurement, and 3) Have meeting US Department of Energy (DOE) goals [17] for: 1) higher an effective plant efficiency. A modular high temperature volume energy efficiency, 2) lower environmental pollution, 3) electricity at was designed using computational fluid dynamics (CFD) tools to a competitive cost, and 4) integration with CO2 capture and achieve a high uniformity in the flow distribution inside the volume sequestration strategies. The potential for integration with coal and to minimize the pressure losses. The paper concluded that gasification and inherent CO2 separation advantages of high tem- surge occurred during the shutdown for a particular configuration. perature fuel cell systems make SOFC-GT systems attractive for In another study, strategies to avoid surge or excessive stress integrated gasification fuel cell (IGFC) power plants [18,19]. Some of during the start-up and shutdown phases were proposed [25], the hybrid fuel cell-gas turbine challenges that have been identified which lead to the finding that a new control strategy was required and investigated previously [20,21] include: compressor surge, for managing the valve responsible for controlling turbine inlet transient control, designing a proper heat engine for integration temperature during the hybrid system start-up and shutdown with the fuel cell, and difficulty of matching gas turbine's pressure emulation. McLarty et al. studied the dynamic operation of an ratio and mass flow rate with the SOFC pressure ratio and mass flow SOFC-GT topping cycle and showed that the pressurized hybrid rate. topping cycles exhibited increased stall/surge characteristics particularly during off-design operation [26,27]. In another study 2. Stall/surge in a compressor by McLarty et al. controls were utilized to mitigate the spatial temperature variation and the stall risk during load following [27]. Placing the fuel cell in the high pressure section between the The results showed that using the combined feed-forward, PI and compressor and turbine increases the fuel cell efficiency by cascade control strategy, 4:1 (SOFC) turn-down ratio could be increasing the reactant partial pressures and lowering some po- achieved and a 65% efficiency could be maintained. Stiller et al. larization effects. The topping cycle design that is used for dynamic suggested that specific incidents should be avoided for safe oper- simulations in this study, introduces the need for a pressure vessel ation of hybrid systems [28]. Some of these incidents are: of significant volume and increases the potential for compressor compressor stall/surge or cell degradation due to thermal cracking stall/surge. Under steady-state conditions the compressor supplies or high temperatures, carbon deposition and anode compartment a specific mass flow rate of air at every combination of shaft speed blocking, and backflow of gas from the burner to the anode, and pressure ratio. These values are typically normalized and exposing the anode to oxygen. In that study, a new control strategy compiled into tables or plotted in compressor maps. Compressor for managing the valve was used to generate the requested inlet performance in gas turbines is limited by two main lines that are temperature ramp during the hybrid system start-up and shut- typically plotted on compressor maps: 1) a choke line at high air down emulation. flow rate and, 2) a surge line at low air flow rate. The surge limit Roberts et al. have mentioned some important disturbances in depends upon the compressor design and system configuration and the hybrid carbonate fuel cell-gas turbine systems due to changes especially upon the pressure dynamics downstream of the in the ambient temperature, fuel flow variation induced by supply compressor. The dynamics of compressor surge/stall are signifi- pressure disturbances, fuel composition variability, and power de- cantly affected by introducing a fuel cell in the place of a combustor, mand fluctuations [29]. In that study, the predicted fuel cell oper- making it difficult to predict surge. Reaching the surge limit might ating temperature, fuel utilization, fuel cell and GT power, shaft reduce the compressor performance temporarily or permanently speed, compressor mass flow and temperatures in the cycle were and could introduce violent pressure and physical perturbations considered as the controlled response to the fuel cell voltage
Details
-
File Typepdf
-
Upload Time-
-
Content LanguagesEnglish
-
Upload UserAnonymous/Not logged-in
-
File Pages11 Page
-
File Size-