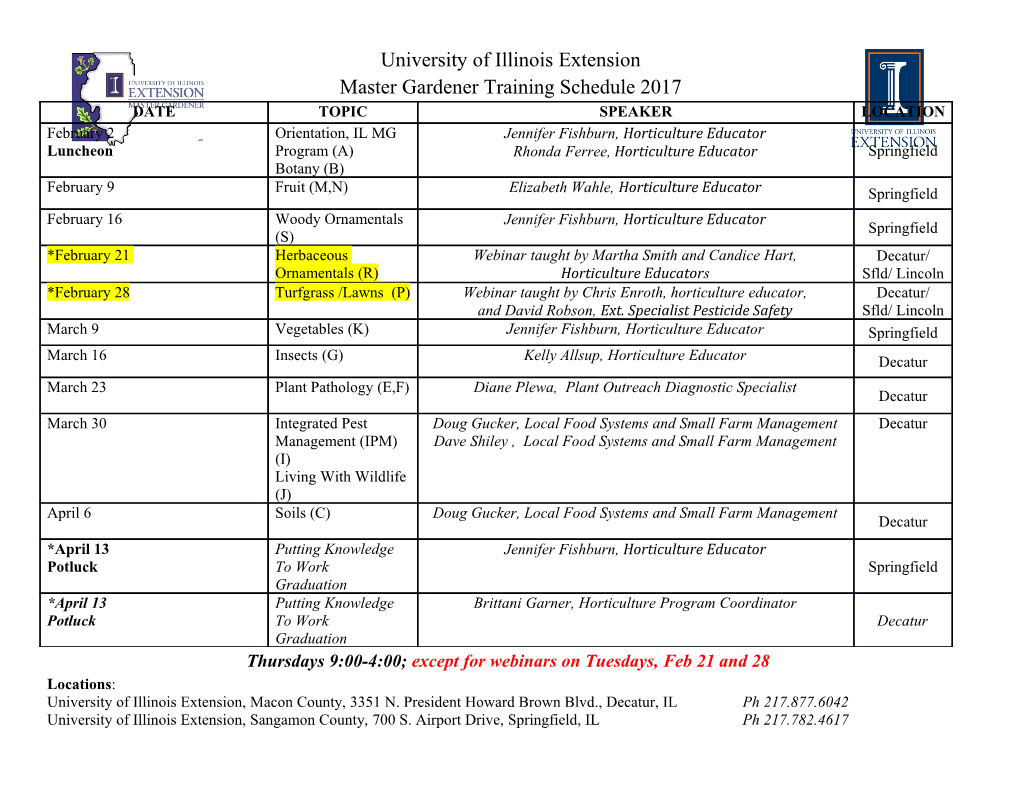
SOLDER MATERIAL SOLUTIONS PASTES • FLUXES • WIRES • ACCESSORIES CONTENTS Henkel's Global Solder Network ....................................................................................................................... 2 Henkel's Solder Portfolio ....................................................................................................................................3 Electronics Assembly Markets ........................................................................................................................... 4 Sustainable and Halogen-Free ...........................................................................................................................5 High-Reliability Alloy ......................................................................................................................................... 6 The Game Changers ........................................................................................................................................... 8 Industry Validation ............................................................................................................................................. 9 Solder Pastes ......................................................................................................................................................10 Liquid Fluxes ......................................................................................................................................................14 Alloys ..................................................................................................................................................................15 Solder Wires .......................................................................................................................................................16 Solder Accessories .............................................................................................................................................18 HENKEL'S GLOBAL SOLDER NETWORK Hemel Hempstead, Yantai, UK China Környe, Hungary Salisbury, Shanghai, North Carolina, China USA Irvine, California, USA Jejuri, India Ipoh, Malaysia Manaus, Singapore, Brazil Singapore Solder Manufacturing Solder Product Development and Technical Service 2 | Henkel's Global Solder Network HENKEL'S SOLDER PORTFOLIO With solder solutions that span diverse applications within numerous market sectors, Henkel is the solder technology market leader. A history of innovative formulations and market firsts – from high-reliability alloys to game-changing, temperature-stable solder pastes – continue to deliver the performance that electronics specialists require for today’s demanding assemblies. Materials development ingenuity is at the core of every Henkel LOCTITE® solder material – and has been for decades. Our multi-award-winning solder portfolio has earned the praise of industry experts and the trust of our customers. With a broad selection of solder pastes, cored and solid wires, liquid fluxes and multiple alloys, Henkel offers a total solution for current and future solder materials requirements. SOLDER MATERIALS Pastes Fluxes Wires Accessories Henkel's Solder Portfolio | 3 ELECTRONICS ASSEMBLY MARKETS When exceptional solder paste transfer efficiency is required for miniaturized devices within handheld applications, or, when uncompromising reliability and high-temperature stability are non-negotiable for automotive electronics, assembly experts turn to Henkel. Whatever the application – from smartphones to medical devices to LEDs to military/aerospace and more – Henkel’s broad solder portfolio delivers expansive choice and exceptional performance. MARKET PASTES FLUXES WIRES LOCTITE® HF 212 LOCTITE MF 300 LOCTITE C 400 Appliances LOCTITE LF 318 LOCTITE MF 390HR LOCTITE SWR SAC305 LOCTITE HF 212 LOCTITE MF 300 LOCTITE C 400 Automotive LOCTITE LF 318 LOCTITE MF 390HR LOCTITE SWR 90ISC LOCTITE GC 10 Computing / Servers LOCTITE HF 108 LOCTITE MF 300 LOCTITE C 400 LOCTITE HF 212 LOCTITE GC 10 LOCTITE MF 300 LOCTITE C 400 Handheld LOCTITE HF 200 LOCTITE MF 390HR LOCTITE SWR SAC305 LOCTITE HF 212 LOCTITE GC 10 LOCTITE C 400 LOCTITE MF 300 LED Lighting LOCTITE HF 212 LOCTITE SWR 90ISC LOCTITE MF R301 LOCTITE LF 318 LOCTITE SWR SAC305 LOCTITE GC 3W LOCTITE C 400 Medical LOCTITE HF 2W LOCTITE MF 390HR LOCTITE SWR SAC305 LOCTITE LF 318 LOCTITE HYDX LOCTITE GC 3W Military / Aerospace LOCTITE HYDX-20 LOCTITE SWR 90ISC LOCTITE HF 2W LOCTITE SWR SN63 LOCTITE GC 10 LOCTITE HYDX-20 Smart Meters LOCTITE GC 3W LOCTITE MF 210 LOCTITE C 400 LOCTITE HF 2W LOCTITE MF 300 LOCTITE CR 32 LOCTITE MF 300 LOCTITE C 400 Wireless Data Infrastructure LOCTITE HF 212 LOCTITE MF 390HR LOCTITE SWR SAC305 LOCTITE LF 318 LOCTITE MF R301 LOCTITE SWR SN63 90iSC high-reliability alloy recommended 4 | Electronics Assembly Markets SUSTAINABLE AND HALOGEN-FREE Embraced at the highest levels of Henkel Corporation, sustainability is central to the company’s philosophy. Creating more value for our customers, while reducing our environmental footprint, underpins all of Henkel’s development efforts. This sustainability strategy also extends to our solder program, which is informed by REACH halogen-free initiatives, RoHS compliance and EICC conflict-free tin raw materials sourcing. As one of the few – if not only – solder materials suppliers that is committed to formulating next-generation solder pastes with zero deliberately added halogens, Henkel sets the benchmark for environmental responsibility. gen- Free alo Sta H nd ts a e r e d s M B H a n s io e t d i in on ef IP D C 21) (IEC 61249-2- n Free oge Re gen Free R al qu lo eq H i a u s re H ir t m s e e t m e e e e n e M n t M s t s H H HALOGEN-FREE AND HALIDE-FREE COMPARISON HALOGEN-FREE HALIDE-FREE Drivers for REACH High-reliability solder interconnects with international standards Classification Non-Governmental Organizations (NGOs) No international halogens added to flux No flux corrosivity or dendritic growth detection Definition Complies with international standards (see below) Specific requirements to give ROL0 classification Test New O2 bond on flux Well-established quantitative halide test performed by IC Procedures Ion Chromatography (IC) on flux Copper mirror No penetration Bromine < 900 ppm JPCA-ES-01-1999 Silver chromate No discoloration Chlorine < 900 ppm Fluoride test No color change International IPC J-STD-004B, Chloride and bromide < 0.005% Standards Bromine 900 ppm max. IPC-TM-650 IEC 61249-2-21 Chlorine 900 ppm max. No pitting Total halogens 1,500 ppm max. Flux corrosion No color change Bromine 900 ppm max. Surface No discoloration IPC-401B Chlorine 900 ppm max. Insulation No dendritic growth Total halogens 1,500 ppm max. Resistance (SIR) No corrosion > 108 Ω Sustainable and Halogen-Free | 5 HIGH-RELIABILITY ALLOY A breakthrough in solder alloy development, Henkel’s high-reliability solder alloy, 90iSC, provides outstanding creep resistance by reducing failure rates due to vibration, drops, thermal cycling and thermal shock, while maintaining solderability and void levels over traditional SAC and SnPb solder. Developed with and globally accepted by the automotive industry, 90iSC is the world’s leading Pb-free, RoHS compliant solder alloy. 90iSC has exceptional performance in high-reliability applications. It is compatible with several Pb-free and halogen-free flux systems, ensuring adaptability for customized manufacturing requirements. The alloy is easily integrated into a wide range of flux technologies. CREEP AMBIENT 1 FAILURE MECHANISM HENKEL'S 90iSC SOLUTION [1] [2] 0.1 • 90iSC alloy shows improved creep resistance at ambient ) 1 - temperature over both SAC305 and SnPb (higher stress s • Creep resistance at a required to give equivalent creep). 0.01 specified temperature is • 90iSC shows improved creep resistance at 150°C over both directly linked to thermal ( STRAIN SAC305 and SnPb. cycle failure resistance. 0.001 • 90iSC has a similar plastic strain constant at 150°C, when compared to SnPb at 80°C. 0.0001 10 100 300 STRESS (Pa) 90iSC SAC305 SnPb 150°C 1 0.1 ) -1 s 0.01 STRAIN ( STRAIN 0.001 0.0001 5 10 100 STRESS (Pa) 90iSC SAC305 SnPb 6 | High-Reliability Alloy THERMAL CYCLING AND THERMAL SHOCK 220 FAILURE MECHANISM HENKEL'S 90iSC SOLUTION [1] [2] 200 180 160 • Thermal cycling causes • 90iSC alloy reduces electrical failures 140 140 stress to increase within the in comparison to SnPb in both -40°C soldered joint. to 150°C and -40°C to 125°C. 120 • Stress relief mechanism is • Under -40°C to 150°C, 90iSC has 100 crack propagation in the bulk similar electrical failure levels to SnPb 90iSC of the solder joint. at -40°C to 125°C. 80 THERMAL DELTA T (°C) T DELTA THERMAL • Thermal shock testing is a more extreme version of 60 thermal cycling. • 90iSC alloy has outperformed SnPb 100 1,000 10,000 and SAC alloys in thermal shock NUMBER OF THERMAL CYCLES TO 50% • The failure mechanism is crack testing. REDUCTION IN SOLDER JOINT STRENGTH propagation in the bulk of the 90iSC SAC305 SnPb solder joint and occurs earlier. SAC305 VIBRATION 72 FAILURE MECHANISM HENKEL'S 90iSC SOLUTION [1] [2] 62 • 20% of airborne failures 52 are attributed to vibrational a) [3] stress . • 90iSC alloy failure resistance is (MP • Failure mechanism is crack comparable to SnPb, but significantly 90iSC propagation along the better than both SAC305 and SnCu. 42 intermetallic compound (IMC) • 90iSC alloy returns the failure and in the bulk. AMPLITUDE STRESS NOMINAL resistance performance back to SnPb • SAC alloys have been
Details
-
File Typepdf
-
Upload Time-
-
Content LanguagesEnglish
-
Upload UserAnonymous/Not logged-in
-
File Pages20 Page
-
File Size-