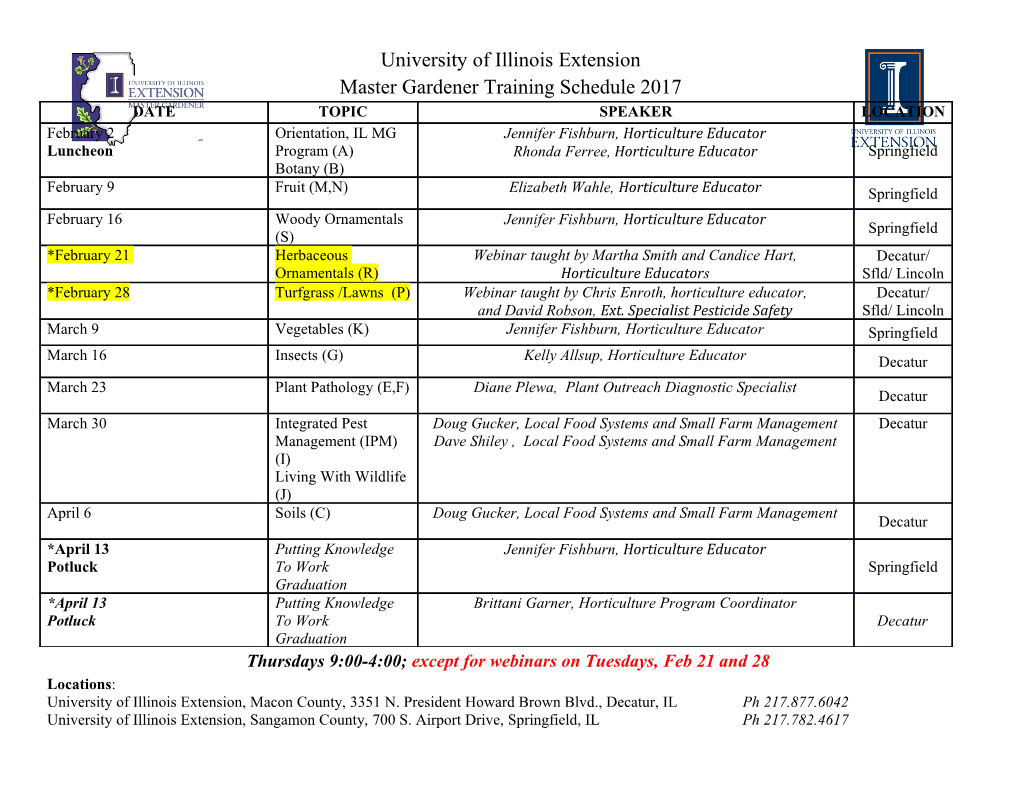
THERMAL DESIGN AND ANALYSIS OF CONCEPTUAL FLIGHT MODEL FOR A LUNAR EXPLORATION ROVER *Takuto Oikawa1, Toshiki Tanaka2, John Walker1, Kentaro Uno1, Paulo Costa3, Nathan Britton2, Kazuya Yoshida1 1 Tohoku University, Aoba 6-6-01, Aramaki, Aoba-ku, Sendai, Japan, E-mail: foikawa, john, unoken, [email protected] 2 ispace inc., Azabudai 3-1-6, Iikura katamachi Annex 601, Minato-ku, Tokyo, Japan, E-mail: ft-tanaka,[email protected] 3 Centro Federal de Educac¸ao˜ Tecnologica´ de Minas Gerais, Av. Amazonas, 5.253, Nova Suic¸a, Belo Horizonte, Minas Gerais, Brazil, E-mail: [email protected] Abstract Antennae Magnesium alloy Currently, Team HAKUTO is developing the Flight CFRP Body Model version of a lunar micro rover. This rover is de- Camera signed to operate during the lunar day to complete the Solar Panel Google Lunar XPRIZE mission requirement. Compared ULTEM to the previous rover iterations, we updated the rover’s Aluminum leg thermal and power performance by incorporating passive Wheel and thermal interface designs within the restricted dimension Motor and mass budget. As part of the qualification for space readiness, alternative Commercial Off-the-Shelf avion- ics are implemented to replace several Pre-Flight Model phase hardware. With the fusion of a new platform, we perform thermal simulation of the rover to justify its per- Figure 1. : Flight model lunar rover formance within the temperature tolerant range. materials and its interface design in preparation for FM 1 INTRODUCTION development. Based on the experimental results, we were able to identify needed improvements, where the temper- In recent years, space missions led by private ven- ature critical components (micro-controller, battery, etc.) tures have increased significantly. The currently ongoing required extra cooling in the projected lunar mission en- Google Lunar XPRIZE (GLXP) is a competition devel- vironment [4]. Various conceptual designs for potential oped as an incentive to promote low cost access to the FM thermal interfaces, based on the PFM experimental lunar surface, using an independent source outside of gov- results and lunar conditions, were conducted using trade ernment funds. As of 2016, there are 16 teams participat- studies [5]. A space system design approach introduced ing in the competition with HAKUTO as the sole Japanese by E.W. Hammond was used as a guideline to conduct de- team. HAKUTO is currently in the design phase of a sign tradeoffs in a clear and concise format to optimize the Flight Model (FM) lunar micro rover, codenamed Moon- design for maximum thermal performance [6]. raker, which we are planning to send to the Moon in the We present the underlying principle for the thermal second half of 2017 (Figure 1). Moonraker has undergone design using previous satellite development’s knowledge many phases of rover development since 2009 [1, 2]. It from Tohoku University on this paper [7]. As an ini- is built with space ready and heritage Commercial Off- tial step, a thermal model is developed, where the rover the-Shelf (COTS) hardware to minimize the development is broken into six different radiating surfaces. Based on and launch cost while increasing its reliability in a space the rovers orientation in reference to the solar radiative environment [3]. In an effort to improve the thermal flux, its surface temperature is determined. Other thermal performance, HAKUTO has developed an unique multi- inputs such as lunar radiation, solar albedo, and conduc- node passive thermal control system in order to use this tion from lunar regolith are also accounted for. By using hardware in the anticipated thermal lunar environment. such heat conditions, a feasible mounting location for the This research covers the thermal interface design of the avionics and the solar panel is determined to optimize the HAKUTO FM rover. rovers thermal performance while retaining its compact In a previous study, we conducted thermal vacuum size (∼4 kg). Once the avionics placement is fixed, the testing on a Pre-Flight Model (PFM) prototype of the lu- thermal isolation concept is studied to separate the radia- nar rover to verify the thermal performance of structural tive surfaces (avionics side) and heat absorbing surfaces (solar panel side). This design keeps the avionics cool using reflective radiative surfaces while isolating against the heat conduction from the solar power side, which is a common technique in satellite thermal control [8]. For this 71R :75 8 RV$8 paper, the final rover design configuration is discussed, Ί and further detailed analysis is conducted using simula- 78 R:7:` V` %J`1 V58 RV$8 tion software. Ή78 R:7 :` V` %J`1 V5 8RV$8 Έ78 R:7 :` V` %J`1 V5 R 8 RV$8 2 LUNAR ENVIRONMENTS AND ·78 R:7 :` V` %J`1 V5R 8 RV$8 CONDITIONS 2.1 Surface temperature model The lunar surface temperature is modeled by Hurley Figure 2. : Lunar surface temperature profile at 45 de- et.al. [9] using the dayside Diviner data [10]. The tem- grees latitude with the mission description perature model is represented in the equation below: n ◦ Tl( ) = 392cos ( ) > 130K ( < 90 ) (1) 2 Expected mission start time. 3 1 day elapsed after the mission start time. where is defined as the solar zenith angle between the 4 Expected mission end time. Moon-Sun line and the vector from the center of the Moon 5 The peak surface temperature on the Moon. to the point on the lunar surface, n is the power factor to shape the temperature profile in the lunar day, and 130 K From the mission timeline, we are concerned mainly is the temperature at the terminator between the day and with two factors regarding thermal performance: 1) the appropriate start time for the competition and 2) can the the night side. Furthermore, is rearranged into a time- ◦ variant function (t) to calculate the time of day in refer- rover operate through lunar mid day (81.5 ). As the ence to the sun’s position. Parameters such as the surface GLXP mission is expected to be completed in two days (assuming that the rover runs at 15 meters every hour), it temperature at a target lunar latitude (ϕlat), overall lunar is critical at a minimum to satisfy the rover’s performance inclination angle (ϕinc), and lunar synodic period (Tp) are introduced to formulate the relationship. requirement during the two-day time period. Most of the COTS hardware implemented into the rover is capable of withstanding lunar temperatures between 1.5 days after 2π − Tp (t) = t cos(ϕlat + ϕinc) (2) the sunrise and mid day. However, a detailed simulation is Tp 4 required to verify the rover’s thermal performance. As an n Hurley et. al. use = 0.25 to curve fit the function additional mission objective, we plan to explore the sky- close to the Diviner’s lunar temperature data [9]. How- light near Lacus Mortis during the science mission, and ever, this coefficient produce some significant tempera- survivability at mid day is critical to operate the rover for ture error between the model and the Diviner data. We an extensive period of time [1]. incorporate the proposed correction factor of n = 0.29 from Walker to reduce the error to within 10◦C accuracy between the temperature model function and the Diviner 2.3 Surface properties data [11]. This temperature curve holds true at a condi- Lunar surface thermal modeling requires three basic pa- ◦ tion of 45 latitude and between 25 hours after the sunrise rameters: albedo (b), solar absorptivity (α), and emissiv- and before the sunrise. The resulting temperature plot at ity (ϵ). Assuming that the terrain at the target site, La- ◦ 45 latitude is shown in Figure 2. cus Mortis, is covered with regolith, lunar albedo is de- Moon Fact Sheet 2.2 Mission milestone termined using NASA’s [12]. Using this value, lunar solar absorptivity is calculated, as shown in The mission for the HAKUTO rover at the Moon is sepa- Equation 3. Note that this equation is valid if the surface rated into two categories: the GLXP and the science mis- is opaque. sion. All of the missions are expected to be completed within a two-week timespan during the daytime. On the α + b = 1 (3) other hand, the lunar night side is not accounted into the mission as the rover is not expected to survive the extreme Lastly, emissivity is the ability of lunar surface to emit cold. Figure 2 shows the timeline of the rover’s activity on its heat via infrared energy. Since the emissivity differs by the Moon, where each mission stage description is shown the wavelength as emitted by spectral radiation, we chose below: a value of 0.9 as a good approximation due to the small 1 Expected landing time on the Moon. particle size of the lunar regolith mock up [13]. HAKUTO THERMAL ENVIRONMENT ON LUNAR SURFACE *No Convection ~T *No R~1 · R~2 R~1R δij convection cosγ = = 2 (5) Radiation (Q ) Solar Radiation (Q ) sp s kR~1k kR~2k kR~1k kR~2k Electronics (Qe) Using Equation 5, γ is calculated by taking the in- verse cos of the dot product operation. Finally, in some rover orientations, the sun vector does not face the rover’s Solar Albedo (Qa) surface (i.e. γ is determined as a negative value). To ac- count for this condition, Equation 6 is used. The sin of this value represents an effective view factor from the sun to the rover’s respective planar surface. Conduction (Q ) Surface Radiation (Qr) c ©HAKUTO ( 1 Space Robotics Lab γ; if γ≥ 0 Figure 3. : Thermal model and its corresponding heat γ = (6) input of the lunar rover 0; if γ< 0 3.2 Surface albedo (Qa) 3 THERMAL MODELING Thermal flux due to albedo (b) of solar radiation is deter- A general thermal model of lunar rover is described in mined by multiplying the albedo factor to Equation 4.
Details
-
File Typepdf
-
Upload Time-
-
Content LanguagesEnglish
-
Upload UserAnonymous/Not logged-in
-
File Pages8 Page
-
File Size-