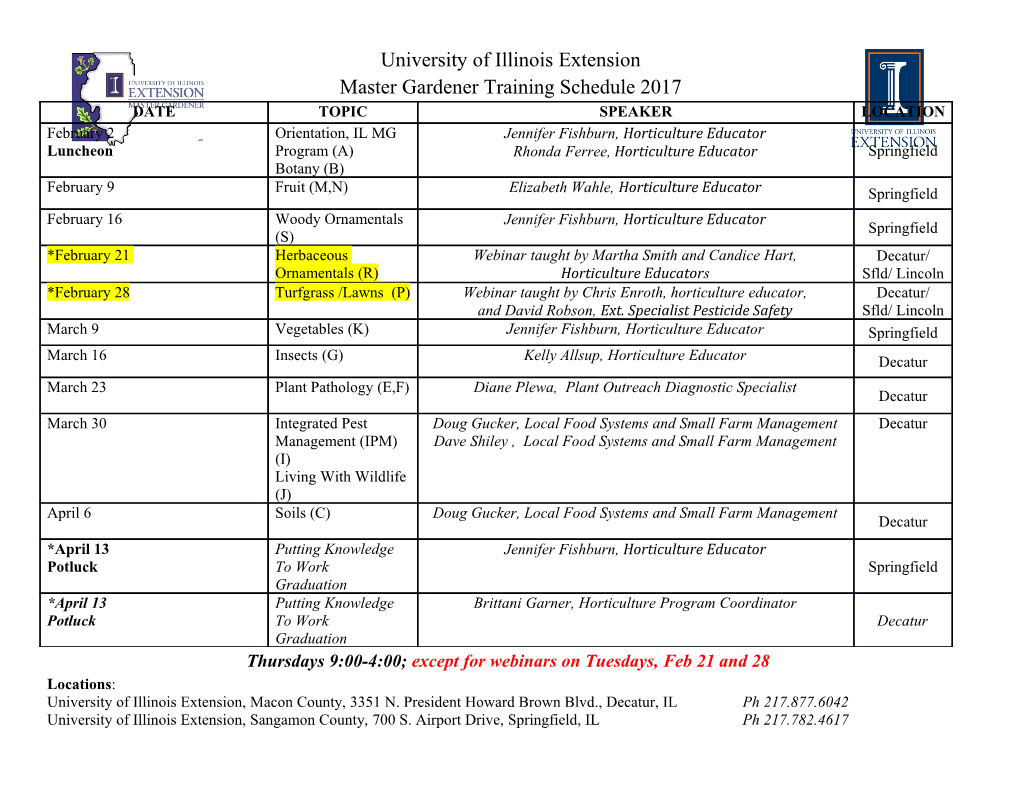
Predicting and Reducing Springback in Bending of an Aluminum Alloy and Selected Advanced High Strength Steels (AHSS) THESIS Presented in Partial Fulfillment of the Requirements for the Degree Master of Science in the Graduate School of The Ohio State University By Tanmay Gupta Graduate Program in Mechanical Engineering The Ohio State University 2019 Master's Examination Committee: Taylan Altan, Advisor Jerald Brevick Copyrighted by Tanmay Gupta 2019 Abstract Sheet metal forming or stamping is the process of shaping thin sheets of metal into a complex-shaped part. Part quality, which includes forming the part shape without any defects and within the required tolerances of the desired part geometry, is of major concern in the stamping industry. Major defects in sheet metal forming are splitting, wrinkling, and springback. The demand for improved safety and increased fuel efficiency in the automotive industry has led to an increased use of the Advanced High Strength Steels (AHSS) and high strength aluminum alloys. However, these high strength materials tend to exhibit low formability and higher springback compared to the conventional mild steels due to thinner gauges and higher strength. Springback significantly affects the dimensional accuracy of stamped parts and accurate prediction of springback in high strength materials becomes a challenge and necessity in the die design stage to reduce the die-recut costs. Springback occurs after stamping operation is completed and part is unloaded from the tools as a result of the elastic recovery of the deformed material. Material model defined in the finite element simulation affects the springback predicted after unloading the tools. Current mathematical models for springback prediction are complex and require material parameters which are costly and tedious to determine. Young’s modulus is one of the most significant parameter affecting the springback prediction. However, the accurate determination of E-modulus is a challenge due to its variation with plastic strain and non-linear elastic unloading behavior ii in AHSS. This study aims to develop a pragmatic approach for accurate determination of E-modulus variation with strain using in-house 4-point bending tests combined with the inverse analysis approach using commercial finite element codes (AutoForm and DEFORM). A similar approach done using wipe bending tests is also reviewed in this study and results from both the methods are compared and applied to real production part. Use of post-stretching to reduce springback is also investigated in the latter half of the study. Post-stretching using a variable blank holder force achieved via a servo hydraulic cushion to reduce springback and residual stresses in aluminum alloy is studied both experimentally and numerically. Finally, post-stretching using concept of “stake beads” is investigated numerically using AutoForm to see the effect of geometrical design of the beads on the forming forces and springback of the part. iii Acknowledgments I would like to thank my advisor, Dr. Taylan Altan, for providing me with continuous encouragement, support and inspiration. I am also grateful to Dr. Brevick for serving as member of my thesis committee. I wish to thank the sponsors of the following research: GM, Bowman, Hyson and the other CPF member companies, as well as all of the personnel of those companies which assisted me. I also thankful to my fellow colleagues at the Center for Precision Forming (CPF) – Ali Fallahiarezoodar, David Diaz-Infante Hernandez, Advaith Narayanan, Cliff Goertemiller Berk Aykas, Hitansh Singhal, Esmeray Ustunyagiz, and, Saul Hernandez for their assistance in my work. I also greatly appreciate Ms. Linda Anastasi for her administrative support. Lastly, I would like to thank my parents, for their enormous support and love throughout my journey. iv Vita 2012................................................................High School, Delhi Public School, Faridabad 2017................................................................B.E. (Hons.) Mechanical Engineering, BITS Pilani, Goa 2017................................................................M.Sc. (Hons.) Chemistry, BITS Pilani, Goa 2017 to present ..............................................Graduate Research Associate, Center for Precision Forming, The Ohio State University Publications 1. Tanmay Gupta, Ali Fallahiarezoodar, Ethan Mclaughlin, Dr. Taylan Altan (2018), R&D Update: Reducing springback in hat-shape bending with variable BHF using a servo-hydraulic cushion, Stamping Journal March/April 2018, Pg. 16-17 2. Tanmay Gupta, Ali Fallahiarezoodar, Dr. Taylan Altan (2018), R&D Update: Reducing springback using post-stretching with stake beads, Stamping Journal May/June 2018, Pg. 20-22 3. Fallahiarezoodar, A., Gupta, T., Goertemiller, C., & Altan, T. (2019). Residual stresses and springback reduction in U-channel drawing of Al5182-O by using a servo press and a servo hydraulic cushion. Production Engineering, 1-8. v Fields of Study Major Field: Mechanical Engineering vi Table of Contents Abstract ............................................................................................................................... ii Acknowledgments.............................................................................................................. iv Vita ...................................................................................................................................... v Publications ......................................................................................................................... v Fields of Study ................................................................................................................... vi Table of Contents .............................................................................................................. vii List of Tables .................................................................................................................... xii List of Figures .................................................................................................................. xiii Chapter 1: Introduction ...................................................................................................... 1 Background ..................................................................................................................... 1 Material Properties .......................................................................................................... 2 Bending ........................................................................................................................... 4 Springback ....................................................................................................................... 6 Chapter 2: Objective and Outline ....................................................................................... 8 Chapter 3: Review on determination of material properties and formability ..................... 9 Introduction ..................................................................................................................... 9 Tensile test..................................................................................................................... 10 vii Biaxial Bulge test .......................................................................................................... 14 Combined – tensile and bulge test - method for obtaining accurate flow stress data ... 16 Frictionless dome test .................................................................................................... 17 Chapter 4: Mechanics and Springback in Bending – A literature review ......................... 21 Introduction ................................................................................................................... 21 Fundamentals of bending and springback ..................................................................... 22 Mechanical properties affecting springback ................................................................. 25 Effect of Stress-strain data and Constitutive model on springback prediction ............. 26 Isotropic Hardening (IH) ............................................................................................... 28 Kinematic Hardening (KH) ........................................................................................... 30 Combined Isotropic and Kinematic Hardening (IH+KH) ............................................. 31 Effect of E-modulus ...................................................................................................... 33 Chapter 5: Effect of E-modulus Variation on Springback, Inverse Analysis Method and The Wipe Bending Test – A Review ................................................................................ 34 Introduction ................................................................................................................... 34 Effect of E-modulus on springback prediction ............................................................. 35 Nonlinear elastic unloading behavior ............................................................................ 37 Variation of elastic unloading modulus with plastic strain ........................................... 38 Strain path dependency of elastic unloading modulus .................................................. 39 viii Inverse analysis method for determination of an apparent E-modulus ......................... 39 Review on determination of
Details
-
File Typepdf
-
Upload Time-
-
Content LanguagesEnglish
-
Upload UserAnonymous/Not logged-in
-
File Pages122 Page
-
File Size-