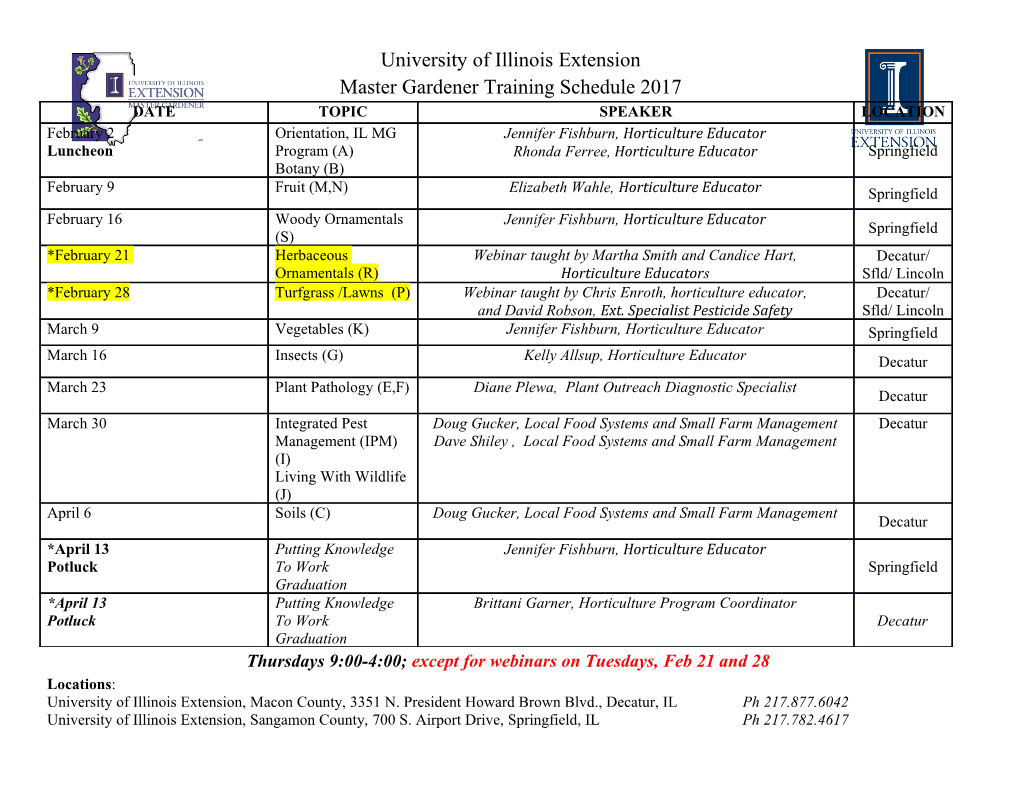
The Processes of Iron and Steel Making This page has been constructed to give the reader a more in-depth insight into the processes carried out at the Wortley Forges, associated and similar works. You will find some descriptions are duplicated on other pages in this site. Iron Mining The Bloomery Iron Making Process The Finery & Chafery Iron Making Process Iron Making by Blast Furnace The Puddling Process Making Cementation Steel Making Crucible Steel Making Bessemer Steel Making Steel by the Siemens Process Magazine Article explaining iron making Iron Mining The availability of Iron Ore was the key to the early iron industry. Even today (and more conspicuously up to the 1970s) a number of steelworks sites were directly a results of a furnace and later a works built were iron ore was available, although some sites are a result of water power, transport, fuel and other economic pressures. Iron is very common on the planet earth and the British Isles are no exception, however only where the iron content of the ore is quite high is the ore worth exploiting. This is one reason why almost all iron ore is now imported into the U.K. from the likes of Africa and Australia. It seems that iron ore was mined in many areas across the country, but these area progressively reduced as the demand increase and larger scale operations became more common. The important iron mining areas were to the south of Cumbria (near Barrow in Furnace), South Teeside, North Lincolnshire and a band across the midlands from Lincolnshire to Oxfordshire. Iron Ore, be worth working, must be high in Iron & Oxygen, but will also include such unwanted impurities as Phosphorus. Return to Top of Page The Bloomery Iron Making Process This is the process that started the Iron Age. It seems most likely that a lump of Iron Ore in a particularly hot fire lead to a strange material left in the embers of the fire. From this, the Bloomery Furnace developed, in this a mixture of Iron Ore and Charcoal was burnt with the help of a blast of air from hand worked bellows. The Output was typically a small lump of Wrought Iron of poor quality, but even this was enough to make an impact on history. Return to Top of Page The Finery & Chafery Iron Making Process Return to Top of Page Iron Making by Blast Furnace How the tower of the first Blast Furnace was developed may never be known but the associated process of iron making increase the volume of iron that could be smelted while also reducing the price. The first record of a Blast Furnace in the U.K. is in 1496. Early furnaces were best located on sloping ground, close to a reliable stream. Water was used to drive the early bellow to create the drought, while the slope helped to provide a near level roadway onto the top of the furnace. The key to the process is the removal of the oxygen from the iron ore at the same time as separating as many of the other impurities as possible. A blast furnace works on a continuous process lasting weeks, months, or in modern times, years and it will be assumed that the furnace is in the middle of a campaign and so the lighting the furnace (blowing in) can be ignored. Clean carbon (Charcoal or later Coke), Iron Ore and Limestone are added to the top of the furnace. Little and often is best as it has the least affect on the burning of the furnace. Also important is that the charge material is alternated (e.g.. Iron Ore, then Coke, then Limestone, and then more Iron Ore). At the top of the furnace the charge is heated and dried by the hot gases being blown through the furnace. Lower down, the iron ore melts as the carbon starts to burn and from just below the middle of the furnace, molten iron drips down through the remaining carbon fuel onto the hearth at the very bottom of the furnace. As there is insufficient oxygen in the air blast to properly burn the carbon fuel oxygen is captured from the iron ore, however, in spite of this, the majority of the gas produced is still Carbon Monoxide. In the lower part of the furnace, the limestone acts as a flux and draws together many impurities together into a layer of slag that floated onto of the molten iron. The molten iron and slag is drawn off periodically. The air blast is introduced a little way above the hearth and must be strong enough to stop the burning contents of the furnace stack dropping into the hearth, but must also not be so strong as to blow the contents out of the top. Until the introduction of the Blast Furnace cast iron had not existed and iron had never been seen as a liquid in any great volume. Since the start of the 18th Century the Blast Furnace has developed in a number of ways. Firstly Coke was introduced as a fuel in place of charcoal, allowing the size of furnace to be increase (charcoal would collapse under the extra weight from a large furnace). This was famously pioneered by Abraham Darby at Coalbrookdale in 1709 and was almost universal within 100 years, however a few charcoal furnace carried on until as late as 1921! Secondly the blast air was heated using heat recovered from the exhaust gases (energy conservation is not that new). Lastly, the Coke and Iron Ore are now mixed and heated, producing sinter, before they are charged into the furnace. Interestingly, you can tell from the texture and colour of the slag whether or not a furnace has had a hot or cold blast. Modern Blast Furnaces can be 35m (120ft) high, 14m (45ft) diameter and can produce 10,000 tons per day. The Iron produced by a Blast Furnace is always call 'Pig Iron'. The title of 'Cast Iron' is only generally used after the iron has been cast into a finished product. Early furnaces producing small quantities of iron could be used to cast products directly and some furnaces, such as Rockley Furnace, had casting pits for large items such as Cannon. With larger furnaces, all iron was cast into pigs and was remelted but from the 1850s molten iron was charged into other types of furnace, mixer or converter. Little if any iron is now cast into pigs in the U.K., as steel making plants are incorporated into the same works as the Blast Furnaces. Return to Top of Page The Puddling Process In 1784 Henry Cort devised a method of producing Wrought Iron from Cast Iron using a Coal fired Reverberatory Furnace. Solid Cast Iron was heated within an enclosed furnace. A Reverberatory Furnace is a long low structure built out of fire bricks. The coal fire was at one end with the hearth between the fire and the chimney. The hearth was slightly dished with a roof that directed the smoke and flame from the fire well above the iron. By keeping the smoke and flame above the iron, no carbon from the fire came in contact with the iron. Solid Pig (Cast) Iron was heated vigorously in the hearth until it was all molten. The fire was then damped down and the iron stirred so as to bring as much as possible in contact with the air. As wrought Iron has a higher melting point than Cast Iron, if the temperature in the furnace was correct the iron began to solidify as the carbon was removed. Eventually the Wrought Iron could be worked into a single lump of iron in the centre of the Hearth. Although in theory this was Wrought Iron it was not usable in this form because of the slag within the lump. For the Wrought Iron to be made usable, it was lifted from the furnace and forged using a 'Shingling Hammer'. Finally it was rolled into bars or sheet. As most of the slag was squeezed out of the iron under the Shingling Hammer this could be a dangerous job, with each drop of the hammer white hot slag would be strayed out across the forge. As the workmen had to hold and move the iron during the forging, there was no option other than for them to dress in heavy protective clothing. An improvement to Cort's puddling process came from Joseph Hall in 1816. Hall added mill scale (iron oxide formed and broken off during the forging and rolling) to the Cast Iron at the start of the Puddling process. Once the iron had melted, the carbon monoxide formed by the mill scale bubbled up through the iron giving the impression of boiling, thus the common name for this refinement 'Pig Boiling'. Return to Top of Page Making Cementation Steel Standard Wrought Iron bars were placed in the Cementation Furnace for conversion into Cementation or Blister Steel. The furnace was constructed from sandstone in the from of a large chest with a lid and was loaded with the iron bars placed in layers inter spaced with large quantities of high quality Charcoal. When fully loaded, the lid was put in place and mortar use to seal the chest. Heating was applied from a fire below the furnace where a coal fire was maintained from a pit. Heat was maintained for up to a week and a further week was taken for the chest to cool before being opened, emptied, and reloaded. The common design for cementation furnaces had two chests side by side with a fire hole in the centre of the two and the whole lot contained within a bottle shaped structure, similar to 'glass cones' and 'pottery kilns', that sheltered the furnaces from the weather and acted as a chimney.
Details
-
File Typepdf
-
Upload Time-
-
Content LanguagesEnglish
-
Upload UserAnonymous/Not logged-in
-
File Pages53 Page
-
File Size-