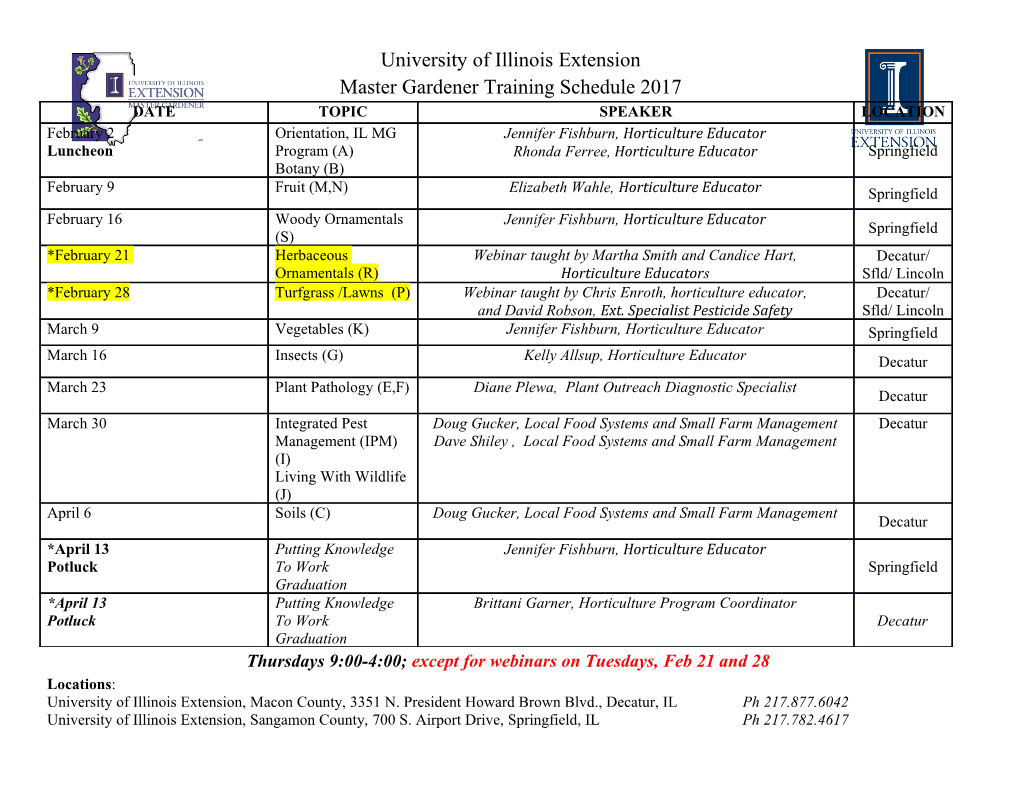
Europaisches Patentamt 19 European Patent Office Office europeen des brevets © Publication number: 0 497 907 B1 12 EUROPEAN PATENT SPECIFICATION @ Date of publication of patent specification © int. ci.5: C23C 16/30, C23C 16/44, 11.05.94 Bulletin 94/19 C07F 19/00 (21) Application number: 90917451.8 (22) Date of filing : 22.10.90 (86) International application number : PCT/US90/06051 @ International publication number : WO 91/06688 16.05.91 Gazette 91/11 (54) VAPOR DEPOSTION PROCESS FOR DEPOSITING AN ORGANO-METALLIC COMPOUND LAYER ON A SUBSTRATE. © Priority: 02.11.89 US 430397 (73) Proprietor : EASTMAN KODAK COMPANY 343 State Street Rochester New York 14650-2201 (US) (43) Date of publication of application 12.08.92 Bulletin 92/33 (72) Inventor : MIR, Jose, Manuel 1035 W. High Vista © Publication of the grant of the patent : Webster, NY 14580 (US) 11.05.94 Bulletin 94/19 Inventor : WERNBERG, Alex 201 Nob Hill Rochester, NY 14617 (US) @ Designated Contracting States : AT BE CH DE DK ES FR GB GR IT LI LU NL SE @ Representative : Parent, Yves et al Kodak-Pathe Departement Brevets et (56) References cited : Licences Centre de Recherches et de EP-A- 0 295 467 Technologie Zone Industrielle GB-A- 2 049 636 F-71102 Chalon-sur-Saone Cedex (FR) US-A- 4 262 630 Journal de Physique, Colloque C1, Supple- ment to vol. 43, no. 10, October 1982, Editions de Physique, Paris, FR, F. Maury et al.: "Raman spectroscopy characterization of polycrystalline GaP thin films grown by MO- CVD process using Et2Ga [-PET2J3 as only CO source", pages c1-347-cl-352 h- o o> Note : Within nine months from the publication of the mention of the grant of the European patent, any person may give notice to the European Patent Office of opposition to the European patent granted. Notice of opposition shall be filed in a written reasoned statement. It shall not be deemed to have been LU filed until the opposition fee has been paid (Art. 99(1) European patent convention). Jouve, 18, rue Saint-Denis, 75001 PARIS EP 0 497 907 B1 Description Technical Field 5 The present invention is directed to a process of producing a layer of a Group lll-V compound by vapor deposition. Background Art 10 All references to Periods and Groups within the Periodic Table of Elements are based on the format of the periodic table adopted by the American Chemical Society and published in the Chemical and Engineering News, Feb. 4, 1985, p. 26. In this form the prior numbering of the periods was retained, but the Roman numeral numbering of groups and designations of A and B groups (having opposite meanings in the U.S. and Europe) was replaced by a simple left to right 1 through 18 numbering of the groups. 15 Following the discovery of the transistor, semiconductor application interest focused on Group IV ele- ments, first primarily on germanium and then on silicon. It was later recognized that useful and, for many ap- plications, superior semiconductor properties are provided by lll-V compounds-that is, compounds consisting of Group III and Group V elements. This has led to intensive investigations of processes for preparing layers of lll-V compounds, particularly processes offering the stringent control of lll-V compound layer stoichiometry, 20 purity, uniformity, and thickness required for successful semiconductor applications. The most commonly employed approach for preparing lll-V compound layers is chemical vapor deposition (CVD), which includes both vapor phase epitaxy (VPE) and metalorganic chemical vapor deposit ion (MOCVD). Although extensively used, this process exhibits a number of disadvantages. First, there is the safety hazard of working with toxic gases. Second, each of the Group III element and Group V element compounds are pyr- 25 ophoric, reacting spontaneously with oxygen. Third, with the Group III and Group V elements being introduced as separate gases, the potential for layers which are stoichiometrically unbalanced in either the concentration of the Group III or Group V element is always present, and precise gas metering is required for balanced sto- ichiometry. In the MBE method a Group III element and a Group V element are introduced under high vacuum into a 30 reaction chamber and thermally reacted in the presence of a substrate. (For the MBE process, working with high vacuum equipment is time-consuming, cumbersome, and operationally limiting.) Constant et al U.S. Patent 4,250,205 discloses a variation on the CVD process described above in which vacuum is used to volatilize a precursor containing both the Group III and V elements. Instead of employing a gaseous compound of a Group III element and a gaseous compound of a Group V element as separate pre- 35 cursors for lll-V compound deposition, a single gaseous precursor is employed which is a coordination com- pound of one Group III element substituted with three volatilizable ligands and one Group V element substi- tuted with three volatilizable ligands. Such coordination compounds are also referred to in the art as lll-V donor acceptor complexes and as lll-V Lewis acid and Lewis base adducts. Constant et al teaches avoiding ligand elimination leading to polymeric compounds. Although the coordination compound approach offers better rep- 40 lication of ratios of III and V elements, and to some extent ameliorates problems of toxicity and oxygen sen- sitivity, the limitations of using toxic and pyrophoric materials in coating remain unabated. Zaouk et al, "Various Chemical Mechanisms for the Crystal Growth of lll-V Semiconductors Using Coor- dination Compounds as Starting Material in the MOCVD Process", Journal of Crystal Growth, Vol. 55, 1981, pp. 135-144 discloses a variation on the process of Constant et al wherein elimination of one ligand from each 45 of the III and V elements of the precursor is recognized to occur during heating. Maury et al, "Raman Spec- troscopy Characterization of Polycrystalline GaP Thin Films Grown by MO-CVD Process Using [Et2Ga-PEt2]3 As Only Source", Journal de Physique, Colloque CI, suppl. no. 10, vol. 43, Oct. 1982, pp. CI-347 to CI-352, is essentially cumulative with Constant et al and Zaouk et al, except for employing polymeric precursors as start- ing materials. Zaouk et al and Maury et al share the disadvantages of Comfort et al. 50 Davey U.S. Patent 4,427,714 describes forming lll-V compound layers by spraying. For example, gallium arsenade layers are disclosed to be formed by processes including (1) spraying a solution of gallium arsenide or a precursor thereof with an inert gas propellant in a reducing gaseous atmosphere; (2) spraying a solution of gallium/arsenic complex (each of the gallium and arsenic atoms having three 55 substituent ligands) with an inert gas propellant in an inert or reducing atmosphere; (3) creating a stable aerosol of trimethyl gallium dispersed in arsine, which is sprayed on a hot substrate; and (4) spraying a polymeric complex formed between trimethyl gallium and methyl or phenyl arsine. 2 EP 0 497 907 B1 GB-A-2 049 636 discloses a method of forming a thin film of chalcogenide by heating material to deposit on a substrate. All of the spraying processes are unattractive, since considerable unwanted deposition occurs on spray 5 confining walls. Thus, precursor waste and burdensome cleaning of equipment are encountered. It has been recognized that lll-V compound layers can be produced by supplying liquids to substrate sur- faces. Ladany et al U.S. Patent 3,802,967 discloses first forming a thin lll-V compound layer by CVD techni- ques and then increasing the thickness of this layer by conventional liquid phase epitaxy. For instance, in Ex- ample 1 a liquid consisting of 97 percent gallium, 2.99 percent gallium arsenide, and 0.01 percent tellurium is 10 flowed over a 1 0 micrometer CVD GaAs layer on a spinel substrate by tipping a graphite boat containing the liquid and substrate. The temperature of the liquid is maintained at 700°C. The Ladany et al process, since it begins with CVD, incurs all of the disadvantages of that process and, in addition, is unattractive in requiring very high temperatures for liquid phase epitaxy. Jensen U.S. Patent 4,594,264 discloses a process for preparing gallium arsenide layers on monocrystal- 15 line, gallium arsenide, or silicon substrates. A gallium-arsenic complex is employed of the formula (I) X3GaAsR3 where X is chlorine, bromine, iodine, phenyl, benzyl, methyl, or trifluoromethyl. and R is hydrogen, phenyl, benzyl, methyl, or trifluoromethyl. 20 The complex is dissolved in a hydrocarbon or chlorinated hydrocarbon solvent which is free of oxygen, sulfur, and nitrogen. The resulting solution is coated as a film on the substrate in an amount sufficient to form a gallium arsenide layer of from 1 to a few micrometers (urn) in thickness. The film is then heated to a tem- perature of less than 200°C to volatilize the solvent while avoiding decomposition of the gallium-arsenic com- plex. The next step of the process is to convert the complex coating remaining to gallium arsenide by exposing 25 the coating to ultraviolet (UV) radiation, such as the UV radiation from a laser. The presence of moisture and oxygen is avoided. All reactions were carried out under an inert, dry atmosphere (typically less than 1 ppm oxygen content) using purified, dry, oxygen-free solvents. Analysis of a layer produced from a complex of CI. 3GaAs(C6H5)3 revealed that it had lost only 70 percent of the carbon and 54 percent of the chlorine of its parent coating as measured prior to UV exposure. These residual carbon and chlorine levels are, of course, unac- 30 ceptably high for the majority of semiconductor uses.
Details
-
File Typepdf
-
Upload Time-
-
Content LanguagesEnglish
-
Upload UserAnonymous/Not logged-in
-
File Pages23 Page
-
File Size-