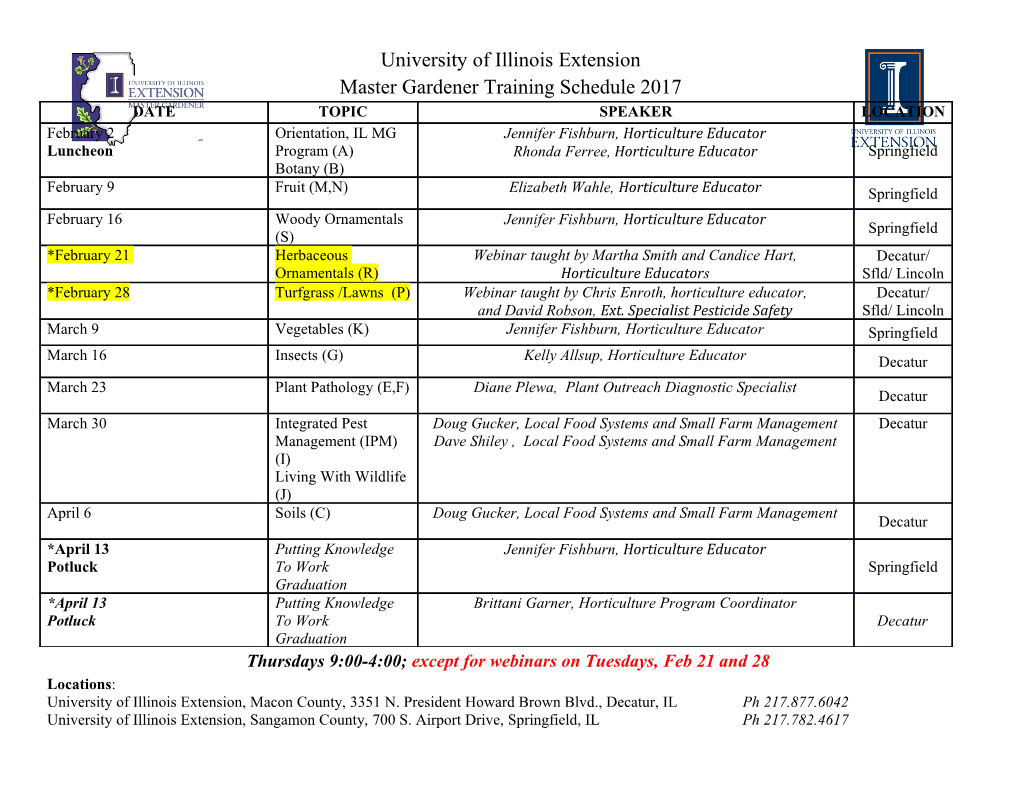
Safe Work Practices for Shipbreaking OSHA 3375-03 2010 Occupational Safety and Health Act of 1970 “To assure safe and healthful working conditions for working men and women; by authorizing en- forcement of the standards developed under the Act; by assisting and encouraging the States in their efforts to assure safe and healthful working conditions; by providing for research, information, education, and training in the field of occupational safety and health.” This publication provides a general overview of a particular standards-related topic. This publication does not alter or determine compliance responsibilities which are set forth in OSHA standards, and the Oc- cupational Safety and Health Act of 1970. More- over, because interpretations and enforcement policy may change over time, for additional guidance on OSHA compliance requirements, the reader should consult current administrative interpretations and decisions by the Occupational Safety and Health Review Commission and the courts. Material contained in this publication is in the public domain and may be reproduced, fully or partially, without permission. Source credit is requested but not required. This information will be made available to sensory impaired individuals upon request. Voice phone: (202) 693-1999; teletypewriter (TTY) number: 1-877- 889-5627. Safe Work Practices for Shipbreaking Occupational Safety and Health Administration U.S. Department of Labor OSHA 3375-03 2010 Cover photo courtesy of H. Reid, Metro Machine Incorporated. Photos courtesy of Metro Machine Incorporated Start to Finish This guidance document is not a standard or regulation, and it creates no new legal obligations. It contains recommendations as well as descriptions of mandatory safety and health standards. The recommendations are advisory in nature, informational in content, and are intended to assist employers in providing a safe and healthful workplace. The Occupational Safety and Health Act requires employers to comply with safety and health standards and regulations promulgated by OSHA or by a state with an OSHA-approved state plan. In addition, the Act’s General Duty Clause, Section 5(a)(1), requires employers to provide their employees with a workplace free from recognized hazards likely to cause death or serious physical harm. Occupational Safety and Health Administration 2 Contents Introduction 4 Lifesaving Materials 14 Interagency Work Group 4 Hazardous Material Spills 14 Steps in Shipbreaking Process 4 Energy Control 14 Initial Visit to Vessel to Determine Medical 15 Suitability for Scrapping 6 Worker Medical Qualifications 16 Towing the Vessel 7 Sanitation 16 Mooring the Vessel 7 Shipboard Rigging 16 Hauling the Vessel 8 Materials Handling 16 Planning 9 Crane Services 17 ForkTrucks 18 Breaking the Vessel 9 Trucks 18 Burning Equipment 10 Training 18 Cold Cutting 11 Communication 19 Mobile Hydraulic Shear Cutters 11 Shoreside Processing of Metals 11 Maintenance Shops 19 Fall Protection 11 References 20 Fire Prevention and Protection 12 Additional Resources 22 Emergency Response 13 OSHA Assistance 23 Drills 13 OSHA Regional Offices 25 Rescue 14 SAFEWORKPRACTICESFORSHIPBREAKING 3 Introduction Interagency Work Group Shipbreaking is a unique part of the maritime indus- In December 1996, the Department of the Navy, the try, primarily involving the dismantling and disposal Defense Logistics Agency (DLA), the U.S. Maritime of obsolete U.S. Navy and Maritime Administration Administration (MARAD), and the U.S. Coast Guard ships, as well as commercial barges and mobile off- (USCG), along with other involved agencies, began shore drilling units. For many years, much of this meeting quarterly to discuss shipbreaking program work was contracted to overseas companies. How- improvements and to share evaluation procedures ever, in recent years the exporting of ships from the and oversight information. In February 1998, the United States to foreign countries for scrapping has group was formally chartered as the Interagency come under criticism due to concerns over worker Panel on Ship Scrapping. The work of the group safety and health, and adverse environmental im- resulted in a set of recommendations that were pacts. As a result, the exporting of ships for scrap- presented in the April 20, 1998, Report of the Intera- ping was stopped by the Navy in December 1997 gency Panel on Ship Scrapping. The recommenda- and by the Maritime Administration (MARAD) in tions covered many aspects of the shipbreaking January 1998.1 Consequently, shipbreaking by do- industry, including contracting improvements, per- mestic companies is rapidly growing, and there is a formance bonds, data gathering and pilot projects, need to improve shipbreaking (e.g., dismantling, polychlorinated biphenyls (PCBs) guidance, regula- ship recycling, or scrapping) processes to ensure the tory oversight and international issues. safety and health of these workers. Under the category of regulatory oversight, the Dismantling of vessels is usually conducted at a panel recommended that the Environmental Protec- pier, drydock, or dismantling slip and includes a tion Agency (EPA) and OSHA, in conjunction with wide range of activities, from removing all gear and DLA, the U.S. Navy, and MARAD, develop a compre- equipment to cutting down and recycling the ship's hensive compliance guide. This guide, entitled A structure. The structural complexity of ships makes Guide for Ship Scrappers,3 outlines the relevant en- shipbreaking a challenging process. It involves vironmental and occupational safety and health re- many safety, health and environmental issues, in- quirements applicable to shipbreaking. The guide cluding exposure to asbestos, toxic fumes, haz- contains recommendations for completing ship- ardous materials, noise, falling objects, lead and breaking operations in a safe and environmentally electrical shock, as well as dangers associated with compliant manner. heat stress, falls, heavy materials handling and fires.2 In light of the need to improve and manage Steps in Shipbreaking the hazards associated with shipbreaking, this docu- Process ment is to be used as a basic guide for employers involved in shipbreaking activities. The hyperlinks to After removal from the fleet site, the vessel is towed OSHA, international, and other documentation pro- or self-propelled to the site where scrapping will vided throughout this publication give more detailed occur. The vessel is then scrapped while being information and recommendations. moored to a pier, anchored, beached, or dry-docked This document does not cover all of the regula- (including graving docks). Most scrapping is per- tions governing the occupational safety and health formed pier-side in slips, which are typically aspects of shipbreaking. However, it highlights im- dredged openings that are adjacent to a shipping portant information through references and hyper- channel. Slips are approximately 400 to 1,000 feet links to OSHA regulations that can be used to help long and 100 to 140 feet wide at the entrance. Ship- employers develop a comprehensive Safety and breaking is generally performed by cutting away Health Management System (SHMS), encompassing large sections, which are then moved to shore for all aspects of a facility’s shipbreaking procedures and further dismantling. A large winch at the head of the processes. The appropriate Code of Federal Regula- slip is used to drag the hull farther out of the water tions (CFR) provisions must be incorporated in all as work progresses. Throughout the scrapping safety and health plans, and the safety processes process, it is important for the appropriate safety and programs must be managed to reduce risk and precautions to be determined and followed to effec- provide a safe and healthful worksite for all workers. tively protect personnel. The scrapping process4 In addition, employers must be aware of and comply usually occurs in a series of steps: with all local and state regulations, which may be more stringent than federal requirements. Occupational Safety and Health Administration 4 • Conduct a vessel survey.5 Diagrams of all com- shore, the remaining ACMs and PCBs are re- partments, tanks and storage areas are used (or moved as they become accessible during the dis- prepared, if not available) to identify areas that mantling of the vessel section. The engine rooms may contain hazardous materials such as fuels, usually contain the most asbestos and, therefore, oils, asbestos, PCBs, lead and other hazardous take the longest for asbestos removal to be con- wastes. Sampling is conducted using a system- ducted. atic approach, usually starting in the compart- • Prepare surfaces for cutting. Following the re- ment that will be cut first. In many cases, a moval of combustible materials, asbestos and facility will presume that certain items contain PCBs, paint or preservative coatings must be hazardous materials and dispose of them as stripped from surfaces to be cut (29 CFR 1915.53). such, in lieu of sampling. In such cases, the em- Hard-to-remove materials on surfaces may re- ployer must use proper engineering controls and quire specific cut-line preparation, such as grit work practices to ensure that workers, involved blasting or flame removal of paint,7 which can with and in the vicinity of the removal, are prop- expose workers to toxic metals and volatile com- erly protected from exposure (e.g., through the ponents of paint. Appropriate precautions must use of wet methods, or wetting agents, and vacu- be taken (e.g., the use
Details
-
File Typepdf
-
Upload Time-
-
Content LanguagesEnglish
-
Upload UserAnonymous/Not logged-in
-
File Pages28 Page
-
File Size-