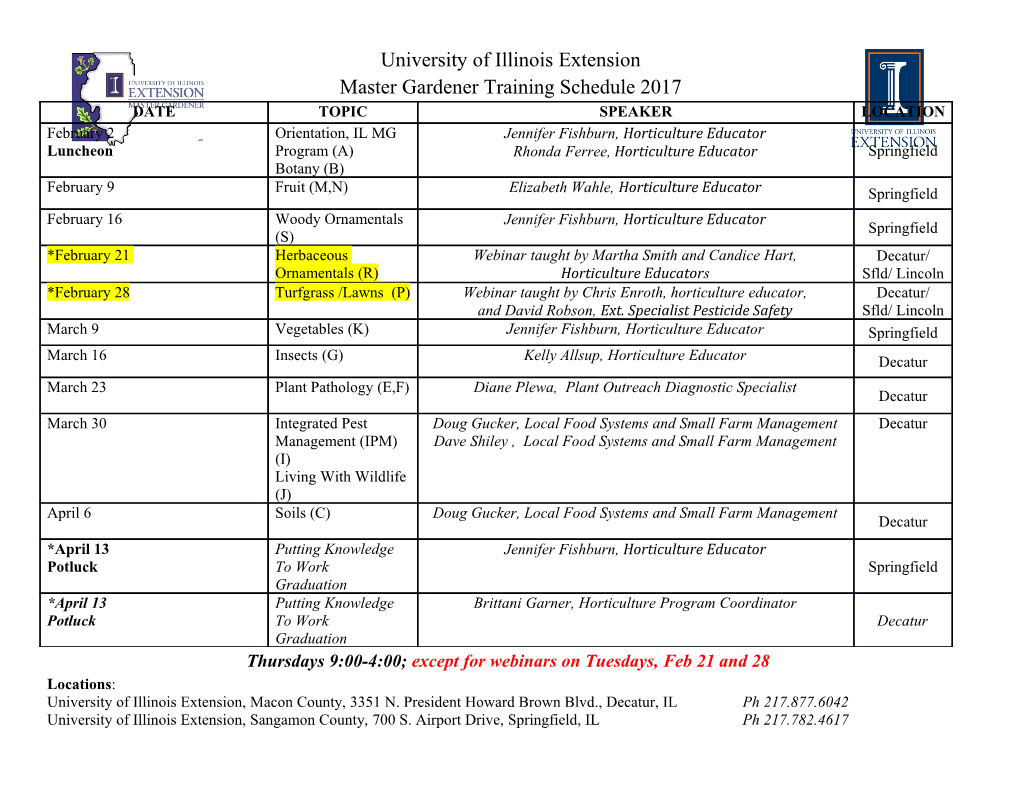
coatings Article The Performance Optimization of Oriented Strand Board Veneer Technology Xianqing Xiong 1,2,*, Qingru Ma 1 and Jie Ren 1 1 College of Furnishings and Industrial Design, Nanjing Forestry University, Nanjing 210037, China; [email protected] (Q.M.); [email protected] (J.R.) 2 Co-Innovation Center of Efficient Processing and Utilization of Forest Resources, Nanjing Forestry University, Nanjing 210037, China * Correspondence: [email protected] Received: 20 April 2020; Accepted: 25 May 2020; Published: 27 May 2020 Abstract: Oriented strand board (OSB) veneer technology and its performance have been widely studied in order to expand the range of OSB substrates. In this paper, OSB was a modified composite with boards as substrates, Myanmar old mahogany bark as the veneer material, and a cornstarch adhesive. Under such conditions, the optimal veneer technology was studied, and the index of the surface bonding strength and the veneer penetration rate were utilized in order to determine the performance. Two different processing technologies, cold pressing and hot pressing, were experimentally compared and hot pressing showed better performance. Subsequently, experiments were performed on the surface bonding strength and veneer penetration rate. The results show that the veneer performance of OSB is best when the unit pressure is 1.0 MPa, the hot-pressing temperature is 90 ◦C, and the hot-pressing time is 240 s. Furthermore, the magnitude of influence of the factors affecting the bonding strength is as follows: unit pressure > hot-pressing temperature > hot-pressing time. The research results have prospective significance for the performance optimization of OSB veneer technology. Keywords: oriented strand board (OSB) veneer technology; cornstarch adhesive; cold pressing; hot pressing 1. Introduction Poplar, eucalyptus, Chinese red pines, and other fast-growing species that are widely distributed in China are the main sources of OSB raw materials [1]. Meanwhile, OSB is widely utilized in fields, like packaging, construction, furniture manufacturing, etc., because of its characteristics, such as light weight, high strength, and water resistance [2]. However, in China, the OSB production cost is high, with poor product quality. Additionally, it lacks market competitiveness due to its low visibility, infrequent use as compared with plywood and particleboard, small production scale, and lack of state-of-the-art equipment in China [3]. Improving the availability of wood is the primary goal of the furniture manufacturing industry [4]. Researchers are making an effort to improve the original characteristics of wood [5–7]. Sandberg et al. [8] introduced an eco-friendly method, called Thermo-Hydro-Mechanical (THM) treatment, which combines the use of temperature, moisture, and mechanical action. They claimed that THM treatment can improve the intrinsic properties of wood. New materials could be produced and the new functionality that is desired by engineers could be achieved without changing its eco-friendly characteristics. Furthermore, Sandberg et al. [9] studied the effect of this method on reducing the damage that is caused by veneer stretching and buckling. Coatings 2020, 10, 511; doi:10.3390/coatings10060511 www.mdpi.com/journal/coatings Coatings 2020, 10, 511 2 of 11 There are many types of OSB, of which bamboo-oriented strand board (BOSB) is widely studied [10]. Fu et al. [11] used bamboo from Hunan province (Phyllostachys pubescens) as a material for developing BOSB and explored the best process conditions for manufacturing BOSB. Sun et al. [12] compared two types of BOSB with different orientation distributions, namely, parallel aligned strand orientation (LVSL) and orthogonally oriented strands (BOSB). The results showed that, when compared with LVSL, BOSB provides a larger maximum bearing capacity and shows excellent impact performance. Sun et al. [13] then studied the bending properties of bamboo strand board I-beams. The bending test confirmed that the rigidity and strength characteristics of the bamboo I-beams exceeded the requirements of APA-EWS in PRI-400-2012. The impact of processing, such as hot pressing on veneers, needs to be modeled to assist in the further optimization of veneer processes [14]. Ormarsson et al. [15] carried out numerical simulations on forming, springback, and deformation, and established a model of veneer hot-pressing technology. In addition, plasticizers, adhesives, etc. also play an important role in particleboard veneering. Tom et al. [16] studied the application of phenolic resin in veneer molding. In addition, Ozarska conducted in-depth research on veneer decoration technology, and published a monograph, A Manual for Decorative Wood Veneering Technology [17]. Due to the low cost and simple production process, adhesives such as phenolic resins and urea-formaldehyde resins have been widely utilized in the wood industry. However, the widespread utilization of these adhesives has caused serious formaldehyde pollution problems [18,19]. Biomass adhesives are natural polymer materials that can be used as adhesives. It is sometimes used more broadly to describe adhesives that are formed from biomonomers, such as sugar, or to mean synthetic materials that are designed to adhere to biological tissue. Adhesives that are based on soy protein are widely studied [20]. Su et al. [21] believe that, when compared with traditional adhesives, biomass adhesives have the following advantages: degradable, nontoxic pollution-free, and environmentally friendly; renewable raw materials that are easy to handle; and, suitable to be produced by cold- or hot-pressing technologies. However, due to the low bonding strength, low water resistance, poor product stability, and high price of soybean protein adhesive, its application is limited. In comparison, cornstarch adhesive has better application prospects [22,23]. 2. Experiment 2.1. Materials and Equipment (1) Oriented strand board (OSB): the OSBs utilized in our experiments are from Nanjing Redsun Decoration City. The format size of the utilized OSB is 1220 mm 2440 mm, the thickness is 18 mm, × and the species is poplar, with a thin strip of shavings. According to GB/T 17657-2013 [24], the density of the OSB is measured as 5.88 g/cm3 and the moisture content is 7.99%. (2) Veneer material: Myanmar old mahogany bark, 0.6 mm, commercially available [25]. (3) Adhesive: the prepared cornstarch adhesive has good adhesive performance, and all of the indexes meet the requirements of GB/T 20241-2006 [26] and GB/T 14074-2006 [27]. The solid content is 30%, the storage period is 100 d, the pH value is 6–7, and the esterification degree is 0.0166–0.0300. ≥ ≥ (4) Main instruments and equipment: tablet press (Monarch Hydraulic Lab Presses, CARVER, Wabash, IN, USA); precision Table saw (MJ6132, Fujian Mars Woodworking Machinery Factory, Fujian, China); circular saw; fixed thickness sander (RP420, Xinhua, Zhejiang, China); and, universal tester (Shimadzu Autograph, Kyoto, Japan). 2.2. Experimental Process In this section, the experimental processes are given. Note that all of the experiments in this paper were repeated three times and the average value of all statistical results was taken into consideration. Coatings 2020, 10, 511 3 of 11 Coatings 2020, 10, x FOR PEER REVIEW 3 of 11 2.2.1. Cold Pressing of Myanmar Old Mahogany 2.2.1. Cold Pressing of Myanmar Old Mahogany Cornstarch adhesive was utilized in this experiment. The amount of adhesive and the unit pressureCornstarch were set adhe to 160sive g /wasm3 and utilized 0.8 MPa, in this respectively. experiment. Cold-pressing The amount time of adhesive was the experimentaland the unit variable,pressure andwere surface set to bonding160 g/m3strength and 0.8 wasMPa, the respectively. test index. TheCold cold-pressing-pressing time time was was the set experimental to 1, 2, 4, or 6variable h, as shown, and surface in Table bonding1. Each experiment strength was was the repeated test index three. The times. cold-pressing time was set to 1, 2, 4, or 6 h, as shown in Table 1. Each experiment was repeated three times. Table 1. The cold-pressing time. Table 1. The cold-pressing time. No. 1 2 3 4 PressingNo. time (h) 11 22 43 6 4 Pressing time (h) 1 2 4 6 The process is designed as in Figure1 1.. Figure 1. FlowchartFlowchart of cold pressing of Myanmar old mahogany. Figure 11 illustratesillustrates thethe operations.operations. In In detail, detail, after after cutting cutting the the OSB OSB base base material material to to a size a size of of50 50mm mm × 50 mm,50 mm we, wesanded sanded the the surface surface to tomake make the the surface surface flat flat and and easy easy to to stick stick the the veneer, veneer, then then stuck × the veneerveneer onto onto the the base base material material surface, surface, aged itage ford 30it min.,for performed30 min., performed the cold-pressing the cold experiment,-pressing checkedexperiment, the veneerchecked adhesive the veneer quality adhesive after coldquality pressing, after cold placed pressing for 72, h,placed made for the 72 adhesive h, made fully the solidified,adhesive fully and solidified, finally trimmed and finally the OSBtrimmed with the a paperOSB with cutter, a paper polishing cutter, the polishing edge with the sandpaper.edge with Substratesandpaper. coating Substrate and coating adhesive and utilization adhesivewere utilization repeated were after repeated the first after substrate the first finished substrate overlaying. finished Noteoverlaying. that the Note shape that stability the shape of the stability two pieces of ofthe substrate two pieces after of coating substrate was ensured.after coating Cold was pressing ensured. was carriedCold pressing out according was carried to the out veneer according technology to the veneer that is technology required by tha thet experimentalis required by process.the experimental The unit areaprocess. pressure The unit was 0.8area MPa pressure and the was gauge 0.8 MPa pressure and wasthe gauge set to 1.3pressure MPa. Thewas cold-pressing set to 1.3 MPa. time The was cold 1 h.- pressing time was 1 h.
Details
-
File Typepdf
-
Upload Time-
-
Content LanguagesEnglish
-
Upload UserAnonymous/Not logged-in
-
File Pages11 Page
-
File Size-