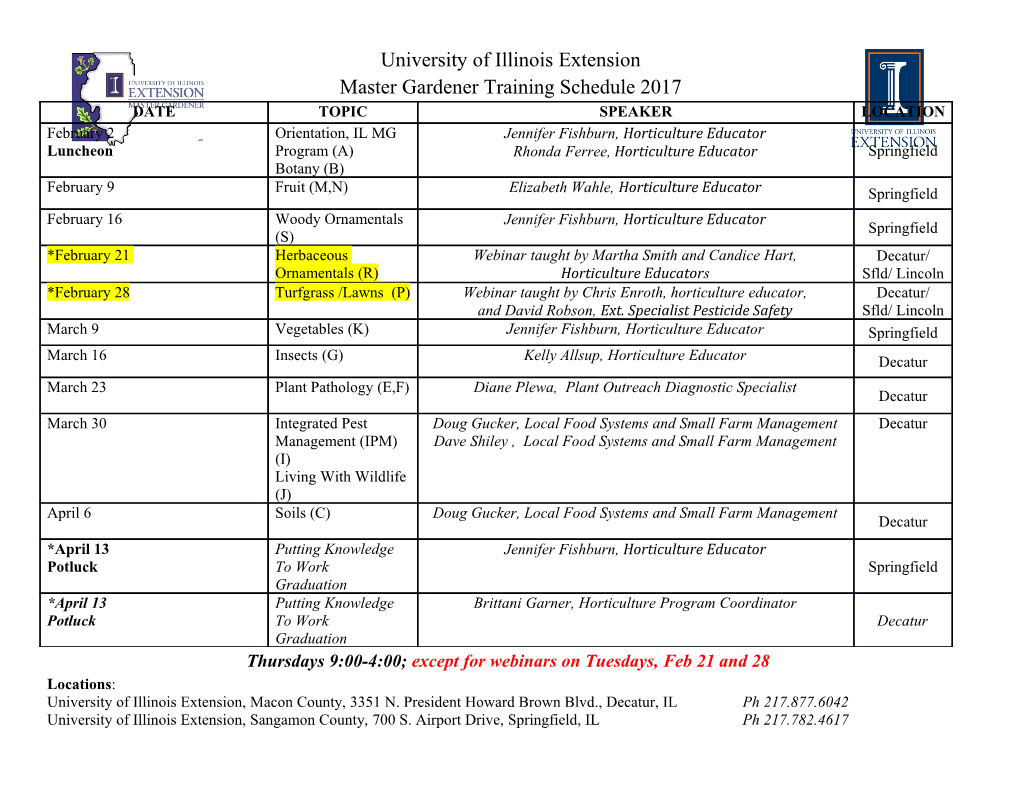
Mihaela Florentina Nitä Contributions to Aircraft Preliminary Design and Optimization l CONTRIBUTIONS TO AIRCRAFT PRELIMINARY DESIGN AND OPTIMIZATION POLITEHNICA University of Bucharest an institution authorized to organize doctoral programs and Hamburg University of Applied Sciences partner institution in the frame of the cooperative supervision process based on the doctoral thesis successfully defended on 28.03.2012, and as to Order no. 5743 of 12.09.2012 issued by the Minister of Education, Research, Youth and Sports for the attainment of the academic title of Doctor by Mihaela Florentina Niță (Man) from Bucharest Bibliografische Information der Deutschen Nationalbibliothek Die Deutsche Nationalbibliothek verzeichnet diese Publikation in der Deutschen Nationalbibliografie; detaillierte bibliografische Daten sind im Internet über http://dnb.d-nb.de abrufbar. ISBN 978-3-8439-1163-4 © Verlag Dr. Hut, München 2013 Sternstr. 18, 80538 München Tel.: 089/66060798 www.dr.hut-verlag.de Die Informationen in diesem Buch wurden mit großer Sorgfalt erarbeitet. Dennoch können Fehler nicht vollständig ausgeschlossen werden. Verlag, Autoren und ggf. Übersetzer übernehmen keine juristische Verantwortung oder irgendeine Haftung für eventuell verbliebene fehlerhafte Angaben und deren Folgen. Alle Rechte, auch die des auszugsweisen Nachdrucks, der Vervielfältigung und Verbreitung in besonderen Verfahren wie fotomechanischer Nachdruck, Fotokopie, Mikrokopie, elektronische Datenaufzeichnung einschließlich Speicherung und Übertragung auf weitere Datenträger sowie Übersetzung in andere Sprachen, behält sich der Autor vor. I.Auf läge 2013 In the memory of my grandfather iii iv Preface The reader will find the results of a work that never ceased to incite my passion for Aircraft Design and gave me the satisfaction of building a useful tool for the scientific community. Now, that I’ve come to the end of this work, I feel that this is only a beginning. I remember what Prof. Dr.-Ing. Dănăilă, the chairman of our Aerospace Engineering Department said, when he was leading a session of presentations of some of my Ph.D colleagues: “Doctoral studies represent a school – a place where students learn”. Students are not suddenly experts just because they start the doctoral studies. Working on the dissertation is not only about reaching a certain degree of innovation. The experience gathered during the studies (the research work, the conferences, the interaction with specialists of the aviation community or the responsibility of guiding students) is an important asset, at least as important as the results provided at the end. At the same time, the research effort openes enormous knowledge opportunities, and, for me, it meant the beginning of a deeper understanding of what Aircraft Design means. The first person to whom I owe a great deal of knowledge accumulated during the research time is Prof. Dr.-Ing. Dieter Scholz. If it wasn’t for his trust in me, I wouldn’t have started this “school” in the first place. I would also like to thank him for the idea of publishing this work at Dr. Hut Verlag and for supporting me in improving the manuscript accordingly. The support of Dr. -Ing. Mihai Neamțu was very important in creating a smooth advancement of my studies. I enjoyed working in an international environment and guiding dedicated students involved in studies and theses that enriched this work with valuable contributions. I am also grateful for the opportunity of cooperating with industry. This research would not have been possible without the financial support of the Romanian Ministry of Labor, Family and Social Protection through the Financial Agreement POSDRU/6/1.5/S/16, as well as the support of the ProExzellenzia Program, funded by the city of Hamburg and European Social Funds. v vi Abstract This work covers two related fields a) aircraft preliminary design and optimization, including aircraft cabin design and optimization and b) the optimization of engineering working processes in cabin design and cabin refurbishing. For a) existing equations or methods for aircraft preliminary sizing and conceptual design are adjusted and new equations or methods are introduced (e.g. equation for Oswald factor estimation, method for winglets efficiency estimation, method for estimating cabin length, method for estimating overhead stowage volume). Equations were combined to an Aircraft Design methodology. The methodology was implemented into Microsoft Excel to create a tool called OPerA – Optimization in Preliminary Aircraft Design. Optimization was initially done with a high-level commercial optimization software, Optimus. A technique called Differential Evolution was selected to be programmed in Visual Basic for Applications (VBA) and integrated directly into OPerA. Four objective functions are selected: the classical minimizing of Direct Operating Costs (DOC) represented by equivalent ton-miles costs, minimizing fuel mass, minimizing maximum take-off mass and maximizing of a composed objective function DOC+AV consisting of a weighting of DOC and Added Values which are selected parameters responsible for additional revenues for an airline. For b) three alternatives are proposed to increase efficiency of cabin design activities: i) a partitioning algorithm delivers the sequence that minimizes information feedback, ii) the analysis of the eigenstructure of the matrix underlines those processes with the greatest influence on the engineering system, and iii) a cross impact analysis identifies groups of processes belonging to five spheres: reactive, dynamic, impulsive, low impact and neutral. The selected reference aircraft for optimization is the Airbus A320-200. Three additional versions of the aircraft are investigated: a version with braced wings, a version with natural laminar flow and a version having both innovations at the same time. A number of 24 combinations of aircraft and cabin parameters, as well as requirements are tested for each objective function and each aircraft version. Varying aircraft and cabin parameters and adding the two innovations braced wings and natural laminar flow delivered these improvements: reduces DOC by about 16 %, maximum take-off mass by 24 %, fuel mass by 50 % and increases DOC+AV by 48 %. The tool provided is an efficient Aircraft Design tool, producing traceable optimizations in Preliminary Aircraft Design. It can be used in teaching as well as in the research of conventional and innovative configurations. Optimizing process chains for cabin redesign activities is not only beneficial, but also helps demonstrating required design and certification capabilities to aeronautical authorities. vii Extended Abstract The Task This work covers two related fields a) aircraft preliminary design and optimization, including aircraft cabin design and optimization and b) the optimization of engineering working processes in cabin design and cabin refurbishing. Aircraft preliminary design is defined here as aircraft Preliminary Sizing and Conceptual Design. Optimization in this work is a) the task of finding optimal aircraft and aircraft cabin parameter combinations and b) the task of finding the optimal sequence of engineering work processes in Cabin Conversions. The Method For a) aircraft preliminary design and optimization existing equations or methods for aircraft preliminary sizing and conceptual design are adjusted and new equations or methods are introduced (e.g. equation for Oswald factor estimation, method for winglets efficiency estimation, method for estimating cabin length, method for estimating overhead stowage volume, proposal of new mission fuel fractions). Equations were combined to an Aircraft Design methodology that ensured a balanced view on benefits and penalties of changing values of design parameters. The methodology was implemented into Microsoft Excel to create a preliminary design and optimization tool, called OPerA – Optimization in Preliminary Aircraft Design. OPerA uses a two-layered optimization strategy: an automated, intrinsic requirements matching in a two-dimensional chart represents the first layer that delivers the design point, and a formal optimization, representing the second layer, for the search of the optimum combination among a maximum of 20 design variables. Formal optimization was initially done with a high-level commercial optimization software, Optimus. The tool enables the application of all relevant optimization algorithms to the Aircraft Design methodology OPerA. A technique called Differential Evolution from the Evolutionary class of optimization algorithms was selected to be programmed in Visual Basic for Applications (VBA) and integrated directly into OPerA. Its efficiency is proven to be equal to Optimus. For the formal design optimization four objective functions are selected: the classical minimizing of Direct Operating Costs (DOC) represented by equivalent ton-miles costs, minimizing fuel mass, minimizing maximum take-off mass and maximizing of a composed objective function “DOC plus Added Values” consisting of a weighting of DOC and Added Values, which are selected parameters responsible for additional revenues for an airline. Weighting factors are calculated based on an expert questioning. Cabin parameters such as seat pitch or aisle width are included into the optimization in order to understand their impact on the design. For b) engineering work processes and their relations are transformed into a square matrix. Three alternatives are proposed to increase efficiency of later stage cabin
Details
-
File Typepdf
-
Upload Time-
-
Content LanguagesEnglish
-
Upload UserAnonymous/Not logged-in
-
File Pages300 Page
-
File Size-