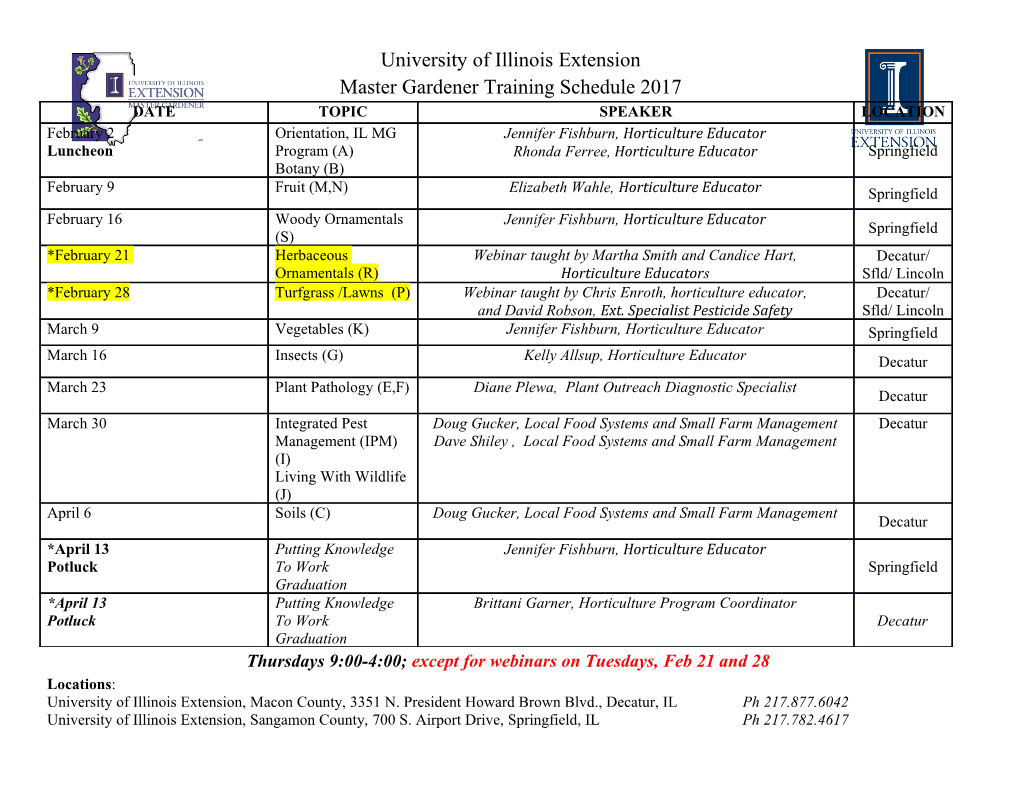
HIGH VELOCITY FORMABILITY AND FACTORS AFFECTING IT DISSERTATION Presented in Partial Fulfillment of the Requirements for the Degree of Doctor of Philosophy in the Graduate School of The Ohio State University By Mala Seth Dehra, B.E, M.S. ******* The Ohio State University 2006 Dissertation Committee: Approved by Dr. Glenn S. Daehn, Adviser Dr. Peter Anderson Adviser Dr. Kathy Flores Graduate Program in Materials Science and Engineering Copyright by Mala Seth Dehra 2006 ABSTRACT High velocity forming methods successfully address problems faced in conventional forming techniques. They can be effectively used for forming metals with low formability like aluminum alloys and high strength steel. They can be instrumental is manufacturing of lighter vehicles with higher fuel efficiency. Electromagnetic forming (EMF) is an HVF method that is gaining wide acceptance due to its advantages and scope for commercialization. A number of experimental studies were carried out with EMF with the main goal of exploring fundamentals about material formability at high velocities, which can be used to establish practical design guidelines and to make models of high velocity formability. Thus the main factors that influence high velocity formability – inertia / size effects; changes in constitutive behavior; impact; and dynamic failure modes, were studied mainly with experiments. The role of changes in constitutive behavior in improving formability was studied from existing studies and new theoretical studies involving High velocity Forming Limit Diagram (FLD) and through solving an inverse problem of ring expansion. ii Tube free-expansion experiments were carried out to demonstrate enhanced metal formability even in the absence of die impact. To further establish the significance of inertia, electromagnetic ring free-expansion experiments with rings of different aspect ratios were carried out. A higher aspect ratio sample had better formability in terms of uniform and total elongation and also had fewer necks than a low aspect ratio (more slender) ring at the same velocity. The results clearly demonstrated the influence of sample aspect ratio (dimensions) and hence inertia on high velocity formability. Die impact experiments were carried out with tubes and rings to show the beneficial influence of die arrest of a moving sample. It was revealed that die impact in an appropriate range of velocities can significantly suppress failure and reduce the number of tears and fractures in the samples. Further a new mode of failure in die impacted samples, spall-like dynamic rupture was observed, which had characteristics similar to classic spall failure. Thus through all these studies, the important factors influencing high velocity formability was studied and it was shown that it can be more complex than quasi-static formability. Boundary conditions for each forming operation can play a more significant role and hence simple tools like FLDs might not be practical tools for studying high velocity formability. iii Dedicated to the memory of my mother, Mrs. Komal Seth iv ACKNOWLEDGMENTS I express my sincere gratitude and appreciation to my advisor, Dr. Glenn S. Daehn, for his continuous guidance, inspiration and support throughout my research. His pursuit for ‘looking at the big picture’, creativity and enthusiasm have been a big inspiration for me. His intellectual guidance, encouragement and understanding made it possible for me to complete this dissertation while I was away from my family. I would like to thank Dr. John Bradley at General Motors USA, my project sponsors, for financial support and creative discussions about my research. I am deeply indebted to my parents and the rest of my family for their constant support. I would have never come so far but for the love and inspiration of my mother Mrs. Komal Seth, my father Mr. Anil Seth, brother Ashish and my grandparents, who encouraged me throughout. My husband, Amit has been a constant source of positive energy for me. I thank him for his understanding, love and support during my prolonged absences. I would also like to thank Dr. Vincent J. Vohnout and my other High Rate Forming group members, Manish Kamal, Kinga Unocic, Jianhui Shang, Edurne Iriondo, Scott Golowin and Yuan Zhang, for their help. v VITA May 30, 1977…………………………..Born - Shimla, India 1999…………………………………….B.E., Metallurgical Engineering Punjab Engineering College, Chandigarh, India 2003…………………………………….M.S. Materials Science and Engineering, The Ohio State University, Columbus OH, USA 2000 – Present………………………….Graduate Research Associate, Dep’t of Materials Science and Engineering, The Ohio State University, Columbus OH, USA PUBLICATIONS 1. Mala Seth, V.J. Vohnout and G.S. Daehn, “Formability of steel sheet in high velocity impact”, J. of Materials Processing Technology, Vol.168 (2005), pp. 390-400. 2. Mala Seth and Glenn Daehn, “Effect of Aspect Ratio on High Velocity Formability of Aluminum Alloy”, Symposium: Trends in Materials and Manufacturing Tech. for Transportation Industries, TMS, San Francisco (2005). 3. Glenn S. Daehn., Manish Kamal , Mala Seth, Jianhui Shang, “Strategies for Sheet th Metal Forming Using Mechanical Impulse”, 6 Global Innovations Symposium: Trends in Materials and Manufacturing Technologies for Transportation Industries: Sheet Metal Forming, TMS Annual Meeting, San Francisco CA, (2005). 4. G.S. Daehn, E. Iriondo, M. Seth, M. Kamal, J. Shang, Electromagnetic and High Velocity Forming: Opportunities for Reduced Cost and Extended Capability in Sheet Metal Forming, Society of Manufacturing Engineers Summit Conference, August, Wisconsin, (2005). vi TABLE OF CONTENTS Abstract ……………………………………………………………………….……….....ii Dedication…………………………………………………………………………...........iv Acknowledgements……………………………………………………………………….v Vita……………………………………………………………………………......……...vi List of Figures………………………………………………………………………..….xiv List of Tables…………………………………………………………………................xxi Chapters: 1. INTRODUCTION .........................................................................................................1 2. HIGH VELOCITY FORMING ....................................................................................6 2.1 INTRODUCTION...............................................................................................6 2.2 HIGH VELOCITY FORMING METHODS ......................................................7 2.2.1 Explosive forming ......................................................................................7 2.2.2 Electrohydraulic forming (EHF) ..............................................................11 2.2.3 Electromagnetic forming..........................................................................12 2.2.4 Gun forming .............................................................................................17 2.3 Advantages and challenges of using aluminum alloys......................................18 2.3.1 Advantages of using Al alloys vehicles ...................................................18 2.3.2 Challenges associated with using Al alloys with conventional forming.....................................................................................................19 2.4 Advantages of High velocity forming ...............................................................20 2.4.1 Formability enhancement.........................................................................21 2.4.2 Wrinkling is suppressed ...........................................................................27 vii 2.4.3 Springback is reduced ..............................................................................28 2.4.4 Economic advantages...............................................................................28 2.5 SUMMARY ......................................................................................................29 BIBLIOGRAPHY…………………………………..……………………………..30 3. LITERATURE REVIEW .............................................................................................36 3.1 INTRODUCTION.............................................................................................36 3.2 MATERIAL AND OTHER FACTORS AFFECTING FORMABILITY AT CONVENTIONAL FORMING VELOCITIES ......................................38 3.2.1 Strain hardening .......................................................................................38 3.2.2 Strain rate hardening ................................................................................39 3.2.3 Anisotropy................................................................................................40 3.2.4 Inhomogeneities .......................................................................................40 3.2.5 Damage accumulation ..............................................................................41 3.2.6 Superimposed hydrostatic pressure..........................................................43 3.3 FORMING LIMIT DIAGRAMS ......................................................................44 3.4 THEORETICAL MODELS FOR CALCULATING FLD’S............................48 3.4.1 Theoretical models for determining FLD’s based on necking theory......48 3.4.2 Theoretical models for determining FLD’s based on sheet non- homogeneity.............................................................................................49 3.4.3 Theoretical models for determining FLD’s based on incorporation of damage evolution.................................................................................52 3.5 SUMMARY FOR CONVENTIONAL FORMING..........................................56
Details
-
File Typepdf
-
Upload Time-
-
Content LanguagesEnglish
-
Upload UserAnonymous/Not logged-in
-
File Pages336 Page
-
File Size-