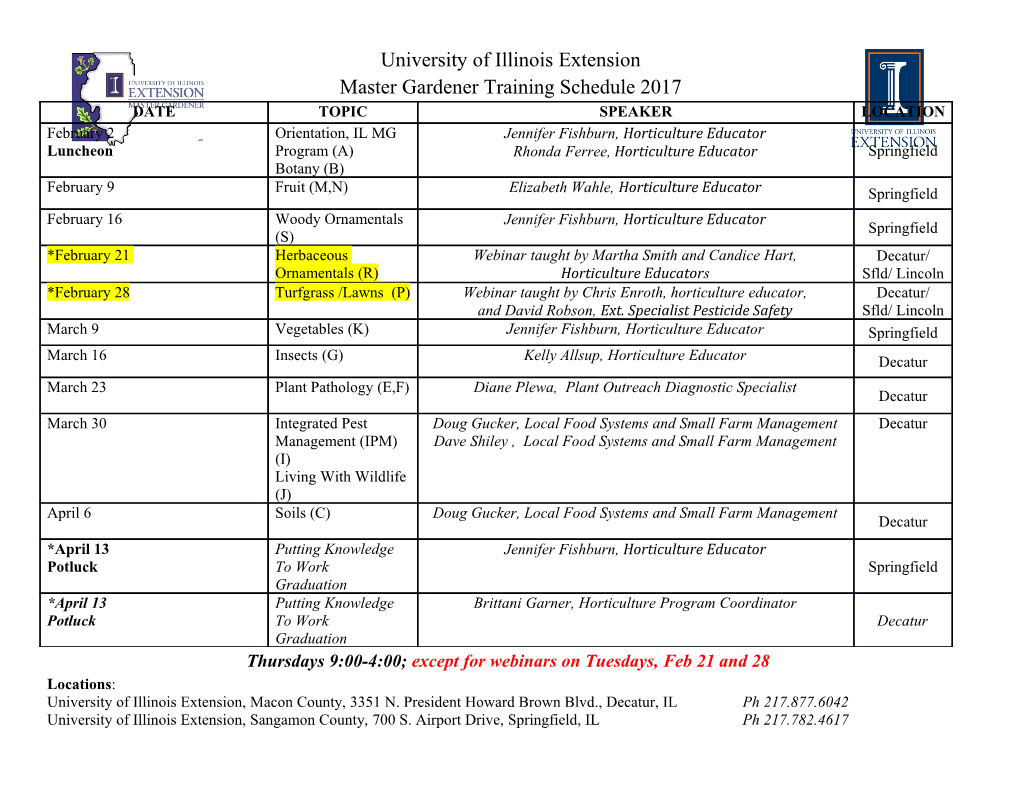
10-13/1 COPY NO ULTRASONIC MEASUREMENT OF WELD FLAW SIZE. PHASE 2 Part I : Studies of the use of the tandem technique and analysis of echodynamic responses for flaw evaluation Final Report Prepared for National Co-operative Highway Research Program Transportation Research Board National Research Council TRANSPORTATION RESEARCH BOARD NAS.NRC Privileged Document This report, not released for publication, is furnished only for review to members of or participants in the work of the National Co-operative Highway Research program. It ís to be regarded as fully privileged, and dissemination of the information included herein must be approved by the NCHFP, P.J. Mudge Welding lnstitute Project No.3769 Report No.3769/15, Part 1 October 1988 Vtt[TECIINOIOGY THE WETDING INSTITUTE Research Laboratory Abington Hall Abington Cambridge CB1 6AL United Kingdom Telephone Cambridge 0223 891162 Telefax 0223 892588 Telegrams WELDASERCH CAMBRIDGE Telex 81183 ACKNOWLEDGEMENTS This work was sponsored by the American Associabion of State Highway and Transportation Officials, in co-operation with bhe Federal Highway Administration, and was conducted in the National Co-operative Highway Research Program which is administened by the Tnansportation Research Board of the National Research Council. DISCLAIMER This copy is an uncornected drafb as submilted by the research agency. A decision concerning acceptance by the Transporlation Research Board and publication in the regulan NCHRP series will not be made untÍl a complete technical review has been made and discussed with fhe nesearchers. The opinions and conclusions expressed or implied in the report are those of the research agency. They are not necessarily those of the Transportation Research Board, lhe National Academy of Sciences, the Federal Highway Administration, or the individual stales participating in the Nalional Co-operative Hi.ghway Research Program. TABLE OF CONTENTS Page LIST 0F FIGURES ..... o.. r......... o....... o........ ..... iii LIST 0F TABLES ... ¡. r.... ................ o................... lv ACKNOWLEDGEMENTS o....o. r...... r......................... o........ v ABSTRACT .r...............¡..................o...o................ Vi SÌIMMARY ............... o......... ...........o........... I CHAPTER 1 INTRODUCTION AND RESEARCH APPROACH .............. ..... 2 Problern Statement Research Objective Research Approach Tandem Testlng Eehodynamic Responses CHAPTER 2 FINDINGS ...........o.....o..o...e..........o'....... 7 Tests on Artificial Notches Tests on lleld Flaws Echodynamic Curves CHAPTER 3 TNTERPRETATION, APPRATSAL, APPLTCATTONS .........,... 15 General Considerations Performance of Tandem Testlng Tandem Tests and Dl.1 Requirements Echodynamíc Responses CHAPTER 4 CONCLUSIONS AND RECOMMENDATIONS .......... 19 Conclusions Recommendations APPENDIX A Specimens and Equipment .........e.o.e.o...e.o...... A-1 APPENDIX B Results of Pul-se-Echo and Tandem Tests . o. G. c....., B-1 APPENDIX C Echodynamic Curves, Data Collection and Results .... c-1 t-1 LIST OF FIGURES 1 Principle of bandem tesfs ' 2 3.75in (95mm) specimen containing machined notches. 3 Artgular spread of refleeled signals v. flaw height,. 4 Echodynamic eurve from a crack, using a 4MHz 45o transducer' 5 Echodynamic curve fnom a crack, using a Zl*'fz 70o transducer ' 6 Bean width and crack response width from a 4l'GIz 45o lransducen' 7 Beam width and crack response widt'h from a 2Ì*12 45o transducer; I Beam width and crack response width from a 21412 70o Cransducer. 9 Nomogram illustPating bhe basis for acceptance and rejection of weld fl-aws with material thickness. 10 Relationship between limiling acceptable flaw slze from 01.1 and material thickness. 11 Echodynamic patlern types. Appendix A A1 Specimen details A.2 3.75in (95mm) specimen containing machined notches A3 3;75ín (95mm) wel-ded specimen J301 A4 1.5in (38mm) welded specimen J3Oz 'l A5 0; 4in ( Omm ) welded specimen J 320 A6 Vertical linearity (dB aecuracy) curve fon USM2, 8079 A7 VerLical linearity (dB accuracy) curve for USM2, K083 A8 Tandem scanning device A9 Micropulse computer controlled uLtrasonic testing system Appendix C c1 Echodynamic curves from drilled holes using a 4l&lz 45o transducer c2 Echodynamic curves from drilled holes using a 4MHz 60o lransducer c3 Echodynamic curves from drilled holes using a 2l{Hz 45o transducer C4 Echodynamic cunves from drilled holes using a 21fr12 60o transducer c5 Echodynamic curves from drill-ed holes using a Zl[Hz 70o transducer c6 Echodynamic curve from a crack using a 4MFIz 45o fransducer c7 Echodynamic cunve from a crack using a Zl¡íHz 70o transducer tll LIST OF TABLES (95mm) 1 Summary of tesl resulls, 3.75in specimens 2 Summary of lesb results, 1;5in (38mm) specimens 3 Summary of test results, 0.4in (lOmm) specimens 4 Summary of tesf results, wêld flaws Appendix A A1 Plate chemical eompositÍon A2 Specimen slzes A3 Details of arüifieial nofches A4 Details of últrasonic transducers Appendix B B1 At'lS D1 .1 ultrasonic flaw acceptance/reiection criberia B2 Debails of ullrasonic tests carnied oul 83-812 Results fnom 3.75in (95mm) samples conlaining notches 813-nt7 Results from 1;5in (38mm) samples conbaining notches 818-821 Results from 0;4in (10mm) samples containing notches 822-82\ Results from welded samples lv ACKNOWLEDGEMENTS This work was performed by The Welding Instiüute, Cambridge, England under conlract to NCHRP; Proiect No. 10-13/1. Peter J. Mudge, Head of lhe NDT Research Depantment, vras bhe Principal Investigator under the general guldance of Dr J.Ð. Harrison' Head of the Englneening and Maberials Research Group. The experimental work b¡as conducted by Messrs P.H. Smith (ttre Laboratory Supervisor), A'M. .Mr S.T. Brown and N.J. Faprant, K.S..provided Hayward and Lank. Mtss A.C. Duncumb addilional assLstance wit,h the echodynamic fesbs. ' ABSTRACT Thle report describes an investigabion into fhe suitabillt,y of using addilional ultrasonic technÍques lo supplernent the pulse-echo lests speclf ied tn AÍ'lS Dl .1 for evaluation of vertical planar f1aws, Tests were carried oub on artificiaL machined dlseonblnulties and real weld defects lo est,ablish ühe influence of flaw size and orienlatlon on ühe reliabilit,y of reJeetion of vertical planar defects using the tandem technique. Addllional fests were carrfecl out bo evaluate the feasibiliûy of using 'the echodynamic response charaeterlslics of flaws to predict their general shape. v1 SUMMARY This work was carried oul under Task 2 of NCHRP Pnoject 10-13/1. The aim was to establ-ish whether applicalion of the tandem ultrasonic technique could improve the reliability of rejection of vertical planar flaws using Al,¡S D1 .1 procedures, and whether flaw echodynamic nesponses could be used t,o discriminabe between flaw types. Tests carried out on an array of 92 maehined reflectors and on 9 neal weld flaws using the tandem technique indicated ühat reliabl-e rejection of such flaws could be attained provided fhey were oriented withÍn around 5ö of vertical-. Defects at greater angles were reIÍably rejected by pulse-echo tests bo D1 .1 requirements. It was esfablished that miniature ultrasonic search units operating aL 2MHz provided optimum performance for landem testing. However, defects in some locations cannot be examined due to access problems. Comparison of echodynamie responses from drilled holes and cnacks indicated that the width of the response is nol a reliable discriminator between planan and non-planar flaws. However, eeho pattern appearance does differ markedly between diffenent types of fÌaw and this may be used to predicb flaw type. In order to lo do this, it is necessary to examine the flaw from a number of orientations with more than one ultrasonic beam ang1e. CHAPTER ONE TNTRODUCTION AND RESEARCH APPROACH PROBLEM STATEMENT There is an urgent need fon ultrasonÍc testing procedures thal can be used lo measure the dimensions of weld discontinuilies (f1aws) with sufficient accuracy to permil evaluation using a fracture mechanics approach. Most state bransportation agencies use the provisions of lhe American lrtelding Sociefy Structural Ï'lelding Code AWS D1 .1 ( 1 ) to determine the acceptability of structural we1ds. These prgvisions are based on an assumed relationship between fhe ul-trasonic 'rlndication Ratingrrand flaw size. The results of lhe firsl phase of research (2), as well as other expenience, indicate lhat this relationship is not valid. Reseanch is needed to develop Ímproved ultrasonic testing procedures, using equipmenl pnesently available, that will permit accunate measurement of the dimensions of flaws common to weldmenls. These procedures are needed for use in both shop and field inspection of weldments to detenmine acceptance during conslruction and for in-service evalualion. Reliable procedures for ultrasonic testing will obviate the costs and delays of unnecessary repairs while neducing the probability that defects, which may lead to structural faifures, will be impropenly evaluated. RESEARCH OBJECTIVE The aim of the program as a whole r^,as to derive and to evaluate ultrasonic lechniques which would al-Iow accurate measurements of weld flaw size to be made, thereby permitting fracture mechanics analyses to be used to determine the structural integrily of steel bridges. The previous work (2) demonslrated lhat the most promising technique for accurate measurements of weld fl-aws utilised the measurement of flight time of ul-lrasound diffracted from defecl edges. Consequently, the major part of the program i^ras devoted to a study
Details
-
File Typepdf
-
Upload Time-
-
Content LanguagesEnglish
-
Upload UserAnonymous/Not logged-in
-
File Pages276 Page
-
File Size-