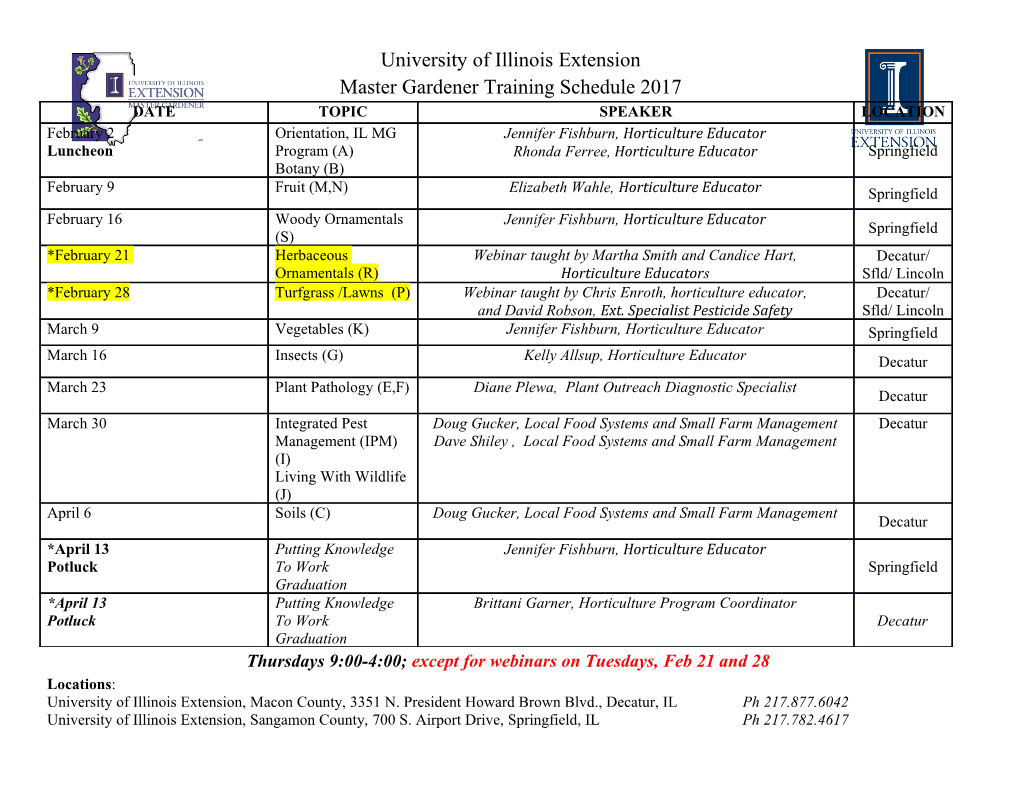
Journal of Marine Science and Engineering Article Methane Number Control of Fuel Gas Supply System Using Combined Cascade/Feed-Forward Control Soon-kyu Hwang 1 and Byung-gun Jung 2,* 1 Process Engineering Department, MODEC Offshore Production System, 9 North Buona Vista Drive, Singapore 138588, Singapore; [email protected] 2 Department of Marine System Engineering, Korea Maritime & Ocean University, Busan 49112, Korea * Correspondence: [email protected]; Tel.: +82-51-410-4269 Received: 4 April 2020; Accepted: 25 April 2020; Published: 28 April 2020 Abstract: Liquefied natural gas began to attract attention as a ship fuel to reduce environmental pollution and increase energy efficiency. During this period, highly efficient internal combustion engines emerged as the new propulsion system instead of steam turbines. However, Otto-cycle engines must use fuel that meets the methane number that was given by the engine makers. The purpose of this study was to develop a system configuration and a control method of methane number adjustment using combined cascade/feed-forward controllers for marine Otto-cycle engines to improve reference tracking and the disturbance rejection. The main principle involves controlling the downstream gas temperature of the fuel gas supply system to meet the required methane number. Three controllers are used in the combined cascade/feed-forward control for adjusting the downstream of the gas temperature: the cascade loop has two controllers and the feed-forward has one controller. The two controllers in the cascade loop are designed with proportional–integral (PI) controllers. The remaining controller is based on feed-forward control theory. A simulation was conducted to verify the efficacy of the proposed method, focusing on the disturbance rejection and set-point tracking, in comparison with a single PI controller, a single PI controller with feed-forward, and cascade control. Keywords: methane number; PI controller; cascade control; feed-forward control; natural gas; disturbance rejection 1. Introduction The International Maritime Organization (IMO) has adopted regulations to address the emission of air pollutants from ships and has implemented mandatory energy efficiency measures to reduce the emissions of greenhouse gases from shipping, under the International Convention for the Prevention of Pollution from Ships (MARPOL). First, sulphur oxides (SOx) and nitrogen oxides (NOx) were reduced as a solution to air pollution. Second, the energy efficiency design index (EEDI) was made mandatory for new ship’ construction as adopted by MARPOL [1–3]. In other words, it will increase energy efficiency to reduce environmental pollution. The final goal of these two items is to reduce pollutants and minimize fuel use. For that reason, liquefied natural gas (LNG) began to attract attention as a ship fuel [4,5]. During this period, various gas engines using natural gas (NG) for marine purpose emerged as new propulsion systems with high efficiency and low operational costs instead of steam turbines [6]. In other words, the Otto-cycle engine, which is one of the gas engine types, has begun to replace the existing ship propulsion system, the steam turbines. Figure1 shows the concept of the Otto-cycle engines. During compression stroke in the Otto-cycle engines, low-pressure fuel gas is injected from the middle of the cylinder liner to perform the compression stroke in the premixed state with the scavenging air. J. Mar. Sci. Eng. 2020, 8, 307; doi:10.3390/jmse8050307 www.mdpi.com/journal/jmse J. Mar. Sci. Eng. 2020, 8, 307 2 of 16 J. Mar. Sci. Eng. 2020, 8, x FOR PEER REVIEW 2 of 16 scavengingThen, at theair. endThen, of at the the compression end of the compression stroke, combustion stroke, proceedscombustion by injectingproceeds theby injecting fuel for the the ignition fuel forthrough the igniti fuelon through valves installed fuel valve ons theinstalled upper on part the of upper the cylinder part of head.the cylinder head. FigureFigure 1. The 1. The concept concept of the of theOtto Otto-cycle-cycle engines engines [7]. [7]. However,However, the the Otto Otto-cycle-cycle engine engine has has the the disadvantage disadvantage of ofhaving having to tomeet meet the the proper proper methane methane numbernumber (MN) (MN) that that was was given given by by the the engine engine make makers.rs. On On average, values ofof 60–8060–80 are are provided. provided The. The MN MNdescribes describes the the ability ability of of NG NG to to withstand withstand compression compression before before ignition. ignition. Pure Pure methane methane has has a a MN MN of of 100, 100,and and pure pure hydrogen hydrogen has ahas MN a ofMN 0. Fuelsof 0. withFuels lower with methane lower methane numbers numbers pose performance pose performance problems for problemsfuel gas for supply fuel gas systems supply (FGSSs) systems due (FGSS to combustions) due to combustion knocking knocking caused by caused higher by amounts higher amounts of ethane, of propane,ethane, propane, and heavier and hydrocarbons heavier hydrocarbons [8]. Major causes[8]. Major of low causes MN are of LNG low ageing,MN are temperature LNG ageing, rise of temperaturethe cargo tank rise inside,of the cargo and low tank MN inside LNG, and forced low vaporization MN LNG forced [9]. A vaporization list of the LNG [9] composition. A list of the andLNG MN compositionavailable fromand MN some available LNG terminals from some is provided LNG terminals in Table is1. provided With the lowin Table MN of1. With LNG the supplied low MN from of theLNG LNG supplied terminal, from it isthe highly LNG likelyterminal, that theit is MN highly will likely be lower that due the toMN the will increase be lower in the due temperature to the increaseof the in cargo the tanktemperature and LNG of ageing the cargo while tank sailing, and which LNG meansageingthat while a system sailing, capable which ofmeans controlling that athe systemMN iscapable needed. of controlling the MN is needed. Table 1. Liquefied natural gas (LNG) compositions and methane number (MN) at some LNG terminals. Table 1. Liquefied natural gas (LNG) compositions and methane number (MN) at some LNG terminals. Description A B C Description Methane (mol.%)A 89.60 86.26B 81.39 C Ethane (mol.%) 5.31 12.44 Methane (mol.%) 89.60 88.236.26 81.39 Propane (mol.%) 3.00 3.29 3.51 Ethane (mol.%) 5.31 8.23 12.44 Butane (mol.%) 1.47 0.96 0.64 Propane (mol.%) 3.00 3.29 3.51 Nitrogen (mol.%) 0.61 1.26 2.02 Butane (mol.%) MN1.47 71.10 069.30.96 67.40 0.64 Nitrogen (mol.%) 0.61 1.26 2.02 MN 71.10 69.30 67.40 The primary contribution of this study is the development of a system configuration and a methane number adjustment control method for marine Otto-cycle engines to improve reference The primary contribution of this study is the development of a system configuration and a tracking as well as the disturbance rejection with combined cascade/feed-forward controllers. First of methane number adjustment control method for marine Otto-cycle engines to improve reference all, we suggest how to adjust the MN using existing equipment in current LNG carriers (LNGCs) and tracking as well as the disturbance rejection with combined cascade/feed-forward controllers. First of LNG-fueled ships (LFSs). Some research has focused on calculation methods and test methods of the all, we suggest how to adjust the MN using existing equipment in current LNG carriers (LNGCs) and methane number. Partho et al. [8] developed a prediction model of the natural gas methane number. LNG-fueled ships (LFSs). Some research has focused on calculation methods and test methods of the Martin et al. [10] studied methane number test of the alternative gaseous fuels. However, a method for methane number. Partho et al. [8] developed a prediction model of the natural gas methane number. controlling the MN in ships’ Otto-cycle engines was needed. The method focusing on the fact that each Martin et al. [10] studied methane number test of the alternative gaseous fuels. However, a method gas has a different boiling point was applied in this paper in order to control the MN of the natural gas. for controlling the MN in ships’ Otto-cycle engines was needed. The method focusing on the fact that each gas has a different boiling point was applied in this paper in order to control the MN of the natural gas. J. Mar. Sci. Eng. 2020, 8, 307 3 of 16 Then, appropriate control methods could be applied in MN control systems. Feed-forward control and cascade control are considered two of the proper control methods. Feed-forward control is used to ensure constant control performance when a disturbance affects a process under feedback control. The weak point of feedback control is that a process variable (PV) is necessary before a manipulated variable (MV) change is taken when a disturbance affects a process. The application of feed-forward control is sufficient to compensate for this weakness. However, the performance of feed-forward control is limited by model uncertainty [11]. In practice, the disturbance rejection and accuracy of the system response are important. Cascade control was adapted to show how to use multiple process variables to improve the response to a disturbance and reference tracking. Several studies focused on control methods using cascade control and feed-forward control. Lee et al. [12] suggested the use of internal model controller (IMC) principles as a controller tuning method for both inner and outer loop controllers in cascade control. Kaya [13,14] proposed the application of the Smith predictor scheme in a long time delay system. Some researchers [15–18] studied feed-forward control with a feedback control system using advanced tuning methods such as robust control.
Details
-
File Typepdf
-
Upload Time-
-
Content LanguagesEnglish
-
Upload UserAnonymous/Not logged-in
-
File Pages16 Page
-
File Size-