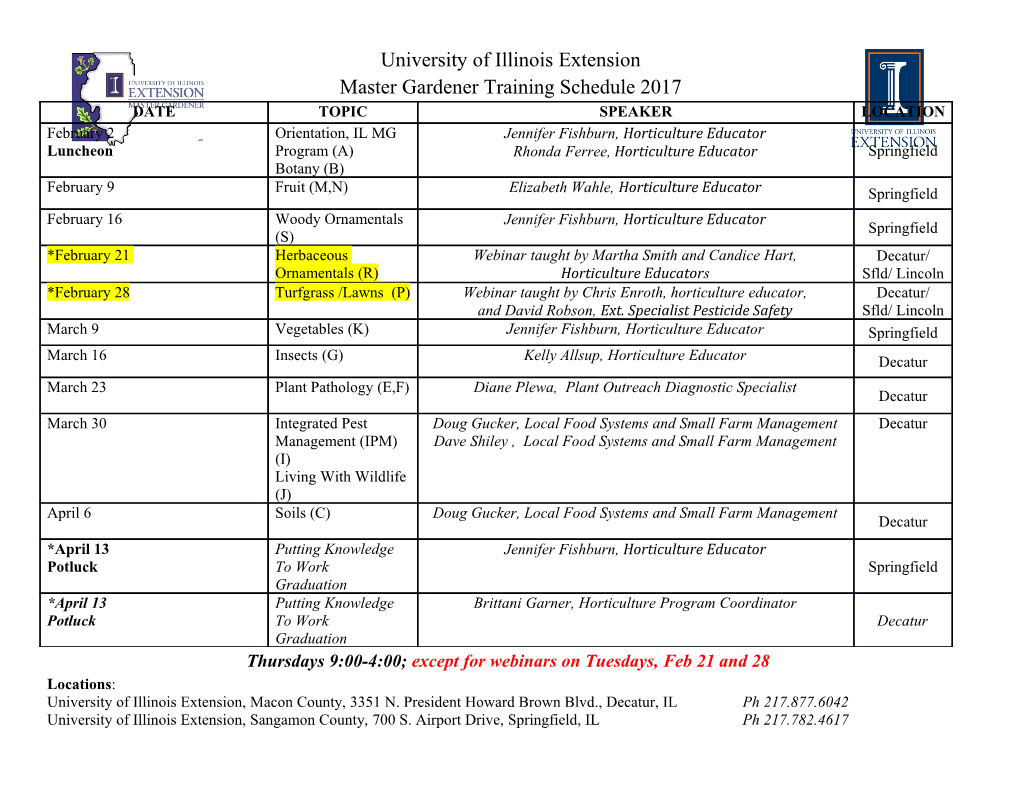
This project has received funding from the Shift2Rail Joint Undertaking under the European Union’s Horizon 2020 research and innovation programme under grant agreement No 730849 D1.1 Review of definitions, standard operating parameters, best practice and requirements, including future technologies and horizon scanning Grant Agreement N°: 730849 — IP/ITD/CCA IP3 Project Acronym: S-CODE Project Title: Switch and Crossing Optimal Design and Evaluation Project start: 1st November 2016 Project duration: 3 Years Work package no.: WP1 Deliverable no.: D1.1 Status/date of document: FINAL 18/09/2017 Due date of document: 31st July 2017 Actual submission date: 18th September 2017 Lead contractor for this document: COMSA Project website: www.s-code.info Dissemination Level PU Public X Restricted to other programme participants PP (including the Commission Services) Restricted to a group specified by the consortium RE (including the Commission Services) Confidential, only for members of the consortium CO (including the Commission Services) Page 1 of 236 Revision control / involved partners The following table gives an overview on elaboration and processed changes to the document: Name / Company short Revision Date Changes name 1 13/07/2017 UoB / DTVS / FERROVIAL / First version RRC / RSSB / COMSA / LBORO / BUT / UPA 2 26/07/2017 UoB / DTVS / FERROVIAL / General review, RRC / RSSB / COMSA / including clarification of LBORO / BUT / UPA concepts, insertion of data and pictures and correction of formatting and spelling. 3 18/09/2017 UoB / COMSA / LBORO Minor revisions to address comments from external review. The following project partners have been involved in the elaboration of this document: Partner Company short name Involved experts No. Marcelo Blumenfeld, Clive Roberts, Edd Stewart, 1 UoB Katherine Slatter, Louis Saade 2 DTVS Lukas Raif, Marek Smolka 3 FERROVIAL Jesús Alonso, Laura Tordera, Fco Javier Royo Stefan Knittel, Hannes Mathis, Andreas Marx, 4 RRC Majid Sawri 5 RSSB Neil Gofton Joan Peset, Sergio Morán, Carles Subirós, Miquel 6 COMSA Morata Hitesh Boghani, Roger Dixon, Sharon Henson, 7 LBORO Roger Goodall 8 BUT Otto Plasek Martin Kohout, Jaromir Zelenka, Monika 9 UPA Eisenhammerová, Petr Vršanský Page 2 of 236 Table of contents 1 Introduction 15 1.1 Introduction to Work Package 1 15 1.2 Guide to this document 18 2 Objectives 18 3 Baseline scenarios 19 3.1 Introduction and methodology 19 3.2 S&C lifecycle 21 3.2.1 Design 21 3.2.2 Manufacture 32 3.2.3 Installation 34 3.2.4 Maintenance 35 3.2.5 Renewal 41 3.3 Digitalization & BIM 41 3.4 Economic and Social Impact 43 3.5 Environment & Climate Change 45 3.6 Available technologies in track switching and crossing (S&C) 46 3.6.1 Conventional S&C 46 3.6.2 High Speed rail switches 47 3.6.3 Continuous Main Line Rail Turnout 48 3.6.4 Flange bearing 48 3.6.5 Rack or cog rail 49 3.6.6 Monorail 49 3.6.7 Guided vehicles 51 3.6.8 Maglev 52 4 Future scenarios for traffic demand 53 4.1 Horizon scanning 53 4.1.1 High speed lines 54 4.1.2 Mainline 58 4.1.3 Urban lines – metro systems 61 4.2 Passengers traffic 65 4.2.1 Mediterranean corridor 67 4.2.2 Scandinavian – Mediterranean corridor 68 4.2.3 North Sea – Baltic corridor 69 4.2.4 Baltic – Adriatic corridor 70 4.2.5 Orient/East – Mediterranean corridor 71 4.2.6 Adriatic corridor 73 4.3 Freight traffic 73 Page 3 of 236 4.3.1 Mediterranean corridor 75 4.3.2 Scandinavian – Mediterranean Corridor 76 4.3.3 North Sea – Baltic corridor 76 4.3.4 Baltic – Adriatic Corridor 77 4.3.5 Orient/East – Mediterranean Corridor. 78 4.3.6 Atlantic corridor 79 4.4 Concluding remarks 80 5 Review of definitions and standard operating parameters 81 5.1 Definitions 81 5.2 Identifying Standard Operating Parameters for S&C 81 5.2.1 The approach adopted 82 5.2.2 Standards Review 83 5.2.3 Output 84 5.3 Concluding remarks 90 6 RAMS analysis 91 6.1 Reliability 91 6.1.1 Failure modes 92 6.1.2 Reliability analysis 100 6.2 Availability 111 6.3 Maintainability 114 6.4 Safety 118 6.5 Concluding remarks 122 7 Focus Group and Baseline Scenario Validation 123 7.1 Introduction 123 7.2 Outcomes 125 8 S&C requirements 136 8.1 Geometrical requirements 136 8.1.1 Cost-effective track and layout parameters 136 8.1.2 Signalling and electro-technical equipment 140 8.1.3 Earthing of the metallic parts 140 8.1.4 Electrical isolation of the rails 140 8.1.5 Facilitation of drainage 141 8.2 Mechanical requirements 141 Page 4 of 236 8.2.1 Non-setting subsoil 141 8.2.2 High quality of supporting structure 142 8.2.3 High quality of earth work 143 8.2.4 Adequate track stiffness 144 8.2.5 High track resistance 145 8.2.6 Compatibility with bridge movements 148 8.3 Environmental requirements 148 8.3.1 Possibility to install noise and vibrations absorbers 148 8.3.2 Use of waste materials 152 8.3.3 Non-contaminant leachate 153 8.4 Construction requirements 153 8.4.1 Fast construction 153 8.4.2 Modularity 154 8.4.3 Easy transport of precast elements to construction site 155 8.5 Maintenance requirements 155 8.5.1 Low maintenance 155 8.5.2 Easy replacement of aged or worn S&C components 155 8.6 Operational/safety requirements 155 8.6.1 Performance parameters 156 8.6.2 Compatibility with linear eddy current brakes 156 8.6.3 Electromagnetic compatibility 157 8.7 Selection of high level requirements 157 8.7.1 Methodology 157 8.7.2 Evaluation framework 158 9 Radical innovations 165 9.1 Rivington’s self-acting railway switches 165 9.2 Abt switch 165 9.3 On-board turnout 166 9.4 REPOINT™ (Redundancy Engineered POINTs), 167 9.5 Actuated wing rails (normally closed) 167 9.6 Winter proof turnout 168 9.7 Rack and pinion railway switch on Rigi mountain 169 9.8 Auto-aligning track switch 170 9.9 Non-load bearing track switch 170 10 Technology concepts from wide range of industries 171 10.1 Roller coaster switches 171 10.2 Landing gear (System architecture) 171 10.3 Conveyor belt systems 172 Page 5 of 236 10.4 Model car road race track 173 10.5 Partition wall 174 10.6 Electrical switch (make before break) 175 10.7 RailPod 175 10.8 Toy trains 175 11 Selection of concepts 177 12 Summary 199 13. References 202 Appendix 1 – Definitions list 215 Appendix 2 – Concepts generated in Project Meeting in Brno UoT 230 Page 6 of 236 Index of figures Figure 1. Six-step methodology for radical change in systems engineering .............................. 16 Figure 2. Baseline scenario general diagram .................................................................. 20 Figure 3. Schematic illustration of a turnout and its components (11) ..................................... 23 Figure 4. Representation of acting forces in dynamic load .................................................. 25 Figure 5. Derailment Turnout in derailing-mode (left) and safe-mode (right); examples from RailCorp network in Sydney/Australia ...................................................................................... 28 Figure 6. HS turnout J60 representation ........................................................................ 29 Figure 7. Technical team working on the manufacturing of a S&C ......................................... 33 Figure 8. Installation of S&C part using a crane ............................................................... 34 Figure 9. Railway inspection ...................................................................................... 37 Figure 10. S&C from conventional line in Spain ............................................................... 38 Figure 11. S&C in Spanish High Speed line ................................................................... 39 Figure 12. BIM model of a railway from Ferrovial ............................................................. 42 Figure 13. A typical layout of a turnout (Switch and Crossing) on railway line ........................... 46 Figure 14. Independently operated switch blades (Source: Railcorp, Sydney/Australia) ............... 47 Figure 15. (a) Conventional S&C; (b) Continuous Main Line Rail Turnout. The photographs are taken from (19) ............................................................................................................. 48 Figure 16. (a) OWLS Crossing (20), (b) Partial flange bearing frog/nose (21), (c) Lift frog (22). ...... 49 Figure 17. Cog railway switch at (a) Schynige Platte Railway (© Kevin Hadley/Wikimedia Commons/CC-BY-SA-3.0); (b) Mount Washington cog railway (© Z22/Wikimedia Commons/CC-BY- SA-3.0); and (c) Pilatus railway line (Attribution: JuergenG at the German language Wikipedia). .... 49 Figure 18. (a) supported monorail; (b) suspended monorail. Reproduced from (29) .................... 50 Figure 19. Track switch for single rail railways (30) ........................................................... 50 Figure 20. Monorail switch (a) flexible beam; (b) showing possible routes from single section of pivot switch (31) ........................................................................................................... 51 Figure 21. Centrally guided transit mode switch (33); (b) Laterally guided transit mode "sinking" switch (33); (c) Laterally guided transit mode vehicle based switch (33); (d) electromagnetically activated vehicle based switch (34). ......................................................................................... 51 Figure 22. Switch used in BR maglev in Birmingham (35) ................................................... 52 Figure 23. Electromagnetic turnout for superconducting maglev train (38) ............................... 53 Figure 24. European rail traffic trend (2011-2015) (40) .....................................................
Details
-
File Typepdf
-
Upload Time-
-
Content LanguagesEnglish
-
Upload UserAnonymous/Not logged-in
-
File Pages236 Page
-
File Size-