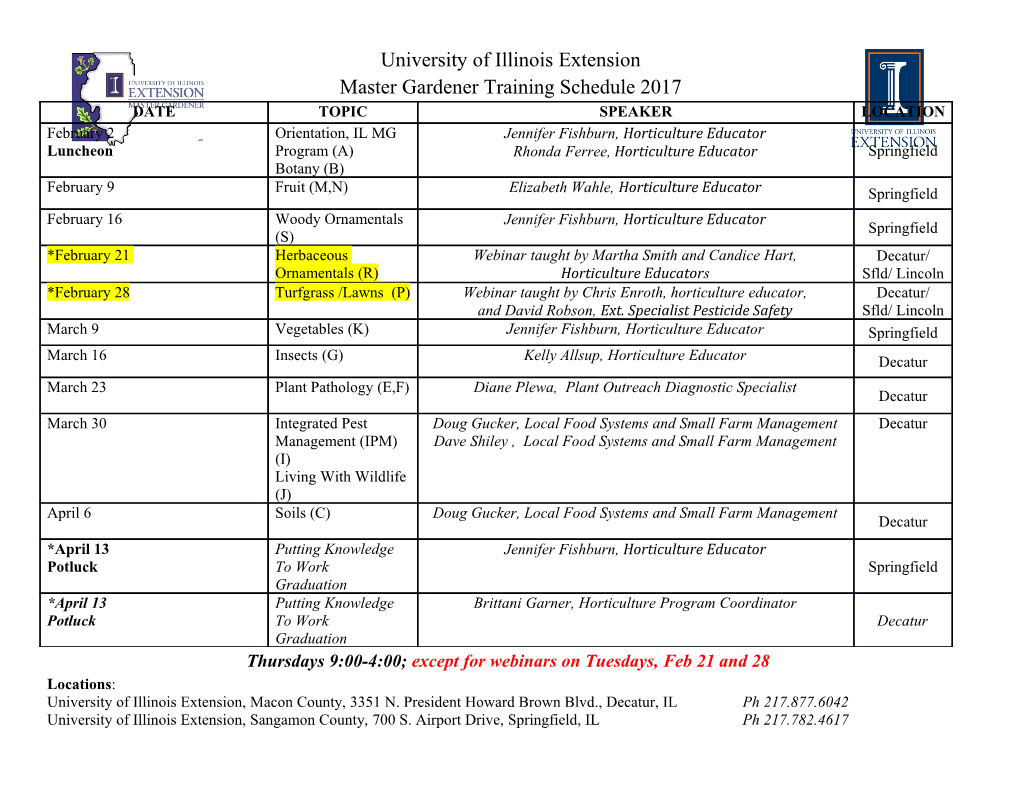
Automobile Ride, Handling, and Suspension Automobile Ride, Handling, and Suspension Design With Implications for Low-Mass Vehicles When carried to the extreme, today's emphasis on automobile mass reduction has significant implications for vehicle ride and suspension design. We therefore review traditional automobile suspension systems and offer comments on the special considerations of suspension systems of extremely low-mass passenger cars. The ride and handling characteristics of an automobile center on the characteristics of the tires. Tires are the vehicle's reaction point with the roadway. They manage the input of forces and disturbances from the road, and they are the final link in the driver's chain of output commands. Tire characteristics are therefore a key factor in the effect the road has on the vehicle, and in the effectiveness of the output forces that control vehicle stability and cornering characteristics. The tire's basic characteristics are managed by the system of springs, dampers, and linkages that control the way in which tires move and react to disturbances and control inputs. The bounce and steering movements of the wheels provide for a variety of simultaneous needs. They provide steering input for directional control, they compensate for (or utilize) body roll to improve cornering ability, and they move vertically in response to roadway irregularities in order to smooth out the ride and maintain adhesion. Wheels are connected to the sprung mass through linkages and are therefore affected by the rolling and pitching movements that occur about the suspensions system's reaction centers. The mechanical requirements for directional control, cornering forces, and ride comfort are continuously changing according to roadway and driving conditions. The suspension and steering linkages are designed to allow the wheels to move as needed to meet the dynamic requirements of various combinations of events. However, the designer is normally constrained by mechanical conflicts between structural members, the engine and drivetrain, and other components that also must fit into the vehicle. Consequently, errors in geometry are common, and the actual suspension system often falls short of the ideal in a variety of ways. Ride Comfort The quality referred to as "ride comfort" is affected by a variety of factors, including high frequency http://www.rqriley.com/suspensn.html (1 of 19) [9/6/2002 08:02:09] Automobile Ride, Handling, and Suspension vibrations, body booming, body roll and pitch, as well as the vertical spring action normally associated with a smooth ride. If the vehicle is noisy, if it rolls excessively in turns, or lurches and pitches during acceleration and braking, or if the body produces a booming resonance, occupants will experience an "uncomfortable ride." The ride quality normally associated with the vehicle's response to bumps is a factor of the relatively low frequency bounce and rebound movements of the suspension system. Following a bump, the undamped suspension (without shocks) of a vehicle will experience a series of oscillations that will cycle according to the natural frequency of the system. Ride is perceived as most comfortable when the natural frequency is in the range of 60 to 90 cycles per minute (CPM), or about 1 Hz to 1.5 Hz. When the frequency approaches 120 CPM (2 Hz), occupants perceive the ride as harsh. Consequently, the suspension of the average family sedan will have a natural frequency of about 60 to 90 CPM. A high-performance sports car will have a stiffer suspension with a natural frequency of about 120 to 150 CPM (2 to 2.5 Hz). Originally, human sensitivity to ride frequency was believed to be associated with the natural oscillations of an adult human body during a walking gait. An adult walks at the rate of about 70 to 90 steps per minute (frequency), and the torso moves up and down about 2 inches (amplitude) with each step. Early designers therefore attempted to constrain vehicle oscillations to those limits, the ride was indeed comfortable, and the theory was therefore believed to be correct. Today, our information about human sensitivity to vibrations is more sophisticated. We know that amplitude affects human sensitivity to frequency, and that there are some frequencies that are especially uncomfortable. For example, a frequency in the range of 30 to 50 CPM will produce motion sickness. The visceral region of the body objects to frequencies between 300 and 400 CPM. The head and neck regions are especially sensitive to vibrations of 1,000 to 1,200 CPM (18 to 20 Hz). These are the types of vibrations that are likely to emanate from the tires or from axle hop. Longitudinal oscillations are sensed primarily in the torso. Surprisingly, humans are most uncomfortable with longitudinal vibrations in the 60 to 120 CPM range (the region of greatest comfort for vertical vibrations). Discomfort from longitudinal disturbances occur when the vehicle pitches or when the seats lean rearward at a higher-than-normal angle. The perception of ride quality is degraded by virtually any disturbance experienced by the occupant. Human sensitivity varies according to the nature of the disturbance. Consequently, a "good ride" depends on the overall design of the vehicle, rather than just the design of the suspension system. To produce a comfortable ride, the high-frequency vibrations of wind and drivetrain noise must be minimized and properly isolated, and the suspension must be set in appropriate rubber mountings to isolate high-frequency roadway-induced vibrations. However, the natural frequency of the suspension system is still considered the cornerstone of a comfortable ride. The static deflection rate of the suspension determines its natural frequency. Static deflection is the rate at which the suspension compresses in response to weight. Other factors, such as the effects of damping (shocks) and system friction, alter the natural frequency of the suspension system. However, the primary determinate is the undamped static deflection rate. If this rate is used in calculations, http://www.rqriley.com/suspensn.html (2 of 19) [9/6/2002 08:02:09] Automobile Ride, Handling, and Suspension results will likely be very close to the actual value needed for a smooth ride. The static deflection rate of the suspension is not the same as the spring rate. Springs are located inboard of the wheels where they are normally subjected to the mechanical advantage of the suspension linkages. Static deflection is related to the distance the sprung mass (essentially the body) moves downward in response to weight. A static deflection of 10 inches in response to a weight equal to that of the sprung mass will produce a natural frequency of 1 Hz. A 5 inch deflection produces a 1.4 Hz frequency, and a 1 inch deflection results in a 3.13 Hz frequency. The natural frequency of a suspension can be determined by a simple formula expressed as follows: NF = Natural Frequency in Cycles Per Minute (divided by 60=Hz). SD = Static Deflection in Inches. Implications of High Payload-to-Vehicle Weight Ratio As vehicle mass is reduced, the payload-to-vehicle weight ratio naturally increases, which has trickle- down effects throughout the vehicle. An extremely low mass automobile, in the order of 1,000 pounds or less, for example, will have an unusually high payload-to-vehicle weight ratio. Variations in payload affect the natural frequency of the suspension. The critical damping force also varies with load. Over-damping (above 100 percent) dramatically reduces ride quality. In order to avoid over-damping at light loads, some degree of under damping is usually accepted at the fully- laden weight. Also, a passive suspension in combination with a high payload-to-vehicle weight ratio require a relatively high static deflection rate (a stiff suspension) in order to avoid undesirable effects on vehicle ride height. Ride height refers to the height of the body at a given load. It is important to keep ride height variations within predetermined limits in order to maintain headlight dip angle, provide adequate suspension stroke, and to provide an appropriate ground clearance. Load naturally affects the standing height of the vehicle. As load increases, the vehicle rests lower on its suspension, and at lighter loads it rests higher. Heavy loads in the luggage compartment can affect the pitch of the vehicle. The importance of a high payload-to-vehicle weight ratio becomes more apparent when the effect of payload on a standard sedan is compared to the effect of the same payload on a hypothetical ultralight vehicle. For example, a standard sedan of 3,500 pounds curb weight and a natural frequency of 1.2 Hz will rest 0.7 inch lower with the weight of two, 175 pound occupants aboard. The same static deflection rate in a 1,000-pound vehicle will cause the body to rest 2.45 inches lower with an equal, two-occupant load. A deflection of this magnitude will cause significant changes in the geometric relationship of suspension components. With a single occupant load, such a suspension would also http://www.rqriley.com/suspensn.html (3 of 19) [9/6/2002 08:02:09] Automobile Ride, Handling, and Suspension allow the body to list to one side. In order to equal the payload-induced deflection of the large car, the 1,000 pound vehicle must have a static deflection rate of 2 inches, which will result in a relatively stiff, sports-car-like ride of 2.2 Hz natural frequency. Consequently, an ultralight vehicle with a relatively high ratio of payload to vehicle weight will also have a relatively stiff ride. A self-leveling suspension and active damping could improve the suspension characteristics, but at higher cost and increased mass. Payload variations can also have a much greater effect on the center of gravity of a low mass vehicle.
Details
-
File Typepdf
-
Upload Time-
-
Content LanguagesEnglish
-
Upload UserAnonymous/Not logged-in
-
File Pages83 Page
-
File Size-