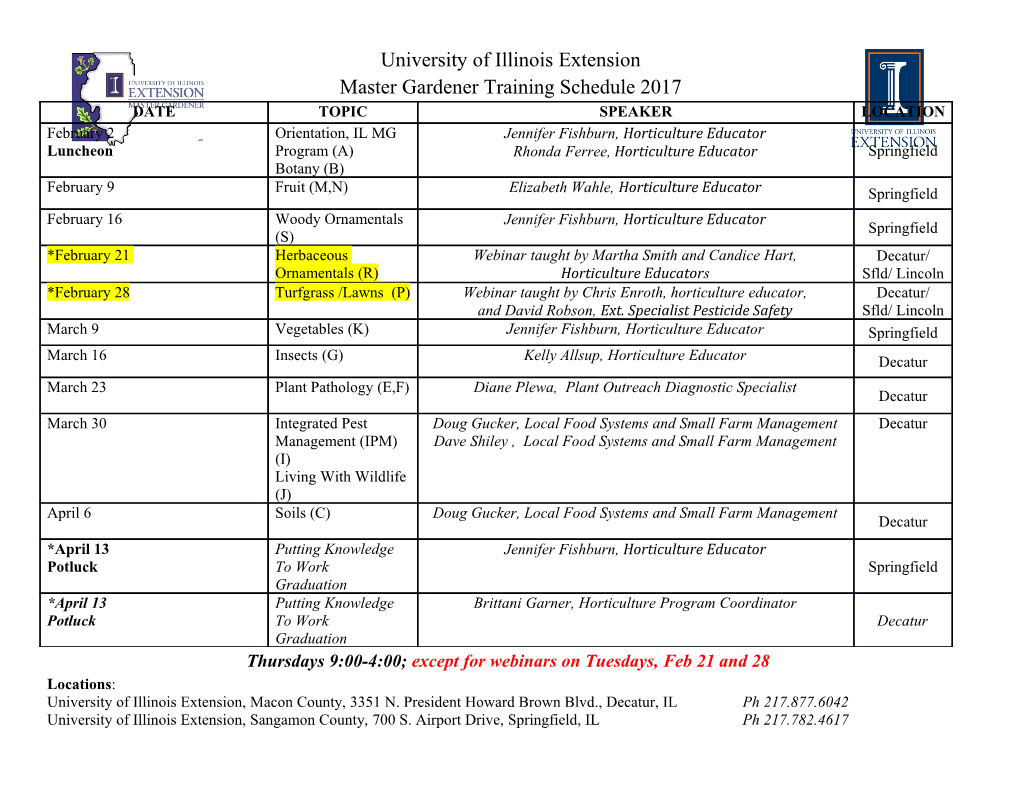
THE EMERGINGWORLD OF DEINKING ......................................... mether by floating, washing, or exploding, the technology to remove ink from wastepaper is$ourisbing in the US. s more and more waste paper is collected by U.S. A recycling programs, paper mills are having a hard time keeping pace. Despite many commitments acrossthe country to recycle paper with new deinking facilities, the demand for waste paperhas been unable to keep up withsup ply. That’s one of the main reasons prices for waste paper are dismal. This disparity in supply and demand has not come about because mills lack the technology to handle thewaste paper, howcver. Complete deinking technologies have devel- oped at arapid pace in recent years, and the paper industry promises 9.3 million tons of deinking capacity in North America by 1995. Processing that capacity will require some form of the two most common and pivotal deinking technologies at the heart of it all: flotation and washing. Steam explosion technologyand other methods for deink- ing are gaining momentum-with many pilot programs proving successful-but they have yet to be used in large- scale commercial productionof deinked pulp. .................... BY MICHAELMISNER 86 WASTE AGE JUNE 1992 .Deinkin~. Contd. .. Flotation deinking is self-describ- ing. Ink is literally floated off paper and out of a pulp slurry. But the flota- tion process is only one crucial ele- ment in a long seriesof measures. An extensive series of steps Bowater, a major newsprint pro- Bowater uses about eight broadsteps to deink 380 tpd of ONP and OMG. ducer in the southern U.S., brought a flotation deinking machine on-line in Calhoun, Tenn., last year. Black Claw- Current and Planned Newsprint DeinkingFacilities in North America son (Middletown, Ohio)built the bulk Capacity in fons of the equipment for Bowater’s $67- Company Metric Location Short million mill. The facility uses about Existing Recycled Newsprint Mills, 1991 eight broad steps to deink 380 of old tpd NewsprintAtlantic Co. OntarioWhitby, a5 94 newspapers (ONP) and old magazines Augusta Newsprint Co. Augusta,Georgia 352 3aa (OMG) to produceTennessee 300 Calhoun, tpd of cleanInc. Bowater, 733 aoa secondary fiber. CPFP Thunder Bay, Ontario 465 51 3 Mills recently began mixing in FletcherChallenge Canada Crofton, British Columbia 150 165 OMG because they found the clay con-Alsip, Corp.FSC Paper Illinois 132 146 tent helps in the flotation stage. Mag- GardenGarfield,StatePaperCo. JerseyNew 209 230 azine paper uses clay to help smooth InlandEmpirePaper Co. Millwood, Washington 72 79 the paper surface and create an opti- Manistique,ManistiqueMichigan Inc.Papers, 53 58 mum surface towhich glossy inks can MacMillan BloedelLtd. Port Alberni, British Columbia 150 165 Powell River, British Columbia adhere. Mills that use flotation but North PacificPaper Co. Longview,Washington 700 772 include no OMG add clay or other Quebec & OntarioPaperThorold, Ontario 31 3 345 fillers directly. The most common mix-Newsprint Smurfit CaliforniaPomana, 129 142 ture of ONP and OMG is a 70130% Newberg, Oregon 361 398 mix, although some millsvary the per- Oregon City, Oregon 21 9 241 centages based on what they want to SoutheastPaper Mfg. Co. Dublin,Georgia 406 448 accomplish. SpruceFallsPower & PaperKapuskasing, Ontario 31 4 346 At the Calhoun mill, clean ONP ContainersSnowflake,StoneCorp. Arizona 279 308 and OMG ride a conveyor to a drum Tolal 5,122 5,646 pulper or a hydropulper. Bowater’s Recycled Newsprint Mill Projects Under Way, 1992-1994 pulper, a rotating drum manufactured by CanadianPacific Forest Products Ltd. Gatineau,Quebec 440 485 Kamyr-Alstrom (Glens Falls, N.Y.), DaishowaForest Products Ltd. Quebec City,Quebec 300 331 throws a slushballof ONP, OMG, and AlabamaKimberly-ClarkPines, Coosa Corp. 31 0 342 water around forQuebec aboutBromptonville, 20 minutes. Inc. Kruger, 54 60 This action serves to break apart the Trois Rivieres, Quebec paper by slowly deteriorating all theSteilacoom, WashingtonCorp.Cascade Boise I 78 196 bonds holding the paper together. InternationalChampionHouston, Texas 450 496 Donahue, Inc. Clerrnont, QuebecClerrnont, Inc. Donahue, The unique rotating abilityof the 322 355 JamesMacLaren Industries Masson, Quebec 191 21 1 drum not only ensures agood tossing, Stone-Consolidated,Shawinigan,Quebec Inc. 200 220 but after time works the paper to one EvergreenPulp & PaperRedrock,Co. Arizona 300 331 end, where tiny slots wait to begin the first of many filtration steps. Pulpand Recycled Newsprint Mill Projects Approved But Indefinitely Delayed, 1992-1994 water drain through these one-mil-AlabamaClaiborne,Newsprint River Alabama 220 243 limeter holes, leaving behind large (Abitibi-Price/Parsons & Whittemore) Bowater E. Millinocket, Maine - 100 undesirables such as plastics, wire, ..........................................................Source: American Newspaper Publishers Association, with Some lnformatlon supplied by Arnerlcan Papermaker 88 WASTE AGE JUNE 1992 .Deinking. .. .Contd.. labels, and “stickies.” Stickies are any adhesive-type sub- ager of Betz PaperChem(Jacksonville, Fla.). “Hydrophobic stance found on waste paper, and they can be a big con- things attract other hydrophobic things. Most ink particles taminant in any recycled paper-making process. Stickies are naturally hydrophobic.” Clay particles coming off the and other contaminants are rejected out the far end of the OMG fibers also help to absorb more ink. drum pulper. Once on the surface of the slurry, the ink and ink- Smaller undesirables face more screens, as the pulp soaked clay is skimmed off the top and the slurry moves to mass moves toward the flotation cells. These holes, six- another stage. At Bowater,the slurry is put throughfive flota- one-thousandths ofan inch in width, stop plasticsand other tion cells, where ink is continuallyremoved in this manner. debris that madeit out of the drum pulper, as well as cap- In the last cell, the pH level of the water is changed fromalka- ture somelarger ink particles. As the pulp moveson toward line to acidic. This final pH shock helps loosen even more the flotation cells, only ink remainsas the last major unde- ink, says Sam Bittes, assistant project manager of engi- sirable targeted for elimination. neering for the Calhounmill. After flotation cells have thor- oughly worked the paper, centrifugal cleanersspin the pulp Captum’ng ink in the cell mass. Denserparticles, including larger inkparticles, are flung The barrage on the ink starts 10 feet before the flotation to the outsideof the vessel and removed. cell, where a section of wide pipe called a static mixer Finally, the pulp is cleaned across fabric washers. These injects air bubbles into the pulp slurry as it moves towardthe are actually fine sheets of 60-meshfabric, meaning they have cell. Full of air and water, the pulp is ready to be dumpedinto 60 holes per square inch. This washing stage is somewhat a long flotation cell. Bowater’s cell, manufactured by the similar to systemsthat use strictly washing to deink their pulp. Beloit Corp. (Dalton, Mass.), is 10 feet wide by 40 feet The principle is the same in that water is drained from the long. There, the forward movement is stopped and the mass pulp and more inkis cleaned off, leaving almost 100%pulp. of pulp nearly comes torest. As it sits there, the bubbles of The deinked pulp at Bowater is then dried and used as air slowly rise to the surface, capturing particles of ink feedstock for the production of newsprint at the Calhoun mill. along the way and dragging themto the surface of the mush. Bowater removes 98-99% of the ink or “all visible ink,” Ink particles hitch rides with the air bubbles because of according to Bittes. The mill adds virgin fiber to produce chemistry. “Air bubbles are hydrophobic, which means they 2,250 tpd of newsprint containing upto 40% recycled con- don’t like water,” explains Tom Woodward, marketing man- tent; on the average, sheetshave 1520% recycled content. ~ ~~~ How Newsarint Is Deinked lwashino Method) Slurry goes into a 3- stage washer where ink is suspended in water , and drained away to Steel Blades waste treatment plant. (Fiber slurry is \ formed into Source: Southeast Paper Manufacturing Co recycled papes) .................................................................................... 90 WASTE AGE JUNE 1992 .Deinking. .. Contd. .. Approximately 800 newspapers use Bowater’s recycled ditionally the only way paper was deinked. In the past five newsprint, including USA Today and the Washington Post. years things have changeddramatically. “Washing is relatively expensive compared to flota- Like laundry ina blender tion,” Bowater’sBines says. “It [washing] was theway it was Strictly washing systems use essentially thesame types done since wheneverdeinking began years ago until about of initial screens and cleaners as the flotation system five years ago. It’s the older, conventional way of doing described, but the core of the line is large washing vessels, it ...[and] it uses huge amounts of water.” Bowater saves or “giant kitchen blenders,” according to Southeast Paper water by primarily using the flotation process. Manufacturing (Dublin, Ga.). Southeast Paper’s washing Started in 1961, Garden State Paper’s Garfield, N.J., system deinks about 560,000 tons per year of ONP to pro- recycled newsprint mill uses only washingto remove the ink duce 100% recycled-content newsprint. from 780 tpd of ONP. “A lot of people are going the flota- Southeast’s process starts by mixing ONP with 20,000 tion route,” says Frank Lorey, senior vice president of Gar- gallons of water and special chemicals that help pull the ink den State Paper. “Essentially, when you go the flotation off the paper.This recipe is mixed inside Black Clawsoncon- route, you can’t use only newspapers; you must have mag- tinuous pulpers, which are 20 feet in diameter and chum the azines or fillers. You also need a way to wash those fillers mass with six-foot rotors. “The process lifts ink from paper off. Another problem with flotation it that it’s hard to float just like detergents lift grease and dirt from clothes in a finely dispersed inks such as flexographic inks, which come washing machine,” the company explains.
Details
-
File Typepdf
-
Upload Time-
-
Content LanguagesEnglish
-
Upload UserAnonymous/Not logged-in
-
File Pages6 Page
-
File Size-