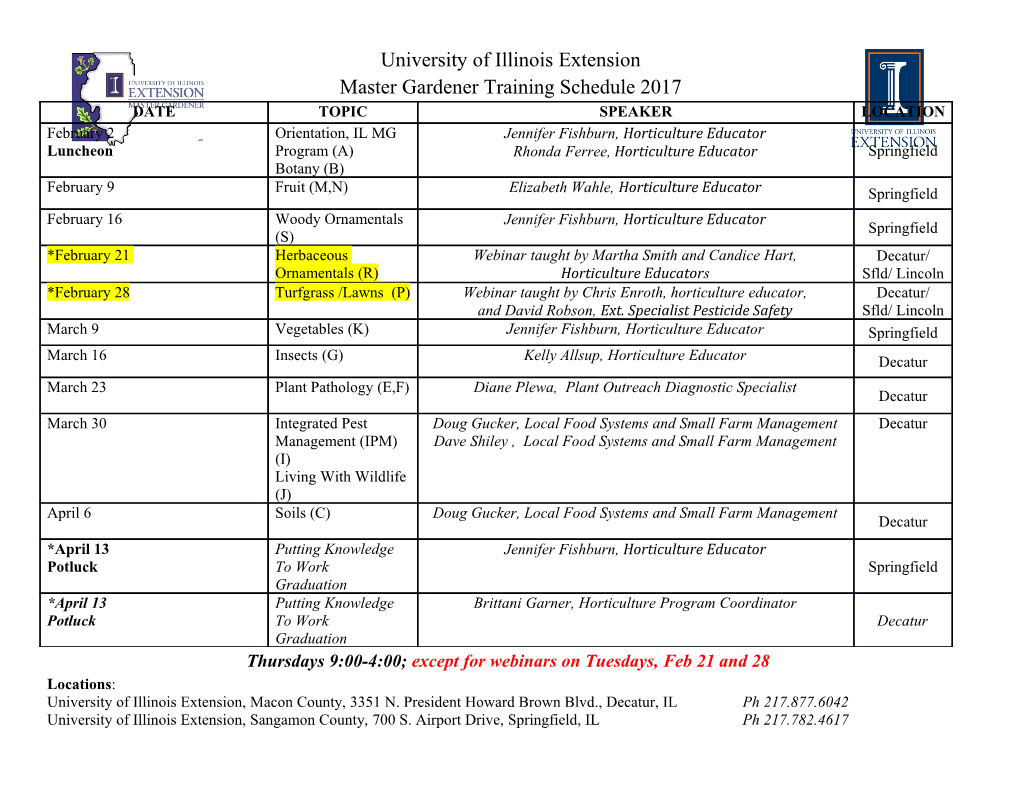
Manufacturing,Masters Research Materials and Design Exhibition Group Projects 201510 September 2015 www.cranfield.ac.uk Please note that some of the work you see today may be work in progress Development of Consultancy Tools from Research which Help Organisations (Through-Life Engineering Services) Background Through-Life Engineering Services (TES) are the technical services that are necessary to guarantee the required and predictable performance of a complex engineering system throughout its expected operational life with the optimum whole-life cost. Aim & Objectives The aim of this project is to gain an in-depth understanding of the research output of the TES Centre (i.e. tools) and consult the TES Club Partners to validate these tools, by identifying how this research fits their business requirements. This study involved creating a standardised portfolio of the tools with the help of interaction with researchers/tool developers. Another major deliverable of the project is to create a generic tool development process that can be employed by the TES Centre in the future. Approach In order to gain comprehensive understanding of the research carried out in the TES Centre we interacted with the researchers/tool developers. A portfolio of the existing and underdevelopment tools has been created and presented to the TES Club Partners. A specific methodology was designed to carry out the entire project, which consisted of three phases. The first phase “Knowledge Capture”, aimed to gain an in-depth understanding of the research output of Through-Life Engineering Services and the proto tools. The second phase consisted of interaction with the TES Club Partners and validation of the tools. The tool portfolio was presented to the partners and workshops were conducted to find a way of how the TES Centre research can benefit their organisations. The third phase included gathering the feedback from companies and collating them in a conference paper. Findings / Recommendations Study and analysis of the existing tool development methodologies revealed the following limitations: Lack of flexibility, difficult to use and implement Developed with a focus on product based environment and have not been modified to take into consideration the recent shift from a product to a service based environment Thus, to overcome these issues and to achieve standardisation a generic tool development methodology developed by the Group Project Team is recommended. "The Group Project Team successfully pieced together an intuitive and effective method for a difficult and ever challenging task of reaching out and commercialising outcomes of academic research.” Dr. Piotr Sydor For further information contact Andy Shaw & Dr. Piotr Sydor [email protected] & [email protected] Team members Deep Chawla Meriem Mahiou Pooja Thourani Project Management background. BSc in Digital Technology Engineering Holds a degree in Computer Science Air Transport and Logistics Management background from ISEP an Engineering Engineering from Shri Shankaracharya from Huddersfield University. She has School. MSc in Management and Institute of Professional Management worked for NATS on the Graduate Information System at Cranfield University and Technology, India. Currently Programme and has Customer Service School of Aerospace, Transport and pursuing her Masters in Management & experience at Virgin Atlantic Airways. Manufacturing. She has worked for CATU Information Systems, at Cranfield Currently pursuing a Masters in Electrical Safety Equipment Company as University. Worked as a project intern Aerospace Manufacturing, key learning a Project Manager assistant and has been cum developer with Soft Galaxy consists of Simulation modelling, involved in a Junior Enterprise experience Services Pvt. Ltd. Also worked for a manufacturing processes and as a Project Manager. She has a year as a coordinator in setting up of the Composites Manufacturing. background in Object programming school “MM Junior School” part of the (Java), database, Network 3G and 4G. Godriwala Education Society. [email protected] [email protected] [email protected] Sarah Cohen Shabaaz Supariwala Shuo-Yuan Chang Digital Technology Engineering Mechanical Engineering Mechanical Engineering background. background from ISEP, an Engineering background. BEng in Mechanical Bachelor of Engineering from National school. MSc in Management and Engineering from Cardiff University. He Chin-Yi University of Technology. he Information System at Cranfield University has worked for General Electric Oil & Gas worked for three years in manufacturing School of Aerospace, Transport and and NRB Bearings LTD as an Engineering processes working in different areas Manufacturing. She has worked for a web Intern. He has a background in Six Sigma, related to product design, operating agency at Fullsix-Ekino as a technical Lean manufacturing projects and Design. machines, maintenance engineering and consultant and has been involved in a He played Snooker for Cardiff University Sales. junior enterprise experience as a Project and represented them in tournaments. and Sales Manager. She has a background in object programming (Java), Database and Network 3G and 4G. [email protected] [email protected] [email protected] Developing a production planning and control system to improve on-time delivery and minimize inventory (Bromford Industries) Background Bromford Industries, formed in 2009 as part of a management buy-out, is primarily a manufacturer of Aerospace and Industrial Gas Turbine components, specialising in the manufacture of fabricated and machined, close-tolerance components that fit predominantly, in the hot gas path area of the engine. It has a demand pattern of 150 to 200 parts with low volume and the business expecting to grow, the company has a traditional ERP system that does not provide reliable planning information for production, so there is regular manual intervention to the production schedules to meet on-time delivery. Aim & Objectives The aim of this project is to map the current system across all work streams, including external contractors, to identify “best-practice” suitable for a low-volume high-variety company. This study has also the aim to quantify non-value adding activities and to propose a way to reduce the work in progress inventory levels. The project also, in conjunction with company management, has the objective of selecting the most appropriate visual management tool for planning and control system. Finally, it will be necessary to elaborate an evaluation of the proposed benefits and possible costs. Approach First of all, the group had to identify different family of products throughout developing a Pareto analysis, the study was based on the impact of the product into the benefits for the company. After this selection, the group split up their task in order to collect more details at the same time: the development of different VSM (value stream mapping) and pick up some testimonies from operators. In the second part of this project, the methodology focused on researching the best practice of visual management tools for the low-volume high-variety environment, evaluating costs and benefits. The group, also, did benchmarking with several companies in order to identify the best practice. Findings/Recommendations Having conducted VSM activities and analysis, root causes of capacity issues were found out and improvements were suggested to increase on time in full deliveries. According to collection of data we proposed a visual management system to increase schedule adherence which could support the existent ERP system. For further information contact Dr. Patrick McLaughlin [email protected] Team members Mr Jose Luna Mr Pedro Duarte Mr Julio Cermeron Sponsored by Mexican Government Sponsored by an Erasmus Scholarship to Aerospace engineering (CONACYT) to study the MSc Aerospace study in Cranfield University (UK) the background. Student of MSc Aerospace Manufacturing. Graduated with Honours MSc in Manufacturing Consultancy Manufacturing. Several experience as a Mechatronics Engineer and (double-degree). Still Graduating in modelling with CatiaV5, with recognised recognized as the best student by the Universidade do Minho courses in CatiaV5 and Lean National Association of Engineering (Portugal).Graduated in MSc Industrial Manufacturing. Internship at the Spanish Schools and Faculties (ITESM - Mexico). Management, ESEIG (Portugal). With Army and in association with ITP as Certificate in Computer Aided Engineering work experience in Pfp SA (Portugal) as a mechanical engineer. and Design applied to Aeronautical Logistics Manager and also in LiderGraf- Engineering (ESTACA - Paris, France). 4 Artes Gráficas, SA (Portugal): Developing [email protected] years of work experience in Procter & a Project on the Analysis and Process Gamble as a manager in the Planning Optimization. department. [email protected] [email protected] Ms Alice Laurent Material sciences and industrial engineering background. Master Degree from Ecole des Mines de Nancy, France. Currently studying for a double degree in Aerospace Manufacturing. Experience as an intern for Snecma (France) in the Industrial and Supply Chain Direction. Responsible for the implementation of a new barcode system in the ERP BaaN to improve stock reliability. [email protected] A Physical Demonstrator of Cybersecurity in Manufacturing (Atkins) Background Within our increasingly
Details
-
File Typepdf
-
Upload Time-
-
Content LanguagesEnglish
-
Upload UserAnonymous/Not logged-in
-
File Pages54 Page
-
File Size-