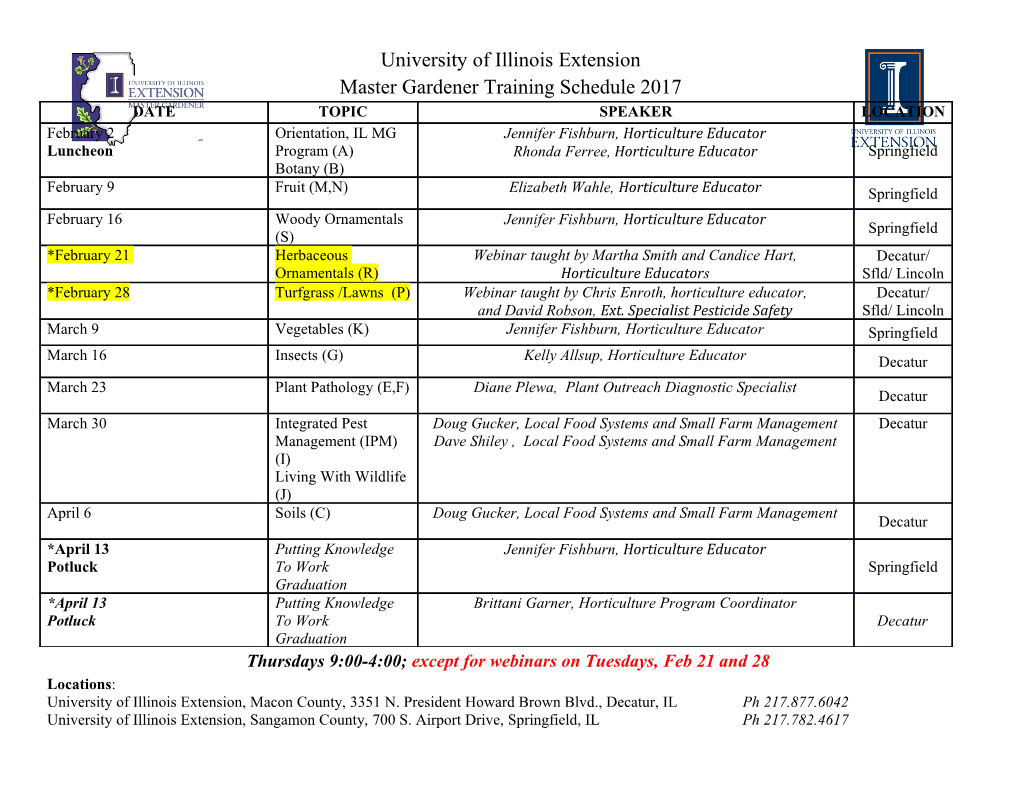
FINITE ELEMENT ANALYSIS AND SIMULATION STUDY ON MICROMACHINING OF HYBRID COMPOSITE STACKS USING MICRO ULTRASONIC MACHINING PROCESS ____________________________________ A Thesis Presented to the Faculty of California State University, Fullerton ____________________________________ In Partial Fulfillment of the Requirements for the Degree Master of Science in Mechanical Engineering ____________________________________ By Panchal, Sagar Rajendrakumar Thesis Committee Approval: Sagil James, Department of Mechanical Engineering Nina Robson, Department of Mechanical Engineering Darren Banks, Department of Mechanical Engineering Spring, 2018 ABSTRACT Hybrid composites stacks are multi-material laminates which find extensive applications in industries such as aerospace, automobile, and electronics and so on. Most hybrid composites consist of multiple layers of fiber composites and metal sheets stacked together. These composite stacks have excellent physical and mechanical properties including high strength, high hardness, high stiffness, excellent fatigue resistance and low thermal expansion. Micromachining of these materials require particular attention as conventional methods such as micro-drilling is extremely challenging considering the non-homogeneous structure and anisotropic nature of the material layers. Micro Ultrasonic Machining (μUSM) is a manufacturing process capable of machining such difficult-to-machine materials with ultraprecision. Experimental study showed that μUSM process could successfully machine hybrid composite stacks at micron scale with a relatively good surface finish. This research uses finite element simulation technique to investigate the material removal during the μUSM process for micromachining hybrid composite stacks. The effects of critical process parameters including the amplitude of vibration, feed rate and tool material on the cavity depth, cutting force and equivalent stress distribution are studied. The outcome of this research can be utilized to further our understanding of performing precision machining of hybrid composite stacks for use in several critical engineering applications. ii TABLE OF CONTENTS ABSTRACT ................................................................................................................... ii LIST OF TABLES ......................................................................................................... iv LIST OF FIGURES ....................................................................................................... v ACKNOWLEDGMENTS ............................................................................................. vii Chapter 1. INTRODUCTION ................................................................................................ 1 2. FINITE ELEMENT ANALYSIS AND SIMULATION ..................................... 9 Damage Criteria .................................................................................................... 13 Failure Criteria for CFRP Substrate...................................................................... 13 Failure Criteria for Ti Substrate ........................................................................... 15 3. RESULTS AND DISCUSSION ........................................................................... 16 Variation in Cavity Depth with Time during the μUSM process ......................... 17 Variation in Cutting Force with Time during the μUSM process ........................ 20 Variation in Equivalent von Mises Stress with Time during the μUSM process . 22 Effect of Vibration Amplitude during the μUSM process .................................... 26 Effect of Feed Rate during the μUSM process ..................................................... 30 Effect of Tool Material during the μUSM process ............................................... 33 4. COMPARISON BETWEEN EXPERIMENTAL AND SIMULATION RESULT...................................................................................... 36 5. CONCLUSION ..................................................................................................... 38 RESEARCH DISSEMINATION .................................................................................. 41 REFERENCES .............................................................................................................. 42 iii LIST OF TABLES Table Page 1. Material Properties used in FE Simulation Study of μUSM Process .................. 11 2. Material Properties of CFRP Substrate ................................................................ 11 3. Conditions Used for FE Simulation of µUSM of CFRP/Ti Stacks ..................... 12 4. Damage Parameters of CFRP Substrate .............................................................. 14 iv LIST OF FIGURES Figure Page 1. Schematic Representation of Micro Ultrasonic Machining Process ................... 6 2. Experimental Setup of Micro Ultrasonic Machining Process ............................. 6 3. Microcavities Machined on CFRP/Ti Stacks using µUSM Process a) CFRP Entrance Side and b) Ti Exit Side ........................................................................ 7 4. Finite Element Simulation Model of μUSM Process of a) CFRP Substrate and b) Ti Substrate ............................................................................................... 10 5. Finite Element Simulation Model of μUSM Process showing Damage on a) CFRP Substrate and b) Ti Substrate ................................................................ 17 6. Variation in Cavity Depth during μUSM process on CFRP and Ti Substrates ... 19 7. Cavity Machined (Magnified View) during μUSM Process on a) CFRP Substrate and b) Ti Substrate ............................................................................... 19 8. Variation in Cutting Force during μUSM Process on CFRP and Ti Substrates .. 22 9. Variation in Equivalent von Mises Stress during μUSM Process on CFRP and Ti Substrates .................................................................................................. 23 10. Variation in Normal Stress acting on Ti Substrate during μUSM Process .......... 25 11. Variation in Plastic Strain in Ti Substrate during μUSM Process ....................... 25 12. Equivalent von Mises Stress Distribution during μUSM Process on a) CFRP Substrate and b) Ti Substrate ............................................................................... 26 13. Effect of Amplitude of Vibration on Cavity Depth during μUSM Process on CFRP and Ti Substrates ....................................................................................... 28 14. Effect of Amplitude of Vibration on Cutting Force during μUSM Process on CFRP and Ti Substrates ....................................................................................... 28 v 15. Effect of Amplitude of Vibration on Equivalent von Mises Stress during μUSM Process on a) CFRP Substrate and b) Ti Substrate .................................. 29 16. Effect of Feed Rate on Cavity Depth during μUSM Process on CFRP and Ti Substrates ............................................................................................................. 31 17. Effect of Feed Rate on Cutting Force during μUSM Process on CFRP and Ti Substrates ............................................................................................................. 32 18. Effect of Feed Rate on Equivalent von Mises Stress during μUSM Process on a) CFRP Substrate and b) Ti substrate ................................................................. 33 19. Effect of Tool Material on Cavity Depth during μUSM Process on CFRP and Ti Substrates......................................................................................................... 35 20. Effect of Tool Material on Cutting Force during μUSM Process on CFRP and Ti Substrates......................................................................................................... 35 21. Comparison of MRR during µUSM Process of CFRP/Ti Stack using WC and Cu Tools ............................................................................................................... 37 vi ACKNOWLEDGMENTS I would like to thank Dr. Susamma Barua, Interim Dean, and Dr. Sang June Oh, Interim Associate Dean Engineering and Computer Science, California State University Fullerton. I would like to offer my special thanks to Dr. Chean Chin Ngo, Chair, Department of Mechanical Engineering, CSUF for granting me permission and giving an opportunity to pursue my thesis in Advanced Manufacturing. I would like to express my very great appreciation to my faculty advisor Dr. Sagil James for his valuable suggestions, enthusiastic guidance and persistent supervision, which were essential for the completion of this thesis research work. I am obligated to him for his constant inspiration and meticulous efforts in amending errors and suggesting improvements. I would like to thank Dr. Nina Robson and Dr. Darren Banks for being in the thesis approval committee. I wish to acknowledge the help provided by all members of the Titan Advanced Manufacturing Laboratory who supported me throughout my research work. I would like to thank Administrative support: Crystal Barnett and Charlotte Sanchez. Special thanks to my parents and family members for their unconditional love along with their support and encouragement. vii 1 CHAPTER 1 INTRODUCTION Fiber reinforced polymers (FRP) are composites of high-strength fibers embedded in a matrix of polymer material (Ku, Wang, Pattarachaiyakoop, & Trada, 2011). The fibers
Details
-
File Typepdf
-
Upload Time-
-
Content LanguagesEnglish
-
Upload UserAnonymous/Not logged-in
-
File Pages50 Page
-
File Size-