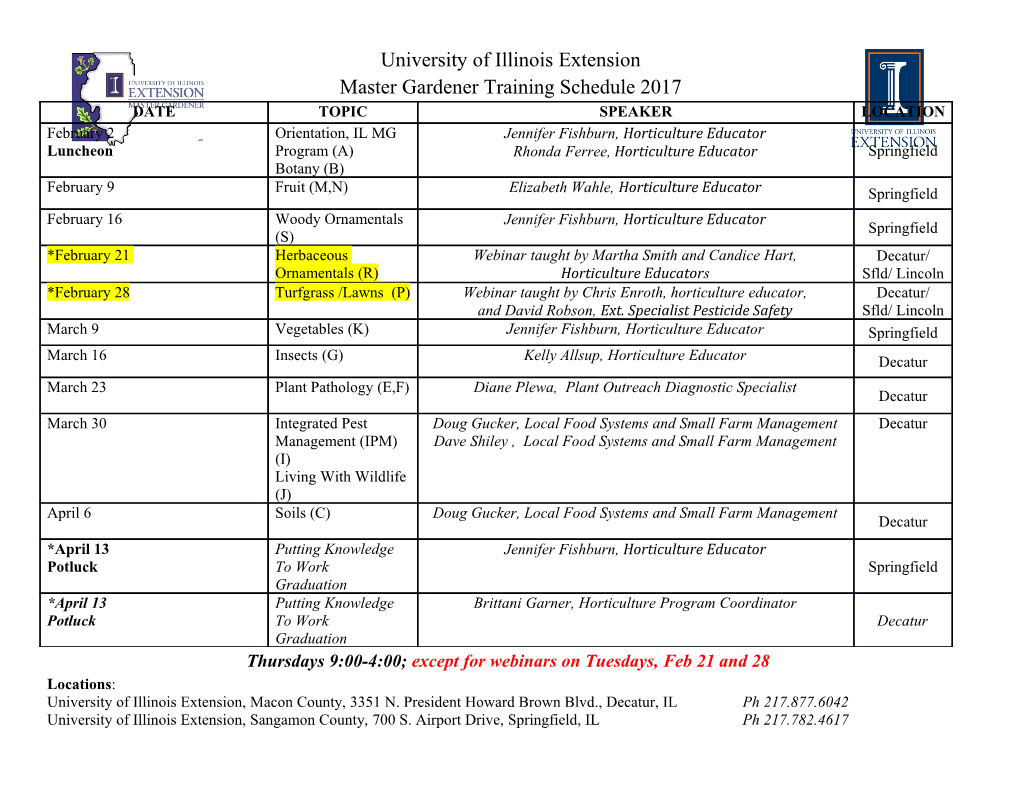
North American Quick Response Centers Control Valves Experience In Motion Providing Value Through Service developed standard repair procedures and a large network of shared technicians throughout the region. You can rest at At Flowserve we know a critical choice any main- ease knowing that your valves will be repaired the same way, tenance professional must make is: Who should every time, by highly skilled service technicians. repair my valves? Flowserve’s expert technicians service all types of control, We also know finding a repair facility that meets the toughest quarter-turn automated or manual-operated valves, including deadlines, restores your valve to near original quality, repairs Valtek®, Kammer®, Fisher®, Masoneilan®, to name a few. To a wide variety of valve styles and is cost-competitive can be ensure this quality, each Flowserve service center is equipped the most challenging part. At Flowserve, we have established with thousands of commonly required parts, produced by the a cohesive network of Quick Response Centers located OEM or built by skilled in-house valve machinists. throughout North America, cooperating and leveraging their collective capabilities, ready to meet your needs. Quick Response Centers Flowserve’s QRCs provide the highest level of service Flowserve’s Quick Response Centers are strategically located including 24-hour emergency repair and on-site repair with to ensure that a QRC is within hours of most major industrial mobile repair units. In emergencies, Flowserve service customer locations. This allows rapid response to customer technicians can be on-site in any North American plant within needs by providing same day delivery of standard parts. 24 hours. Flowserve understands how critical it is to have a Special parts can be delivered in days instead of weeks. trusted partner that will offer fast service and quality prod- With the help of Flowserve QRCs, plant managers are able to ucts to keep your facility in operation. This is why we have maximize plant uptime and profitability. Springville is a primary control valve manufacturing facility. 2 flowserve.com Flowserve QRCs... • Are strategically located for timely response • Provide best-in-class aftermarket support and service • Maintain a comprehensive inventory for fast turnaround • Offer on-site troubleshooting & engineering support • Readily adapt to ever changing control valve needs QRC Capabilities While each QRC may offer a particular service capa- bility unique to its facility, some of the core capabilities common to each location include the following... • Control Valve Repair • Actuation Repair • Valve Automation Since Flowserve is an established valve manufacturer, we • Remanufactured Valves have the equipment and capacity to turn around any repair • Field Service & On-Site Repair or remanufacture project, large or small, quickly - including • Oxygen Cleaning plant shutdowns. Veteran application engineers stand ready at each location to make valuable recommendations to extend • Full Machine & Weld Shops the life of your valve or improve its performance. These engi- • Turnaround Management neers also specialize in upgrading valves to spring cylinder • Plant Surveys actuators and four-way positioners or automating quarter- turn valves, which can dramatically increase performance. 3 Profiler® Testing & Certification All new and repaired valves are tested prior to shipment, using the Profiler® control valve diagnostics system. Using our Profiler diagnostic testing system, after reassembly each repaired valve is stroked, seat leak tested, hydro tested, and quality tested to industry standards. All vital data about each valve is kept on record with Profiler software, providing easy access for future reference. A copy of the diagnostic test results is available to the customer upon completion of the repair project. Flowserve’s Profiler technology also enables us to run diagnostics while in the field on all of your valves. Based on the diagnostic results, problems can be fixed in the field which avoids the need for expensive repair maintenance. FlowStarTM Data Management FlowStarTM asset management software allows Flowserve engineers and technicians to track performance and support improvement programs using a proven, system- atic approach. Every valve that comes to a Flowserve QRC for service is fully inspected upon arrival. During the initial inspection all important valve data is recorded in the FlowStar system. Our technicians then review the data prior to repair to determine if an upgrade is needed. In many cases, such upgrades cost little or no more than the original repair bid, but significantly improve the valve’s performance and/or life. FlowStar keeps these records on file for future reference. FlowStar also stores important service information to track each repair and cleaning performed on your valve. The stored information allows our Flowserve technicians to identify significant trends and provide you with detailed feedback and recommendations regarding your valves. FlowStar also allows alliance partners to access their own equipment database for reviewing or exporting equipment details and various reports. 4 flowserve.com Third Party Repairs Flowserve has the expertise and proven experience to repair ALL major control valve manufacturer’s products. We use OEM parts on all repairs, regardless of brand origin, so you can rest assured your valve assembly is restored to the original OEM specifications. If OEM parts cannot be sourced within your critical time frame, we have the expertise and capability to resolve these issues and meet your deadlines. We also specialize in out of the ordinary valve repair. Included in these repairs are valves such as: gate, globe, check, quarter turn, or MOV. We can repair even your most difficult valves, even if the valve is obsolete or parts are difficult to find. Before After Remanufacturing Whether cost is the issue or delivery is of critical importance, remanufactured products can be a valuable option and solution. The most costly aspect of control valve repair is not the repair itself, but rather the cost of downtime and lost production. These costs can easily be cut in half with remanufactured replacement valves. Remanufactured valves offer predictable cost, a firm and fast re-install date, and the quality you expect. Flowserve remanufactured valves are assured compliance to original manufacturing and industry specifications. Also, our All repaired valves, regardless of manufacturer, will undergo OEM based product carries a new valve warranty. the following quality assurance checks: • Positive Material Identification (PMI) • Body thickness testing to ANSI specifications • Flange inspection to ANSI specifications • Measure all critical dimensions and tolerances • Reassemble with OEM parts • Complete diagnostics test and birth certificate • Documentation of as-received and as-built conditions • Data and photos entered into FlowStarTM database. To ensure the best solution is provided, Flowserve’s experi- enced application engineers can perform a technical review of the process conditions prior to building a remanufactured. When a review is not practical, we will produce an “equal” product based on information from the OEM serial plate. Remanufactured products are available for day to day require- ments, as well as larger project needs. 5 Turnaround Management With specialized technology, our qualified teams can help with your turnaround preparation. Prior to most major turnarounds, we send staff into the field to perform a valve survey and walk down. This survey enables us to pre-order the majority of the required repair materials and minimize the amount of discovery work. Using our Profiler® software, we can run diagnostics on all your valves to make sure you have all the information necessary to have a smooth turnaround. Based on the diagnostic results from Profiler, many problems can be fixed in the field, eliminating the need for expensive repair maintenance. Let our control valve experts help you determine if your valves need to be Field Services serviced, and make sure your turnarounds are a success. The Flowserve QRC network is equipped to handle all of your control valve repair needs on-site, including turnarounds. Our Flowserve QRCs have mobile field service units of all sizes and a large network of qualified field service technicians and machinists available to make your field repair jobs a success. Whether your need is to troubleshoot a single valve or you are bringing down an entire unit, Flowserve’s qualified field personnel are capable of getting your control valves back in service without leaving your property. In an emergency, we have staff on-call 24 hours a day to help you through your crisis. Our Flowserve trained service tech- Flowserve’s QRC staff is committed to making your turn- nicians can be at your facility, anywhere in North America, arounds smooth, successful, and within budget. We can within 24 hours. We understand the importance of keeping TM utilize FlowStar to manage all of your control valve data, your facility in operation and minimizing downtime. In order identify bad actors, and make the information available to you to help get your operation back on it’s feet we keep thousands via the internet. of commonly required parts at our QRCs for quick and easy access. 6 flowserve.com Re-Instrumentation Whether you’re looking for digital or analog signal control, Flowserve’s positioners offer the highest perfor- mance and can be mounted on most control valves,
Details
-
File Typepdf
-
Upload Time-
-
Content LanguagesEnglish
-
Upload UserAnonymous/Not logged-in
-
File Pages16 Page
-
File Size-