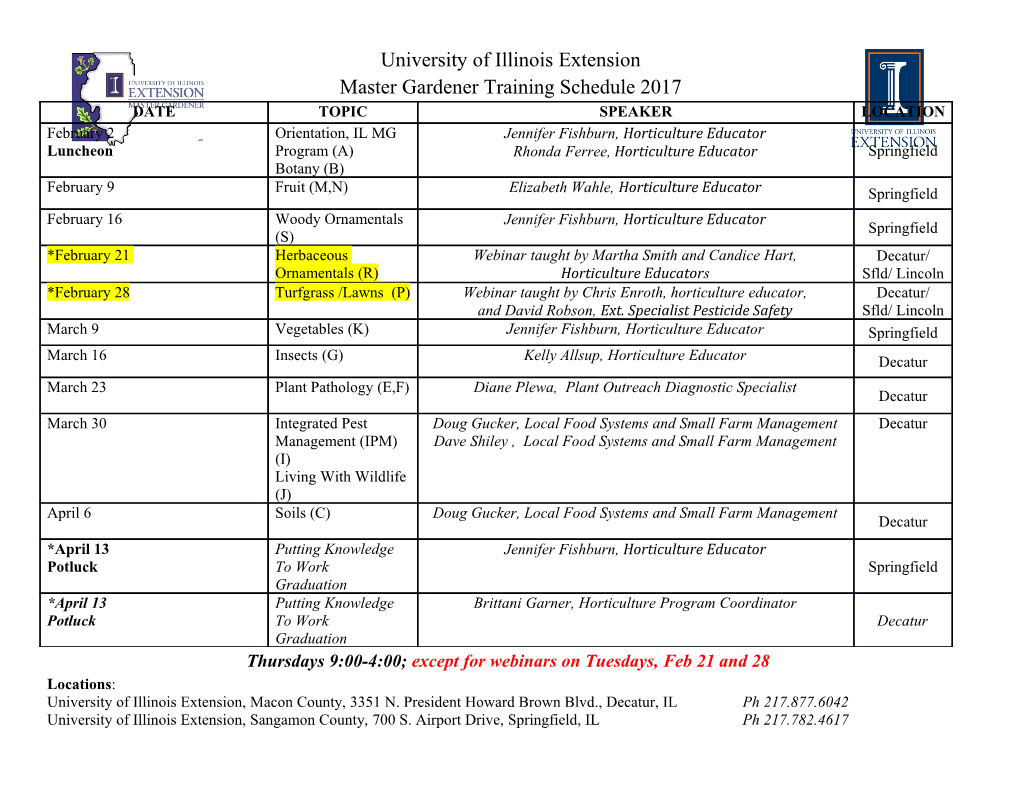
Project No. 10-682 Investigation of the Use of Laser Shock Peening for Enhancing Fatigue and Stress Corrosion Cracking Resistance of Nuclear Energy Materials Fuel Cycle/Reactor Concepts Mission Relevant Investigator Initiated Research Vijay K. Vasudevan University of Cincinna Sue Lesica, Federal POC Sebasen Teysseyre, Technical POC Final Report Project Title: Investigation of the Use of Laser Shock Peening for Enhancing Fatigue and Stress Corrosion Cracking Resistance of Nuclear Energy Materials Technical Workscope: MR-IIR Covering Period: October 1, 2010 – June 30, 2016 Date of Report: March 7, 2017 Recipient: Name: University of Cincinnati Street: 2600 Clifton Ave. City: Cincinnati State: Ohio Zip: 45221 Contract Number: 102835 Project Number: 10-682 Principal Investigator: Vijay K. Vasudevan - (513) 556-3103 - [email protected] Abhishek Telang (PhD student); Chang Ye (Postdoctoral Fellow); S. R. Mannava and Dong Qian Collaborators: Sebastien Teysseyre, John Jackson (INL), B. Alexandreanu, Yiren Chen (ANL) Project Objective: The objective of this project, which includes close collaboration with scientists from INL and ANL, is to investigate and demonstrate the use of advanced mechanical surface treatments like laser shock peening (LSP) and ultrasonic nanocrystal surface modification (UNSM) and establish baseline parameters for enhancing the fatigue properties and SCC resistance of nuclear materials like nickel-based alloy 600 and 304 stainless steel. The research program includes the following key elements/tasks: 1) Procurement of Alloy 600 and 304 SS, heat treatment studies; 2) LSP and UNSM processing of base metal and welds/HAZ of alloys 600 and 304; (3) measurement and mapping of surface and sub-surface residual strains/stresses and microstructural changes as a function of process parameters using novel methods; (4) determination of thermal relaxation of residual stresses (macro and micro) and microstructure evolution with time at high temperatures typical of service conditions and modeling of the kinetics of relaxation; (5) evaluation of the effects of residual stress, near surface microstructure and temperature on SCC and fatigue resistance and associated microstructural mechanisms; and (6) studies of the effects of bulk and surface grain boundary engineering on improvements in the SCC resistance and associated microstructural and cracking mechanisms. TPOC: [email protected] Federal reviewers: [email protected] TABLE OF CONTENTS Section Page # Cover Page……………………………………………………………………………….. 1 1. Executive Summary ………………………………………………………………………. 4 2. Introduction ……………………………………………………………………………… 7 3. Effects of Laser Shock Peening on SCC Behavior of Alloy 600……………………………. 13 3.1 Introduction…………………………………………………………………………… 13 3.2 Experimental…………………………………………………………………………… 16 3.3 Results and Discussion…………………………………………………………………. 19 3.3 Conclusions…………………………………………………………………………….. 30 4. Effects of Laser Shock Peening on SCC Behavior of Alloy 600 in Tetrathionate Solution. 34 4.1 Introduction…………………..……………………………………………………….. 34 4.2 Experimental…………………………………………………………………………… 37 4.3 Results…………………………………………………………………………………. 43 4.4 Discussion………………………………………………………………………………. 56 4.5 Conclusions…………………………………………………………………. 60 5. Surface Grain Boundary Engineering of Alloy 600 for Improved Resistance to Stress Corrosion Cracking………………..……………………………………………………….. 63 5.1 Introduction…………………..……………………………………………………….. 64 5.2 Materials and Methods…………………………………………………………………. 65 5.3 Results…………………………………………………………………………………. 69 5.4 Discussion………………………………………………………………………………. 82 5.5 Conclusions…………………………………………………………………………….. 87 6. Iterative Thermomechanical Processing of Ally 600 for Improved Resistance to Corrosion and Stess Corrosion Cracking………………..…………………………………………….. 92 6.1 Introduction…………………..……………………………………………………….. 93 6.2 Materials and Methods…………………………………………………………………. 94 6.3 Results…………………………………………………………………………………. 99 6.4 Discussion……………………………………………………………………………. 113 6.5 Conclusions…………………………………………………………………………….. 118 7. Effect of Thermo-Mechanical Processing on Sensitization and Corrosion of Alloy 600 Stduied by SEM- and TEM-Based Diffraction and Orientation Imaging Techniques…….. 124 2 7.1 Introduction…………………..……………………………………………………….. 125 7.2 Materials and Methods………………………………………………………………. 126 7.3 Results and Discussion………………………………………………………………. 129 7.4 Conclusions……………………………………………………………………………. 146 8. Effect of Laser Shock Peening on Stress Corrion Cracking of Alloy 600 in Simulated Pressurized Water Rector Environment……………..………………………………….. 151 8.1 Introduction…………………..…………………………………………………….. 151 8.2 Experimental………………………………………………………………………… 152 8.3 Results and Discussion………………………………………………………………. 156 8.4 Conclusions……………………………………………………………………………. 162 9. Effect of Mechanical Loading and Temperature on Relaxation of Residual Stresses Induced by Surface Treatments in Alloy 600……………..……………………………….. 163 9.1 Introduction…………………..……………………………………………………….. 163 9.2 Experimental…………………………………………………………………………… 165 9.3 Results and Discussion………………………………………………………………. 166 9.4 Conclusions…………………………………………………………………………….. 170 10. Gradient Nanostructure and Residual Stress Induced by Ultrasonic Nanocrystal Surface Modification in 304 Austenitic Stainless Steel for High Strength and High Ductility…… 172 10.1 Introduction…………………………………………………………………………… 173 10.2 Experimental Details………………………………………………………………… 174 10.3 Results and Analysis……………………………………………………………….. 178 10.4 Discussion…………………………………………………………………………… 194 10.4 Conclusions…………………………………………………………………………. 202 11. Effects of Ultrasonic Nanocrystal Surface Modification on the Residual Stress, Microstructure and Corrosion Resistance of SS304 Welds………………………………… 208 11.1 Introduction…………………………………………………………………………. 208 11.2 Experimental Methods…………………..…………………………………………… 209 11.3 Results and Discussion………………………………………………………………. 212 11.4 Conclusions………………………………………………………………………….. 218 12. Directions for Future Work………………………………………………..………………. 221 13. Publications ……………………………………………………………………………….. 222 14. Presentations ………………………………………………………………………………. 223 3 1.0 Executive Summary Stress corrosion cracking (SCC) of Alloy 600 has been a major problem in commercial light water reactor (LWR) nuclear power plants. Localized corrosion and intergranular SCC (IGSCC) have been observed in Alloy 600 in the high temperature (288-340 ˚C) pure water environment of LWRs. Additionally, IGSCC of Alloy 600 has been reported even at room temperature under certain conditions in thiosulfate and tetrathionate solutions. In general, SCC can be attributed to the presence of tensile stress, an aggressive environment and a susceptible microstructure. Therefore, SCC mitigation techniques address these factors by modifying the environment, metallurgical processing treatments and alleviating the tensile stresses by mechanical surface treatments/stress relief. This study investigated the application of laser shock peening (LSP) as a technique to mitigate SCC in Alloy 600. LSP induced large compressive residual stresses (-550 MPa) that decreases gradually through depth. The pressure pulse generated during the LSP treatment causes plastic deformation, resulting in high dislocation density, twins and formation of misoriented sub-grains/crystallites that have sizes in the range of 50-300 nm in the near-surface region. Slow strain rate tests (SSRTs) and constant load tests performed in tetrathionate solution at room temperature were used to evaluate the effect of LSP on the SCC behavior. LSP treated samples had a significantly longer time to failure and reduced susceptibility to SCC as compared with untreated sensitized Alloy 600. These improvements were attributed to LSP induced compressive residual stresses, increased yield strength (YS) and hardening caused by near- surface microstructural changes. SSRTs in simulated PWR environment also show similar results with higher YS, tensile strength and strain to failure. Additionally, the gage section shows fewer cracks and smaller crack lengths in the LSP treated samples as compared with the untreated samples. 4 The other approach involved using mechanical surface treatments/cold work followed by annealing to engineer the Alloy 600 microstructure for increased resistance to corrosion and IGSCC. We demonstrated a novel method of surface grain boundary engineering (SGBE) in Alloy 600 using iterative cycles of ultrasonic nanocrystalline surface modification (UNSM) treatment and strain annealing. Three cycles of UNSM and strain annealing at 900-1000 ˚C were used to modify the microstructure to a depth of 250 µm from the surface. This surface treatment based method increased the fraction of low coincident site lattice (CSL) grain boundaries whilst decreasing the fraction and connectivity of random high angle boundaries (HABs) in the near surface region. Similar results were achieved using thermo-mechanical processing (TMP) with iterative cycles of 10% cold work and strain annealing in Alloy 600. A disrupted random HAB network and large fraction (70%) of CSL boundaries (Σ3-Σ27) reduced the propensity to sensitization. SSRTs in tetrathionate solutions at room temperature show that SGBE and TMP lowered the susceptibility to intergranular SCC. Detailed analysis using EBSD showed cracks arrested at J1 (1-CSL) and J2 (2-CSL) type of triple junctions. The probability of crack arrest, calculated using percolative models, was higher after SGBE and TMP in Alloy 600 and explains the improved IGSCC resistance. The effects of UNSM on residual
Details
-
File Typepdf
-
Upload Time-
-
Content LanguagesEnglish
-
Upload UserAnonymous/Not logged-in
-
File Pages225 Page
-
File Size-