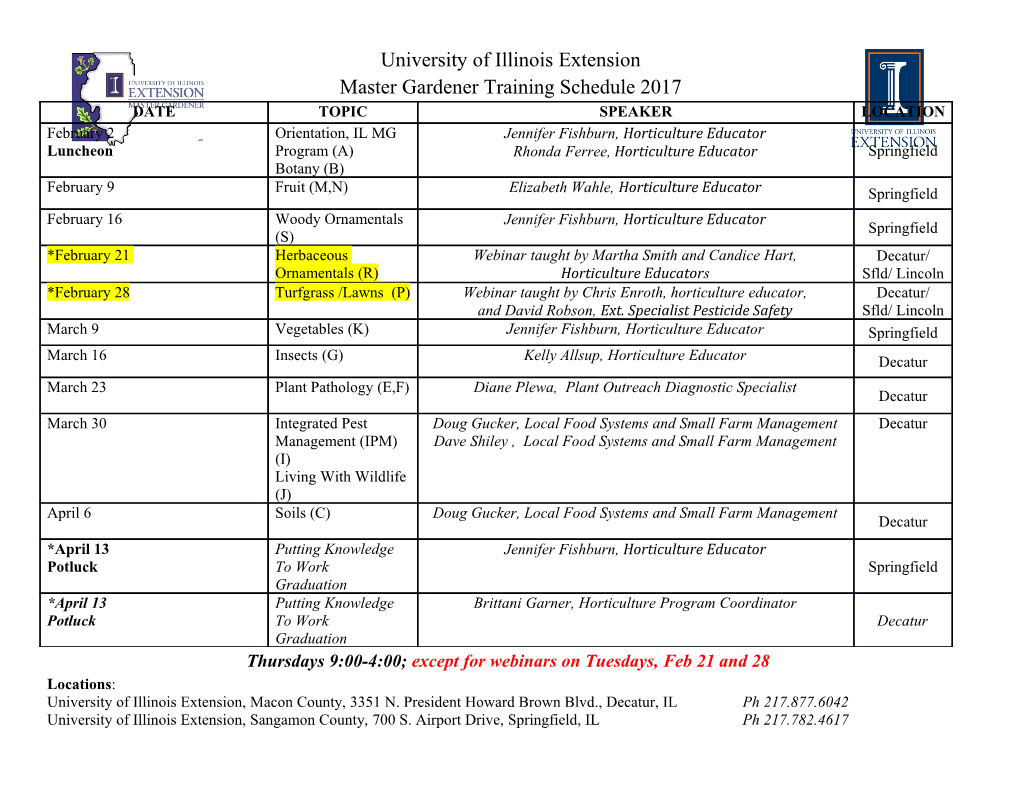
MODELING OF MULTIBODY DYNAMICS IN FORMULA SAE VEHICLE SUSPENSION SYSTEMS A Thesis Submitted to the Faculty of Purdue University by Swapnil Pravin Bansode In Partial Fulfillment of the Requirements for the Degree of Master of Science in Mechanical Engineering May 2020 Purdue University Indianapolis, Indiana ii THE PURDUE UNIVERSITY GRADUATE SCHOOL STATEMENT OF THESIS APPROVAL Dr. Jing Zhang, Chair Department of Mechanical and Energy Engineering Dr. Hamid Dalir Department of Mechanical and Energy Engineering Dr. Lingxi Li Department of Electrical and Computer Engineering Approved by: Dr. Jie Chen Head of the Graduate Program iii Dedicated to loving memory of my mother and grandmother. iv ACKNOWLEDGMENTS I would like to express sincere gratitude to my advisor Dr. Jing Zhang for providing guidance and being an incredible source of knowledge throughout my research work. I would like to thank members of advisory committee, Dr. Hamid Dalir and Dr. Lingxi Li for sharing their thoughts and feedback which helped me broaden my perspective of research work. I would also like to thank Mr. Jerry Mooney for his valuable inputs for my thesis. I would like to thank IUPUI and entire staff of Department of Mechanical and Energy Engineering for providing support and assistance during various stages of my research. I would also like to thank my lab mates Tejesh, Harshal, Michael Golub, Jian, Xuehui and Lingbin for their support. Lastly, I would like to thank my aunt and all my family, for supporting me both financially and emotionally , along with my friends, Madhura, Tripthi, Jay, Fermin, Sailee and Riddhi for always being with me throughout my graduate journey. v TABLE OF CONTENTS Page LIST OF TABLES :::::::::::::::::::::::::::::::::: viii LIST OF FIGURES ::::::::::::::::::::::::::::::::: ix SYMBOLS :::::::::::::::::::::::::::::::::::::: xii ABBREVIATIONS :::::::::::::::::::::::::::::::::: xiv ABSTRACT ::::::::::::::::::::::::::::::::::::: xv 1 INTRODUCTION :::::::::::::::::::::::::::::::: 1 1.1 Formula SAE and formula hybrid vehicles :::::::::::::::: 1 1.2 Multibody dynamics :::::::::::::::::::::::::::: 3 1.3 Motivation :::::::::::::::::::::::::::::::::: 5 1.4 Knowledge gap ::::::::::::::::::::::::::::::: 7 1.5 Objective of thesis ::::::::::::::::::::::::::::: 8 1.6 Structure of thesis ::::::::::::::::::::::::::::: 8 2 LITERATURE REVIEW :::::::::::::::::::::::::::: 10 2.1 Suspension system parameters ::::::::::::::::::::::: 10 2.1.1 Camber angle :::::::::::::::::::::::::::: 10 2.1.2 Caster angle ::::::::::::::::::::::::::::: 11 2.1.3 Kingpin inclination ::::::::::::::::::::::::: 12 2.1.4 Scrub radius ::::::::::::::::::::::::::::: 13 2.1.5 Wheel rate :::::::::::::::::::::::::::::: 13 2.1.6 Roll center height and roll rate :::::::::::::::::: 15 3 EXAMPLE OF MCPHERSON STRUT SUSPENSION SYSTEM :::::: 17 4 FSAE VEHICLE MBD MODELS :::::::::::::::::::::::: 22 4.1 Model description :::::::::::::::::::::::::::::: 22 4.1.1 Front suspension :::::::::::::::::::::::::: 22 vi Page 4.1.2 Rear suspension ::::::::::::::::::::::::::: 23 4.1.3 Full vehicle assembly :::::::::::::::::::::::: 24 4.2 Vehicle tests ::::::::::::::::::::::::::::::::: 25 4.2.1 Parallel wheel travel test for front suspension system :::::: 25 4.2.2 Parallel wheel travel test for rear suspension system ::::::: 28 4.2.3 Skid-pad test for full vehicle assembly ::::::::::::::: 32 5 WHEEL MODEL ::::::::::::::::::::::::::::::::: 37 5.1 Wheel slip calculations ::::::::::::::::::::::::::: 38 5.2 Tire side slip angle ::::::::::::::::::::::::::::: 39 5.2.1 Four wheel method ::::::::::::::::::::::::: 39 5.2.2 Single track or bicycle model method ::::::::::::::: 40 5.3 Friction coefficient ::::::::::::::::::::::::::::: 42 6 SUSPENSION MODEL ::::::::::::::::::::::::::::: 43 6.1 Suspension motion ratio :::::::::::::::::::::::::: 44 6.2 Lateral load transfer :::::::::::::::::::::::::::: 47 6.2.1 Load transfer from unsprung mass :::::::::::::::: 48 6.2.2 Load transfer from direct lateral force ::::::::::::::: 48 6.2.3 Load transfer from body roll :::::::::::::::::::: 49 7 MODIFIED VERSION OF THE FSAE VEHICLE :::::::::::::: 52 7.1 Model description :::::::::::::::::::::::::::::: 52 7.1.1 Front suspension system :::::::::::::::::::::: 52 7.1.2 Rear suspension system :::::::::::::::::::::: 53 7.1.3 Full vehicle assembly :::::::::::::::::::::::: 54 7.2 Modified vehicle tests :::::::::::::::::::::::::::: 55 7.2.1 Parallel wheel travel test for front suspension system :::::: 55 7.2.2 Parallel wheel travel test for rear suspension system ::::::: 61 7.2.3 Skid-pad test for full vehicle assembly ::::::::::::::: 66 7.3 Comparison between current models with literature data :::::::: 71 vii Page 8 CONCLUSION :::::::::::::::::::::::::::::::::: 78 9 CONTRIBUTION OF THE THESIS WORK ::::::::::::::::: 82 REFERENCES :::::::::::::::::::::::::::::::::::: 83 PUBLICATION ::::::::::::::::::::::::::::::::::: 85 viii LIST OF TABLES Table Page 1.1 Limitation on accumulator capacity :::::::::::::::::::::: 3 ix LIST OF FIGURES Figure Page 1.1 Present IUPUI Jaguar FSAE vehicle ::::::::::::::::::::: 5 1.2 Spring-damper location in the FSAE vehicle ::::::::::::::::: 6 2.1 Camber angle [12] :::::::::::::::::::::::::::::::: 11 2.2 Caster angle [12] :::::::::::::::::::::::::::::::: 12 2.3 Kingpin inclination [12] :::::::::::::::::::::::::::: 12 2.4 Roll center location [12] :::::::::::::::::::::::::::: 15 3.1 McPherson strut wire suspension model ::::::::::::::::::: 17 3.2 McPherson strut solid suspension model ::::::::::::::::::: 18 3.3 Wheel rate ::::::::::::::::::::::::::::::::::: 19 3.4 Toe variation :::::::::::::::::::::::::::::::::: 19 3.5 Caster variation ::::::::::::::::::::::::::::::::: 20 3.6 Camber angle variation ::::::::::::::::::::::::::::: 21 4.1 Front suspension system for present vehicle :::::::::::::::::: 22 4.2 Rear suspension system for present vehicle :::::::::::::::::: 23 4.3 Full vehicle assembly for present vehicle ::::::::::::::::::: 24 4.4 Camber variation for front suspension system :::::::::::::::: 25 4.5 Toe variation for front suspension system ::::::::::::::::::: 26 4.6 Normal force variation for front suspension system :::::::::::::: 27 4.7 Motion ratio for front suspension system ::::::::::::::::::: 27 4.8 Roll center location for front suspension system ::::::::::::::: 28 4.9 Camber variation for rear suspension system ::::::::::::::::: 29 4.10 Toe variation for rear suspension system ::::::::::::::::::: 29 4.11 Roll center location for rear suspension system :::::::::::::::: 30 4.12 Motion ratio for rear suspension system ::::::::::::::::::: 31 x Figure Page 4.13 Normal force variation for rear suspension system :::::::::::::: 31 4.14 Skid-pad test :::::::::::::::::::::::::::::::::: 32 4.15 Tire side slip angle in front at constant acceleration ::::::::::::: 33 4.16 Tire side slip angle in rear at constant acceleration ::::::::::::: 34 4.17 Tire side slip angle in front and rear at constant velocity :::::::::: 35 4.18 Yaw at constant acceleration :::::::::::::::::::::::::: 36 5.1 Four wheel method [16] :::::::::::::::::::::::::::: 40 5.2 Single track model [16] ::::::::::::::::::::::::::::: 41 6.1 Suspension model :::::::::::::::::::::::::::::::: 43 6.2 Motion ratio [20] :::::::::::::::::::::::::::::::: 45 6.3 Lateral load transfer [20] :::::::::::::::::::::::::::: 47 7.1 Modified front suspension system ::::::::::::::::::::::: 53 7.2 Modified rear suspension system :::::::::::::::::::::::: 53 7.3 Modified full vehicle assembly ::::::::::::::::::::::::: 54 7.4 Camber variation for modified front suspension system ::::::::::: 55 7.5 Camber comparison for modified front suspension system :::::::::: 56 7.6 Toe variation for modified front suspension system ::::::::::::: 57 7.7 Normal force variation for modified front suspension system :::::::: 58 7.8 Motion ratio for modified front suspension system :::::::::::::: 59 7.9 Roll center location for modified front suspension system :::::::::: 59 7.10 Geometric representation of roll center :::::::::::::::::::: 60 7.11 Roll center comparison for modified front suspension system :::::::: 61 7.12 Camber variation for modified rear suspension system :::::::::::: 61 7.13 Camber comparison for modified rear suspension system :::::::::: 62 7.14 Toe variation for modified rear suspension system :::::::::::::: 63 7.15 Normal force variation for modified rear suspension system ::::::::: 64 7.16 Motion ratio comparison for modified rear suspension system :::::::: 64 7.17 Roll center location for modified rear suspension system :::::::::: 65 xi Figure Page 7.18 Roll center comparison for rear suspension system :::::::::::::: 66 7.19 Skid-pad test setup ::::::::::::::::::::::::::::::: 68 7.20 Slip angle comparison in front and rear suspension system ::::::::: 68 7.21 Yaw rate for modified version of the vehicle ::::::::::::::::: 69 7.22 Skidpad test comparison :::::::::::::::::::::::::::: 70 7.23 Lateral load comparison for modified version of the vehicle ::::::::: 71 7.24 Camber variation comparison of modified front system and reference [21] : 71 7.25 Camber variation comparison of modified rear system and reference [21] :: 72 7.26 Toe variation comparison of modified front system and reference [21] ::: 73 7.27 Motion ratio comparison of modified front system and reference [16] :::: 74 7.28 Motion ratio comparison of modified rear system and reference [21] :::: 74 7.29 Motion ratio comparison with reference [22] ::::::::::::::::: 76 7.30 Roll center location comparison with reference [23] ::::::::::::: 77 xii SYMBOLS KS Spring rate KW Wheel rate KφF Front roll rate (Nm/deg) KφR Rear roll rate
Details
-
File Typepdf
-
Upload Time-
-
Content LanguagesEnglish
-
Upload UserAnonymous/Not logged-in
-
File Pages103 Page
-
File Size-