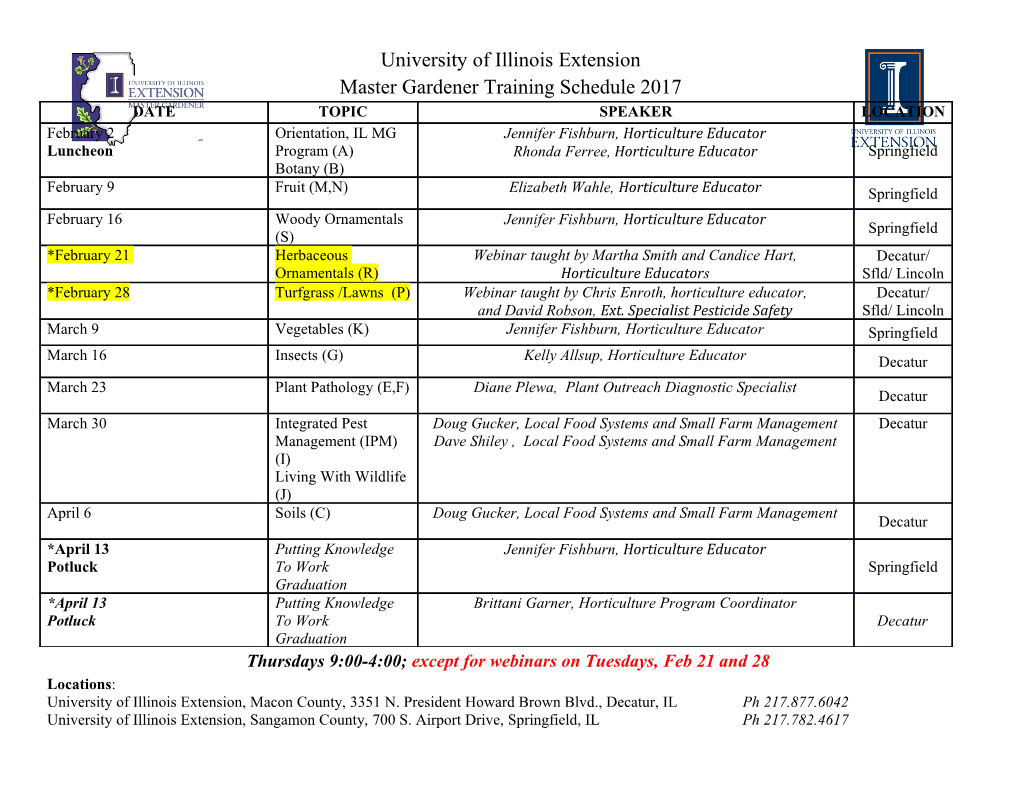
IN-SITU MEASUREMENT AND NUMERICAL SIMULATION OF LINEAR FRICTION WELDING OF Ti-6Al-4V Dissertation Presented in Partial Fulfillment of the Requirements for the Degree Doctor of Philosophy in the Graduate School of The Ohio State University By Kaiwen Zhang Graduate Program in Welding Engineering The Ohio State University 2020 Dissertation Committee Dr. Wei Zhang, advisor Dr. David H. Phillips Dr. Avraham Benatar Dr. Vadim Utkin Copyrighted by Kaiwen Zhang 2020 1 Abstract Traditional fusion welding of advanced structural alloys typically involves several concerns associated with melting and solidification. For example, defects from molten metal solidification may act as crack initiation sites. Segregation of alloying elements during solidification may change weld metal’s local chemistry, making it prone to corrosion. Moreover, the high heat input required to generate the molten weld pool can introduce distortion on cooling. Linear friction welding (LFW) is a solid-state joining process which can produce high-integrity welds between either similar or dissimilar materials, while eliminating solidification defects and reducing distortion. Currently the linear friction welding process is most widely used in the aerospace industry for the fabrication of integrated compressor blades to disks (BLISKs) made of titanium alloys. In addition, there is an interest in applying LFW to manufacture low-cost titanium alloy hardware in other applications. In particular, LFW has been shown capable of producing net-shape titanium pre-forms, which could lead to significant cost reduction in machining and raw material usage. Applications of LFW beyond manufacturing of BLISKs are still limited as developing and quantifying robust processing parameters for high-quality joints can be costly and time consuming. LFW is a highly dynamic process involving rapid heating and deformation at high strain rate (of the order of 10 s-1). Currently, there is a limited ii fundamental understanding of the temperature and deformation transients during LFW which are critical parameters to study the joint quality. This dissertation research aimed to (1) develop and valid a physics-based process model and (2) apply it to study the effect of processing parameters and work-piece geometry on temperature and deformation transients during LFW. Given the broad scope, the research was performed in collaboration with Boeing Research & Technology (Berkeley, MO), EWI (Columbus, OH), and OSU’s CEMAS (Columbus, OH). The key innovations generated from this dissertation include: Optimized sample geometries for high-temperature, high-strain-rate mechanical tests based on thermal-electrical-mechanical numerical simulations Measured temperature and deformation transients in-situ during LFW Developed a computationally efficient 2.5-D model considering heat conduction, stress, and severe plastic deformation that was validated for different heat inputs and work-piece geometries Highlights of the research approaches and outcomes are described in the following. Numerical models based on thermal-electrical-mechanical simulation in ABAQUS®, a commercially-available finite element code, were developed to correct true stress-strain data for high-temperature compression test, and to design a new specimen geometry for hot torsion test. The modeling results increased the accuracy of the Ti-6Al-4V flow stress data tested at different temperatures and strain rates in Gleeble® at Boeing Research & Technology. Initial welding of sub-scaled Ti-6Al-4V coupons with one square inch weld area was performed on a 20-ton mechanically driven LFW machine in EWI. Three heat inputs iii designated as low, medium and high energy were tested. A high-speed camera was utilized to monitor the entire welding process for each weld. Type-K thermocouples were instrumented through drilled holes at four different offset distances from the weld interface for temperature measurement. Full-scaled Ti-6Al-4V welding coupons and net-shape pre-forms with weld area of five and nine square inches respectively were performed on an MTI LF 35-75 hydraulic LFW welder at Lightweight Innovations for Tomorrow (LIFT). Same welding parameters described previously were employed to produce full-scaled LFW joints. Black and white speckle patterns were painted onto the coupon side surfaces to map the surface deformation in-situ by digital image correlation (DIC) via a high-speed camera. An infrared camera was also utilized to measure the surface thermal profiles near the interface during heating and cooling of the LFW process. Machine recorded experimental data such as oscillator positions, applied forging force and resultant shear force were used to calculate the effective interface friction coefficient as a function of processing time via Coulomb’s friction law. This effective friction coefficient was then inputted into the LFW process model to describe the interface heat generation based on frictional-sliding behavior. The computational efficient 2.5-D models considered a transverse cross section that was perpendicular to the oscillation direction. The simulation procedure consisted of two stages: the conditioning stage and the merged stage. Modeling of the conditioning stage involved frictional heating while modeling of the subsequent merged stage involved only plastic deformation heating. The models were used to predict the temperature, stress and iv deformation for the three different heat inputs as well as the different coupon geometries. The modeling results were consistent with the experimental data including thermocouple and infrared camera measured thermal profiles, machine recorded axial shortening (or upset), surface strains measured by DIC, and the final flash shapes. The results presented in this dissertation, taken as a whole, represented a significant step toward establishing a predictive simulation of LFW process. Such a predictive simulation tool is essential to ensure sound joints and parts in current and future generations of energy-efficient structures. v Dedication Dedicated to my parents and Heting Li Their love and support make me strive to be a better person vi Acknowledgments As an undergraduate laboratory assistant and later a graduate research associate in the last six years at The Ohio State University Welding Engineering Program, I would like to acknowledge a lot of people who helped me to make this study possible. First of all, I want to express deep appreciation to my academic advisor Dr. Wei Zhang for his selfless guidance over years. His support, patience, professional expertise, encouragement, kindly reminders, and demand for excellence always inspired and motivated me for striding forward. He also gave me many opportunities to advance my research as well as my professional development, and these experiences have all became invaluable life lessons and unforgettable memories so far in my life. I feel truly blessed, fortunate, and honored to have had the chance to work with him, and this research would not have been possible without his devotion. I would also like to thank Dr. Boian Alexandrov and Dr. John Lippold for bringing me into the Welding and Metallurgy Group when I was an undergraduate. Without their teaching and guidance, I could never make myself this far. Gratitude must also be extended to Dr. David Phillips and Dr. Avraham Benatar for serving in my dissertation committee and providing many guidance as well as teaching welding-related courses in the past a few years. I would also like to acknowledge the project team that made this research possible. First, many thanks to Mr. Austin Mann from Boeing Research & Technology for vii collaborating and leading the project (TMP R4-6). He provided materials and process parameters into this project and also involved in Gleeble® testing and analyses, machining of materials and welds, and post-weld heat treatment with his colleague Mr. Sean Thuston. Second, I would like to acknowledge Dr. Samuel Kuhr and Prof. Hamish Fraser at OSU for doing the material characterizations at CEMAS and providing adequate guidance and comments. Many thanks to Dr. Mike Eff at EWI and Mr. Zachary Danko at MTI for making linear friction welds and generating welding-related experimental data. Last but not least, I wish to acknowledge the support and guidance from the LIFT program management office, in particular Bhavi Shah (TMP R4-6 project manager) for the overall project management and arrangement of welding in LIFT at Detroit. I would also like to extend thanks to many former and present faculty, staff, graduate and undergraduate students in the Welding Engineering Program for their support and help over years and to this study. Especially Dr. Xun Liu for providing in-situ monitoring tools, Dr. Carolin Fink, Dr. Ying Lu, Dr. Daniel Tung, Dr. Tyler Borchers, Dr. Yousub Lee, Dr. Hyeyun Song, Dr. Adam Hope, Dr. Jim Rule, Dr. Collin Whitt, Dr. Xuesong Gao, Mr. Alexey Kuprienko, Mr. Ed Pfeifer, Mr. Marc Ruggeri (DSI), Mr. Tyler High, Mr. Grant Pfeifer, and Mr. Menachem Kimchi for their generous help and shared wisdom both mentally and technically on academic and in life. Finally, my family and my girlfriend Heting Li deserve recognition for their support, love, faith, patience, and sacrifice while I worked on this research and dissertation. I love you all. viii Vita May 31, 1992………………………………………….... Born-Xi’an, China 2010-2014……………………………………………......B.S. Welding Engineering, The Ohio State University 2014-2016………………………………………………. M.S. Welding Engineering, The Ohio State University 2016-present…………………………………………….
Details
-
File Typepdf
-
Upload Time-
-
Content LanguagesEnglish
-
Upload UserAnonymous/Not logged-in
-
File Pages296 Page
-
File Size-