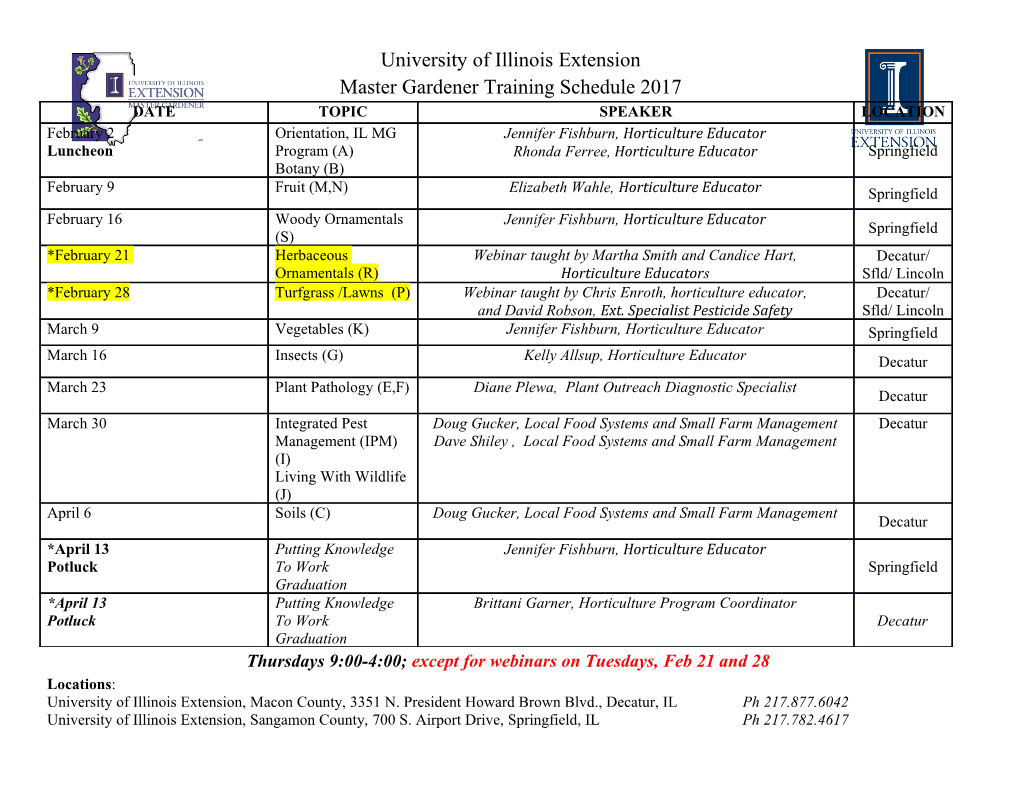
arc POWER MANAGEMENT STRATEGY FOR A PARALLEL HYBRID ELECTRIC TRUCK Introduction and Motivation Simulation model and preliminary rule-based control Dynamic programming techniques Improved rule-based control law Simulation results Dyno test results Conclusions Chan-Chiao (Joe) Lin, Huei Peng, Jessy W. Grizzle The University of Michigan arc What is a Hybrid Vehicle? • A HV has at least two sources of motive power - Prime: IC engines, fuel cells, gas turbines - Secondary: Batteries, flywheels, ultra- capacitors, hydraulics • The most popular type: ICE + battery/motor (HEV) • Bottom-line: “Better” than any single power source. COE Control Seminar-11/01-2002- 2 1 Potential Steps Towards Breakthrough arc in Fuel Efficiency 90 HEV DI ∆ 10mpg 80 80 ∆ 15mpg 70 MT 60 Small engine ∆ 10mpg Aero-roll 50 Light-weight ∆ 8mpg 40 ∆ 4mpg ∆ 6mpg 30 27 20 10 0 EstimatedMetro-Highway Fuel Economy (mpg) Description: Current Taurus Ultralite Aero/Roll Conv. P/T Match Opt. P/T Match Adv. P/T Adv. Hybrid P/T Weight (lbs): 3200 2000 2000 2000 2000 2000 TBD Powertrain: 3.0 L, 2-valve Same Same 1.4 L, A/T 1.4 L, Auto M/T 1.2L CIDI, Auto M/T Same Source: Mike Schwarz, Ford Motor Company COE Control Seminar-11/01-2002- 3 HEV Configurations arc Ê Series Î Simpler mechanical transmissions Î Optimum engine efficiency and low emission Î Both ICE and Electric drive rated to the maximum power requirement (main disadvantage) Î lower overall efficiency (main disadvantage) Ê Parallel (e.g. Chrysler MYBRID ESX2) Î More flexibility—sizing and control design more complicated Î Lower power/weight/cost, and better efficiency. Ê Series-parallel combination (e.g. Toyota Prius) COE Control Seminar-11/01-2002- 4 2 arc Growing Market (Toyota) 1997 1998 1999 2000 2001 2002/ 1997- Period 1-3 2002/3 Model Prius 323 17,653 15,243 19,011 29,459 7,402 89,091 Estima - - - - 5,886 5,840 11,726 Hybrid minivan Crown - - - - 1,574 520 2,094 mild hybrid system Coaster 9 3 12 15 9 8 56 hybrid (bus) Total by 332 17,656 15,255 19,026 36,928 13,770 102,967 year/month Cumulative 332 17,988 33,243 52,269 89,197 102,967 total http://www.toyota.com/about/news/environment/2002/04/22-1-hybrid.html COE Control Seminar-11/01-2002- 5 Advanced Powertrain arc 60 50 FUEL CELL SYSTEM USING H2 (GM Data) 40 HSDI DIESEL 30 Average Car Pass. Power G-DI ENGINE 20 10 PERCENT THERMAL EFFICIENCY Bus/Truck Average Average Bus/Truck Power 0 0 20406080100120 PERCENT LOAD Source: Ricardo Why hybrid vehicles? - load leveling - regenerative braking COE Control Seminar-11/01-2002- 6 3 Transportation Sector Contribution to Oil arc Gap Stacy C. Davis, ORNL, TRANSPORTATION ENERGY DATA BOOK: EDITION 21 COE Control Seminar-11/01-2002- 7 arc Ground Vehicle Energy Use 14 12 Actual Projected 10 Class 3-8 Trucks 8 Class 1-2 Trucks (Pickups, Vans, SUVs) 6 (90% 2a, 10% 2b) 4 Automobiles 2 0 Energy Use - Million Barrels per Day 1970 1980 1990 2000 2010 2020 source: EIA Annual Energy Outlook, 1998 Federal Highway Administration, Highway Statistics COE Control Seminar-11/01-2002- 8 4 arc Emission Ê Engine out vs. tail-pipe Ê Temperature effect? This presentation: Engine out, hot engine only V. Johnson, NREL COE Control Seminar-11/01-2002- 9 arc Nox Emission Stacy C. Davis, ORNL, TRANSPORTATION ENERGY DATA BOOK: EDITION 21 COE Control Seminar-11/01-2002- 10 5 arc PM Emission Stacy C. Davis, ORNL, TRANSPORTATION ENERGY DATA BOOK: EDITION 21 COE Control Seminar-11/01-2002- 11 arc Hybrid Vehicle Control Problems Main-loop Servo-loop Performance Fuel economy/ NVH/driveability/fuel target emission economy/emission “Control signal” High level Low level (throttle, (Power) current, duty cycle) Horizon/dynamics Long/slow Short/fast (detailed) (simple) To satisfy Government/ Consumers Green consumers Scenarios Driving cycles Test matrix Algorithm Optimal, Robust, adaptive, intelligent ad-hoc COE Control Seminar-11/01-2002- 12 6 Power Management Problem for Parallel HEV arc • Goal: To develop a control strategy to minimize fuel consumption (and emission) while meeting the power demand from the driver • Key problem: determine the total amount of power to be generated, and its split between the two power sources • Maintain adequate battery energy (charge sustaining) RegenerativeRechargeMotorEngineHybrid Mode ModeMode: Mode Braking: When? : WhenWhen?: When Mode and and how the much split? power? Engine Transmission Eng. Command Driver Control Gear Command Module Motor Command Battery Electric Motor COE Control Seminar-11/01-2002- 13 Preliminary Rule-Based Control Strategy arc Power assist Desired vehicle Actual vehicle 0.65 DriverFuel Consumption (kg/kW hr) speed speed Ê Low power 500 450 0.6 4 .2 Æ Motor only 0.26 0 27 the battery is charged by the 400 0. SOC 5 2 2 1 0. 23 . 2 0.55 0 . 350 0 Power request0 engine at a constant “recharge . Ê Medium power 2 300 1 Battery SOC 4 0.5 0 200power”400 600 level800 1000until1200 SOC1400 hits1600 1800the2000 250 6 Æ Use engine 1 .2 0.2 0 Time (sec) 200 2 Engine Torque (Nm) Engine Torque max boundary Charge 150 0.23 0.24 0.25 Ê High power 100 0.26 Sustaining .27 0 Pmot = −Pch , Peng =ÆPreqBoth+ Pch engine Strategy 50 Braking 800 1000 1200 1400 1600 1800 2000 2200 2400 & motor Engine Speed (rpm) Control Motor only Power Split Recharge Control Control • Regenerative braking • Friction brake • Motor only mode • Engine provides • Engine only mode additional power to • Hybrid mode charge the battery COE Control Seminar-11/01-2002- 14 7 Problems of Existing (Main-loop) Control arc Approach Ê Based on simple concepts (e.g., load leveling) and mostly static maps. Ê Tuning is done through trial-and-error. Ê Don’t know the full potential (is 20% improvement good?) Ê Not re-useable (fuel economy vs. fuel economy plus emission). COE Control Seminar-11/01-2002- 15 arc 2003 Fuel Economy Champions Honda Civic Honda Insight Toyota Prius (Manual) (Automatic) (Automatic) Gas Mileage 46/51 57/56 52/45 (City/Highway) http://www.fueleconomy.gov/feg/feg2000.htm COE Control Seminar-11/01-2002- 16 8 arc Outline Ê Introduction and Motivation Ê Simulation model and preliminary rule-based control results Ê Dynamic programming techniques Ê Improved rule-based control law Ê Simulation results Ê Dyno test results Ê Conclusions COE Control Seminar-11/01-2002- 17 Baseline Truck: Navistar International arc 4700 Series Engine Vehicle/Driveline Ê V8 DI Diesel Ê Total Mass: 7258 Kg Ê Turbocharged, Intercooled Ê Wheelbase: 3.7 m Ê 7.3 liters Ê CG Location: 2.2 m from front Ê Bore: 10.44 cm Ê Frontal Area: 5 m2 Ê Stroke: 10.62 cm Ê Air Drag Coefficient (CD): 0.8 Ê Compression Ratio: 17.4 Ê 4 Speed Automatic Transmission Ê Rated Power: 210 HP@2400 rpm Ê Rear Wheel Drive - 4x2 From www.navistar.com COE Control Seminar-11/01-2002- 18 9 arc Schematic of the Hybrid-Electric Truck Vehicle Dynamics Traction Force Engine Exhaust DS Gas Drivetrain Ê Parallel hybrid T EM PS ICM TC Trns D Motor Ê Post-transmission type C IM Air Inter cooler DS Power Control Module Battery COE Control Seminar-11/01-2002- 19 arc Hybrid Truck Parameters DI Diesel Engine V6, 5.475L, 157HP/2400rpm DC Motor 49kW Capacity: 18Ah Module number: 25 Lead-acid Battery Energy density: 34 (Wh/kg) Power density: 350 (W/kg) Automatic 4 speed, GR: Transmission 3.45/2.24/1.41/1.0 Vehicle Curb weight: 7504 kg COE Control Seminar-11/01-2002- 20 10 arc HE-VESIM in Simulink Hybrid Electric Vehicle Engine SIMulation Load Input Data T pump w eng w eng T pump Eng cmd T motor T shaft DIESEL ENGINE Gear Load Output Variables w shaft w motor cyc_mph clutch cmd w trans DRIVELINE Dring Cycle Motor cmd Current T wheel HEV Current soc w motor T motor w wheel DRIVER Controller ELECTRIC MOTOR Brake BATTERY Slope v veh VEHICLE DYNAMICS 0 slope Double Click Double Click to Close All to Plot Result Assanis, D.N. et al. “Validation and Use of SIMULINK Integrated, High Fidelity, Engine-In-Vehicle Simulation of the International Class VI Truck,” SAE Paper No. 2000-01-0288 Lin, C.C., Filipi, Z.S., Wang, Y., Louca, L.S., Peng, H., Assanis, D.N., and Stein, J.L., “Integrated, Feed-Forward Hybrid Electric Vehicle Simulation in SIMULINK and its Use for Power Management Studies”, SAE Paper No. 2001-01-1334 COE Control Seminar-11/01-2002- 21 arc Preliminary Rule-Based Control Ê Braking rule Fuel Consumption (kg/kW hr) Power 500 4 450 .2 0.26 0 assist 27 400 0. 5 2 2 1 0. 23 . 2 0 . 350 0 0 . 2 300 1 Ê Power split rule 4 250 6 1 .2 0.2 0 200 2 Engine Torque (Nm) Torque Engine 150 0.23 0.24 0.25 100 0.26 0.27 Ê Recharge rule 50 Motor 800 1000 1200 1400 1600 1800 2000 2200 2400 onlyEngine Speed (rpm) FE NOx (g/mi) PM (g/mi) (mi/gal) Conventional Truck 10.343 5.3466 0.5080 Hybrid Truck (Preliminary Rule-Base) 13.159 5.7395 0.4576 COE Control Seminar-11/01-2002- 22 11 arc Outline Ê Introduction and Motivation Ê Simulation model and preliminary rule-based control results Ê Dynamic programming technique Ê Improved rule-based control law Ê Simulation results Ê Dyno test results Ê Conclusions COE Control Seminar-11/01-2002- 23 Dynamic Optimization Based Algorithm arc Objective • To develop an optimal control policy that minimizes the fuel consumption over a giving driving cycle Advantage • Explore the full potential of hybridization • Benchmark for a better control strategy Methodology • A sequence of decisions applied to a dynamic system to minimize the total fuel costs --> Multistage Decision Process • Optimal control problem u(0) u(1) u(N −1) x(1) x(2) x(N −1) x(0) f (0) f (1) f (N-1) x(N) L(0) L(1) L( N −1) COE Control Seminar-11/01-2002- 24 12 Problem Formulation arc • Discrete-time Nonlinear System x(k +1) = f
Details
-
File Typepdf
-
Upload Time-
-
Content LanguagesEnglish
-
Upload UserAnonymous/Not logged-in
-
File Pages25 Page
-
File Size-