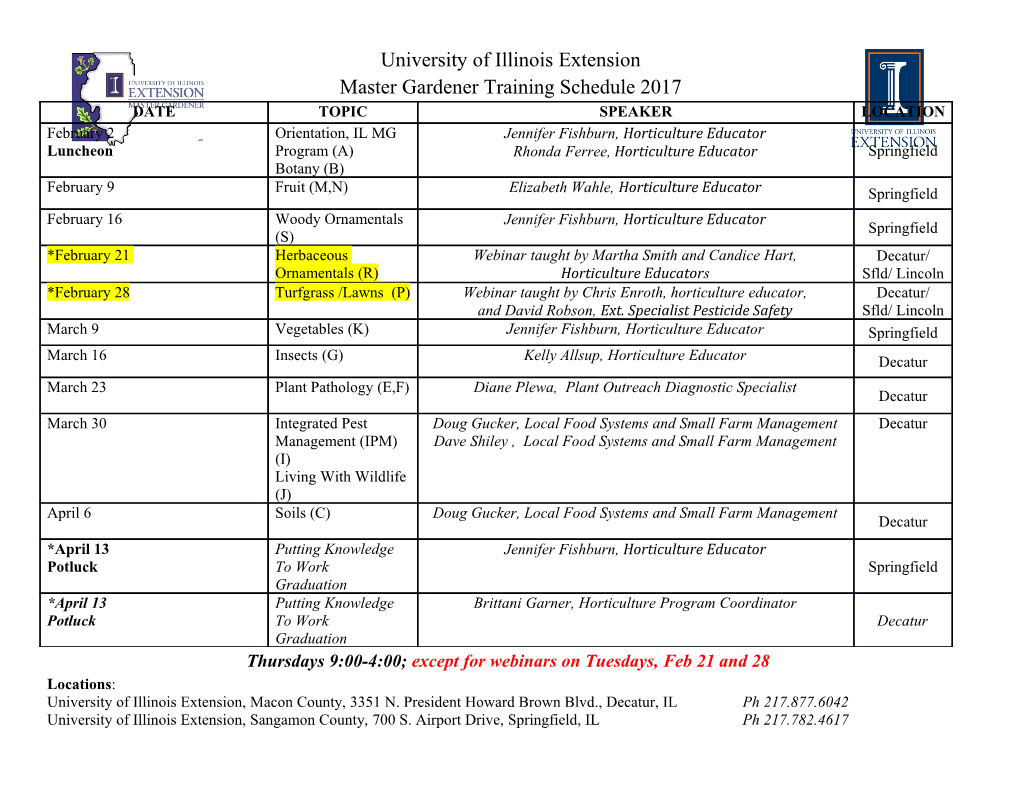
PROCEEDINGS, Thirty-Fourth Workshop on Geothermal Reservoir Engineering Stanford University, Stanford, California, February 9-11, 2009 SGP-TR-187 A SINGLE-WELL EGS CONFIGURATION USING A THERMOSIPHON Zhe Wang, Mark W. McClure and Roland N. Horne Stanford Geothermal Program Department of Energy Resources Engineering, 367 Panama St. Stanford University, CA 94305-2220, USA e-mail: [email protected], [email protected], [email protected] The design concept includes a number of novel ideas, ABSTRACT including: 1. Use of single well systems in place of This paper describes the investigation of a single-well multiwell systems, with level-to-level enhanced geothermal system comprised of a fracturing. downhole thermosiphon and a novel completion 2. Use of downhole heat exchangers in place of design using a downhole heat exchanger. The surface heat exchangers. thermosiphon is a device that takes advantage of the 3. Use of gravity head thermosiphons in place gravity head difference between liquid flowing down of well pumps. the annulus and vapor flowing up the tubing. 4. Use of downhole circulation of secondary Without a connection to a large reservoir volume, a working fluid in place of water. downhole heat exchanger will rapidly deplete the heat near the wellbore and cannot generate useful These four concepts may be expected to have a energy output for very long. Therefore to enhance number of advantages over conventional ideas, as heat extraction, the effectiveness of a second annulus will be described here. outside the casing was investigated. A working fluid would circulate by natural convection down the outer The conventional concept of an EGS includes a annulus and upwards through fractures created in the region of fractured rock, through which fluid is reservoir. This configuration has the advantages that circulated from one well to another well, Figure 1. a second injection well is not required, the need for downhole pumping is avoided by the thermosiphon effect, and the fractures carrying fluid through the reservoir makes the system sustainable. A limitation is that reliance on free convection to circulate fluid through an EGS reservoir does not result in large flow rates, which lowers the productivity. We constructed a coupled finite-difference wellbore and reservoir model representing the fluid mechanics, fluid phase behavior and heat transfer. We investigated the energy output of the system and the feasibility of sustainable deployment. INTRODUCTION Enhanced Geothermal Systems (EGS) are an attractive prospect for the development of base-load, carbon-free electricity generation. However, achieving EGS electrical generation at a reasonable cost is based upon a number of technological advances to reduce the expense of installation or to increase the rate at which energy can be recovered. Figure 1: Conventional two-well EGS configuration, This study is investigating an uncommon design for from Tester et al. (2006). an EGS system, which is a hybrid of a downhole heat exchanger and an EGS fracture network. An alternative idea is to fracture the formation and then produce and inject in the same well, as in Figure 2. The single well concept removes one of the wells, authors, including US Patent 4201060 (Outmans, and circulates fluids from one interval to another 1980). Nalla et al. (2004) analyzed the thermal output within the same well. The fluid may travel down the of this configuration, albeit with much smaller casing and back up the inner tubing. Variations of separation. In such a configuration, as shown in this idea have been suggested by a number of Figure 2, geothermal water would move convectively authors, including US Patent 4201060 (Outmans, through the annular space surrounding the heat 1980). exchanger, and circulate 500 to 1000 m through the fracture network in the formation. Hence the heat transfer to the heat exchanger is enhanced over simple conduction. It may also be feasible to use multilateral completions in place of, or as well as, fractures, although that concept is not discussed in this paper. At least in early adoption, EGS projects are likely to use binary power plants because of their ability to work effectively with lower temperature fluids. Some of the energy losses inherent in geothermal systems using binary power plants are associated with the energy required to pump the geothermal fluid to the surface to pass it through the heat exchangers. An alternative is to circulate the Figure 2: Sketch of single-well, coaxial downhole secondary fluid down the well bore, which heat exchanger with fractures. effectively puts the heat exchanger downhole. An important advantage to this is that there is no longer The advantage of a single-well system is that only any need for downhole pumps, which are one of the one well needs to be drilled (or perhaps an abandoned more problematic components in the operation of a oil or gas well could be used in which case no wells binary geothermal project. Secondary working fluid need to be drilled). could be pumped at the surface, where pumps and pump motors operate under more benevolent The disadvantage is that the connection of a fracture conditions and are easily accessible for maintenance. network to a single well in such a configuration has yet to be demonstrated in a geothermal rock. The term thermosiphon (sometimes spelled thermosyphon) is somewhat loosely applied to Our study includes the concept of a downhole heat devices that circulate fluid (and heat) due to exchanger, also shown in Figure 2. Traditional variations in buoyancy between fluids of differing coaxial downhole heat exchangers have been used in temperature and sometimes different phase (liquid direct use applications. The problem with using a and vapor). Among many other applications, the device that extracts heat only by conduction is that two-phase form of the devices has been used to cool conduction is unable to bring heat to the wellbore computer processors. It is this two-phase type of very quickly or for very long, and thus cannot be thermosiphon that seems most appropriate for used for large scale heat extraction (Nalla et al., geothermal use. 2004). One advantage of thermosiphon in downhole heat We explored the idea of connecting the heat exchanger is to remove the need for a downhole exchanger to an EGS fracture network, which would pump. Downhole pumps have drawbacks in two bring additional heat to the wellbore. Water would ways: firstly, in the harsh downhole environment circulate through the reservoir and through an outer pumps have relatively short times between repairs; annulus, between the outside of the casing and the secondly, it is less efficient thermodynamically to use drilled radius of the wellbore. Circulation through pumps to pressurize the fluid and then use it in heat the second annulus and through the reservoir exchangers on the surface (DiPippo, 2008). Another fractures is driven by free convection. The advantage of the thermosiphon is to make use of the convection brings additional heat to the heat tremendous pressure difference between the exchanger, and may extend the duration of time that outflowing and inflowing fluid to provide a source of heat can be extracted. hydraulic energy. The thermosiphon effect can be achieved by circulating the secondary working fluid Our idea of enhancing heat flow to the device would downhole, through the coaxial downhole heat be to fracture the formation from two intervals 500 to exchanger. The boiling point of the working fluid, 1000 m apart, as has been suggested by a number of (typically isopentane, but other choices are possible), 2 is lower than that of water, which results in a more The heat transfer from the reservoir by convection prominent thermosiphon effect than would be dominates because conduction through the rock to the achieved with water. A second reason to circulate the wellbore is small, especially in the long term. secondary working fluid is to prevent scaling in the However, the rate of convection is limited by the tubing. flow rate through the reservoir. In a conventional two-well EGS design, the density difference exists The concept of the downhole thermosiphon, depicted over the entire length of the wellbores from surface to in Figure 2, can be described as follows: cold bottom, and circulation by pumping from the surface secondary working fluid is injected into the annulus is also possible. Therefore a lower rate of heat between the tubing and casing, and extracts heat from extraction would be achieved in a system that uses a formation as it flows downward. In the working part downhole heat exchanger, unless the circulation rate of the formation, a second annulus outside the device in the reservoir can be improved. allows formation fluid to circulate from one fractured interval to the other. There is no contact between the working fluid in the wellbore and in the fluid in the METHODOLOGY formation. As opposed to only heat conduction, the heat transfer is enhanced by the convective flows in the fracture and in the second annulus. After the 1. Wellbore Calculations downflowing fluid is heated, it will be returned to the A numerical wellbore model was built to simulate the surface through the inner tubing. It may be useful to heat transfer between coaxial flow in the wellbore install a choke at the base of the tubing string to and the hot surrounding rock. Heat transfer occurs depressurize the upflowing fluid to achieve within the coaxial tubings between upward flow and vaporization, which would thus enhance the downward flow, as well as between the wellbore and thermosiphon behavior. Once the thermosiphon is the surroundings. Mass balance, momentum equation operating, the working fluid would circulate and energy conservation complete the wellbore spontaneously in the wellbore, and the pressure model (Ouyang and Belanger, 2004). difference between upward and downward flows at ∂ρ ∂(ρq) πr2 = (1) the surface would be recovered in the binary turbine.
Details
-
File Typepdf
-
Upload Time-
-
Content LanguagesEnglish
-
Upload UserAnonymous/Not logged-in
-
File Pages12 Page
-
File Size-