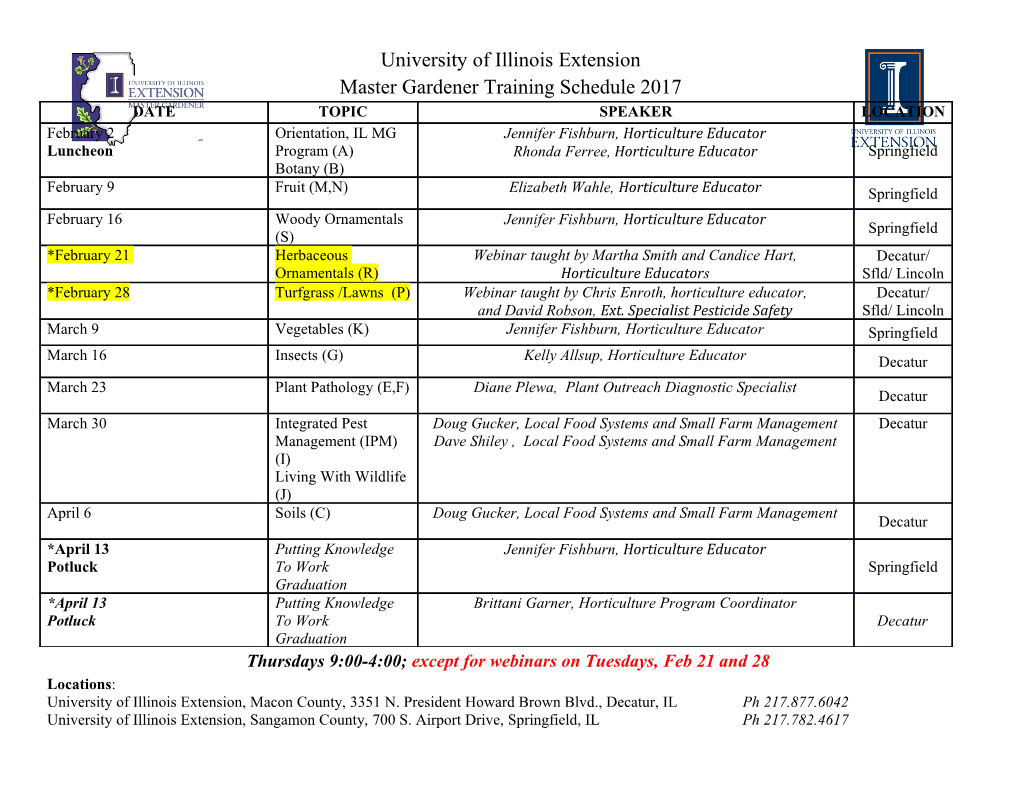
Failure of the HP Boiler Feed Water Pump on an Ammonia Plant A catastrophic failure occurred on the main High-Pressure Boiler Feed Water Pump Train on an Ammonia Plant. The direct cause of the failure was flow reversal from the Boiler Feed Water system and/or the Steam Drum, to the turbine driven High Pressure Boiler Feed Water Pump. While the failure of the pump is the focus of the paper, the identified causal factors involve failures of several auxiliary operating systems, which are also discussed. The paper presents the sequence of events and associated root causes that resulted in the failure of the pump as well as recommendations to prevent a re-occurrence. Godfrey Harrylal, Shiva Maharaj Industrial Plant Services Limited, Trinidad and Tobago, W.I. Introduction valves in the discharge piping of the pumps are designed to prevent liquid vaporization in the he high-pressure boiler feed water pump casing and pump damage, by ensuring positive train of an ammonia plant experienced a flow. The ARC valves on each pump also act as failure on 25th September 2015. The fail- check valves to prevent reverse flow. The pumps T ure occurred in a 1,850 MTPD (2,040 are also furnished with minimum flow lines from STPD) ammonia plant. This paper describes the the ARC valves that converge to a single line failure that occurred, the investigations and the back to the deaerator. lessons learnt. The turbine utilizes a mechanical hydraulic speed governor for speed control. The governor con- trols turbine speed by adjusting the quantity of System Configuration MP steam supplied to the turbine. The governor As shown in Figure 1, boiler feed water (BFW), has an output between 0 – 100% representing leaving the deaerator, is directed to the steam minimum (3,026 rpm) to maximum (3,728 rpm) drum for the purpose of high pressure (HP) steam governor speed settings. The DCS boiler feed generation using two (2) identical boiler feed wa- water flow controller, acts in two ways. It con- ter pumps. The main HP BFW pump is driven trols the speed set point of the turbine and also by an API 611 condensing turbine which utilizes the output to the control valve on the discharge medium pressure (MP) steam, and the standby of the standby pump. HP BFW pump is driven by an electric motor, which operates at the 4,160V level. Deaerated boiler feed water from the BFW pumps is fed to the steam drum via the three paths The HP BFW pumps are API 610 centrifugal each with a control valve and a tilting disc check multi-stage, opposed impeller, horizontally split valve. Two of the paths include BFW pre-heat- volute pumps. Automatic recirculation (ARC) ing and steam generating shell and tube heat ex- changers. 2018 41 AMMONIA TECHNICAL MANUAL STEAM DRUM 40 LP Steam FT CH-V3 CH-V2 CH-V1 Restriction Orifice Control RO-1 Val ve DEAERATOR CV1 Restriction BFW Restriction Orifice Preheating/ Orifice RO-A RO-B Steam HP BFW Gen. Pumps Heat Control Exchangers Val ve CV2B To Dump Control Val ve CV2A Turbine Control Valve CV3 Control Valve Flow Control Valve FCV Temperature Flow Indicator Indicator Figure 1. Simplified System Diagram Incident Description which initiated a shutdown of the primary re- former and downstream systems (total plant trip) On 25th September 2015, the plant experienced a as per design. spurious activation of the process air compressor shutdown signal resulting in the synthesis gas With the main process systems offline a plant op- compressor and downstream steam generating erator was dispatched to initiate shutdown of the equipment to shut down as per the plant’s design main and standby BFW pumps which were still interlock logic. Despite the shutdown signal that online. The operator utilized the mechanical trip initiated these events, the process air compressor lever on the turbine driver for the main HP BFW remained online which resulted in a deficit MP pump and initially observed a speed reduction. steam mass balance since the process air com- Within seconds, the operator heard an accelerat- pressor is one of the largest consumers of MP ing sound and observed the turbine speed to be steam. increasing past 5200 rpm (well over the maxi- mum of 3728 rpm). An instruction was given by The ensuing steam system upset resulted in the the shift supervisor to evacuate the area immedi- following sequence of events over a 40 minute ately and within seconds the catastrophic failure period: a high steam drum level, low BFW flow of the main BFW pump and turbine unit oc- to the steam drum, the automatic start of the curred. Thankfully, only minor injury was sus- standby HP BFW pump on low flow, no BFW tained by an operator which was treated by on flow to the steam drum and eventually low steam site first aid. Figure 2 shows the resulting dam- drum level. These events culminated in the acti- age. vation of the steam drum low level interlock AMMONIA TECHNICAL MANUAL 42 2018 Figure 2. A – BFW pump & turbine view from pump discharge side; B – Dispersion of components; C – BFW pump turbine damage; D – BFW pump shaft damage Actions Before the BFW Pump Failure closing of the valve was still in progress. It is believed that the turbine’s mechanical hydraulic During the steam upset with the trip of the syn- governor compensated for the reduction in steam thesis gas compressor train, the steam drum level flow by opening to allow more flow as evidenced was rising. The plant operators attempted to con- by a return to 3500rpm. The corresponding drop trol the steam drum level by reducing the BFW in discharge flow also had the unintended side ef- flow from the main pump. To reduce the BFW fect of auto-starting the standby pump against its flow, the speed of the BFW turbine was reduced closed discharge control valve. The steam inlet by using the governor control to bring the turbine valve was then reopened from the partially closed speed to minimum governor. With the level still position. rising, the flow through the steam inlet valve for the turbine driver of the main BFW pump was re- As the steam system was now being managed, duced by a plant operator partially closing the the steam drum level began to fall. The plant op- valve. This action only momentarily dropped the erators at this time did not observe any flow be- main pump’s speed from 3500rpm to 1900rpm. ing indicated on the outlet of the pumps. Without The pump’s speed returned to 3500rpm while the isolating the main pump, the discharge control 2018 43 AMMONIA TECHNICAL MANUAL valve on the standby pump was opened fully, but Inspection of the ARC valve on the main pump still no flow was observed. The steam drum level revealed the presence of debris lodged between continued to fall until the eventual plant trip due and around the main check valve and lower body to low-low steam drum level. seating surfaces, likely preventing the check valve from closing fully, shown in Figures 3B & 3C. The vortex plug on the recirculating/bypass Findings end of the ARC was also found to be stuck in the valve body, possibly restricting bypass flow. The Inspection Findings debris was confirmed to be a section of the The steam turbine was a total wreck with the tur- pump’s casing inter-stage ring. The pump suc- bine casing disintegrated and the rotor compo- tion strainer, shown in Figure 3D, was found to nents dispersed across the site. The damage be distorted in a collapsed inverted condition noted on the pump skid and foundation indicated which suggests flow reversal and was found to be clockwise rotation from the drive end of the train, fouled on both the upstream and downstream indicating that the machine was experiencing re- sides with the pump rotor’s wear ring material verse rotation as it usually operates in a counter- also found in the ARC valve. clockwise direction from this frame of reference. This damage, combined with the dispersion of Of the three check valves on the lines to the parts shown in Figure 2, indicated reverse rota- Steam Drum, two (CH-V1 & CH-V3) were tion of the unit. Additionally, more evidence of found stuck in the open position with debris reverse rotation was observed upon inspection of lodged in the seating area – shown in Figures 3E the pump’s internal components. The shaft was & 3F. The debris that was found in one of the bent toward the non-drive end as shown in Figure valves was identified to be SMAW welding elec- 2D with significant deterioration to the casing trodes. On the other valve, twisted tape turbula- wear rings, inter stage rings, impeller rings, im- tors from within the tubes of a BFW pre- peller and bushings at the discharge end of the heater/steam generator were noted between the pump, some of which is shown in Figure 3A. disc and seating area. Figure 3. A – Main HP BFW pump wear rings found damaged; B & C – Wear ring debris lodged in main BFW pump ARC check valve seat; D – Main HP BFW pump strainer found fouled on both sides; E & F Check valves found open AMMONIA TECHNICAL MANUAL 44 2018 Discussion there were three pathways available to the fluid being pumped – the common recirculation line, Analysis of the Sequence of Events the common discharge line, and most im- portantly, because of its reduced output, back to The trip signal generated by the air compressor the main pump.
Details
-
File Typepdf
-
Upload Time-
-
Content LanguagesEnglish
-
Upload UserAnonymous/Not logged-in
-
File Pages10 Page
-
File Size-