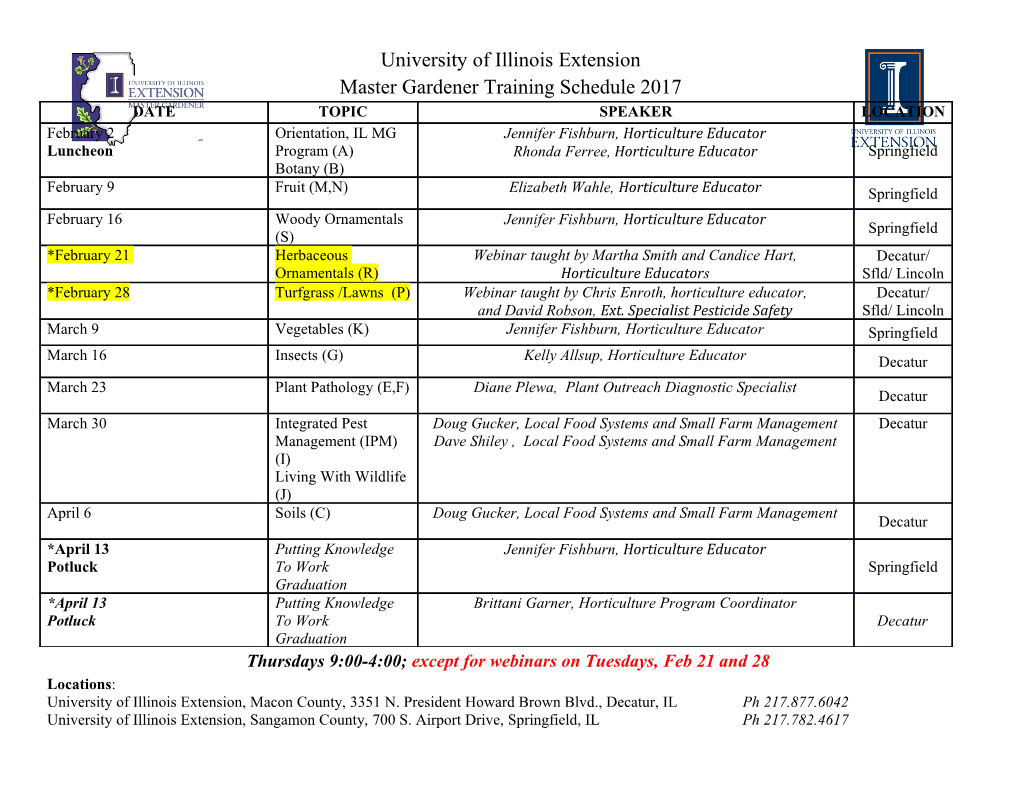
ACC Limited Bargarh Cement Works “National Award for Excellence in Energy Management 2018-19” Milestones of IDCOL Cement Limited Year Description ❖ Foundation stone laid by Industrial Development Corporation Of 1963 Orissa Ltd (IDCOL), Govt. of Orissa on 19th Dec’1963 ❖ Plant started on 10th May 1967 with 2 wet process kiln each of 600 TPD 1967 (0.37 MTPA) & Grinding capacity 0.3 MTPA 1982 – ❖ First phase of expansion with capital of 1.6 Million INR to increase volume. 1985 ❖ Installation of Cement Mill No 3. (1st Phase) ❖ Grinding capacity enhanced to 0.565 MTPA. 1991 – ❖ Second Phase of expansion by commissioning of one new dry process kiln with 1995 capacity 1800 TPD of five stage SP with in line Pre calciner. (2nd ❖ Cement Grinding capacity enhanced to 1 MTPA by installation of 2 HPGRs and Phase) mixing plant. 2 ACC Limited 1 Takeover by ACC in Dec 2003 Year Description ❖ Acquisition of plant by ACC Limited in Dec 2003. Cost of share purchased – 176.41 Cr. (23 Cr. equity shares @ Rs 7.67 per share) Reasons for Disinvestment of the erstwhile IDCOL Cement Limited : - Dec., 2003 ❖ Sick unit, Too much Bureaucratic & Political interference , Excess manpower, high overtime, Poor Industrial culture , Poor Technical capabilities of the employees to run the plant efficiently. ❖ Labor unions were very strong supported by local politicians resulted in poor performance of the plant. ❖ Investment of INR 86 Cr. to increase the kiln capacity from 1800 TPD to 2600 TPD. 2005-2006 ❖ Conversion of Raw mill to 3 fan system, Replacement of Kiln ESP with Bag House & (3rd Phase) Cooler ESP upgradatation by addition of 2 fields Investment of INR 572 Cr. to increase the clinker capacity to 0.9 MTPA and cement production capacity from 1.02 MTPA to 2.144 MTPA by following up gradations:- ❖ Addition of one more stage to PH with new down comer duct and fan. ❖ Installation of Slag VRM (145 TPH). 2007 - ❖ Close circuiting of existing cement mills. 2010 ❖ Installation of new limestone crusher at mines (650 TPH). th (4 Phase) ❖ Installation of Mixing plant. ❖ Cement Silo (10,000 tonnes) ❖ Packing plant. ❖ CPP (2X15 MW) ❖ Wagon tippler. ❖ Stacker reclaimer system for coal and slag handling. 3 ACC Limited Bargarh - Location Western Odisha – Nearest Airport Jharsuguda 100 KM, Raipur 220 Km Approved Capacity after Plant Expansion : Clinkering : 0.9 MTPA, Cement – 2.14 MTPA, CPP - 30 MW 4 ACC Limited 2 Mines Overview Dungri Limestone Quarry (DLQ) is located at 43 KM from the plant. Lime stone is being transported through Meter Gauge railway line by wagons. Limestone reserve available at DLQ as on 01.04.2014 is 11.89 Mio Tons. Mines Lease Area 448.392 ha Mines Reserve 11.89 MT Life of Mine 10 Years Stripping Ratio 4 5 ACC Limited Plant - Equipment Details Coal & Slag Quarry Transportation Raw Mill Raw meal Silo Kiln Stock Piles • Six Stage • Dungri Mines located • 2 Nos CF Silo • Coal: 20000 • Transportation of • Vertical Roller Mill Preheater with 53 KM from Plant MT Limestone by Capacity 230 TPH • Capacity : Inline Calciner • Limestone reserves Wagons through ( Make: Loesche, 5000 MT each • Kiln BDP 2860 TPD • Slag: 30000 12.4 Million Ton meter gauge 1995) • Old Folax cooler MT • Expected life 10-12 yrs • Feed through open (Fuller KCP – 1995) • Impact crusher 650 railway line. circular stock pile • Clinker storage silo TPH (Make L&T, 2009) • LOCO – 1200 HP (2NOs), 635 HP (3 (Cap: 30000 MT) (Cap : 60000 MT) Nos) CPP Packing Plant Cement Silos Slag VRM Cement mills Coal Mill • 5 Packers (3 in old • 5 Silos with manual • CM#3 (90 TPH), • Vertical Roller • Capacity – 2 X 15 extraction system • Vertical Roller Packing plant and 2 in mill for Slag with HPGR2 as pre- MW • Silo 1 to 4 - 3000 MT Mill Capacity New Packing Plant) grinding grinder • CFBC Boilers – 2 (Year – 1967) (Loesche 1995) • Capacity : (Pfeiffer – 2009) (Fuller KCP 1995) Nos • Silo No 5 – 2500 MT • 25 TPH (Normal Packers 1 & 2 – 150 • Capacity 145 TPH • CM# 4 (55 TPH) with • Make : Cethar Vessels (Year – 1987) coal) • Mixing plant Cap TPH, Packer 3 – 100 • Silo 6 – 10000 MT HPGR1 as pregrinder• 12.5 TPH Year : 2009 300 TPH for PSC TPH, Packers 4 &5 – (2009) • (Petcoke) 240 TPH • Total – 24500 MT and F2R 6 ACC Limited 3 Energy Conservation Team Structure Team Leader : Director Plant Energy Champion : Head Operation Team Members Circle area Champions Narendra Bhardwaj 1 Raw Material extraction S Kundu 2 Raw Material crushing S Sen Parmanand Rai 3 Raw Mills Sunil Samal 4 Kilns JN Majhi D Bhadra 5 Coal Mills Tamal Core Energy Team Circles 6 Cement Grinding N B Jagati Pankaj Vidyarthi 7 Packaging Tapan Mohanty 8 CPP Boiler Balraju S Mishra 9 CPP Turbine Aklesh 10 Auxiliaries Lokesh Verma M Jadhav 7 ACC Limited Plant achievement highlights .... Sl.No Major Energy❑ savingsSignificant improvementprojects in Reduction of 21Savings unit/t of cementUnit (19.1%) in Increase Cement Mill 3 Output from 90 to 134 TPH by process optimisation adding 1 Electrical Energy from 2016-17. 4.5 (kWh/t cem) separate fly ash feeding system, roller replacement Reduction of Slag VRM❑ MainFirst Drive Plant Power within LH residue group optimisation producing of Product 100% mix Composite Green Cement and 2 (Fly ash & Slag) with the addition of Separate feeding system and optimise Hydraulic 5.5 (kWh/t cem) system and Residue optimisationSuccessfully established Green cement in the market with better quality. Installation of VFDs & GRR installation at different equipment 3 ❑ Reduction of Clinker Factor by 4.27 % (From 48.6%3.5 to 44.4%)(kWh/t cem) Reduction of Clinker factor by 4.5% by increase of fly ash and activated 4 2.5 (kWh/t cem) additives with separate❑ flyWe ash saved feeding Natural system Resources By Utilization of Portable screen through Optimization of Bag filter Mechanicalfan, Air Compressor separation , Pumps and operation we have recovered 76000 High Grade 5 limestone, for waste soil Mix dump. 1.8 (kWh/t cem) Reduction of utility Power by optimization of Colony & Lighting TR Voltage, 6 2.2 (kWh/t cem) drinking water pump ❑operACC, office Bargarh & Street lightCement etc Works Won CII Green CO Gold Award in 2019 Reduction in idle running of the equipments by providing the interlocks in 7 1 (kWh/t cem) DCS. ❑ ACC Bargarh is Certified for ISO 50001 -Energy Management System, ISO Installation of New Energy14001 Efficient- Environment Burner in Kiln Management System and ISO 9001- Quality 8 Management System 60 MJ/t Clinker Improve heat Transfer by implement CFD implementation at Cyclone 1 A ,1 B, 9 15 MJ/t Clinker and 3 ❑ ACC Bargarh Cement Works won CII Energy Award as Energy Efficient Unit Optimization of Grate speedin 2015 with under grate pressure in PID loop and 10 Optimize cooler air flow distribution 10 MJ/t Clinker 8 ACC Limited 4 Summary Of Energy Savings Project in Last 3 Years Major Energy Total Total Savings Year Saving Project Investment (Million INR) (Nos) (Million INR) 2016-17 13 44 39 2017-18 12 18.9 7.5 2018-19 20 107.5 40 9 ACC Limited Summary : ENCON Efforts No. Of Projects 25,000 T CO2 No Investment Reduction Energy Conservation Projects ( Summary for Medium Investment last 3 years) 34% ‰ No investment 66% ▪ No of project implemented : 15 ▪ Saving Kwh/T of Cement : 10 44 Energy Savings▪ Saving in INR, Crore : 6.48 ‰ Medium Investment Savings inprojects CR implemented ▪ No of project implemented : 29 No Investment ▪ Saving Kwh/T of Cement : 11.6 ▪ Saving in INR, Crore : 8.0 42% Medium Investment 58% 10 ACC Limited 5 Where we are………. overall KWh/Ton of Cement Impact of 15 CR 21 kWh/t 11 ACC Limited Energy reduction trend Reduction in Clinker Factor Saved 230.0 %Clinker factor Grinding power Kwh/T Cem Clinkering power, Kwh/T Clk 40,000 T CO2 emission/yr 210.0 190.0 48.67 170.0 46.87 44.4 150.0 130.0 61.4 51.8 110.0 47.8 90.0 70.0 94.9 92.4 86.0 50.0 2016-17 2017-18 2018-19 Year 12 ACC Limited 6 Achievement in PAT Target 900 881 Reduction of 850 130 kCal/kg of Cement 800 /kg of 752 751 kCal Cement 750 700 650 Baseline PAT Cycle-1 PAT Cycle-2 Reduction of 14.8 % from baseline of PAT Cycle 13 ACC Limited STEC – kCal/Kg of Clinker Concerned Area ,We are in process to Major up gradation / replacement of Cooler in October 2019 14 ACC Limited 7 ACTION PLAN FOR ENCON ❑ Major Up gradation and partial Replacement of Cooler in major shutdown to Improve Clinker productivity , Reliability, Electrical and Thermal energy. Investment : INR 150 Million ❑ ReplacementTarget of In efficient Energy Fan with Savings High efficiency fan for PH fan. Raw Mill Fan, Cement Mill Fan 100 MJ/t clinker ❑ Increase AFR usage in Kiln with the tie up with Municipality and other waste 8agencies kWh/t clinker 4.5 kWh/t cem ❑ Installation of LV VFD in Ground Clinker Silo Bagfilter fan, Gr Slag Silo Bag filter Fan, CF Silo Bagfilter fan and applications 15 ACC Limited Innovative Project : 1 Beneficiation of Clay Mixed Limestone Mines Life Increasedwith Portable Power screen ▪ Limited Reserve of Lime stone Issues/ ▪ Clay Mixed Limestone was not usable due to the following reasons ▪ Difficulties to maintain Crushed Limestone quality (LSF) Challenges ▪ Jamming in VRMby & Klin, 15 Cyclone Months ▪ Also its affect on the burnability during clinkerization ▪ Impact overall Kiln Production and Power consumption Ideas ▪ To utiliseNatural very good quality Resources high grade lime stone recovered , we need to Segregate of Clay /Initiatives ▪ We initiated to Install Mobile Screen in line with all permits and requirement and Taken 1 Lakhfinally installed MT Mobile (High Screen toGrade recover limestone LS from ) anotherclay mixed stone 6 lakhs MT is under process Jamming & Clogging issues resolved Result • Mineral Conservation by utilization Clay mixed limestone • Increase Mine Life • Less Stripping Ratio • Reduction of RME Cash Cost, Total savings RS 12 million.
Details
-
File Typepdf
-
Upload Time-
-
Content LanguagesEnglish
-
Upload UserAnonymous/Not logged-in
-
File Pages21 Page
-
File Size-