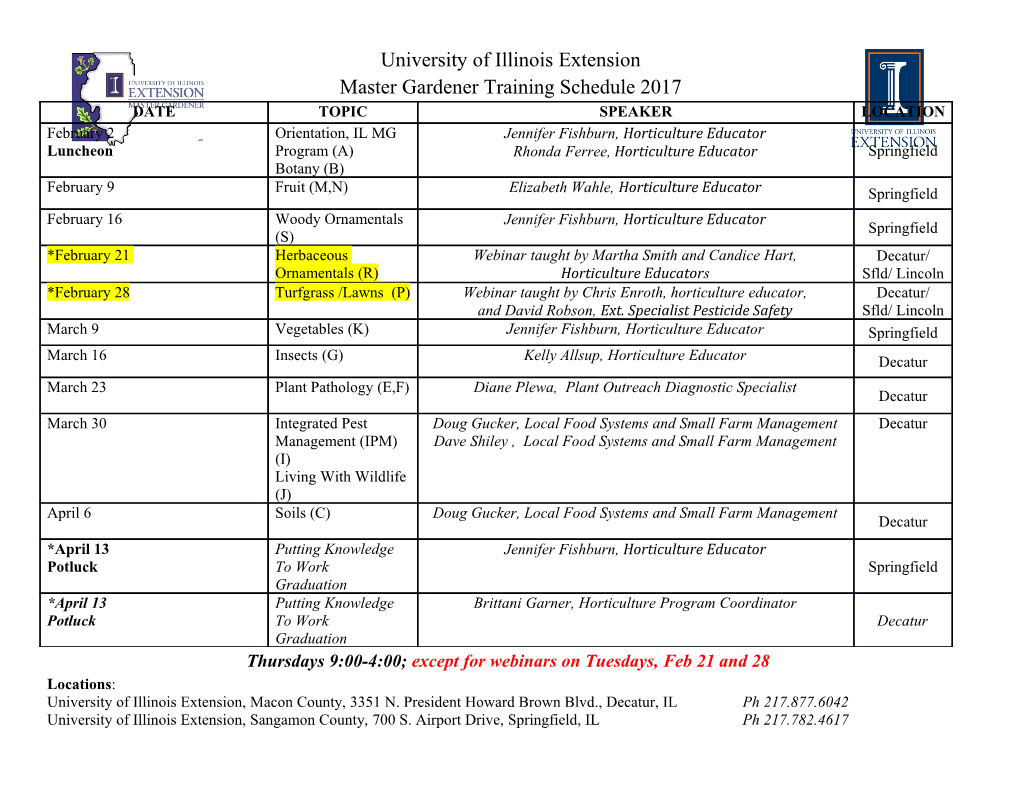
ICES-2020-209 Thermal control of a light-weight rover system in the permanently shadowed regions of the lunar south pole D. Ivanov1 and D. Fernandes2 Ispace Europe, 5 Rue de l’Industrie, Luxembourg, L-1811 The exploration of the Earth’s Moon has become a topic of great interest in recent years to both private and governmental entities. ispace is aiming to be the enabler for private industry to access new business opportunities on the Moon by capitalizing on lunar resources and expanding our presence in space. The Polar Ice Explorer (PIE) is an in-situ resource utilization (ISRU) exploration mission that aims to find and characterise potential water ice deposits in the lunar polar regions. In the scope of this project, the rover thermal control system development will be discussed. PIE leverages on ispace developed and flight qualified Team HAKUTO’s SORATO rover. The paper explores findings from three key areas: operations in the permanently shadowed regions (PSR) of lunar poles, thermal control design of the rover system and modelling of lunar environment. Thermal modelling of the lunar polar region was conducted with a particular attention towards identification of surface properties, lunar regolith characteristics and modelling of environmental fluxes. Operational mission constraints, such as cooling rates and heater power requirements, were investigated. Thermal design philosophy aimed to maximise passive control means through decoupling of the rover from the ground, reduction of heat losses and conductive path management. Mechanical issues induced by larger temperature swings were investigated. Active control means were considered for elements with tighter operational ranges, such as batteries, motors and externally mounted elements. The rover thermal design challenges and preliminary findings enabling operations in the PSR were outlined. Nomenclature α = Solar absorptivity β = Infrared emissivity a = surface albedo MCp = System heat capacitance Cp = Specific Heat Capacity GR = radiative coupling GL = linear conductive coupling k = thermal conductivity dt = time step dT/dx = temperature gradient Fij = view factor from surface i to surface j Tsink = Sink temperature h = height g = gravitational acceleration SSM = Second Surface Mirror OSR = optical solar reflector 1 Thermal Engineer, Integrated Mechanical Systems Department, [email protected]. 2 Mechanical Engineer, Integrated Mechanical Systems Department, [email protected]. Copyright © 2020 ispace inc. I. Introduction The lunar environment, especially polar regions, is characterized by large surface temperature swings throughout each synodic day1 equal to 29.5 Earth days or 708 h. Typical non-illuminated portion of the lunar cycle lasts 354 h. Long night period creates a significant design challenge for surface operations. Surface exploration assets cannot rely solely on solar power to sustain themselves throughout the full lunar night. In addition, The South Pole contains rougher terrain and topographical features with significant heights which cast large shadows2 due to low elevation angle of the sun. Permanently shadowed regions (PSR) are particularly interesting areas for commercial exploration of the lunar surface as they contain trapped volatiles which can be extracted and converted into fuel to enable sustainable mission operations3. However, PSR temperatures as low as 50 to 70 K make it a very challenging thermal task. Thermal design of the polar rover presents several challenges4. Large swings in temperature cause materials to expand and contract thus creating stresses on mechanical assemblies and interfaces. Minimization of thermal strains requires careful selection of materials with low coefficient of thermal expansion. Operations in the PSR cause embrittlement issues due to reduction of ductility. On the other part of the spectrum, the lunar day may cause severe outgassing issues, which promote rapid degradation of lubricants and enhances abrasive effects of the lunar dust at seals. The lunar dust readily adheres to equipment and outer coatings 5. This not only causes mechanical failures of bearings, wheels and motors but also degraded performance of radiative coatings and reduced power generation of solar cells. These challenges coupled with a large power requirement to survive the lunar night significantly constrained thermal design of the polar rover. Several lunar landings and operations that lasted longer than one lunar day include Chang’e 4 and Lunokhod missions. Both utilised Radioistope thermoelectric generators (RTG) or Radioisotope heater units (RHU) to survive the lunar night6. On the opposite side, ESA’s Heracles EL3 mission and Blue Origin’s Lander are aiming to bring enough hydrogen and oxygen with them to allow rover or other payloads to take advantage of the regenerative fuel cell system7 and extend mission lifetime to more than 3 lunar cycles by supplying both heat and electricity throughout the non-illuminated portion of the lunar month. Both solutions have their advantages and disadvantages, but fuel cell based systems enable more commercial entities to be involved in the future lunar economy. Overall thermal design trend is to insulate and isolate critical components with tight operational ranges, as well as, add active thermal control solutions like heaters, pumped fluid loops and heat pipes to manage internal environment. Solar panels and RTGs were the two most preferred power sources for shorter and longer missions respectively. The following paper will dive deeper into the thermal design of the rover exploring non- RTG and non-RHU solutions to allow for a feasible commercial alternative. Figure 1: Rover overview Rover dimensions are 529 x 602 x 372 mm. Total mass of the rover is approximately 10.7 kg excluding the payload. All instruments were accommodated on the internal side of the platform with exception for stereo cameras and antennas. Key objectives of the mission are mapping of the lunar surface and prospecting the area for water ice deposits. Nominal rover mission is expected to last for 1 lunar day or 12 earth days assuming landing two days after sunrise, with no night survival capabilities. However, subsequent design upgrade would be done to improve mission duration and attempt night survival. Overall rover platform is designed to be compact, low mass and energy conservatives. Further chapters of this paper will describe the modelling of lunar environment, explore thermal hardware trade-offs and outline operational requirements for shadows. 2 International Conference on Environmental Systems II. Modelling of lunar thermal environment A. Mission thermal environment Thermal environment (Infra-red, albedo and solar flux) depends on the mission phase. The mission was therefore divided into several segments: Pre-launch, Leop, Earth Orbit, Transit, Landing and lunar surface operations. The lander ensures sustainable thermal environment compatibility of the rover up-until lunar surface operations phase. The exploration rover will rely on its own thermal control system while operating on the lunar surface. Therefore, key thermal drivers would be moon IR, solar flux at landing latitude and dissipation modes. The rover thermal design utilised a Solar Power Flux with an average value of 1367 W/m2 ± 3.5 %. In addition, ± 1% variation during 11 year solar cycle is also considered, with minimum value of 1321.6 W/m2 (Summer Solstice) and a maximum value of 1412.9 W/m2 (Winter Solstice)8. This environment is applicable at all times except when the Sun is blocked (i.e. during eclipse). Sink temperature to space was taken as 2.53K. However, this mainly applies to the top surface with radiators. Surfaces with a view factor to lunar ground used an adjusted sink temperature. Several important orbital parameters were included in order to accurately model the lunar environment. The lunar equatorial plane is inclined by 1.53o to the sun’s ecliptic plane and by 6.68 o to the orbital plane around the earth. The ecliptic plane is inclined by 5.15 o to the lunar orbital plane. In comparison, the earth is inclined by by 23.28 o to sun’s ecliptic plane. These parameters determine general motion and view conditions between the moon, the earth and the sun in the solar system9. Distance to sun was chosen to be 1 A.U, which is approximately true due to close vicinity to Earth. Figure 2: Mission thermal environment definition B. Topographical Elevation Topographical map of the moon, taken from the Kaguya and LRO data, shows a typical distribution of highlands, craters and mares on the surface. The sun elevation angle does not exceed 10 degrees at poles and would therefore cast large shadows when illuminating any boulder, crater rim or mountains. Identification of these key topographical features was critical in defining the mission trajectory and designing the thermal control system of the rover9. Further assessment of these features is shown in the next chapter. 3 International Conference on Environmental Systems Figure 3: Lunar topographical elevation a) global 2D map, b) global 3D map C. Solar Elevation Angle Solar elevation angle was investigated for a proposed landing site in the Amundsen Region. One full revolution with respect to stars (sidereal month) was taken as 27.32 Earth Days. The time between two new Moons (synodic month or lunation) was taken as 29.53 days. Longest solar day in 2023 was estimated to be 12 days, 1 hour, 10 minutes starting at 2023-01-25 00:12:27 (± 45 minutes). Solid red lines represent solar elevation angles
Details
-
File Typepdf
-
Upload Time-
-
Content LanguagesEnglish
-
Upload UserAnonymous/Not logged-in
-
File Pages12 Page
-
File Size-