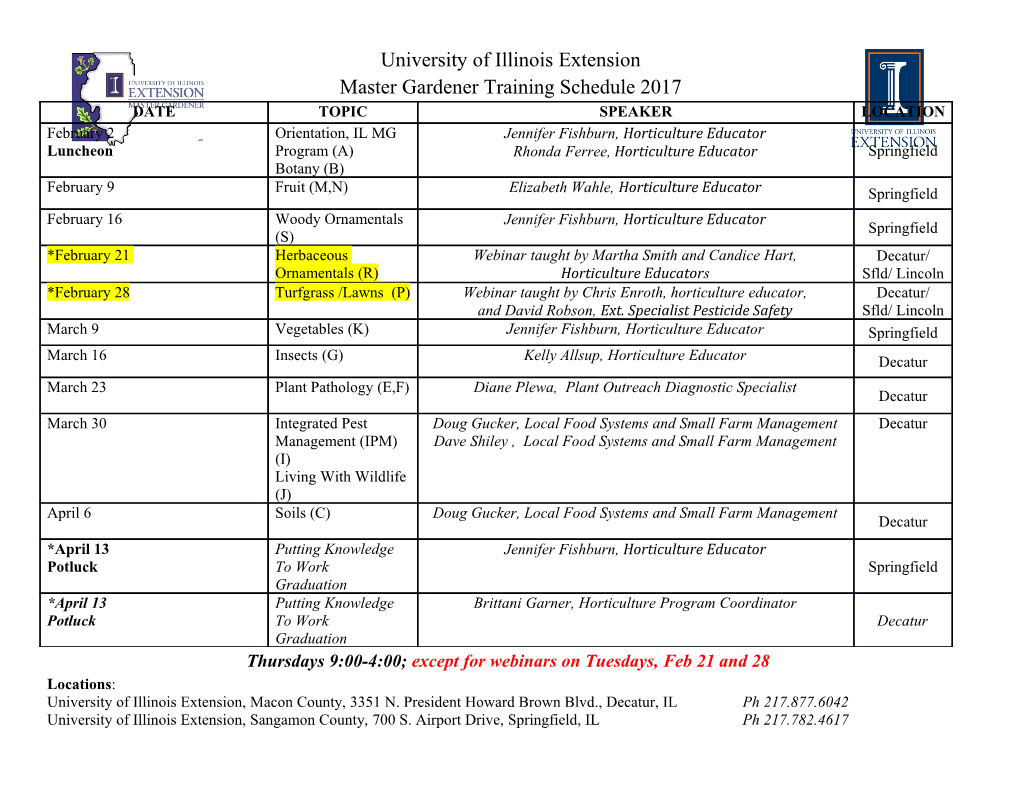
IADC/SPE 119570 Step-Change Improvements with Wired-Pipe Telemetry Scott Allen, SPE, and Chris McCartney, SPE, Occidental Petroleum; Maximo Hernandez, SPE, and Michael Reeves, SPE, NOV IntelliServ; Azaad Baksh and Danial MacFarlane, Baker Hughes Downloaded from http://onepetro.org/spedc/proceedings-pdf/09dc/all-09dc/spe-119570-ms/1784944/spe-119570-ms.pdf by guest on 25 September 2021 Copyright 2009, SPE/IADC Drilling Conference and Exhibition This paper was prepared for presentation at the SPE/IADC Drilling Conference and Exhibition held in Amsterdam, The Netherlands, 17–19 March 2009. This paper was selected for presentation by an SPE/IADC program committee following review of information contained in an abstract submitted by the author(s). Contents of the paper have not been reviewed by the Society of Petroleum Engineers or the International Association of Drilling Contractors and are subject to correction by the author(s). The material does not necessarily reflect any position of the Society of Petroleum Engineers or the International Association of Drilling Contractors, its officers, or members. Electronic reproduction, distribution, or storage of any part of this paper without the written consent of the Society of Petroleum Engineers or the International Association of Drilling Contractors is prohibited. Permission to reproduce in print is restricted to an abstract of not more than 300 words; illustrations may not be copied. The abstract must contain conspicuous acknowledgment of SPE/IADC copyright. Abstract This paper describes the rationale, justification and benefits associated with the deployment of wired-pipe telemetry drillstrings at Occidental of Elk Hills, Inc. (OEHI) in Kern County, California. Recent technological advances in Measurement While Drilling (MWD) systems, Logging While Drilling (LWD) systems, and wired-pipe telemetry systems have overcome historical data bandwidth issues enabling real-time acquisition of critical data streams. These data sets include: continuous annular pressure for equivalent circulating density (ECD) management; vibration diagnostics for drilling optimization; instantaneous downlink commands to Rotary Steerable Systems (RSS) that aide in eliminating secondary non-productive time (NPT) and enhancing directional control; and memory quality formation evaluation measurements to improve reservoir navigation and wellbore placement. With this new wealth of data, onsite drilling personnel, geoscientists, and office engineering staff are able to make real-time decisions that serve to enhance wellbore quality and reduce overall costs. Utilizing wired-pipe to its full potential has helped to deliver an average drilling time savings of 10%. Introduction The benefits of drilling dynamics and formation evaluation from MWD and LWD tools are well known. However, these systems are impacted by bandwidth limitations which restrict the amount of data that can be transmitted to surface in real time. Recent advances in technology have addressed this issue. At the OEHI asset, Oxy and the service providers worked together to evaluate the application and benefits of deploying wired-pipe transmitted data in a land based environment. The technology was tested in combination with multiple downhole LWD and RSS tools. The system was tested in both a 5-in. tubular/mud-based and a 4-in. tubular/foam-based environment. Benefits in the Use of Wired-Pipe Telemetry One of the major challenges in a fast rate of penetration (ROP) drilling environment is transmitting all the required data to surface in a timely manner. When mud-pulse telemetry or electromagnetic data transmission is used, a large amount of this data is stored in memory and downloaded after the tool is tripped out of the hole. The drawback to this system is the lag time in receiving and processing the downhole measurements on the surface. As downhole acquisition technology continues to advance, these measurements are requiring additional bandwidth. This reduces the data density of mud-pulse telemetry points transmitted to surface while drilling, thus, making real-time interpretations and decisions challenging. In order to make an interpretation from a full data set, the operators must wait for the bottomhole assembly (BHA) to be tripped out of the hole and the memory data to be downloaded. 2 IADC/SPE 119570 In contrast, wired-pipe telemetry systems provide a bandwidth more than 1,000 times greater than conventional mud-pulse or electromagnetic telemetry systems. Data rates typically achieved with mud-pulse telemetry systems range from 3 to 40 bits per second (bps). In addition, these systems are affected by noise introduced by mud pumps, signal loss due to depth, fluid properties, and/or fluid flow rate since flow is required for transmission. Electromagnetic telemetry data rates range from 3 to 20 bps and these tools are limited in the vertical drilling distance since the signal attenuates heavily in certain formations. Because wired-pipe has a bandwidth of ~57,600 bps, the MWD/LWD personnel on location are able to configure downhole tools to transmit all acquired data through the network at the fastest possible update rates. Transfer of information to the surface can be reliably achieved at a fixed high-speed real-time transmission without being affected by depth, formation resistivity, fluid properties or flow rates. Hence, the drilling progress is optimized regardless of logging and steering requirements. Downloaded from http://onepetro.org/spedc/proceedings-pdf/09dc/all-09dc/spe-119570-ms/1784944/spe-119570-ms.pdf by guest on 25 September 2021 Full Telemetry Redundancy Within the wired-pipe telemetry configuration, the mud-pulse telemetry system serves as a backup should the wired-pipe system malfunction or fail. This redundancy ensures minimum data requirements are continually met and avoids NPT for equipment troubleshooting or repair. The wired-pipe network was fully operational for 87% of the time while it was being used at OEHI. The majority of the downtime experienced was due to learning curve related elements regarding pipe handling and installation resulting in damage to some of the components during the startup of the project. When the proper handling methods were used, the reliability of the system noticeably increased as shown in Fig. 1. Time distribution per well 250 5" String 4" String 200 150 Telemetry not required Actual Telemetry Hrs Telemetry Down Hrs NPT 100 Hours (Total (Total well hours) Hours 50 0 1234567891011121314151617 Well number Fig. 1—Telemetry use and reliability. Minimum NPT even when wired-pipe telemetry is unavailable. High-Speed Bi-Directional Communication The wired-pipe telemetry network enables concurrent high-speed transmission of data between the downhole tools and surface equipment. Thus, the control of the BHA while running RSS or other advanced services that require surface control are enhanced (i.e; formation pressure testing and seismic while drilling). Since there are no restrictions to when commands are sent to the downhole tools, the fully bi-directional nature of wired-pipe telemetry reduces NPT while improving control of all tools. This is in contrast to the downlink transmission process using mud-pulse telemetry systems that require several minutes to send commands to downhole tools. IADC/SPE 119570 3 The initial two (2) wells drilled with wired-pipe telemetry at OEHI realized a drilling time savings of 4 and 6.5 hours respectively (Fig. 2). These wells were drilled in 43.4 hours and 41.5 hours. A 10% time savings and reduced drilling costs significantly improved the project economics. Time No. of Downlink Time and Saved Well Downlinks Confirmation (hr:mm) (hr:mm) 25 bps Mud- Downloaded from http://onepetro.org/spedc/proceedings-pdf/09dc/all-09dc/spe-119570-ms/1784944/spe-119570-ms.pdf by guest on 25 September 2021 Pulse A 58 04:00 0 Telemetry B 71 04:15 0 C 54 03:45 0 Wired- 1 50 N/A 04:02 Pipe Telemetry 2 72 N/A 06:24 3 62 N/A 04:00 Fig. 2—Comparison of downlinking efficiency during the project (all the above wells were drilled in the same field). Wired-Pipe Telemetry Components & Handling The drillstring used for wired-pipe telemetry is similar to a conventional drillstring in functionality, handling, and specifications. The drillpipe is modified to accommodate an inductive coil in the secondary shoulders of the pin and box which allow for data transmission from one joint of drillpipe to the next. The coils at the end of each joint of pipe are connected via a high-strength, high-speed data transmission conductor cable embedded inside the tool joint that exits to the joint internal diameter at the connection upset. The conductor cable is under tension inside the pipe. Electrical continuity from the drillpipe to the BHA is achieved by using an interface sub; therefore, the system network allows bi-directional transmission to and from the downhole tools. Data boosters are embedded in pipe tool joints at ~1500 ft intervals (10-15 per well) to increase signal-to-noise ratio and ensure no data is lost. Also, the boosters are fitted with temperature and pressure sensors allowing for the ability to acquire measurements along the drillstring. On the surface, a data swivel mounted to the topdrive enables the extraction of data flow inside the drillpipe to the surface computers while the pipe is rotating. This system allows for full bi- directional communication at ~57,000 bps while drilling (Fig. 3). Tubular handling and care was of utmost importance since damage to connections could potentially harm the networking components. Proper training of rig personnel on double-shouldered connections was critical to the success of the project. Because tubular dimensions and specifications were the same as regular non-wired, double-shouldered connections, no additional safety hazards were identified with the use of the equipment involved. 4 IADC/SPE 119570 Top Drive Swivel Extracts the Signal on the Rig Telemetry Pipe Conveys the Telemetry Signal Downloaded from http://onepetro.org/spedc/proceedings-pdf/09dc/all-09dc/spe-119570-ms/1784944/spe-119570-ms.pdf by guest on 25 September 2021 DataLink Boosts the Signal, Wellbore Measurements Interface Sub Connects to MWD Tools Fig.
Details
-
File Typepdf
-
Upload Time-
-
Content LanguagesEnglish
-
Upload UserAnonymous/Not logged-in
-
File Pages14 Page
-
File Size-