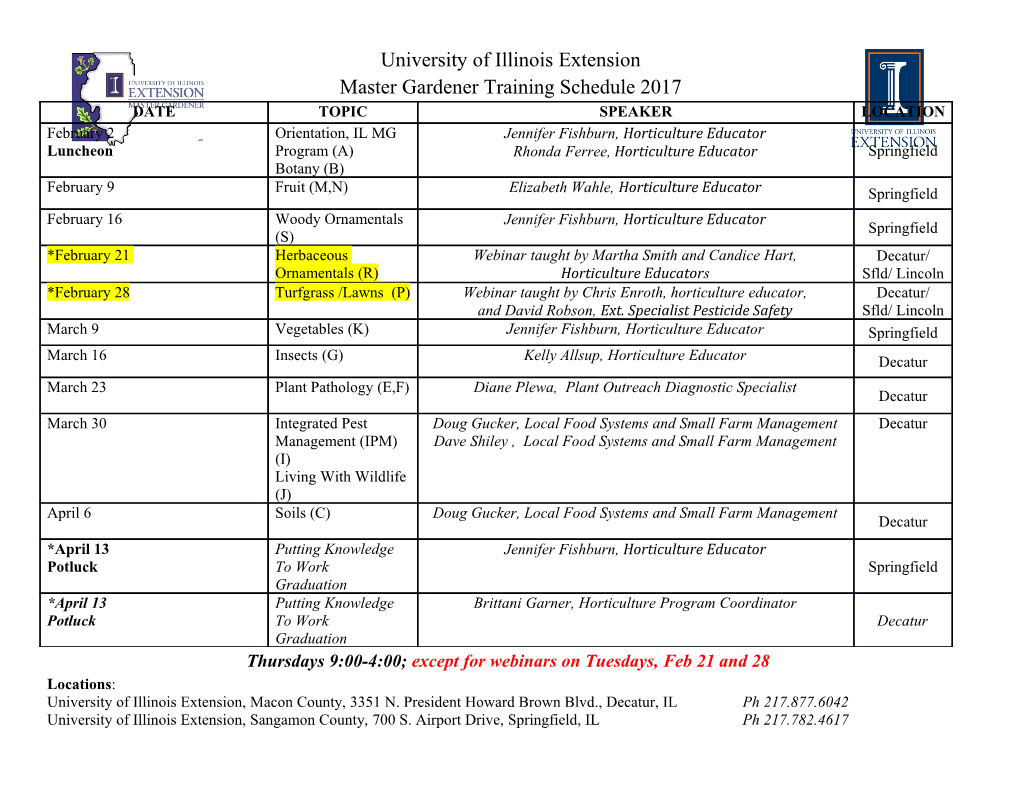
FALL 2004 VOL.46 NO.1 Sunil Chopra and ManMohan S. Sodhi Managing Risk To Avoid Supply-Chain Breakdown Please note that gray areas reflect artwork that has been intentionally removed. The substantive content of the article appears as originally published. REPRINT NUMBER 46109 Managing Risk To Avoid Supply-Chain Breakdown On March 17, 2000, lightning hit a power line in Albu- querque, New Mexico. The strike caused a massive surge in the surrounding electrical grid, which in turn started a fire at a local plant owned by Royal Philips Electronics, N.V., damaging millions of microchips. Scandinavian mobile-phone manufac- turer Nokia Corp., a major customer of the plant, almost immediately began switching its chip orders to other Philips plants, as well as to other Japanese and American suppliers. Thanks to its multiple-supplier strategy and responsiveness, Nokia’s production suffered little during the crisis. In contrast, Telefon AB L.M. Ericsson, another mobile- phone customer of the Philips plant, employed a single- sourcing policy. As a result, when the Philips plant shut down after the fire, Ericsson had no other source of microchips, which disrupted production for months. Ultimately, Ericsson lost $400 million in sales.1 (Ericsson has since implemented new processes and tools for preventing such scenarios.2) These two dramatically different outcomes from one event demonstrate the importance of proactively managing supply- chain risk. Supply-chain problems result from natural disasters, labor disputes, supplier bankruptcy, acts of war and terrorism, and other causes. They can seriously disrupt or delay material, information and cash flows, any of which can damage sales, increase costs — or both. Broadly categorized, potential supply- chain risks include delays, disruptions, forecast inaccuracies, systems breakdowns, intellec- By understanding the tual property breaches, procurement failures, inventory problems and capacity issues. Each variety and interconnect- category has its own drivers (see “Supply-Chain Risks and Their Drivers,” p. 54) and miti- gation strategies (see “Assessing the Impact of Various Mitigation Strategies,” p. 55). edness of supply-chain How a company fares against such threats depends on the type of disruption and the risks, managers can tailor organization’s level of preparedness. To prevent the kind of heavy sales losses suffered by balanced, effective risk- Ericsson after the Philips plant fire, managers must perform a delicate balancing act to keep inventory, capacity and other elements at appropriate levels across the entire sup- reduction strategies for ply chain in a dynamic, fast-changing environment. Dell, Toyota, Motorola and other their companies. leading manufacturers excel at identifying risks to their supply chains, and at creating powerful mitigation strategies that neutralize potentially negative effects. With a clear Sunil Chopra and Sunil Chopra is IBM Distinguished Professor of Operations Management and Information Sys- ManMohan S. Sodhi tems at the Kellogg School of Management. Contact him at [email protected]. ManMohan S. Sodhi is associate professor of operations management at Cass Business School in London. Contact him at [email protected]. FALL 2004 MIT SLOAN MANAGEMENT REVIEW 53 chain. While bare-bones inventory Supply-Chain Risks and Their Drivers levels decrease the impact of over- forecasting demand, they simultane- Before companies can devise effective means of reducing supply-chain risks, managers ously increase the impact of a supply must first understand the universe of risk categories as well as the events and conditions chain disruption. Similarly, actions that drive them. Then, armed with clear, specific knowledge about these crucial risks, taken by any company in the supply- companies can proceed to select and tailor mitigation strategies likely to be most effec- chain can increase risk for any other tive. (See “Assessing the Impact of Various Mitigation Strategies.”) participating company. Supply-chain risks can become Category of Risk Drivers of Risk full-fledged supply-chain problems, Disruptions I Natural disaster causing unanticipated changes in flow I Labor dispute due to disruptions or delays. Disrup- I Supplier bankruptcy tions can be frequent or infrequent; I War and terrorism I Dependency on a single source of supply as well as the short- or long-term; and cause prob- capacity and responsiveness of alternative suppliers lems for the affected organization(s), Delays I High capacity utilization at supply source ranging from minor to serious. A sim- I Inflexibility of supply source ple delay along the chain may create a I Poor quality or yield at supply source temporary risk, whereas a sole sup- I Excessive handling due to border crossings or to change in transportation modes plier holding up a manufacturer to force a price increase represents a Systems I Information infrastructure breakdown long-term risk. A machine breakdown I System integration or extensive systems networking I E-commerce may have a relatively minor impact on a manufacturing company with Forecast I Inaccurate forecasts due to long lead times, seasonality, product variety, short life cycles, small customer base redundant capacity, whereas a war I “Bullwhip effect” or information distortion due to sales that disrupts shipping lanes can have a promotions, incentives, lack of supply-chain visibility and major impact on a shipping company. exaggeration of demand in times of product shortage Most companies develop plans to Intellectual Property I Vertical integration of supply chain protect against recurrent, low-impact I Global outsourcing and markets risks in their supply chains. Many, Procurement I Exchange rate risk however, all but ignore high-impact, I Percentage of a key component or raw material procured from a single source low-likelihood risks. For instance, a I Industrywide capacity utilization supplier with quality problems rep- I Long-term versus short-term contracts resents a common, recurrent dis- Receivables I Number of customers ruption. Without much effort, the I Financial strength of customers customer can demand improvement Inventory I Rate of product obsolescence or find a substitute. In contrast, in I Inventory holding cost regions where earthquakes are rare, I Product value preparedness to prevent major disrup- I Demand and supply uncertainty tion may be weak or uneven. Capacity I Cost of capacity Leading companies deal with this I Capacity flexibility range of supply-chain risks by hold- ing reserves. Just as insurance compa- understanding of the types of supply-chain risks, managers in nies hold cash reserves to meet claims, top manufacturers hold many types of industries can tailor effective risk-reduction supply-chain reserves that include excess inventory, excess capac- approaches to their own companies. ity and redundant suppliers. The big challenge for managers here: Mitigate risk by intelligently positioning and sizing supply-chain A Variety of Risks reserves without decreasing profits. So while stockpiling inven- Managing supply-chain risk is difficult because individual risks tory may shield a company against delivery delays by suppliers, are often interconnected. As a result, actions that mitigate one building reserves in an undisciplined fashion also drives up costs risk can end up exacerbating another. Consider a lean supply and hurts the bottom line. The managers’ role here is akin to that 54 MIT SLOAN MANAGEMENT REVIEW FALL 2004 of a stock portfolio manager: Attain the highest achiev- able profits (reward) for varying levels of supply-chain Assessing the Impact of Various Mitigation Strategies risk and do so efficiently. (See “Choosing Supply-Chain Risk/Reward Trade-Offs,” p. 56.) This means the manager Unfortunately, there is no silver-bullet strategy for protecting organi- must seek additional profits for any level of risk protection zational supply chains. Instead, managers need to know which mitiga- and preparedness or increase prevention and preparedness tion strategy works best against a given risk. (Systems risk and intellectual property risks are not included here.) without reducing profits. Success at this task requires a good understanding of supply-chain risks and remedies, both broad and tailored to the manager’s own company. Mitigation strategy DisruptionsDelays Forecast Procurementrisk Receivables riskCapacity risk Inventory risk risk Delays Delays in material flows often occur when a sup- Add capacity plier, through high utilization or another cause of inflexi- bility, cannot respond to changes in demand. Other Add inventory culprits include poor-quality output at supplier plants (or Have redundant suppliers at their suppliers’ plants), high levels of handling or inspec- tions during border crossings and changing transportation Increase responsiveness modes during shipping. If material-flow delays are fre- Increase flexibility quent, however, companies can plan mitigation strategies Aggregate or pool demand based on historical information. Organizations can avoid delays, or at least prepare for Increase capability them, by appropriately and economically placing and sizing Have more customer accounts their capacity and inventory reserves. One simple solution is to maintain excess flexible capacity in existing plants. Toyota Greatly Increases Risk Decreases Risk Motor Corp., for example, accomplishes this on its assembly Increases Risk Greatly Decreases Risk lines by employing team leaders who can work on any sta- tion. Besides
Details
-
File Typepdf
-
Upload Time-
-
Content LanguagesEnglish
-
Upload UserAnonymous/Not logged-in
-
File Pages12 Page
-
File Size-