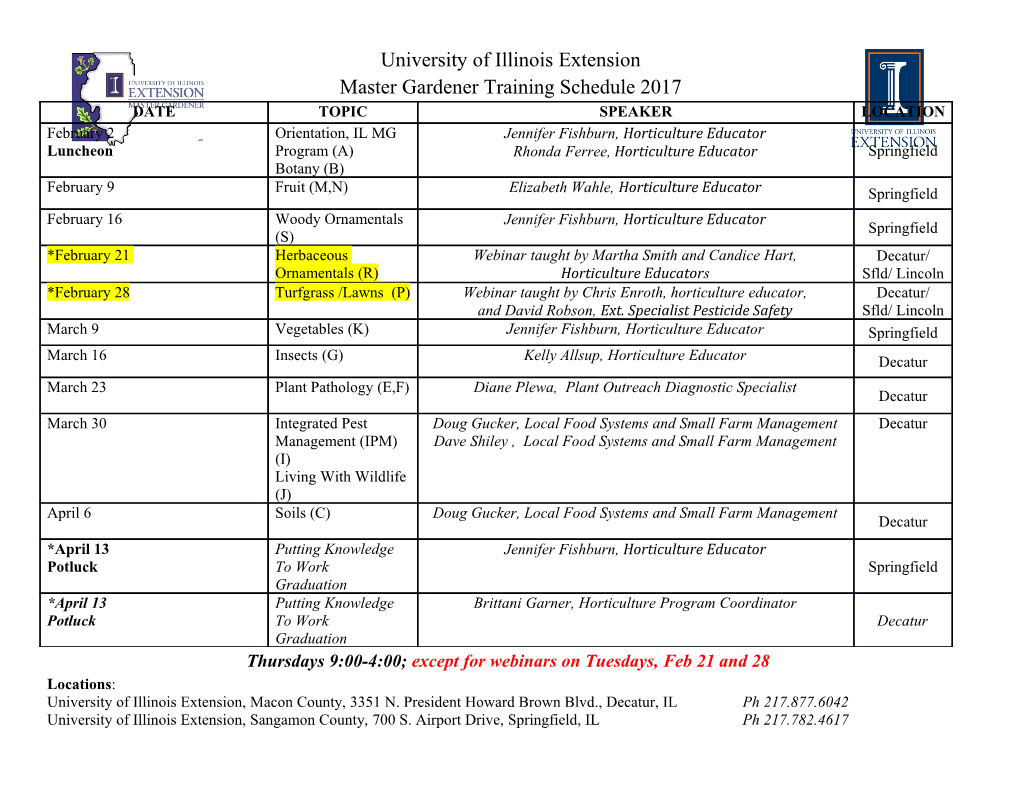
AU0221634 A New Fuel for Research Reactors M. R. FINLAY and M. I. RIPLEY Materials Division Australian Nuclear Science and Technology Organisation Private Mail Bag 1 Menai NSW 2234 SUMMARY The Replacement Research Reactor (RRR) to be constructed at Lucas Heights will use fuel containing low enriched uranium (LEU), <20%wt 235U, whereas its predecessor HBFAR operates with fuel fabricated from high-enriched uranium (HEU). The fuel will be based on uranium silicide (U3S12) with a density of 4.8 gU/cm3. This fuel has been qualified and in use in 20 research reactors worldwide for over 12 years. A brief description is given of the metallurgy, behaviour under irradiation, and fabrication methods, all of which are well- understood. Progress on development of new, higher density LEU fuel based on uranium molybdenum alloys is also described and the implications for the RRR discussed briefly. 1. INTRODUCTION still higher fuel densities may be achievable and mention is made of work to this end. There has been a worldwide move from use of high enriched uranium (HEU) to low enriched uranium 2. RERTR PROGRAM (LEU) fuels for research reactors, where LEU is taken to be <20 wt% ^U (natural uranium contains The change from HEU to LEU fuels for research 0.7 wt% 235U). There have been a number of reactors has been driven by the US Department of initiatives to compensate for this reduction in Energy (DOE) through its Reduced Enrichment for uranium enrichment and negate the associated 10- Research and Test Reactors (RERTR) program. 15% penalty in neutron flux. Fabrication techniques This program was established in 1978 as part of the have been developed to their practical limits to US Federal Government's nuclear non-proliferation maximise the uranium density achievable. In 1988, policy. The RERTR mission is "to develop the US Nuclear Regulatory Commission (1) technologies that could be used to minimise and approved the use of a new high-density LEU fuel eventually eliminate the use of highly-enriched consisting of uranium silicide (U3Si2) dispersed in a uranium in civil applications worldwide". A major matrix of aluminium up to a density of 4.8 gU/cm3. goal of the program (2) is to eliminate the use of Numerous research reactors around the world have HEU in research and test reactors without made successful conversions to this fuel and unacceptable penalties in neutron flux performance ANSTO's Replacement Research Reactor (RRR) is or economic or safety aspects of those reactors. To planned to begin operation using this fuel. facilitate this goal, an international program of LEU fuel development and qualification has been led by There are, however, some research reactors that Argonne National Laboratory (ANL) for over require higher neutron fluxes and, hence, uranium 20 years. This program facilitated the qualification loadings greater than 4.8 gU/cm3. Also, silicide fuel and use of silicide fuels in many research reactors is not easily reprocessable using current worldwide. In 1996, the program focussed on the commercially available technologies. As a result, the development of new, higher density fuels because of focus of fuel development is to develop a readily the realisation that some research reactors could not reprocessable fuel with uranium density of 8- successfully convert to silicide fuel without major 9 gU/cm3. Uranium molybdenum dispersion fuels penalties. Uranium molybdenum alloy fuel (3) was have emerged as the primary candidates and a identified as being capable of providing increased coordinated international research program is under way to evaluate and qualify them. In the longer term 156 neutron performance, and could also be reprocessed absorber. using conventional reprocessing technology. Initially HIFAR used fuel containing 93% enriched A related DOE program, the Foreign Research uranium, although this was subsequently reduced to Reactor Spent Nuclear Fuel Acceptance Program, 60% as a result of the RERTR program. has also indirectly driven development of higher Improvements in fuel plate design and fabrication, density fuels. Under this program the US has agreed and cost issues, have ameliorated this change. to take back spent US-origin research reactor fuel, In conventional HEU fuels the fuel meat is an alloy including silicide fuel, generated up to 2006. After of uranium and aluminium, known as uranium that time many research reactor operators will be in aluminide (UA1 -A1). Pure uranium metal is not used the difficult position of having no alternative but to X because its equilibrium phase, a-uranium (stable up store their spent fuel indefinitely. Previously, an to 660°C), is known to exhibit an unacceptably high alternative disposal route was available whereby rate of growth and swelling under irradiation. HEU aluminide fuels could be reprocessed by a Aluminium is used to stabilise the cubic y-phase commercial reprocessor and returned as a stable under irradiation at these temperatures. Aluminium wasteform. This was originally the case for silicide is an ideal alloying element because of its low fuel also but with the closure of the UK Dounreay neutron capture cross-section, high thermal facility in 1999 the reprocessing options for silicide conductivity, workability and high corrosion fuel are now very limited. UMo fuel will be able to resistance in water. be reprocessed in conventional (nuclear power plant fuel) reprocessing lines in the UK and France and so To fabricate fuel plates the uranium-aluminide is research reactor operators who want to use the pressed into flat plates less than lmm thick. Placing reprocessing alternative will need to complete the plate in an aluminium "picture frame" and conversion to UMo fuel before the 2006 deadline. sandwiching the assembly between two aluminium The need for a readily reprocessed fuel has been sheets provides further corrosion protection. The recognised by both RERTR and research reactor layers are bonded together by hot rolling. fuel manufacturers and has stimulated activity to The requirement to shift from HEU to LEU prove and qualify UMo fuel for use before 2006. (<20 %wt) presented research reactor operators with problems for the continued use of UAL.-A1 fuel. 3. HIGH ENRICHED URANIUM FUEL The main limitation was the low density of uranium in the UA1 -A1 fuel meat, ~1.7gU/cm3, as shown in HIFAR and most research reactors of its generation X Table 1. The uranium density in the fuel meat is have fuel assemblies that consist of fuel plates lower than the phase density because the fuel meat containing high enriched uranium (HEU). HEU fuels contains only 10-50% of the phase by volume, with are attractive to research reactor operators because the balance being aluminium. Early work in the the increased percentage of the fissile isotope ^U RERTR program demonstrated increased uranium facilitates the high neutron fluxes required for density to a practical limit of -2.4 gU/cm3 through research reactor applications. Importantly, with higher uranium loading and the use of powder increasing enrichment a concomitant reduction in metallurgical fabrication routes rather than ^U occurs: ^^U not only contributes very little in traditional casting. At higher loadings fabrication the fission process, but also acts as a neutron Table 1 Density of different uranium alloys. DENSITY OF URANIUM (g/cm3) ALLOY ALLOY TYPE PHASE IN PHASE IN FUEL MEAT U metal a 19.0 19.0 UA1X-A1 Cast UAL, 6.1 1.7 UAL, 6.1 UA1X-AI Dispersion UA13 6.8 2.4 UA12 8.1 U3Si2 12.2 U3Si2-Al Dispersion 4.8 U3Si 15.2 U-5Mo 17.9 UMo-Al Dispersion U-8M0 17.3' 6-9 U-9Mo 17.0 157 problems arise from the mismatch between the fuel The high volume loadings of U3Si2 (40 to 50% by meat and aluminium cladding. volume) in the fuel meat have the potential to cause Hence, in. order to convert successfully to LEU in problems during fabrication. In particular, there are existing research reactors without unacceptable three problems associated with dispersion type fuel penalties in neutron flux, safety or economics it was plates and high volume loadings. They are: necessary to consider higher density uranium alloys • Dogboning, which is the thickening of the fuel which were capable of maintaining a metastable y- meat at the ends of the plate that can lead to phase. localised increases in uranium density and consequently high heat fluxes during irradiation. 4. LOW ENRICHED URANIUM FUEL • Minimum cladding thickness, which becomes a The principal reason for changing from HEU to concern as volume loading of fuel particles LEU fuel has been the non-proliferation issue, ie. increases, because the likelihood of two fuel HEU is more attractive to a potential proliferator as particles contacting each other during rolling it shortens the further technological steps required and becoming embedded in the cladding also to reach nuclear weapons grade material compared increases. Dogboning increases the likelihood of with LEU. The use of LEU incurs a 10-15% penalty such a breach, and hence strict control of in neutron fluxes due to there being an increased maximum fuel particle size is required. 238 number of U atoms which absorb neutrons. • Stray fuel particles, which are found on the Development of LEU fuels has focussed on surface of the compact in increasing numbers, increasing the uranium content (density) to increase as volume loading increases. They can be 235 the number of fissile U atoms per unit volume of dislodged during rolling and transported to the fuel meat. fuel plate surface. Since the fuel particles are sources of heat and fission products it is Uranium Silicide important that they do not come into contact with the coolant. The development of a new dispersion-type fuel containing uranium silicide in aluminium began in As with uranium-aluminide, uranium silicide can the early 1980s under the RERTR program.
Details
-
File Typepdf
-
Upload Time-
-
Content LanguagesEnglish
-
Upload UserAnonymous/Not logged-in
-
File Pages6 Page
-
File Size-