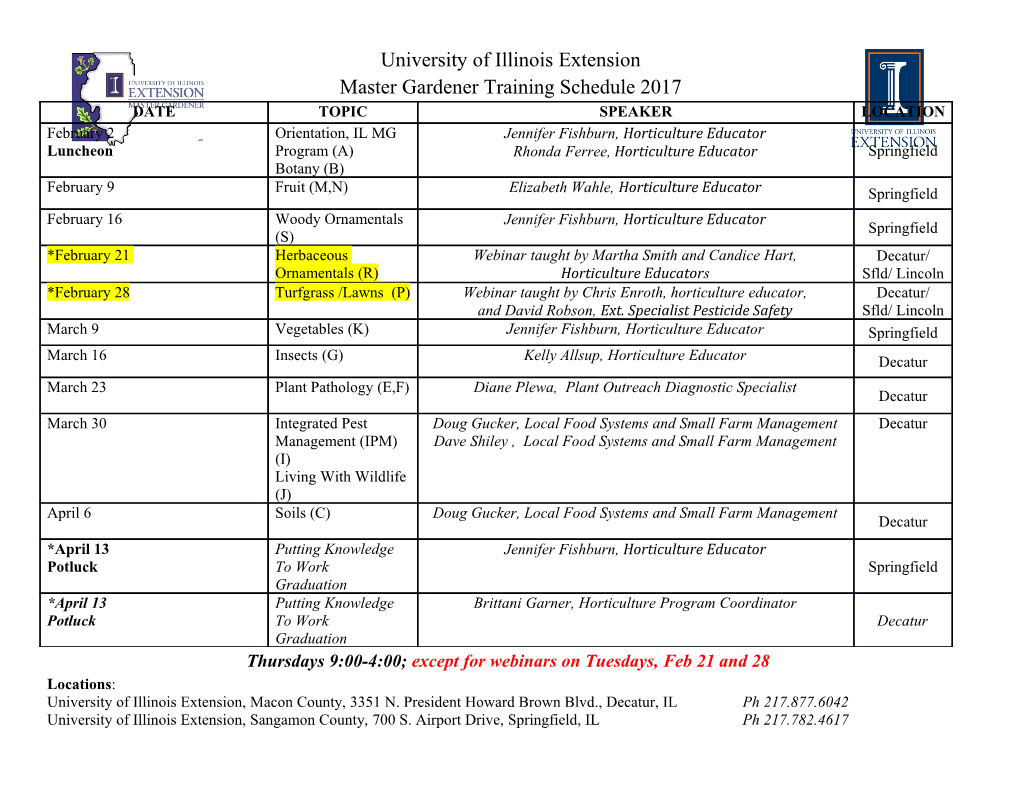
Practical Induction Heat Treating, Second Edition Copyright © 2015 ASM International® R.E. Haimbaugh All rights reserved www.asminternational.org CHAPTER 1 History of Metallurgy and Induction Heating THIS CHAPTER includes a brief history of metallurgy, followed by a discussion of the development of scientific theories involving the electri- cal nature of induction heating. The author incorporates personal experi- ences and memories throughout. History of Metallurgy The Egyptians are believed to have worked copper for centuries before 3500 B.C. A piece of heat- treated steel was found in one of the pyramids, and it is thought to date from 3000 B.C. Early metal workers found certain metals and ores could be refined, processed, and made into tools and weapons, but it was not until the Iron Age and the Hittites that metallurgi- cal processes were developed that would consistently produce strong steel weapons. Although the art of metallurgy developed as early smiths found that heating and cooling iron in different ways could make iron either softer or harder, metallurgical theory lagged behind until relatively mod- ern times. In 1864 Henry Clifton Sorby first used a microscope to study metals. This was followed by Albert Sauveur trying to convince American steelmakers that something practical was to be gained from microscopic examination. However, it has only been since about 1930, when x- ray dif- fraction with wave mechanics was applied to metals, that the science of metallurgy was born. The first induction phenomenon was observed by Michael Faraday in the middle 1800s when the effect that caused the heating of transformer and motor windings was considered to be undesirable. The first construc- tive use of induction occurred in 1916 when it was used to melt metals. Induction heat treating came into prominence in the 1930s, when high- 2 / Practical Induction Heat Treating, Second Edition frequency motor- generator sets were developed and used for the induction hardening of crankshaft journals and bearings. In 1938, Caterpillar in- stalled a power supply for induction hardening track links, and by 1943 they had 16 induction-hardening units in production (Ref 1). In 1941 Vaugn, Farlow, and Meyer presented a paper titled “Metallurgical Control of Induction Hardening” at the convention of the American Society for Metals, which provided proof that alloy elements such as nickel and chro- mium were wholly unnecessary for maximum surface hardness and that carbon steels could be used in place of alloy steels. Caterpillar subse- quently purchased a 500 kW, 9.6 kHz motor generator set for induction hardening their final drive gear with a 642 mm (25.7 in.) diameter by a 125 mm (5 in.) wide face. In an article in the July 1943 issue of Metal Progress, the Caterpillar process for contour hardening this gear was pre- sented. Figure 1.1 shows the contour pattern produced at that time by Caterpillar. Caterpillar must be considered the early pioneer in the contour hardening of gear teeth. Progress in research in metallurgical principles of induction hardening continued, and at the 26th annual meeting of the American Society for Metals in 1944, D.L. Marten and F. E. Wiley presented a paper that re- ported investigation of temperature, composition, and previous structure upon induction-hardening characteristics of plain carbon steel (Ref 2). The basic metallurgical theory as presented at that time is still being taught today. Fig . 1 .1 Hardness survey (Rockwell C scale) of hardened tooth, sectioned on center. Magnified 2¾ diameters. Source: Ref 1 Chapter 1: History of Metallurgy and Induction Heating / 3 Induction Heating after World War II In 1946, Edwin Cady listed the basic types of induction equipment (Ref 3) with frequencies ranging from 25 Hz to 50 MHz: • Electronic circuit (vacuum tube, 300 to 530 kHz, and greater than 1 MHz) • Spark gap (15 to 60 kHz and 125 to 450 kHz) • Rotary converter (motor generator, 1 to 10 kHz) • Mercury arc (400 Hz to 3 kHz) • Standard power cycle (line frequency of 60 Hz, or 25 Hz as generated by some steel mills) While other types of power supplies and converters have been used over the years, the intent of this book is to discuss those commonly used for induction heat treating. The first induction heaters sold by General Electric during World War II had rectifier tubes for the conversion of the alternating current (ac) to di- rect current (dc). Output control and tuning were accomplished through a combination of different taps on the output of the tank coil and a control knob that tapped the plate transformer for different output voltages. The power was turned on and off through the use of a main solenoid- activated contactor. Cycle times were controlled through use of a mechanical, cam- driven timer. The output was the high voltage obtained directly from the tank voltage, and low- turn work coils could not be used. Coil designs to heat small areas were developed in many creative ways. For example, to get around overloads, a shunt coil was used. This was a coil made of copper tubing that was placed directly across the high- voltage output from the tank circuit. The coils were typically wound to a 102 mm (4 in.) diameter; the number of turn shunts varied from 5 to 13. The shunts were water cooled, with the water coming from T connections on both sides of the shunt. While it seemed that all of the power would be lost in the shunts, they actually worked quite well. If power reduction to prevent a slight overload at the “heat on” position was needed, a 13-turn shunt could be installed and used. If the overload was severe, a 5- turn shunt could reduce the power substantially. Setup instructions would indicate what shunt was to be used. The shunts, when used properly, actually leveled the power output so that the plate amperage was held more constant. As the workpiece on heating passed through the Curie temperature, the plate amperage with the use of a shunt did not drop as much. The use and development of induction heat treating practices continued to grow after World War II, and output transformers were developed to help the power supplies and load match when using low-turn work coils. Around 1948, General Electric performed research on the optimum design 4 / Practical Induction Heat Treating, Second Edition for output transformers for radio-frequency (RF) induction heaters. They ran tests on both the size of the transformer (settling on 152 mm, or 6 in.) and the stepdown ratio (11:1 found to be most desirable). The primary was sealed in beeswax, and the secondary was one turn, water-cooled, similar to current output transformers. The first transformer tops for sealing and mounting the outputs were Bakelite, which was later replaced by Micolex. In the 1950s General Electric went to a 279 mm (11 in.) diameter trans- former with a 7:1 stepdown ratio. Because of the output transformers’ single turn secondary, low turn work coils could now be used. In addition, the coils could be grounded on one side, so arcs that occurred with high- voltage coils were practically eliminated. From the 1940s through the 1950s, the use and application of large motor generators and RF oscillator induction power supplies continued. In the mid-1950s General Electric introduced a new RF induction heater. It featured an aluminum-enclosed oscillator section; the internal bus compo- nents were silver plated. Rectifier tubes were still used for the dc conver- sion, but two of the models that were available had three triode rectifier tubes so that thyratron power controls could be used for stepless power control and for power turn-on. Two of the models featured an internal output transformer that was rigidly attached and had an air core. The out- put power ratings were proven through running a water load in a work coil. The induction heaters featured what was called a filament regulated transformer- capacitor network that provided about 3% regulation through swings of line voltage. Motor- driven voltage regulators could be furnished on request. The induction hardening of air-to- air missile fuse bodies was developed during the Korean War. These were the striking end of the air- to- air mis- siles. The bodies required a soft nose to allow collapse on impact, to ex- plode the missile. The requirement was for the body to be hard but the nose totally soft. At that time induction tempering did not produce parts in specification. A 20 kW RF induction heater was used for austenitizing with direct tank-loaded coils (high voltage). The coils themselves were contoured to the shape of the fuse body, starting with 6.35 mm (0.25 in.) 3 copper tubing at the top for about four turns, moving into 4.18 mm ( /16 in.) copper tubing around the bottom to provide higher current concentration. The nose of the fuse body was placed onto a brass, water- cooled nest to prevent the nose from heating and hardening. Nitrogen atmosphere was used to prevent scale, with an austenitizing cycle of 9 s. The parts were oil quenched in mineral oil and then furnace tempered. The final surface fin- ish was good enough that the fuse bodies could be plated afterward with any finish machining or polishing. About 1959, International Harvester (IH) found that customers who purchased new tractors were replacing the track shoe bolts with Cater- pillar bolts before use. The Caterpillar bolts were induction hardened and did not wear. The IH bolts were overall hardened and tempered but did Chapter 1: History of Metallurgy and Induction Heating / 5 not have contour- hardened heads. The heads of the bolts wore in use, and the bolts had to be chiseled out for replacement.
Details
-
File Typepdf
-
Upload Time-
-
Content LanguagesEnglish
-
Upload UserAnonymous/Not logged-in
-
File Pages7 Page
-
File Size-