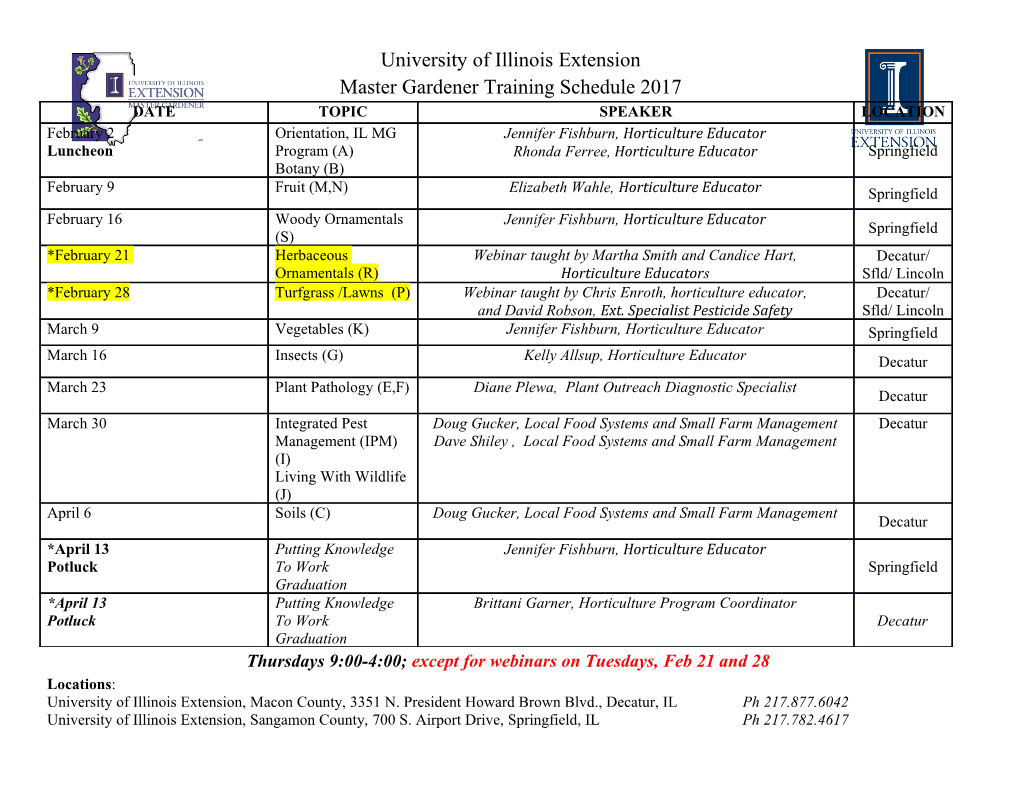
United States Patent (19) 11 Patent Number: 4,794,050 Campbell et al. (45) Date of Patent: Dec. 27, 1988 (54) RESISTANCE WELDING OF GALVANIZED STEEL OTHER PUBLICATIONS 75 Inventors: Donald H. Campbell, Honjo et al., “International Journal of Materials and Niagara-on-the-Lake, Canada; Product Technology" vol. 1 No. 1 pp. 83-114 1986. Gerald L. Evarts, Tonawanda, N.Y. Primary Examiner-John F. Terapane 73) Assignee: Occidental Chemical Corporation, Assistant Examiner-Eric Jorgensen Niagara Falls, N.Y. Attorney, Agent, or Firm-James F. Tao; William G. (21) Appl. No.: 59,298 Gosz 22 Filed: Jun. 8, 1987 57 ABSTRACT A coating for improved resistance welding of galva 51) Int. Cl." ................................................ B22F7/04 nized steel parts or sheets comprises a binder, and a 52 U.S.C. ........................................ as a to a 428/551 metal phosphide pigment, preferably a ferrophosphorus 58 Field of Search ................ 428/551, 555, 556, 621 pigment, having a particle size of from about 0.1 to 56 References Cited about 30 microns. The pigment can also include up to U.S. PATENT DOCUMENTS about 40% by weight of an additional metal such as tin, 4,337,299 6/1982 Van den Bergh .................. 428/551 aluminum or lead, which can be combined with the 4,350,539 9/1982 Torok et al. ........................ 428/555 metal phosphide in pigment form or deposited onto the 4,497,876 2/1985 Kidon .................................. 428/621 surface of the particles. The coating can be applied to 4,524,111 6/1985 Oka et al. ............................ 428/551 either the faying or non-faying surfaces of the galva 4,601,957 7/1986 Fujimoto et al. ................... 428/621 nized steel, or to the resistance welding electrode, and 4,707,415 11/1987 Ikeda et al. ......................... 428/621 may be removed, if desired, after the welding operation. FOREIGN PATENT DOCUMENTS The advantages of the present invention include a sig 59-111388 3/1984 Japan ................................... 428/556 nificant reduction in welding current and an increase in 59-111389 3/1984 Japan ................................... 428/556 the weldability lobe width, a restoration of the dynamic 59-146844 8/1984 Japan . resistance beta peak, and an increase in electrode life. 61-41540 2/1986 Japan . 61-253397 11/1986 Japan. 11 Claims, No Drawings 4,794,050 1. 2 usually adhere to one of the two sheets as a weld "but RESISTANCE WELDING OF GALVANIZED STEEL ton', and the size of this weld button can be measured with a set of calipers. The weld button size is usually BACKGROUND OF THE INVENTION considered a good measure of the nugget size. The The present invention relates to an improvement in 5 limits of the weldability lobe are defined by the welding the resistance welding of galvanized, i.e. zinc or zinc conditions which produce a minimum weld size on one alloy coated, steel parts or sheets which is achieved by side, and expulsion on the other (expulsion occurs when coating either the alvanized surface to be welded or the liquid metal is expelled from the weld during welding). welding electrode with a resin binder containing a metal A line representing a nominal button size (part way phosphide pigment, and preferably a ferrophosphorus O between the minimum and expulsion) is also often in pigment. The welding improvements realized by prac cluded. ticing the present invention are improved weldability The weldability lobes are characterized by lobe posi lobes and dynamic resistance curves for better welding tion, lobe width and the position of the nominal button control for resistance welding systems as well as in line. See, generally, D. W. Dickinson, Welding in the creased electrode life. 15 Automotive Industry, Report SG 8-15 of the Committee The use of galvanized steel sheets in the automotive of Sheet Steel Producers, the American Iron and Steel industry has become increasingly popular in recent Institute. The lobe position is defined as the average years due to the increase in concern for corrosion pro welding current of the lobe. Though lobe position is not tection for automobile body panels. Corrosion problems considered to be a critical weldability parameter, higher are particularly severe in environments where salt is 20 welding currents do result in higher energy costs, as used for preventing the icing of snow on highway well as a decrease in electrode life. More significant is roads. Although efforts have been made to enhance the the width of the weldability lobe defined as the differ corrosion-resistance of steel sheets, such as by using ence in welding currents between minimum button and various chemical conversion treatments and paint coat expulsion at a particular welding time. This is a measure ings, the corrosion protection method of choice cur 25 rently is galvanized steel, with the galvanized coating of a materials' "flexibility” during spot welding. The formed by either hotdipping or electrodeposition. position of the nominal button line, although considered For zinc or zinc alloy coated sheet steels to success of lesser importance, is also a measure of a materials' fully substitute for uncoated sheet steels, they must flexibility during spot welding. A central position for exhibit acceptable formability and weldability charac 30 this line indicates a button size with adequate current teristics. As a general rule, coated steels have not dem range to both higher and lower currents. onstrated properties as good as their uncoated counter Dynamic resistance is used as a measure of weld parts. Users of these products are continually looking quality and is defined as the resistance of the weld for new coated sheet steels which provide the advan across the electrodes (as a function of time) during tages of a coated steel, but have weldability and form 35 welding. The dynamic resistance has been correlated to ability characteristics similar to uncoated steels. weld development in uncoated steels, and successfully The most common method of joining steel sheets used as an input signal for feedback control. Unfortu (particularly in the automotive and appliance industries) nately, the results for zinc or zinc alloy coated steels is ressstance spot welding. Resistance spot welding is have not been as good. In particular, feedback systems ideally suited for joining thin sheet materials and is well 40 have been largely unsuccessful in controlling weld de adapted to mass production industries. In addition, op velopment in such coated steels which exhibit a feature erating costs for this process are relatively low. Resis less resistivity trace or curve. The dynamic resistance tance spot welding has been used with uncoated steels trace for uncoated steel, in contrast, exhibits a charac quite successfully since the 1930's. teristic "beta peak', followed by a resistance drop. It is Resistance spot welding is used to form joints be 45 the presence of this "beta peak" which makes resistive tween two materials. The process uses a set of elec feedback control possible. See Dickinson, supra. trodes to apply pressure to the weld area, to maintain When resistance welding uncoated steels, a single set the components in position, and to pass current through of copper welding electrodes can be expected to make the weld. As the current flows, joule heating of the approximately 50,000 welds. When welding galvanized substrate occurs. Due in part to the cooling effects of 50 steels, however, the electrode life is reduced to about the electrodes, a molten nugget eventually develops at 1000-2000 welds or less. Since the production line the weld centerline or faying surface. On cooling, this must be stopped each time an electrode is replaced, at a nugget resolidifies and effects a joining between the two considerable expense to the user, the relatively limited materials. electrode life for galvanized steels represents a signifi As mentioned, resistance spot welding of uncoated 55 cant economic disadvantage. steels has historically been quite successful. However, The use of ferrophosphorus pigment for both im the resistance spot weldability of coated sheet steels has proved corrosion protection and weldability has been not been as successful. The problems can be best seen by suggested in the prior art. For instance, U.S. Pat. No. reference to some typical measures of spot weldability. 3,884,705, issued May 20, 1975 and U.S. Pat. No. The weldability lobe is defined as the range of weld 60 4,119,763, issued Oct. 10, 1978, both disclose the use of ing conditions (weld current and weld time) over which coatings containing ferrophosphorus and zinc pigments, weld nuggets of an adequate size can be formed. This, in and a non-metallic corrosion inhibitor such as zinc chro effect, defines a "window' of acceptable welding con mate, as a replacement for zinc-rich coatings. These ditions. When practical, weld nugget sizes during lobe coatings also contain a non-metallic corrosion inhibitor testing are estimated with a destructive test known as 65 such as zinc chromate. As contemplated in these pa the peel test. This test consists of welding two 1-inch tents, the ferrophosphorus pigment-containing coating by 4-inch samples at two points, and destructively pull is applied to bare steel panels rather than to galvanized ing apart the second of the welds. The weld nugget will sheets. The ferrophosphorus pigment used in such ap 4,794,050 3 4. plications is commercially available from the Occiden tal Chemical Corporation under the trademark Ferro DESCRIPTION OF THE PREFERRED phos (R) pigment. EMBODIMENTS A ferrophosphorus pigment dispersed in a resin to The steel sheets or formed parts which are used in the bind adjacent steel plates to form a vibration-damping 5 present invention contain a thin layer of zinc metal or a composite suitable for resistance welding is disclosed in zinc alloy which is direct contact with the steel surface.
Details
-
File Typepdf
-
Upload Time-
-
Content LanguagesEnglish
-
Upload UserAnonymous/Not logged-in
-
File Pages6 Page
-
File Size-