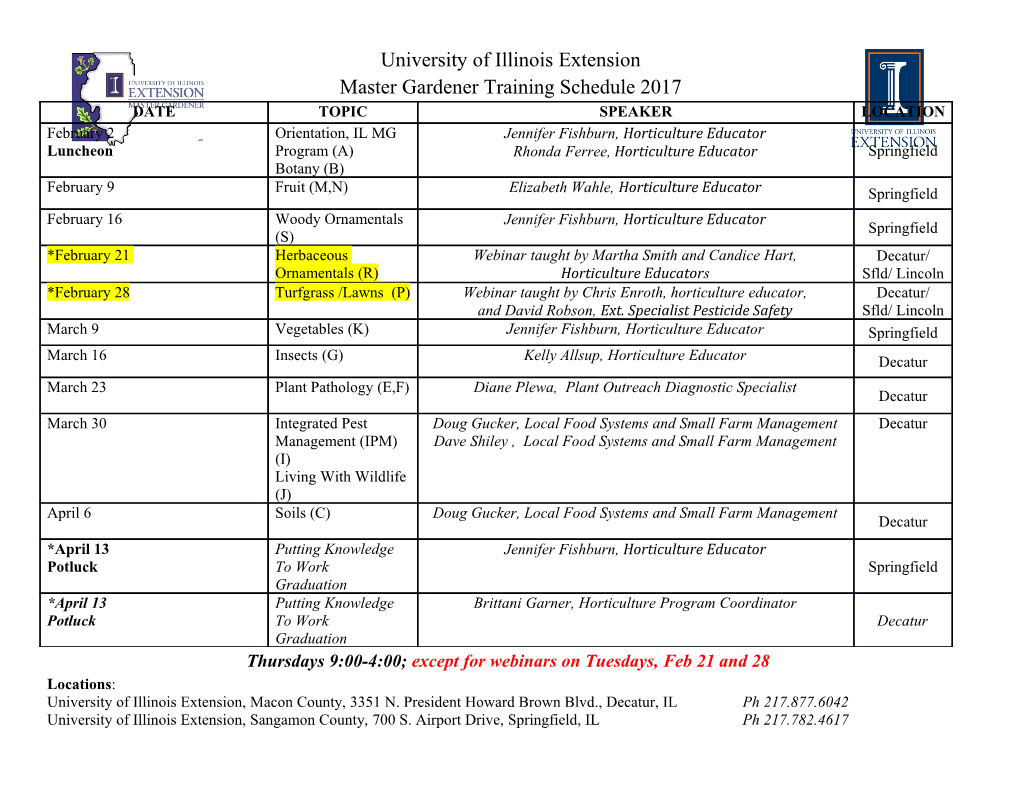
STEREO MECHANICAL DESIGN, INTEGRATION, AND TESTING STEREO Spacecraft Mechanical Design, Integration, and Testing Stuart W. Hill, Teresa M. Betenbaugh, and Weilun Cheng his article describes the significant mechanical efforts stemming from the Solar TErrestrial RElations Observatory (STEREO) mission. Because of the unique two-observatory mission design, the STEREO observatory mechani- cal design and integration were confronted with several nonstandard difficulties. Impacts to the mechanical effort from the STEREO launch stack, dual-spacecraft requirement, and the observatories’ nearly identical design are addressed. Each sec- tion details these aspects and how they specifically impacted the mechanical effort. Considerable attention is given to the unanticipated issues encountered and how they were either eliminated or mitigated. These issues resulted in several lessons learned, which also are presented, that are being carried forward for future dual- Tspacecraft missions throughout the space community. INTRODUCTION The Solar TErrestrial RElations Observatory the more unique aspects of the mission that forced the (STEREO) spacecraft mechanical effort experienced mechanical team to maintain an adaptable approach to many of the standard challenges that mechanical teams the STEREO mechanical engineering effort. face throughout a spacecraft’s development effort. In addition to these challenges, the STEREO mechanical effort encountered many others specific to the STEREO MECHANICAL DESIGN mission due to the unique dual-spacecraft mission design. The STEREO spacecraft mechanical design under- Many of these challenges were anticipated; however, as went considerable changes from origination to flight. Ini- with all complex engineering efforts, several were unan- tially, the STEREO mission scheduled the two spacecraft ticipated or thought to be of minimal impact to the to be launched independently from each other on two overall effort. This article introduces the evolution of dedicated Athena launch vehicles. Because of Athena the STEREO mission mechanical design and several of launch-vehicle availability problems, the STEREO mis- JOHNS HOPKINS APL TECHNICAL DIGEST, VOLUME 28, NUMBER 2 (2009) 187­­­­ S. W. HILL, T. M. BETENBAUGH, AND W. CHENG sion was forced to find other candidate launch vehicles. the balance requirement was levied on the STEREO Several different launch vehicles were considered, launch stack by the Delta II launch vehicle. The physi- including a scenario with both spacecraft on a single cal layout and placement of spacecraft components were Space Shuttle flight, as shown in Fig. 1. In the end, the driven by this requirement. As component and instru- STEREO mission determined that a single Delta II ment masses changed during development, the mechan- launch vehicle would be used. The choice to use a single ical layout for both spacecraft had to be modified. Once launch vehicle to deliver the STEREO spacecraft into instruments and components were packaged on the their proper orbits placed a packaging requirement on spacecraft to meet specific field-of-view (FOV) and ther- the physical launch configuration for both spacecraft. mal requirements, the mechanical design space to con- From this requirement, the STEREO spacecraft eventu- figure the spacecraft in a balanced state was very small. ally were designed to launch in a stacked configuration, Figure 2 shows the STEREO launch stack mated to the with STEREO B placed below STEREO A. The stacked Delta II launch vehicle during fairing installation. launch configuration drove much of the mechanical design for the STEREO spacecraft and created unique challenges throughout both the design and the integra- DUAL-SPACECRAFT CHALLENGE tion and testing (I&T) effort for the STEREO mission. The dual-spacecraft mechanical operation car- The final, as-flown mechanical design of both ried with it rather obvious requirements related to the STEREO spacecraft was an efficient primary load- overall amount of hardware and ground-support equip- carrying central cylinder surrounded by honeycomb ment (GSE) needed to process two spacecraft. These decks that supported the majority of the spacecraft’s requirements were relatively easily met. The design stage instruments and components. Each spacecraft structure of the program essentially was carried out as a single- was designed specifically to support the spacecraft’s role spacecraft design to be built twice with the majority of in the launch-stack configuration. STEREO B, which both spacecraft designs being identical. For mechanical supported STEREO A during launch, was designed assembly and I&T, space requirements were double that with a stronger central load-carrying cylinder, whereas the central cylinder for STEREO A was designed to support lifting operations of the entire stack. The honeycomb decks supporting spacecraft components and instruments were consistent between both space- craft and were mounted around the central cylinder, creating internal bays around the cylinder. These inter- nal bays contained the majority of spacecraft compo- nents, whereas the instruments were mounted on the exterior of the panels. With components mounted on both the inside and outside of the spacecraft structure, access to internal components, while not disturbing externally mounted components, became a mechanical design focus. As a part of the launch-vehicle requirements, the launch stack had to be static and dynamically balanced. Before the third-stage release and ignition, the launch stack was spun-up for stability during burn. The third stage had no attitude control system, and because of this, Starboard 1 2 3 4 5 6 7 8 9 10 11 12 13 Port 1 2 3 4 5 6 7 8 9 10 11 12 13 Primary payloads Figure 1. Proposed STEREO launch configuration in Space Shuttle. Figure 2. STEREO stack on Delta II launch vehicle. 188 JOHNS HOPKINS APL TECHNICAL DIGEST, VOLUME 28, NUMBER 2 (2009) STEREO MECHANICAL DESIGN, INTEGRATION, AND TESTING of a traditional spacecraft mission. However, because of far more daunting and challenging than those at the sin- the parallel processing of the New Horizons mission in gle-spacecraft level. Because much of the environmental the APL cleanrooms, both missions were relatively tight testing of the STEREO mission was conducted in the on space. I&T operations were conducted at times in a stacked configuration (vibration, acoustic, spin balance, serial manner, and at other times they were conducted in and mass properties), the stack requirements had to be parallel. All mechanical configurations and operations, fully understood and planned for. Stack-specific require- with the exception of lifts, were conducted at least once ments for testing, such as access and GSE setup, were in parallel. The potential for parallel operations necessi- much more involved than similar requirements for a tated that each piece of required GSE had to be provided single spacecraft. Because of the overall height of the in duplicate. Obviously, operations to assemble and test stack and the unique configurations in which the stack one spacecraft were repeated on the other, and some ended up, the STEREO I&T team was challenged up to overall efficiency was realized by repeating the same effort. the very end of the program. Although this originally was planned as a time-saving feature of the dual-spacecraft processing effort, much of this time was taken up by spacecraft-unique problems “IDENTICAL” SPACECRAFT or dissimilarities that were not foreseen in the original When the STEREO spacecraft are reported in the planning of the STEREO effort. Concurrent operations news, they usually are described as “nearly identical with both spacecraft did provide the capability to switch observatories.” Although the spacecraft were designed from one spacecraft to the other when testing went long similarly, the observatories did have significant dif- or unplanned events took place on one spacecraft. This ferences. These differences became more apparent as feature of the program, which was utilized very well as assembly and I&T operations progressed. The individual the program continued, was the most time-saving and characteristics of each observatory became important to useful aspect of dual-spacecraft processing. understand in order to properly prepare the STEREO Some of the less obvious aspects of the STEREO dual- observatories for launch. Two of the key differences were spacecraft mechanical processing effort are mentioned the design of the top and bottom mounting interfaces below. One item to be noted is that two spacecraft were of the central cylinder and the placement of the In situ assembled, integrated, tested, and launched by a small Measurements of PArticles and Coronal mass ejection mechanical team of approximately six to seven individu- Transients (IMPACT) suite of instruments on the +y als. This small team was able to maintain consistency decks. These two externally visible differences were between the two mechanical efforts while enabling les- used as quick references to distinguish STEREO A from sons learned on one spacecraft to be passed quickly to STEREO B. others within the team. Because of this benefit, very few The primary cylinder designs of the two spacecraft failures or problems were repeated on both spacecraft. were driven by the unique launch loads and interfaces Within this small mechanical team, each member spe- required for each spacecraft. STEREO B, which was the cialized in a handful of operations for which they pri- bottom spacecraft in the launch stack, had
Details
-
File Typepdf
-
Upload Time-
-
Content LanguagesEnglish
-
Upload UserAnonymous/Not logged-in
-
File Pages11 Page
-
File Size-