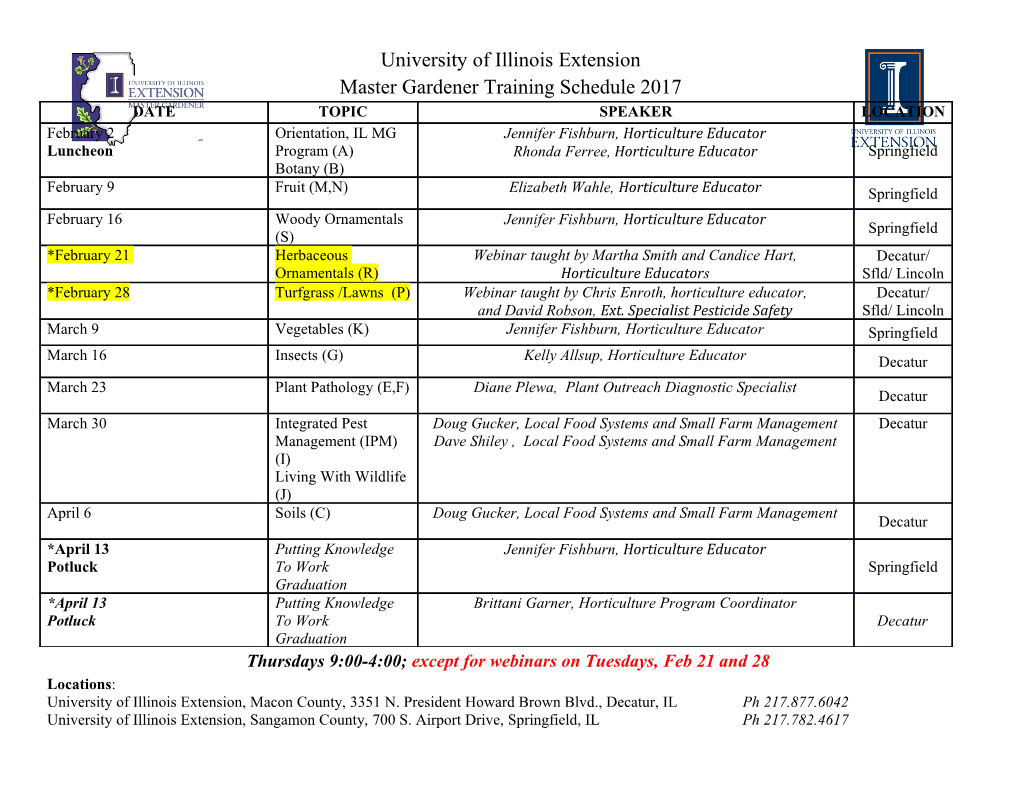
Sensors and Actuators A 113 (2004) 1–11 Analysis of thin film piezoelectric microaccelerometer using analytical and finite element modeling Qing-Ming Wang∗, Zhaochun Yang, Fang Li, Patrick Smolinski Department of Mechanical Engineering, University of Pittsburgh, 639 Benedum Hall, Pittsburgh, PA 15261, USA Received 5 November 2003; received in revised form 11 February 2004; accepted 28 February 2004 Available online 24 May 2004 Abstract Microaccelerometers using piezoelectric lead zirconate titanate (PZT) thin films have attracted much interest due to their simple structure and potentially high sensitivity. In this paper, we present a theoretical model for a microaccelerometer with four suspended flexural PZT-on-silicon beams and a central proof mass configuration. The model takes into account the effect of device geometry and elastic properties of the piezoelectric film, and agrees well with the results obtained by the finite element analysis. This study shows that the accelerometer sensitivity decreases with increases in the beam width, in the thickness of the bilayer beams, and in the elastic modulus of the mechanical microstructure. Increases in the beam length increase sensitivity. For a fixed beam thickness, a maximum sensitivity exists for appropriate PZT/Si thickness ratio. In addition, it is found that with appropriate geometrical dimensions, both high sensitivity and broad frequency bandwidth can be achieved. The calculation of the stress distribution in the suspended PZT/Si beam structure when the device is subjected to large vibrational acceleration indicates that the thin film microaccelerometer can stand extremely large g conditions with very good mechanical reliability. In the dynamic analysis, it is found that both analytical model and finite element modeling give very close results of the resonance frequency of the device. The results of this study can be readily applied to on-chip piezoelectric microaccelerometer design and its structural optimization. © 2004 Elsevier B.V. All rights reserved. Keywords: Piezoelectric accelerometer; MEMS; Sensitivity; Lead zirconate titanate (PZT) thin film 1. Introduction piezoelectric accelerometers have been widely used in con- dition monitoring systems to measure machinery vibration. Piezoelectric accelerometers use the direct piezoelectric Recently, microaccelerometers using piezoelectric thin film effect of a piezoelectric ceramic, crystal or thin film to gen- have drawn much research interest due to the miniaturiza- erate an electrical charge output that is proportional to ap- tion trend of electronic devices, their low cost and their suit- plied acceleration [1–3]. In an accelerometer, the stress in ability for batch manufacturing [4–7]. Research has focused the device occurs as a result of the seismic mass vibration on the thin film accelerometer design [8], fabrication [9], imposing a force on the piezoelectric materials. The total device’s measurement capabilities [10] and structural anal- amount of accumulated charge is proportional to the applied ysis and modeling to increase the sensitivity of the devices. force and the applied force is proportional to acceleration. For example, Eichner et al. [11] have measured the me- The electrodes on the piezoelectric device collect the charge chanical vibration and electromechanical sensitivity of mi- that can be transmitted to a signal conditioner that is remote cromachined accelerometer devices with four piezoelectric or built into the accelerometer. Once the charge is condi- read-out capacitors; Ries and Smith [12] have used the finite tioned, the signal is available for display, recording, analysis element method to analyze a deformable array transducer; or control as a varying voltage [2]. and Yu and Lan [13] presented system modeling for the de- Piezoelectric accelerometers have the advantages of low sign of a microaccelerometer. However, it should be pointed cost, simple structure, easy integration with electronic cir- out that all of these studies simply assume that the piezo- cuitry, wide frequency response and high sensitivity. Thus, electric PZT thin films are very thin and can be neglected in the mechanical analysis. Considering that the thickness of ∗ Corresponding author. Tel.: +1-412-6244885; fax: +1-412-6244846. PZT films deposited on-chip by sol–gel spin-on deposition, E-mail address: [email protected] (Q.-M. Wang). or screen printing are typically from 0.5 to 5 m, even up to 0924-4247/$ – see front matter © 2004 Elsevier B.V. All rights reserved. doi:10.1016/j.sna.2004.02.041 2 Q.-M. Wang et al. / Sensors and Actuators A 113 (2004) 1–11 20 m [14,15], the effect of thickness and the elastic prop- PZT thin film elements, thus, greatly enhance the sensitivity erties of piezoelectric films should be taken into considera- of the device. Each piezoelectric transducer is composed tion in structural analysis and device performance modeling. of an upper electrode, a piezoelectric thin film and a lower Inclusion of the effects of film thickness in analysis would electrode. The two PZT elements on each beam are poled provide a more accurate estimation of device performance in opposite directions along the thickness. To collect the and, therefore, would aid in device design. generative electric charge from the thin film piezoelectric The aim of this paper is to study both the static and dy- elements when the accelerometer is subjected to an applied namic behavior of the microaccelerometer accounting for acceleration, the two PZT thin film transducer elements on the effect of PZT film thickness. Both an analytical and a each beam can be connected electrically either in parallel or computational model are developed and the results are com- in series. In the case of series connection, the two PZT thin pared. Using the analytical model, the effects of device ge- film elements are connected through the lower electrodes, ometry and the elastic properties of PZT thin film on the while output electrical terminals (connections) are made sensitivity of the accelerometer are evaluated. The results of through the two top electrodes, as shown in Fig. 2(a). Since, this analysis can be used as a base for thin film piezoelectric the stresses of the two PZT elements are in the opposite di- microaccelerometer design and performance optimization. rections due to bending of the beam, i.e. one is subjected to tensile stress and the other compressive stress; the two series connected elements behave like two series voltage sources. 2. Analytical models of thin film piezoelectric In the case of parallel connection, the electrical terminals accelerometer are made through the top electrode and the bottom electrode. The two piezoelectric thin film elements connected in par- 2.1. Static analysis allel behave like two current sources in parallel. In order to connect the two elements in parallel, the two elements need Generally, the two important parameters in evaluating ac- not to be separated physically by etching processing, but the celerometer sensors are sensitivity and operating frequency top electrodes for each element need be separated during range. Sensitivity can be defined as the generative charge per poling process so that opposite polarization can be produced applied acceleration. Operating frequency range is the flat for the two elements. After poling, the top electrodes can frequency response region below the fundamental resonance be connected by depositing a thin film conductive layer on frequency of the sensor. We consider a microaccelerometer the top of the two devices so that it serves as one electrical configuration with four suspended symmetric beams and terminal. In this paper, for simplicity, we will focus on the a central proof mass. The PZT thin film on each flexural first case with the coordinate system is shown in Fig. 2(a). beam is patterned into two transducer elements, thus eight In practical fabrication of PZT thin film devices on silicon piezoelectric transducers are arranged on four beams sym- chip, sol–gel spin-on coating for PZT films is commonly metrically to form the sensing devices in the structures, as used. A few micrometer up to 10 m thick PZT films and shown in Fig. 1. Yu and Lan [13] have adopted a similar con- their properties have been reported [15–18]. The piezoelec- figuration in their device analysis. When the central mass is tric PZT thin film devices are usually with the multilayer subjected to vertical vibration (acceleration), the suspending structure Pt/Ti/PZT/Pt/Ti/SiO2/Si(1 0 0), in which Pt/Ti elec- flexural beam structure can effectively convert and amplify trodes are very thin, typically from 100 to 150 nm. It is the vertical force (or vibration) of the central mass into the well known that the use of Ti thin film (∼10–40 nm) adhe- planar stress in the transverse direction of the piezoelectric sion layer greatly promotes the bonding strength between the platinum layers with SiO2 and PZT [19]. For simplicity, we ignore the effect of electrode layers in our analysis in this paper, with only PZT/Si two-layer structure for the sus- pended beams being considered for the thin film microac- celerometer modeling. The geometry of the accelerometer structure used for our modeling is given in Table 1. Table 1 Component dimensions in a piezoelectric accelerometer Length of suspension beam, l (m) 400 Width of suspension beam, b (m) 200 Thickness of suspension beam, h (m) 5 Length of seismic mass, lm (m) 800 Thickness of seismic mass, hm (m) 300 Thickness of PZT film, hPZT (m) 0.5–5 Seismic mass, m (mg) 0.26 Fig. 1. A 3D view of the piezoelectric thin film microaccelerometer. Q.-M. Wang et al. / Sensors and Actuators A 113 (2004) 1–11 3 Fig. 2. Piezoelectric thin film elements are connected in (a) series or (b) in parallel. The following assumptions are made in establishing the the beam suspension. Fig. 3 shows the schematic free-body mechanical model of the PZT thin film microaccelerometer: diagram of one of the supporting beams.
Details
-
File Typepdf
-
Upload Time-
-
Content LanguagesEnglish
-
Upload UserAnonymous/Not logged-in
-
File Pages11 Page
-
File Size-