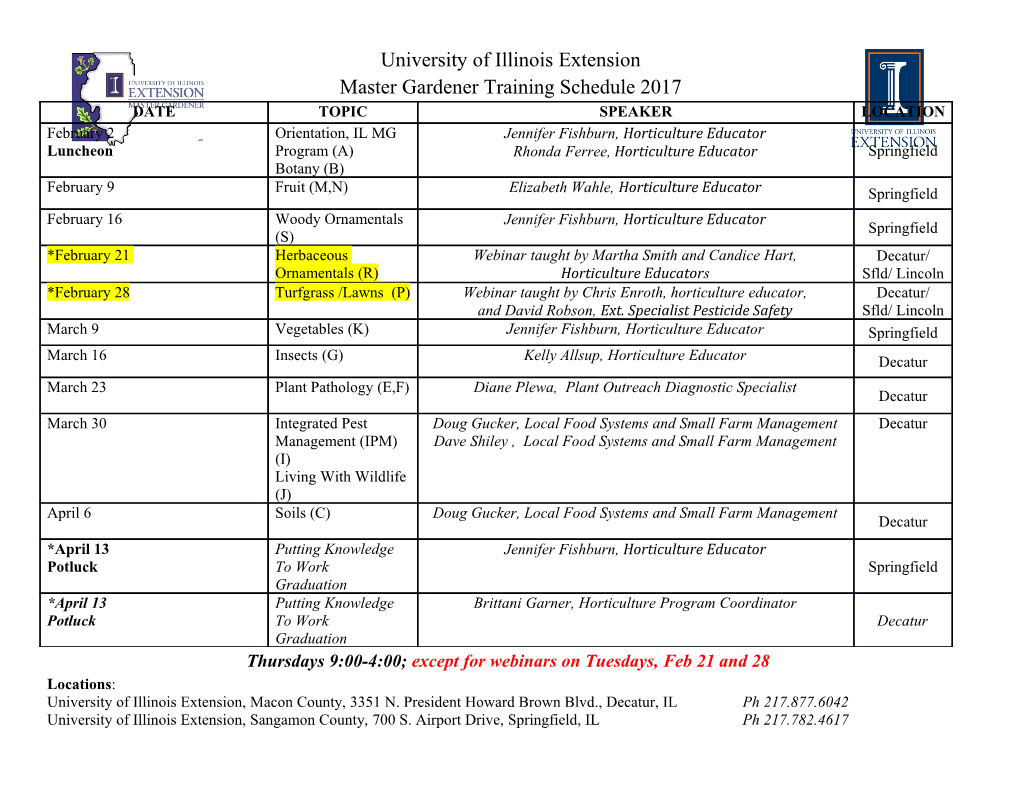
OWI GmbH Rodenbacher Str. 44 - 46 Tel: ++49 (0) 93 52 5 09-0 97816 Lohr am Main Fax: ++49 (0) 93 52 5 09-100 Germany [email protected] www.owi-lohr.de Formteile aus Holz und Kunststoff Technical production data Technical data Development/construction of Manufacturing of veneer on three moulding appliances rotary-cutting lines Moulded parts made of plywood NURBS-modelling and wood laminates 3D surfaces and 3D volume models Processing of high-grade veneers Digitalisation of hand models and other special surfaces supplied by the customer Multiplex boards Construction of our own appliances Diversity / ergonomics / aesthetics Variable compression techniques: FEM calculation more than 60 electrically, high- frequency and steam-heated Production from a renewable resource presses CNC-processing at around 50 workstations Design and creation Assembly and fi nishing Development and construction MOULDED PLYWOOD PARTS Production to order Assembly and varnishing OWI moulded plywood E parts 04.15 MOULDED PLYWOOD PARTS A family business Since 1927 OWI, managed in the third Hungary – is complementing the produc- generation as family business, is supplier tion of moulded plywood parts. Thanks to especially to the seating furniture industry. its advantageous cost structure, OWI Zala Today the site in Lohr am Main in Germany with its employees contributes greatly to is the centre for development, sales and ensure your supply of goods in the right plastic injection moulding production. quality and cost. Already since 1993 the OWI Zala BT – a state of the art manufacturing company in used outside for the first time. process. The still warm trunks are trimmed OWI-Thermoformholz® is also available in to the peeling length and de-barked. The a flame retardant version compatible with peeler blade is fixed in a central position on B1 DIN 4102, Part 1. the rotary cutting lathe, and produces a continuous strip of veneer. The veneer can be between 0.8 mm and 2.1 mm thick; we Rotary-cut veneer prefer to use a thickness of 1.2 mm. On the belt drier the veneer is dried to a wood In our artificially watered wood stores we moisture content of 6 ± 2 %, cut to the Moulded parts made of rotary-cut can keep up to 20000 cubic metres (solid) required width with computerized clippers, beech veneer of beech logs of a quality suitable for and sorted according to quality. The rotary-cutting. In steam heating and boiling material is then conditioned in the con- Beech plywood is a wonderful material to production of moulded parts. Beech stands pits the wood is prepared for the peeling trolled atmosphere of the veneer store. work with. The curved parts produced out for its hardness, durability, elasticity from it are aesthetically attractive, versatile, and strength. Its natural colour and and form the basis of many different types structure make it a versatile material that of ergonomically designed seating. We can be used for many different purposes. process beech from the Spessart forest in Depending on customer requirements, the Northern Bavaria and from the Zala area in moulded parts can be stained or varnished, Hungary. covered with a layer of sliced veneer of The trunks are approx. 100 to 140 years another wood species, or with laminates or old and drawn from sustainably managed undercoating films. OWI also process forests, with FSC or PEFC certification if melamine resin laminates (HPL, CPL). desired. With OWI-Thermoformholz®, we have Because of its mechanical properties, succeeded in taking this material a step beech is particularly suitable for the further, allowing beech plywood to be MOULDED PLYWOOD PARTS Compression moulding In the compression moulding centre the veneer is combined depending on the product to form plywood or wood laminates, and glued with the suitable adhesives. Using pressure and heat, seats, seatbacks, seat shells, armrests, side pieces or frame pieces are pressed into shape on The processing of moulded parts We accompany you throughout your development process: the single or multi-daylight presses After compression moulding the moulded compression moulding machines. The parts are not yet fixed in their contours. Using state-of-the-art CAD/CAM systems, facturers of office furniture and furniture cycle time of the pressing process depends The raw products are milled to contour, we can help you progress highly efficiently for public buildings. We are also familiar on the thickness of the moulded parts. drilled or sanded at one of our many CNC and with great precision from the design with the special requirements of large- The pressing tools are made of wood or machines and other special machines. For stage to the prototype. Our project scale seating arrangements (multi-purpose aluminium and are steam, electrically or finishing we have dust-free spraying rooms managers are not only experts in wood halls, congress centres, grandstand high frequency-heated. At this we select a that provide optimum conditions for moulding technology: they are equally seating) and of living rooms. Customer- suitable technique for each individual part, accuracy with their modern technology. familiar with the language of designers specific moulded parts are also used in depending on the lot size and other As a manufacturer producing to order, we and developers. We offer the platform you many other applications. technical parameters (dimensions, toler- take care of assembly and the logistics as need for well-timed and technologically ance requirements, …), from our machine agreed with you, such as warehousing and sound project management for new pool, which also includes presses allowing commissioning, as well as delivery – on moulded parts and whole construction to exert pressure from the side. The time and in the numbers required – direct series. State-of-the-art technology makes it maximum veneer length we process is to the address specified by you. possible to gauge the potential for distor- 2.20m. Even today, our employees carry out the tion. Critical areas can be neutralized For highly sophisticated, visible parts, face final quality check for our highly special- quickly and precisely on site. The compres- veneers are sanded before pressing, an ised products by hand, according to criteria sion moulding tools are made in house of operation that can only be left out for and statistical values agreed individually solid aluminium or wood on our 5-axis parts which are later to be upholstered. with each customer. CNC machines based on the CAD data After packaging the parts are delivered provided of the customer. ready for assembly. Our speciality is the production of mould- ed parts of superior optical and mechani- cal quality, such as seating and seat backs. Our customers are predominantly manu- MOULDED PLYWOOD PARTS.
Details
-
File Typepdf
-
Upload Time-
-
Content LanguagesEnglish
-
Upload UserAnonymous/Not logged-in
-
File Pages4 Page
-
File Size-