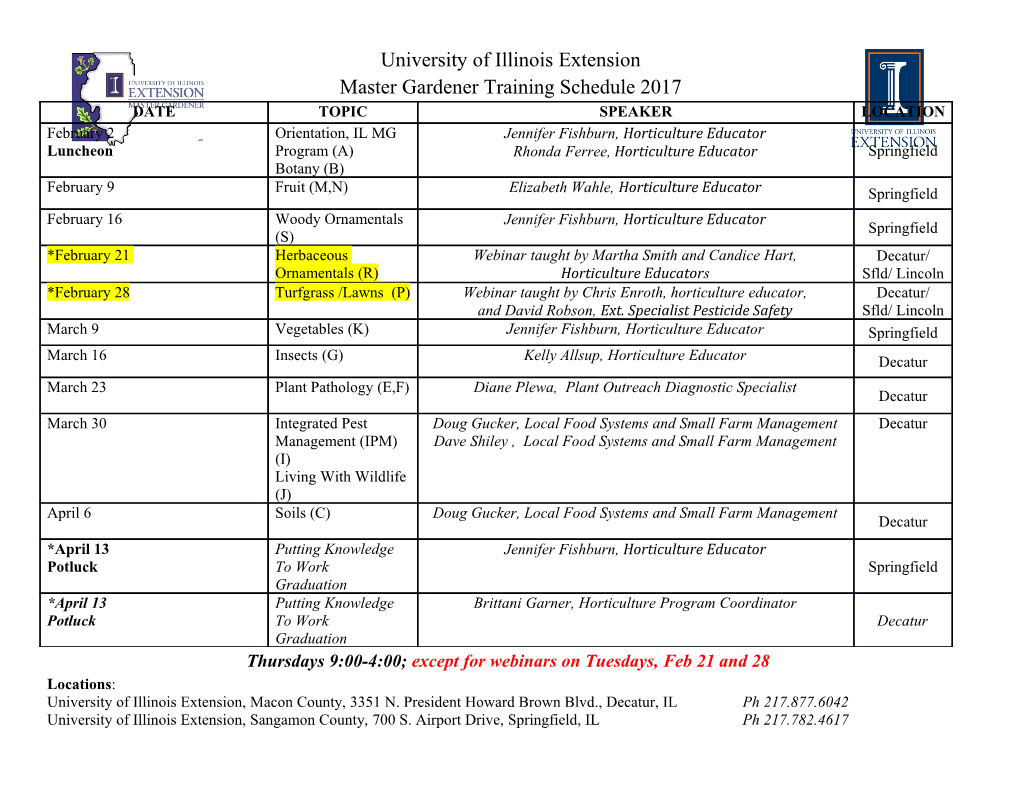
processes Article An Experimental Investigation of Water Vapor Condensation from Biofuel Flue Gas in a Model of Condenser, (1) Base Case: Local Heat Transfer without Water Injection Robertas Poškas *, Arunas¯ Sirvydas, Vladislavas Kulkovas and Povilas Poškas Nuclear Engineering Laboratory, Lithuanian Energy Institute, Breslaujos 3, LT-44403 Kaunas, Lithuania; [email protected] (A.S.); [email protected] (V.K.); [email protected] (P.P.) * Correspondence: [email protected]; Tel.: +370-37401893 Abstract: Waste heat recovery from flue gas based on water vapor condensation is an important issue as the waste heat recovery significantly increases the efficiency of the thermal power units. General principles for designing of this type of heat exchangers are known rather well; however, investigations of the local characteristics necessary for the optimization of those heat exchangers are very limited. Investigations of water vapor condensation from biofuel flue gas in the model of a vertical condensing heat exchanger were performed without and with water injection into a calorimetric tube. During the base-case investigations, no water was injected into the calorimetric tube. The results showed that the humidity and the temperature of inlet flue gas have a significant effect on the local and average heat transfer. For some regimes, the initial part of the condensing heat exchanger was not effective in terms of heat transfer because there the flue gas was cooled by convection until its temperature reached the dew point temperature. The results also showed that, at Citation: Poškas, R.; Sirvydas, A.; higher Reynolds numbers, there was an increase in the length of the convection prevailing region. Kulkovas, V.; Poškas, P. An After that region, a sudden increase was observed in heat transfer due to water vapor condensation. Experimental Investigation of Water Vapor Condensation from Biofuel Keywords: waste heat; condensation; experiments; vertical tube; biofuel flue gas; local heat transfer; Flue Gas in a Model of Condenser, (1) condensation efficiency Base Case: Local Heat Transfer without Water Injection. Processes 2021, 9, 844. https://doi.org/10.3390/ pr9050844 1. Introduction The water vapor condensation process is important for many industrial applications, Academic Editor: Francesca Raganati such as nuclear, chemical, and thermal. To increase the efficiency of thermal power and boiler stations, they are equipped with condensing heat exchangers (economizers). The Received: 9 April 2021 design of condensing heat exchangers depends on the power required [1]. Despite of that, Accepted: 10 May 2021 Published: 12 May 2021 most condensing heat exchangers have housing where a few hundreds of small diameter tubes are installed and the relative length x/d of these tubes could be more than 150. The Publisher’s Note: MDPI stays neutral flue gas from the boiler is routed to these tubes, cooling water flows around them, and a with regard to jurisdictional claims in counter-current flow arrangement is usually used. published maps and institutional affil- As the flue gas leaving the boiler is still of high temperature and humidity, especially iations. when incinerating biofuel, there is a possibility to gain additional heat and increase the efficiency of boiler stations by condensing water vapor from flue gas in condensing heat exchangers. When the dew point is reached, water vapor from flue gas starts to condensate. The condensation process generates an additional amount of heat, which is usually used to heat the return water from consumers. Besides, when the condensate film flows down the Copyright: © 2021 by the authors. Licensee MDPI, Basel, Switzerland. condenser tubes, it precipitates various solid particles from the flue gas that are the most This article is an open access article significant source of environmental pollution, especially when incinerating biofuels [2,3]. distributed under the terms and Although the efficiency of boilers is usually less than 100%, it can be increased by installing conditions of the Creative Commons condensing heat exchangers in boilers, as condensing heat exchangers can get additional Attribution (CC BY) license (https:// amount of heat from the same amount of burned fuel [4,5]. creativecommons.org/licenses/by/ Despite the fact that the general principles for the designing of this type of heat 4.0/). exchangers are known, not much knowledge is acquired of processes taking place in Processes 2021, 9, 844. https://doi.org/10.3390/pr9050844 https://www.mdpi.com/journal/processes Processes 2021, 9, 844 2 of 15 condensing heat exchangers and peculiarities of these processes in the case of flue gas. The review of publications showed that there are many experimental and theoretical studies related to pure water vapor condensation in tubes at a high condensable gas-water vapor content (90–100%, by volume) and small amount of non-condensable gas [6–10], etc. The investigations in Reference [11] of average condensation heat transfer with the steam flow rate of 2.5–5.5 g/s and non-condensable gas mass fraction from 0% to 10% in a vertical tube, whose active length of condensation was x/d ≈ 38, demonstrated that condensation heat transfer decreases with the increase of the non-condensable gas fraction. The analysis of pressure influence also showed that, in the case of pressure decrease in the system, the obtained heat due to the condensation process also decreased. The calculated average condensation heat transfer coefficient at various experimental conditions (system pressure and inlet non-condensable gas mass fraction at inlet) varied from 3 to 10 kW/m2·K. The local condensation heat transfer of pure steam and a steam–nitrogen mixture in a vertical tube was investigated in Reference [12]. The investigations were performed in a relatively long vertical test section (x/d ≈ 230) with the measurements of the cooling water temperature, bulk steam temperature and tube wall temperature along the test section. The steam and the cooling water supply was performed in a counter-current configuration. The steam was supplied from the upper part of the test section. When the pure steam was supplied to the test section at a flow rate of about 11.2 kg/h, the bulk steam temperature was constant (about 100 ◦C) almost till the middle of the condenser tube, i.e., up to x/d ≈ 107, which indicated that condensation is taking place in that part of the test section. When x/d was in the range from 107 to 162, a sudden decrease in the bulk temperature to about 17 ◦C was observed. From x/d ≈ 162 until the end of the test section, the bulk temperature was almost constant. The bulk temperature breakdown at x/d ≈ 107 means that, after that point, all the vapor was condensed and there was a single phase only, i.e., condensed water flowing in the tube. The character of the cooling water temperature was not so evidently expressed as that of the bulk steam temperature. The cooling water (flow rate 290 kg/h) temperature (at the inlet of about 17 ◦C) was changing insignificantly from the end of the test section until about x/d ≈ 107. From x/d ≈ 107 until the beginning of the test section, the cooling water temperature was increasing and reached almost 40 ◦C. The obtained character of the water temperature clearly indicated when the water was gaining heat due to steam condensation. With the increase of non-condensable gas mass fraction up to 10.2%, the bulk steam temperature drop was not so evidently expressed as in the case with pure steam. In this case, also, the decrease from about 100 ◦C at x/d ≈ 107 was observed, and the temperature was continuously decreasing until the end of the test section, where it was about 60 ◦C. Along all the test section, two-phase flow was observed, as not all the steam was condensed, as in the case before. The cooling water temperature was negligibly increasing from ≈17 to ≈20 ◦C from the end of the test section until about x/d ≈ 107. From x/d ≈ 107 until the beginning of the test section, the increase was better expressed, meaning that the cooling water was heated from ≈20 to ≈40 ◦C. The analysis of the local condensation heat transfer showed that the increase of the non-condensable gas mass fraction significantly decreased the local condensation heat transfer. However, this was true until x/d ≈ 65, and further from that point, the change of non-condensable gas mass fraction at the inlet from 3% to 30% practically had no influence on heat transfer. The results presented in papers [11,12] also generally reflect the main aspects occurring in vertical heat exchangers in the case of pure steam or steam condensation with small amount of non-condensable gas. The main conclusions determined in these works are that, in the case of pure steam, the condensation occurs almost in the initial part of the experimental section and it results in very high heat and mass transfer rates. When incinerating biofuel or other fuels, the flue gas usually contains a relatively small amount (~5–25% vol.) of water vapor and the remaining portion consisting of non-condensable gas is high. Thus, in the case of flue gas, the situation is different in comparison to that presented in References [11,12]. Processes 2021, 9, 844 3 of 15 The condensation of flue gas generated by incinerating natural gas was studied in Reference [13]. The experiments were performed in a rather short vertical tube x/d ≈ 80, with inlet water vapor volume fraction of 15–18%. The Reynolds number for flue gas during the experiments was varied from 2300 to 5000. The results indicated that the water vapor in the flue gas increased the average total heat transfer at least by about two times in comparison with dry air in the same range of Reynolds numbers.
Details
-
File Typepdf
-
Upload Time-
-
Content LanguagesEnglish
-
Upload UserAnonymous/Not logged-in
-
File Pages15 Page
-
File Size-