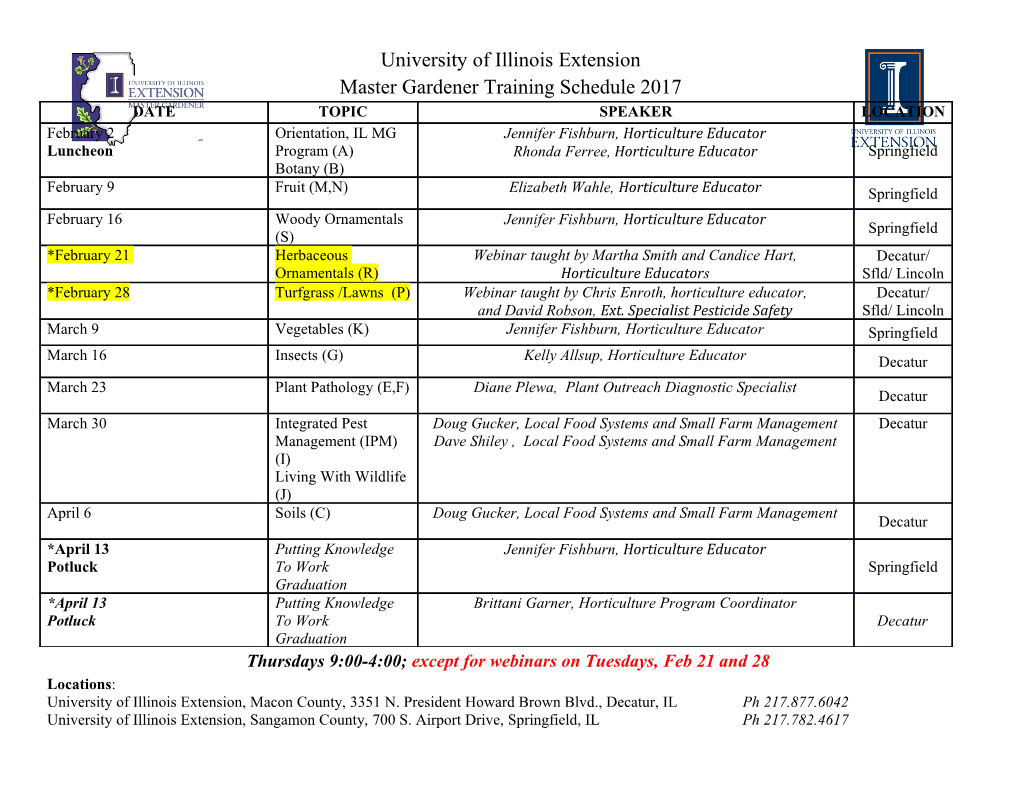
UNIVERSITY OF CINCINNATI Date:___________________ I, _________________________________________________________, hereby submit this work as part of the requirements for the degree of: in: It is entitled: This work and its defense approved by: Chair: _______________________________ _______________________________ _______________________________ _______________________________ _______________________________ Comparison Study Between OSHA Rule of Thumb and Software Model Respirator Cartridge Service Life Thesis submitted to the University of Cincinnati Division of Graduate Studies in partial fulfillment of the requirements for the degree of Master of Science In the Department of Environmental Health of the College of Medicine 8-12-2008 by Celeste Hemphill B.S., Eastern Kentucky University, 2005 Committee: Roy McKay, Ph.D. (Chair) Glenn Talaska, Ph.D. Paul Succop, Ph.D. Abstract This study was conducted to determine the percentage of time the OSHA Rule of Thumb for respirator cartridge service life agrees with a computer calculated model for CBRN-approved air purifying respirators. Test conditions used and organic vapors evaluated in the OSHA/NIOSH MultiVapor software model were chosen from the NIOSH certification testing criteria for CBRN respirators. Service life predicted from the software model evaluated at concentrations of 2600, 260, 26, and 2.6 ppm was compared to the OSHA Rule of Thumb. When determining service life for CBRN approved respirators, applying the OSHA Rule of Thumb was found to be most successful at 26 ppm (96.6%). Success rate of the OSHA Rule of Thumb was found to be 93.2% and 94.9% at the concentrations of 260 and 2.6 ppm, respectively. Statistical analysis of the data indicates the OSHA Rule of Thumb to be acceptable in determining service life for CBRN approved respirators. ii iii Acknowledgements I would like to give my deepest thanks to my advisor Dr. Roy McKay for encouragement and guidance through this project. I would also like to thank my thesis committee members, Dr. Glenn Talaska and Dr. Paul Succop of the University of Cincinnati for their guidance and assistance with this project. This research was partially by the National Institute for Occupational Health (NIOSH) University of Cincinnati Education and Research Center Grant #T42- OH008432-03 and the Powell/Cohrssen Scholarship fund. Without the assistance of this I would not have been able to gain valuable experience at the University of Cincinnati and conduct this research project. Lastly I would like to thank my family and friends that supported me as I have worked my way through school. iv Table of Contents Abstract…………………………………………………………………………....ii Acknowledgements……………………………………………………………….iv Table of Contents………………………………………………………………….v List of Tables……………………………………………………………………..vi List of Figures……………………………………………………………………vii I. Introduction………………………………………………………………..8 II. Methods…………………………………………………………………..13 III. Results……………………………………………………………………15 IV. Conclusions………………………………………………………………22 V. Tables…………………………………………………………………….27 VI. Figures…………………………………………………………………....43 VII. References………………………………………………………………..46 VIII. Appendices……………………………………………………………….48 v List of Tables 1. TIC/TIM Families and TRA…………………………………………………27 2. Canister Test Challenge and Breakthrough Concentrations…………………28 3. Organic Vapors Evaluated in This Study and Corresponding CAS #.............29 4. NIOSH Certification Testing Conditions…………………………………….31 5. Software Model Cartridge Data……………………………………………...32 6. Exposure Limits……………………………………………………………...33 7. OSHA Rule of Thumb……………………………………………………….34 8. OSHA Rule of Thumb Applicability at 25% Relative Humidity……………35 9. OSHA Rule of Thumb Applicability at 80% Relative Humidity……………36 10. OSHA Rule of Thumb Applicability at Both Relative Humidity’s………….37 11. Summary of OSHA Rule of Thumb Applicability…………………………..38 12. χ2 for OSHA Rule of Thumb at 25% Relative Humidity…………………...39 13. χ2 for OSHA Rule of Thumb at 80% Relative Humidity…………………...40 14. χ2 for OSHA Rule of Thumb at Both Relative Humidity’s Combined…….41 15. Chi Square ( χ2 ) Distribution Table………………………………………….42 vi List of Figures 1. OSHA Rule of Thumb Applicability at 25% Relative Humidity……………43 2. OSHA Rule of Thumb Applicability at 80% Relative Humidity……………44 3. OSHA Rule of Thumb Applicability Comparison at 25% and 80% Relative Humidity……………………………………………………………45 vii I. Introduction The first lines of defense to protect workers from harmful chemical and physical agents encountered in the workplace are engineering and administrative controls. When engineering and administrative controls are found to not protect the worker, personal protective equipment is used. Use of personal protective equipment in the workplace is regulated by the Occupational Safety and Health Administration (OSHA). Employers are required to provide an employee a respirator that protects from exposure to harmful airborne contaminants. OSHA’s Respiratory Protection Standard, 29 CFR 1910.134 states that when respirators are used in the workplace, a written respiratory protection program must be established and implemented by the employer. This program must include procedures for the following: respirator selection, medical evaluations of employees required to wear respirators, fit testing for tight-fitting respirators, proper use of respirators in routine and emergency situations, schedules for respirator maintenance; adequate air quality, quantity, flow of breathing air for atmosphere supplying respirators, training of employees of the respiratory hazards of potential exposure, training of employees in the proper use of respirators, and evaluation for the effectiveness of the program. Once a respirator has been selected, a requirement in the respiratory protection program is the development and implementation of a cartridge change-out schedule for the conditions in which the chosen respirator will be used (OSHA, 2006). 8 A respirator cartridge change-out schedule is used to determine the length of time that a cartridge can be used before being discarded and replaced. Service life is the length of time a cartridge will effectively remove contaminants from the incoming air stream. Calculating the breakthrough time that a contaminant can be detected on the downside of the cartridge is one method that can be used to determine cartridge service life (Plog, 2002). Other methods include: experimental testing, math models, or manufacturer’s recommendations (OSHA, 2006). When using these methods, several factors must be considered to calculate the cartridge service life including: cartridge type, concentration of the contaminant, temperature, humidity, filtering capacity of cartridge, pattern of respirator use, and breathing rate (Plog, 2002). Once all factors have been considered and the service life of the cartridges determined, a change-out schedule can be developed and implemented in a written respiratory protection program. An accurate cartridge change-out schedule must be implemented to ensure that workers are adequately protected from exposure to harmful airborne contaminants in the workplace. A quick method used to determine the service life of a cartridge is the Rule of Thumb developed by OSHA. This method can be applied to determine the cartridge service life when exposed to chemicals at varying environmental conditions. The Rule of Thumb consists of four suggestions: (1) if a chemical’s boiling point is above 70ºC and the contaminant concentration is less than 200 parts per million (ppm), service life is generally expected to be 8 hours at a normal work rate; (2) cartridge service life 9 is inversely proportional to work rate; (3) when the concentration is decreased by a factor of 10, the service life is increased by a factor of 5; (4) service life is reduced by 50% when the relative humidity is above 85% (OSHA, 2007). This study will be conducted with the suggestion concerning the concentration. For example, if the service life of a cartridge at 100 ppm is 30 minutes; when the concentration is reduced 10 fold to 10 ppm, the service life can be increased to 150 minutes. The generalizations of the Rule of Thumb are thought to be correct, but service life should be determined in conjunction with other methods such as math models or software programs. OSHA and NIOSH have developed the software program MultiVapor, which is used to determine the cartridge service life. This program allows the user to enter in parameters of the cartridge being evaluated, the environmental conditions in which the cartridge will be used, the contaminant(s) the cartridge will be used against, and the contaminant airborne and breakthrough concentrations. Once all parameters have been entered into the program, an estimated average breakthrough time will be given, along with the minimum and maximum breakthrough time in minutes. When choosing a respirator, the employer must select and provide one appropriate to protect the worker from the respiratory hazards that are potentially present in the workplace. OSHA’s Respiratory Protection Standard requires all respirators to be certified by The National Institute for Occupational Safety and Health (NIOSH) and used in compliance with the respirator’s certification (OSHA, 2006). Within The Centers for Disease Control and Prevention (CDC) and in the Department of Health and Human Services (DHHS), NIOSH is the regulatory agency responsible for testing 10 and certifying respirators and cartridges as well as issuing recommendations for the use of respirators (NIOSH,
Details
-
File Typepdf
-
Upload Time-
-
Content LanguagesEnglish
-
Upload UserAnonymous/Not logged-in
-
File Pages68 Page
-
File Size-